Turquoise
Energy Ltd. News #64
Victoria BC
by Craig Carmichael - June 3rd, 2013
www.TurquoiseEnergy.com
= www.ElectricCaik.com
= www.ElectricHubcap.com
= www.ElectricWeel.com
Month In Brief
(Project Summaries)
- day by day... mostly related one way or another to the electric Mazda
RX7
In Passing (Miscellaneous
topics, editorial comments & opinionated rants)
- DirectVotes.ca: The Referendum Site - at least, the idea.
Electric Transport - Electric
Hubcap Motor
Systems
* Mazda RX7 & mixed batteries... and still more repairs...
continued.
* EV Individual Battery Monitoring System - software development.
Other "Green" Electric Equipment Projects
* Solar PV system + inverter charges electric car via its usual
charging
system.
* Solar PV system main panel improvements
* MSP430 software development: in something that should be simple,
roadblocks are thrown up by inconsistent C syntax, lack of
assembly language documentation and lack of examples.
* Roadblocks surmounted -- working, effective software written in
Assembler!
Electricity Generating (no reports)
Electricity Storage - Turquoise
Battery Project etc.
* New chemical Ideas: Prussian blue & Potassium-Ion, Barium
chloride &
barium manganate (stable, insoluble!)...
* NiMH: 14.0 volts is a better float charging voltage than 13.8
or 13.9V: it
holds a lot more charge using 14.0 volts, and the float current after
charging is still low.
* More NiMH D cell "Handy Battery Sticks" (tubes): 12v, 60AH batteries
- just
25 pounds (for
electric
Mazda, of course)
* My last NiMH soldered battery pack disaster! (I trust.)
No Project Reports on: DSSC
solar cells, LED Lighting, Pulsejet steel
plate cutter, Magnetic
Motion Machine, Ultra efficient vehicle transmission/torque converter,
CNC Gardening/Farming Machine (sigh, maybe summer 2014!),
Woodstove/Thermal Electricity Generator, Peltier heat pump.
Newsletters
Index/Highlights: http://www.TurquoiseEnergy.com/news/index.html
Construction Manuals and information:
-
Electric Hubcap Motor - Turquoise Motor
Controller - 36 Volt Electric
Fan-Heater (say, this heater is now obsolete! Use Peltier module heat
pump!)
- Nanocrystalline glaze to enhance Solar
Cell performance - Ersatz 'powder coating' home process for
protecting/painting metal
Products Catalog:
- Electric Hubcap Motor Kit - also please inquire about Electric
Caik
3KW Motor Kit
- Sodium Sulfate - Lead-Acid battery longevity/renewal
- NiMH Handy Battery Sticks & Dry Cells (cheapest NiMH
prices in Victoria BC)
- LED Light Fixtures
Will accept BITCOIN
...all at: http://www.TurquoiseEnergy.com/
(orders: e-mail craig@saers.com)
May in Brief
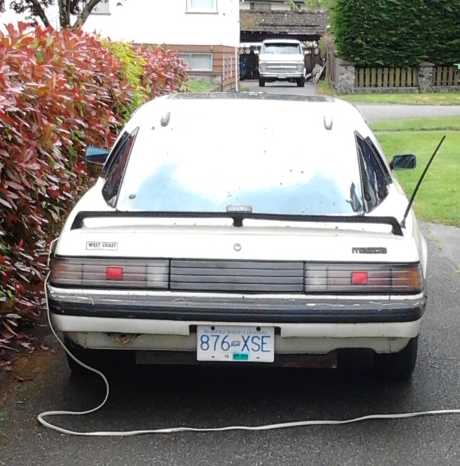
Charging the Mazda RX7 at Tom's while discussing electric cars and bikes
In May again the electric
Mazda RX7
took
priority. Now that I had it, I wanted to have it working properly and
with a useful driving range for local travel - and it wasn't at all
co-operative. On top of ongoing battery woes and gradually weeding out
weak renewed batteries, and then failure of the main circuit breaker
while driving, it had various
problems which had more to do with age and disuse than it being
electric. Besides zinc primer paint on rusty battery mountings and
various interior cleaning jobs, during the month:
* I replaced what were once windshield wiper blades
* I replaced most of the lights with 12V LED lights. But I ran out of
"2 filament" LED lights before getting to the front turn
signals/running lights. I need to order more to finish, and more again
for the Sprint and the 4-runner. I can't find 6" round LED headlights
any more than 4"x6" square ones... is there one more little big oil
conspiracy here?, to make sure the 'always on however inappropriate or
annoying' lights - that also burn the most gas - continue to do so?
* I disassembled and fixed the driver's door, twice - the outside door
latch had quit opening the door. (That was after taking the passenger's
door apart and greasing the sticking latch mechanism and window winding
mechanism earlier.)
* I fixed the windshield wiper mechanism - when it rained while I was
driving, I discovered the wipers were seized solid.
* The signal light blinker, already blinking much too fast, quit
working most of the time. Pushing it one way or another could get it
going temporarily. I managed to extract the blinker unit from under the
dash, and resoldered a half dozen bad solder connections to the 17 pin
plug
on its single sided circuit board.
* When the running lights were turned on, the left rear
turn signal came on with them, and two running lights came on with the
left turn signal. I finally found there was an unconnected ground wire
under the hood, from the _front_ left two-filament turn/running light
bulb.
* One headlight was dead. A new
headlight didn't help. Neither did fixing a wiring problem. It turned
out both the wiring and the headlight were bad.
* Then the first time I used the headlights at night, they went out. I
replaced an old
exposed fuse wire that was apparently too corroded to run two
headlights at once
and
blew.
* I fixed the windshield washer.
The pump was seized solid. (No surprise since it appeared to be made of
solid rust.) I used WD40, then a hammer with a countersink to break
loose
the
shaft.
On the 6th I finally
finished a 6-stack NiMH 'cube' battery for it, removing the
weakest lead-acid. It didn't seem to help a whole lot. The next run was
1.2
miles (2 Km), the farthest yet by a small margin and there were two of
us in the car, but the batteries had just been charged and the voltages
(nominal 108) were down into the
60's whenever I "hit the gas" by the time I got back.
By leaving it on charge overnight instead of just for a
few
hours, I managed to drive it to the plaza the next morning, a 3 Km
round trip. The voltages were over 90 on the way there, but dropping
into the 70's again by the time I got back - but it was a good
improvement. Then I figured
I should just leave it plugged in, per my original intent with the
float charging, despite any little noises from the batteries. It didn't
seem to help - another trip to the plaza on the 8th drained things down
to about the same low voltage levels.
That left making more NiMH batteries (I made three simpler
"giant
flashlight tube" ones this time and put them in a wooden box) or buying
new PbPb's, and getting rid
of the remaining renewed PbPb's and the oldest 'new' battery with
sodium sulfate added. I finally had to conclude that for whatever
reason they just didn't seem to hold anything like full charge - except
one with sodium sulfate added when new that was the
best battery in the car.
I can play with them using "the pentagon" headlights panel
as
a
heavy load and see if anything helps. I'll want some of them for the
boat if
they'll work well. I started feeling overwhelmed. The grass was 15"
tall and
the hedge was up to where the city might complain, I still hadn't
finished the income tax that should
have been done in March, after all the time and effort I still couldn't
drive the electric car even to downtown, and all the other projects
were
languishing.
I finished converting all ten 12v power adapters to
13.8 to 13.9v battery chargers, giving one for each battery as
intended, and as soon as that was done, I had to change 4 of them to
14.0 volts which seems to be a better float voltage for the NiMH
batteries: 13.8 or 13.9 volts doesn't fill them even close to full
capacity, and steady-state current once charged seems to be much lower
at 14.0 and even 14.1 volts than what I thought when I initially
measured NiMH performance a couple of years ago. Then I put in an 11th
battery
and needed another charger. I just threw in a regular battery charger
for the time being.
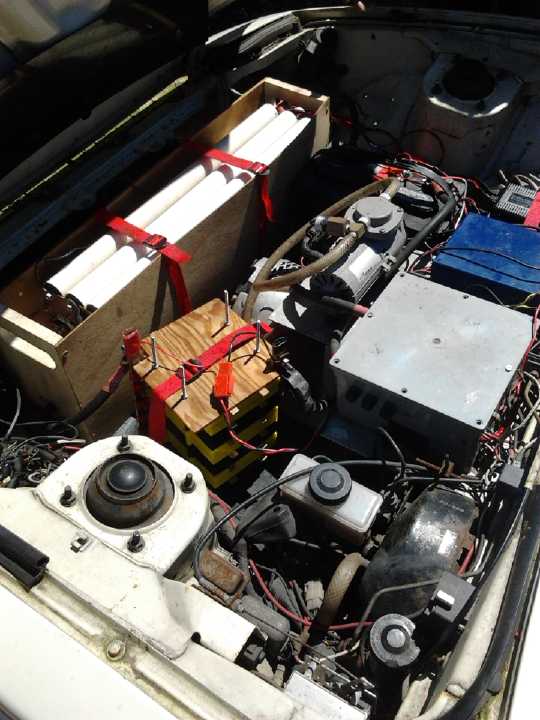
Under the RX7 Hood: One yellow and black NiMH D cell 12V 60AH cube
battery,
three more as 18 pipes in a box (shown without lid), and just one lead
acid on the far side.
At the top corner extreme right: 5 little black power adapter float
chargers under a
red strap.
(One of their output plugs can be seen on the cube battery.)
Besides the car itself was
the individual battery monitor
project. Setting up to write microcontroller software ate my time
without evident progress, as there was a
fair learning curve. For all the vast reams of code I wrote in the
1980's and 1990's, I hadn't programmed in a decade, I had to do
stuff in "C" language which was never my forte to get things going, and
the silicon industry is a few generations of chips beyond what I had to
work with in 1986. I tried using the assembly language that came with
the C compiler, but was unable to create a successful program with it.
On the 21st the roadblocks finally started to clear: I
finally finished my lengthy overdue tax package with 8 claimed SR
& ED projects I'd invested my time, space and money in, and got it
off. I bought a reconditioned
battery and removed the weakest one from the RX7, and on the 22nd I
borrowed yet another battery making 132 volts. That gave the RX7 some
zip
and some range - made it actually usable (except for the malfunctioning
turn signal blinker, and the dead headlight for night driving). The
four 60 AH NiMH's seem like a fair match with the 80-95 AH lead-acids.
And I finally got an assembly language, Naken Asm,
to successfully assemble a program which downloaded and ran properly on
the MSP430 microcontroller, using the debugger that accompanied the C
compiler. At last I could start writing software to make the various
planned controls and the battery monitor! I soon had it displaying
numbers and letters on a 4 digit 7-segment LED display with SPI
interface that I had, and reading analog inputs (for battery voltages
and temperatures).
The RX7 car testing, fixing and improving went on in
various work sessions day by day until the very last day of the month,
when the last problem (hopefully) was remedied. Range between charges
and total daily distance gradually went up. But on the 24th the main
breaker packed it in, with the smell of burned
bakelite.
I brought some tools and a heavy 4' battery
cable, bypassed the breaker with it and drove home. I took it out and
repaired it by
silver soldering in two new nickel contact pads and un-bending its
overheated copper arms, and took a 3.4 mile test drive before dark.
Everything
worked smoothly. On the 29th I drove a total of 8 miles - the first
one with the parking brake on. (but obviously not pulled up very
tight.) In spite of some charging, some of the batteries were getting
down there by the end. Oddly,
two of the NiMH's were getting pretty low while the other two had a
fair charge left. I suspect that the low ones each have one set of the
six series strings of ten cells that isn't connecting properly, or at
all. The next day I drove 5 miles/8Km in one trip, going easy on the
pedal. The weak lead-acid was down to 11.8 volts afterwards (the rest
were 12.4-12.6). The 'weaker' NiMH's were still at 12.3, so they had
some life left. (The other two were above 12.5.) I can doubtless
squeeze another couple of kilometers out of that weakest PbPb, making
it 10, and I *think* it's
gradually improving, bit by bit, with cycling. I gave a friend a ride
in the evening and the headlights went out - the above mentioned fuse
wire.
Finally on the 31st I drove
5.5 miles/8.8Km in one trip - using 12.5
amp-hours, or 300 watt-hours/Mile (188 WH/Km). It was the highest
energy usage figure so far, but it still beats figures I saw recently
for the iMiEV (320 WH/M), the Leaf (340 WH/M) and the Volt (360 WH/M).
Yet it doesn't attain the 215-250 WH/M figures I saw for the crushed
EV-1's of 1997-2002 fame. On June first evening I drove a total of
7.4 miles (with a good charge half way),
travelling more on 'through' streets with less stopping and starting
than usual, and that used just 252WH/M or 157WH/Km. Added to a 4.3 mile
trip that morning, the day's total was 11.7M or 19Km. With some
reservations the car seems fit for local travel. I think I only used
the gas Toyota Tercel station wagon two or three times in the whole
last half of May. (Once was short hauls to bring home firewood from a
couple of trees cut down on a nearby boulevard, and once for a shopping
trip with at least three destinations.) But the charging is
pretty slow, and it would certainly go farther without the limitations
imposed by the weakest lead-acid and now the two weaker NiMH batteries
(which I'll investigate).
I've been told the car is very quiet from the outside. But
there's no sound insulation at all from the rear end, where the battery
compartment is vented right next to both rear wheels, and I certainly
want
to put a
good cover over the compartment to muffle the sound of the rear end
gears, bearings, brake shoes, wheels and bits of gravel on the tires.
On the evening of the 25th I started writing on something
I've had in mind for a couple of years now and reserved a domain name
for: the DirectVotes.ca website where
anyone can initiate a referendum on any issue, with interactive choice
ranking voting. Making it work will be a big job, but at least now the
idea is now on the web. Perhaps the pressure of known, stated public
opinion
can reverse the trend towards tyrannical, out of control government.
(See In
Passing, below.)
Hands on with projects is exciting, but if I don't get
them out there, they're not much good to anyone.
I'd been planning to do a promotional video about CAT
standard 12 VDC plug & sockets, and I shot some footage as I wired
up the CAT click-lock plugs and sockets for the RX7. If it's to become
a real standard people have to know about it and what's good about it.
On the evening of the 29th I downloaded the videos from my 30$
camcorder - the only one that works with my version of Windows
Movie Maker (which is the only really working video cutter and
paster I've
found so
far) - and cleared it out for new footage, which I then shot some of
for the
promo. I got a "part two -
hands on" video put together, of
making them and wiring them up, shooting a few more little clips to
fill in things I'd missed as I went. It's ready to upload (still a
pretty amateur
production), but I'll upload it with part 1 when that's ready, and I
should upload the click-lock plug and socket 3D printer designs to thingiverse.com
at the same time.
Someone says he knows people in the
standard making association, and it wouldn't hurt to get in touch with
them, either, with an eye to getting it 'officially' endorsed. On the
other hand, I doubt anyone ever endorsed car cigarette lighters as
being a standard for 12 VDC appliance plugs and sockets, but in the
absence of
anything else, they're inheriting the position by default. The longer
that goes on, the
harder a better standard will be to adopt. But a cigarette lighter to
CAT socket adapter will fit right into the cigarette lighter socket for
backwards compatibility, which will be a big help.
Downloaded video
clips on the camera included some going back months about making the
Electric Caik Motor and MnMn battery making. I must put those together
as far as they've gone, and upload
them or add to them.
In the solar PV system, I've had a schottky isolation
diode floating in the air between the
DC to DC converter and the breaker panel ever since putting in the
collectors and system last
summer. It would have fried with really high current.
In order to connect the high-powered
inverter for charging the car on the battery side of the diode(s),
where I hoped it wouldn't misbehave, on the 31st I
finally put
together a diode-heatsink assembly for the DC to DC converter. I
waited until after dark to install it in the breaker panel - easier
when the solar panels
wouldn't be live. (Another late night!) I used 3 dual 20 amp schottky
diodes for a total of 120 amps capacity. Since the DC to DC puts out up
to 80 amps, this should be more than necessary.
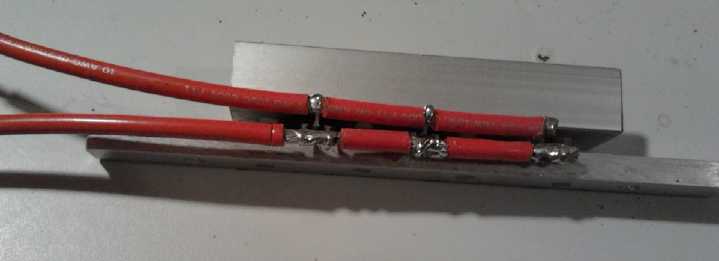
New triple diode to handle all the amps the DC to DC converter will put
out.
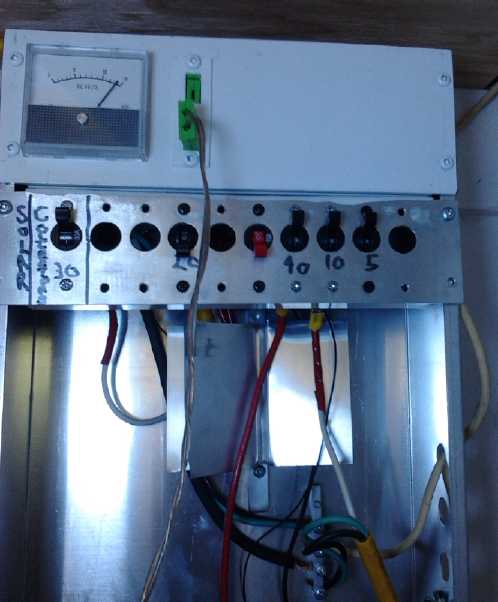
Rearranged solar system main panel with all breakers on the front,
and the above diode inside with heat sink fins added.
After I had driven over 4
miles on June first, it delivered 400 watts to the car in light
overcast near noon, working smoothly - success! This soon dropped to
350 watts. The diodes' heatsink fins in the breaker panel were quite
warm but not too hot to hold on to. Soon, when the clouds got thicker,
the DC to DC converter started buzzing (rapidly going on and off), and
the solar system batteries went down to 12.5 volts, but when they
thinned, everything perked back up again with the panels at about 28
volts, roughly their maximum power point. It was windy with fluffy
clouds, and the buzzing went on and off and up and down in pitch. The
Zahn DC to DC converter seems able to handle this - kudos to the
design! (...most aspects of it.) I bought a new Blue Sea Systems 50 amp
circuit breaker to put
the inverter on its own circuit. I hope that's big enough since the 60
amp breaker is not only triple the price but larger, so it won't fit in
my breaker plate holes.
In Passing
Incidental news, editorial comments & opinionated rants
DirectVotes.ca: The Referendum Site
On the evening of the 25th
I started
writing on something I've had in mind for a couple of years now and
reserved a domain name for: the DirectVotes.ca
website where anyone can initiate a referendum on any issue, with
interactive choice ranking voting.
The referendum format is much superior to
the petition, because with a petition you're counting "yes" votes
without counting "no" votes, a one-sided process that may tell you more
about the
tenacity of the petitioners or the effectiveness of their methods of
signature gathering than about majority or average
opinion.
The interactive choice ranking vote system is superior to
the "Illiterate's X" single ballot because
it can show any diversity of views on a subject as well as give a 50+%
final tally to show the most popular choice or compromise. The choice
ranking vote itself ("instant runoff", "1 - 2 vote", "STV") is a fair,
positive voting system, where voters simply mark the choices in order
of preference, being assured that that's the most effective way to get
what they want and eliminate what they don't want. The single "X"
ballot is
largely a negative, fear driven system yielding unfair, unwanted
results, where voters vote to prevent what they want least rather than
to get what they want most. This
politicizes and polarizes our whole society.
Obviously the results of
these unofficial referendums won't bind
governments
directly. But if a clear majority of thousands or millions of people
vote mostly one way,
no government that's been elected can arrogantly claim "In electing us,
the public have asked us to [do whatever we please]" contrary to
that, or to begin any contrary program thinking - or just hoping - it's
what people want.
The serious and almost global trend towards having rulers
who oppress and micromanage the general public while putting themselves
and their supporters above the law, rather than leaders who
lead and try to level the playing field for everyone, needs to be
reversed.
I've been most hesitant to begin this complex undertaking
knowing
the time and effort it's bound to involve, but it could well be the
best thing I ever do. So I decided I should at
least write up an introductory page and then connect up the URL to
hopefully
start spreading the idea even if
I don't immediately get to the forms, databases and organizational
thought that will be needed to actually make the site functional.
Ideas on software and how to organize things to get it
going are welcome. Mine are pretty vague so far. Once long ago I
did a web form where people filled in their info and when they clicked
"send" it was sent to me as an e-mail. I'll look that up again as a
place to start.
Electric
Hubcap Motor Systems - Electric Transport
A Superior EV Charging System... a superior battery monitoring
system...
and an old beater electric car (1982 Mazda RX7)
A better charging system?
A 13.8 - 13.9 volt float charging system with .62 ohm
resistors means that if the battery voltage is at 12 volts,
1.9v/.62Ω=3.0A. Only a battery down to 11 volts would tax the limit of
the 5 amp power-adapter chargers, at 4.7 amps. When the battery is up
to 13.3 volts, current is down to an amp.
So the charging characteristic with NiMH batteries is to
fairly rapidly bring up a low battery to maybe 50%, more slowly charge
it up to around 75%, and then gradually top up the last 25%. At least,
there's my theory.
But as I consider it, with the extra voltages needed to
charge lead-acids, this might be 'rapid' to 33%, rather slowly to 67%
or less, and then only very gradually to 100%. It would be useful to
have smaller series resistors to increase currents, but then a low
battery might blow the 5 amp power adapter or cause it to shut off and
not charge.
More ideally, a charger that would put out a constant 5
amps or so (or 10+ amps for NiMH?) until the charging voltage reaches
13.9, and then doesn't rise above that voltage, with the current
gradually dropping off, would give considerably improved
charging speed. That's not what I got from XS Cargo for 3.95$ each - at
least not without adding some active component circuits to them. But
it's my present concept of 'ideal'.
After writing the above, I
discovered 14.0 volts is a better float voltage figure for NiMH - they
don't reach a full charge at 13.8 or 13.9 volts. (In fact, 13.8 volts
may be only 1/2 to 2/3 charge.) And after charging, the 'idle current'
to maintain 14.00 volts... up to abut 14.10 volts... is pretty
low. Above 14.1 volts current starts going up, with cell heating
starting at about 14.2. Setting to 14.0 gives just a little margin for
error and drift. However, this adjustment doesn't alter the gist of the
preceeding paragraphs.
Increasing range, replacing batteries, NiMH's in the car and
increasing voltages
On the 6th I finally finished a
6-stack NiMH battery and put it in the Mazda, removing the weakest
lead-acid. It seemed to help, but only a little. Tom Sawyer and I then
ran an
extension cord through the car from back to front, using an existing
hole he found in the firewall and the hard carpet protector cover going
by the
passenger door. Now plugging in the car at the 'gas' cap would energize
all
the chargers. And the power bar at the back has a breaker-switch so it
can all be turned off even with the car plugged in.
The next run was 1.2 miles (2
Km), the farthest yet by a small margin and there were two of us in the
car, but the batteries had just been charged and the voltages were down
from the nominal 108 into the 60's when I "hit the gas" by the time we
got back.
So the next question was, what voltages did other cars
with lead-acids typically drop down to under load? Someone had e-mailed
that he had an idea for LED alarms in the dash when any battery voltage
was more than 20% low. Mine were certainly going lower than that. I
phoned Cam
Rawlinson, really the local expert on such things, and he mentioned
that at my
slow charging rate, a full charge could take 30 hours. This should
hopefully be an exaggeration, but a good point
nonetheless. Perhaps I was fooled because the regular chargers would
say "charged" and shut off after a couple of hours, and if they were on
the weakest battery, it was still the weakest battery on the next trip.
So I left the charge on overnight instead of just a few hours, and
managed to drive to Esquimalt plaza the next morning (7th), a 3Km round
trip.
The voltages were over 90 on the way there, but were dropping into the
70's
again - with a pretty light foot on the pedal throughout - by the time
I got back. Anyway it was a good improvement over the previous 2 Km
record.
The NiMH was down to about 12.2V. Then I figured I should just leave
the car
plugged in, per my original intent with float charging (and despite
little sucking/hissing noises from the lead-acid batteries) and see
what happened.
To go along with that, I adapted two more chargers the
same day making 8 on the 7th, and could at last, by adding one regular
charger in the
back, charge all the batteries at once. I did the 9th on the 10th and
finally had all my individual 12 volt chargers, one for each battery.
Another decent
battery or two
(making 120 or 132 volts) would fit and should up the range too. But I
decided I'd like
to put three 60AH NiMH's in the front to reduce the weight there (25
pounds versus
45 to 60), because the springs are virtually bottomed out with 5
lead-acids - mostly it's the front-left spring. Eliminating the 3
weakest lead-acids might then give more
range than keeping them as extras.
It's interesting
that this would then become almost the same 9 battery set I've been
considering
for the 36 volt Chev Sprint, tho wired differently. In the case of the
Sprint, the plan has been to have three 70AH NiMH batteries where the
radiator used
to go, and three or (more likely) six lead-acids in the back simply to
add storage capacity. The NiMHs can take the high charging currents
made by regenerative braking, increasing city driving range. The
lead-acids
would be [schottky] diode
isolated so they would only supply 36 volts to the front when the front
voltage dropped lower than their voltage and the .3 to .5 volt diode
drop. Since charged NiMH's are
about .5 to 1 volt higher than charged PbPb's, the PbPb's wouldn't
normally start discharging into the NiMH's except when they were needed
in actual driving conditions, owing to high current draw or a fairly
low state of charge in the NiMH's. The diode prevents the NiMH's from
discharging into the PbPb's, which also prevents high regen braking
currents from trying to charge them.
I'll comment at this unfocussed point that there's a
microswitch at
the 'gas' cap that won't let the car drive if it's open, ie, if the
charger cord is plugged in. There's also lights on the dash saying
either "drive power" or "charger cord". The lights seem to be more
valuable than at first glance: a friend showing his EV pick-up truck,
and even some officials from GM at an auto show, left their cords
plugged in and each spent an hour trying to figure out why their
vehicle wouldn't move. I tried once to go and nothing happened, but I
saw the "charger cord" light. Better to
spend the hour at your chosen time wiring up a light than one at an
inconvenient time wondering why your car won't move!
(An idea I had before was
to have the plug
sticking straight out the back. When you try to drive away, the cord
simply unplugs. Of course, that might work fine in my own yard with the
cord wrapped around the tree, but in other situations it might unplug
at the wrong end, or if it's
long enough, it might be left lying out in the street.) Or you might
forget and leave your cord somewhere away from home.
Meanwhile back
at the RX7, on the 11th I went for another
drive - 1.3 miles to Tom's house, where the car could get a
partial
recharge. (3 hours, as it turned out.) To my surprise, the voltage
started flagging badly a couple of blocks before I got there - right
down into the 60's of volts, just over 1/2 the nominal 108. One battery
(an old weak one but not usually lowest) was unexpectedly low, showing
just over 10 volts shortly after stopping. Some testing showed
that one of the power adapter chargers wasn't working right. I swapped
a couple of them and left the best battery off charge. The car did
better on the return trip than outbound, voltages staying in the 90's.
It was fortuitous that I'd
picked a destination where the car could recharge - on this occasion I
probably wouldn't even have made it home from the plaza.
When I got home and checked things again, two
of the chargers weren't working. It turned out that the 5 watt, 1/2 ohm
resistors I'd put in to prevent excessive current when the batteries
were very low were burned out. I had calculated that they might
dissipate considerably over 5 watts with a very low battery. That's
'theory', but low batteries should soon rise over 12 volts and the
dissipation
would drop. So I hadn't really expected trouble.
By the time I was done fixing the second one (with 2
resistors in parallel for 10 watts), it was getting dark. I plugged one
into the strongest battery (not one of the two just fixed, as it
happened)
and saw a spark inside the plug through the plastic. Sure enough, its
resistor too
was now burned out. Then I noticed that the CAT click-lock socket on
that battery was wired backwards, with '+' going to '-' and vise versa.
Until the 10th, I had been
connecting a regular charger to that battery via its aligator clips, so
the
socket hadn't been in use and the mistake had gone unnoticed. Now it
was blowing the resistors in the chargers.
Here is a prime example of where the battery monitoring
system would
be valuable: I would have known from the start or soon after starting
that one battery was already too low. I could then have returned home
and
worked out the cause before trying to drive to a destination...
which this time was luckily not very distant. (Maybe even without
blowing 2 more chargers... or maybe not.)
This trip also disclosed in rain that the windshield
wipers weren't
working (why did I bother getting new blades?), the driver's door, tho
just taken apart and "fixed", again
wouldn't open from the outside, and the turn signal lights wouldn't
blink any more. More bad or loose
connections? Sigh! For an electric car, this thing sure had its
electrical problems!
Also on the 11th: I put together seven 12V "Handy Battery
Stick"
tubes making 9 total, with nine and a wooden box to go, to replace 3 of
the car
batteries. The many boxes of loose D cells lying around
vanished. I'll get more D cells when I have money again. I had to take
apart the last 30AH soldered-together car starter battery, and use the
battery made up of 12 - 6 volt pipes to get enough cells for this
battery. I made a wooden box to hold them all on the 12th.
On the 13th I fixed the wipers. The pivot shafts were
seized up in their sleeves. They gradually loosened with WD40 and
vice-grips... but I didn't know that was the problem until I'd taken
everything apart and almost removed the entire wiper assembly from the
car. Just before it got dark, I took it for a 1.0 mile spin, and the
voltages stayed up above 90 volts (nominal 108) virtually the whole
time. I had the impression the renewed batteries were in fact very
gradually increasing in capacity. One of the headlights didn't work...
and the windshield washer appeared to have no water pump at all, just a
hose from the bottle to the squirter jets! How's that supposed to work?
(It turned out there was a tiny pump motor on the underside of the
easily removable plastic reservoir.)
On the 16th I drove 2.8 miles around noon, and the
voltages stayed in the 80s and up. Before dark I drove 3.0 miles
(slowly and on the levellest ground available) just
to see if I could. Voltages went down into the 60's climbing an
unavoidable hill at 2.6-2.7 miles, and stayed in the 70's and 80's
until I stopped and plugged the car back in at the 3.0 mile mark. I
guess I overdid it after only a partial recharge. But it was the
farthest yet for both trips and for one day - 9.25 Km.
I assembled the NiMH battery box components on the 17th, and also fixed
the driver's door latch. I made it so the upper two 25 pound batteries
could be
installed in the box separately once it was in place, avoiding the need
to lift a nearly 80 pound box. That left the 40 to 60 pound lead-acids.
On the 18th I had Tom with his good back come over and help me shuffle
the heavy batteries around, making:
Under the Hood: * the original stacked box NiMH (from the back)
*** the new triple NiMH box * just one
(the best) PbPb.
In the 'trunk' battery space: ***** the five next best
lead-acids,
all 'size 27'.
Removed: The two weakest lead-acids: the smaller size 24 from
under the hood, and the weakest one from the back.
Total: 10 batteries instead of 9, with 145 pounds up front (down
from 240), and 250 pounds in back (up from 165)
This gave the low left front spring some relief and the
improved
handling on speed bumps was immediately obvious. The removed batteries
were
the two remaining renewed ones. The smaller one was weaker partly
because of
its size. The larger one was only a little weaker than a
couple of others. Of the six now in the car were three newish 'stock'
batteries (all very good), and three with 'a heaping tablespoon' of
sodium sulfate simply added to the acid when they were new(ish), about
3 or 4 years and 6 years old now but little used (two somewhat weak and
the
third excellent).
With the weakest batteries out and 120 volts instead of
108, more range was expected, but how much more remained to be seen.
Evidently I needed to up the float charge voltage for the NiMH's from
13.9 to 14.0 volts to get the most out of them.
On the 19th I converted the 10th and last 12v power
adapter to a float charger - 14.0 volts - and took the car for a 3.2
mile drive. I could have gone a little farther, but the two lowest
batteries were getting down, with voltages drooping from the nominal
120 down into the 80's. If they would last as long as the others, I'm
sure it would go about 6 or 7 miles, perhaps more - finally a useful,
if still very minimal, distance.
On the 20th, my new Cycle Analyst performance
monitor from Cam Rawlinson indicated that the car used 7.6AH to go 3.3
miles, or (calling
the ever drooping voltages 120 volts all the way) 276 WH/mile or 172
WH/Km. This is in
line with expectations. It's about 25% more 'juice' than GM's EV-1,
said to be
around 225 WH/mile or 140 WH/Km. It's also 55% above my
"ultra-efficient transmission" target of 111 WH/Km, which I expect to
be 50% better than a "standard" EV car drive. Some trips were up to
300 WH/mile or 188 WH/Km. Using 200 WH/Km and all decent
batteries, range should rise to 15 miles/24 Km. On flat terrain and
smooth roads without a lot of stopping and starting, 30+Km would be
reasonable, but Victoria - and BC in general - is hilly and Esquimalt
in particular has in recent years become full of speed bumps and
congested shrinking main roads.
With 4 NiMH batteries evidently wanting 14.0 volts for a
NiMH float voltage, I had next to pull out 3 more of the chargers and
raise
their voltage. Why is it there are so many things to do on this car,
and that so many of them seem to so soon need re-doing? It wasn't my
intention to take on yet another project that would eat week after week
of my project time! On the other hand, I don't have the Chev Sprint
ultra-efficient conversion running yet, gasoline passed 140¢/liter
here this month, and with every country trying to make their currency
hit zero first, it seems likely fuel prices will only go up.
On the 21st I broke down and bought a reconditioned
battery from Battery Doctor to replace the weakest battery. The
improvement was evident. That evening Tom Sawyer phoned and said he'd
collected some old batteries in his travels, and swapped them as
'cores' for one new
battery, but he doesn't have his electric car yet, so I should use it
until then. We installed it the next day. (I had lunch with them. He
not only has his great electric scooter, but an electric 2 seat kids'
car, which the young neighbors also got to ride and drive.) The
performance of the car was certainly going up as the number of
batteries went from 9 to 10 to 11. We had it on charge at his place and
with the first new battery as well as the 11th battery, there were too
many new factors to try and determine range so I went home and plugged
it in for the afternoon and overnight. I had to swap some plugs around
with 11 batteries and only 10 chargers.
I'm pretty
sure the range will be over 5 miles/8 Km now. I drove downtown and
back, 3.8 miles/5.0Km, on the 23rd - another record distance. (I had to
take one old battery as a "core" to Battery Doctor in exchange for the
one I bought.) It remains to be
seen whether the last rather weak battery is a help or a hinderance. I
can't say it isn't very gradually improving with cycling... but if so
it's happening too slowly to say that it is, either. The rest of the
batteries seemed not to go down below 1/2 charge, suggesting they'd be
good for at least 8 miles/13Km. One disturbing thing that happened
during the trip was that the knob that turned the main breaker off and
on from the driver's position worked its way out with vibration, and
the car quit in a driveway. I started thinking of ways to lock it into
place by friction.
On the morning of the 24th I got under the dash,
disassembled a few things, and removed the box that controlled the turn
signals. I took it up to my electronics shop and opened it. A cheap
single sided circuit board covered the bottom. The 17 pin plug
connected to the middle of that, and there were about 1/2 a dozen bad
solder joints on that. Why had the signal lights worked as long as they
had? I resoldered all the plug contacts and put it together again. At
last, the signal lights worked properly! It seemed all the important
things for local driving were now working.
But the car got its revenge: the main breaker for the
drive system, rated 250 amps at 125 VDC, quit connecting and smelled
burned. Luckily I was able to push the car around a corner and park in
a legal parking zone. I called Tom, whose house I had been going to,
and he picked me up on his electric scooter. We rode to my place and
got some tools and a heavy cable with which to bypass the breaker by
connecting the main contactor direct to the battery. That left only the
450 amp in-line fuse to protect against any major electrical problem,
but I was able to drive home okay.
The converters of the car buried this very large breaker
under a bunch of other things in a plastic box, and it was
difficult to remove it. The obvious way, to pull it up, would have
required dismounting several components and unsoldering several small
fuse holders. In fact, I think the breaker was wired into place, then
mounted, and then everything else was added with no thought about
replacement or maintenance. But I pulled out the main contactor and
chipped away around a hole to give a heavy cable enough free play to
undo it, and slid the breaker out sideways under all the small
components.
By taking on this car, I'm learning not only how EV
conversion things are done, but some "how not to" as well.
I figured this was going to be a pricey component to
replace, so I drilled away the rivet ends to open it and see if
anything could be done. The contacts inside the breaker were sooty
black... and the silver solder of the pair on one side had melted and
left the contacts in odd, angled positions. Furthermore, when the
switch was closed, the contacts were still loose with play between
them. That kept it from firmly clicking "on"... which just might
explain why
it had turned itself off the previous day. Had it been
deteriorating for some time, and had just picked this particular day to
finish coming apart, or was it just because I was turning it off after
driving, where the previous owner says he never touched it?
Nothing went smoothly, but before dark on the 25th I had
the breaker repaired by silver soldering on new pure nickel metal
contacts cut from a pre 1982 Canadian nickel and bending the nearly
melted copper mounting arms straight so the contacts closed firmly, and
I got
everything back together in the car. I took a 3.4 mile test drive and
nothing unusual happened.
On the 26th I found a disconnected ground wire under the
hood to the front turn signal/running light (a two filament
bulb) that had been causing the left turn signal/running lights
cross-connection problem that was mostly apparent at the rear. That
just left the burned out right headlight.
The next day I drove 4 miles to Lordco (new record
distance) and bought a new one. It didn't help.
On the 28th the car used a lot more electricity than usual
to go 3 miles: over 1 KWH, 339 WH/Km. The parking brake was only
on for 1/2 of the trip, so that half was probably well over 400.
Later I went to fix the headlight wiring. There was an
added wire running from one headlight to the other. It seems after the
accident (before I had the car), the light hadn't worked and the owner
ran the wire. But it was just stuffed into the plug and not soldered. I
removed the new bulb (might as well get my 20$ back) and spliced and
soldered the wire onto the original wire at the plug, wrapping it with
electrical tape. But it still didn't work. I opened the other light and
found the other end likewise stuffed into the plug, but it seemed much
tighter. I fiddled around and touched the wire to the connections, then
soldered that end too, but
it wouldn't work. Finally, a voltmeter said there was voltage. Then it
occurred to me to check the bulb with the meter. Sure enough! Given
everything so
far on this car and Murphy's law, why hadn't I immediately just assumed
it was both a wiring problem and a burned out bulb?
The headlights still weren't quite finished their pranks.
The evening of the 30th I took a friend for a ride, my first after dark
drive. After a couple of blocks, the headlights went out and wouldn't
come on again. On the 31st I found an exposed fuse wire that I'd
noticed looked rather decrepit (was this really a manufacturer's
original?) had burned out. I guess it just couldn't handle powering two
headlights. I then drove 5.5 miles. On the last .5 mile, the voltages
rapidly started to drop quite a bit. Not only was the weakest lead-acid
down to 11.75 volts after the trip, but two of the NiMH batteries were
down to 12.0 and 11.9, meaning they didn't have much charge left. The
other two were 12.2 and 12.3 volts - down a lot but not out. I suspect
one string of the six strings of 10 D cells is making poor or no
connection in each of the weaker two.
Also that day I pulled out the windshield washer reservoir
and excavated a small rusty blob from the underside - the seized solid
pump. Some scraping, WD40, and a hammer and a nail set to tap the end
of the shaft with, got it freed up, and it ran and pumped. It still
looks like a rusty blob except the silvery outer end of the shaft is
visible.
That not only ends the month, but also was the last
obvious 'factory equipment' problem on the car.
Automated
Individual Battery Monitoring System
I'm beginning to think the individual battery monitoring
system is just what's needed - it's a big
issue for lead-acid or any non-uniform mix of batteries, but probably
it's a good idea on any electric car, period. Of course electric car
makers
either will put them in themselves or give no practical access to the
battery voltages, but converted cars, and e-bikes and electric powered
boats, could be good markets. Compared
to the labor of making motors and controllers, battery monitors would
be pretty easy to make and I could see selling a good number of them.
There are just 8 analog inputs on each MSP430G2553 chip.
In order to get enough analog inputs to monitor 10 to 12 batteries (or
even more), I figure I could either monitor some 24 volt sections
instead of 12 volt to reduce it to 8, put in a 4051 type chip (an 8 to
1
line analog switch/multiplexer) to make more inputs, use a second
MSP430 chip with 8 more
inputs, or an MSP430 variant with more inputs - some have up to 12. The
trouble with the chips with more pins is they're usually made too
miniaturized for a 58 year old to work with by hand.
Using two optically isolated MSP430's, one with the
display as the master, and one as 'slave' just sending out voltage
readings, might work out well: With batteries in
the front and rear as the Mazda and many other EVs have, the only link
needed would be a
serial SPI cable, instead of running multiple battery sensor cables
from
the rear batteries to the front of the car. And the two sections would
each be 72 volts nominal or less, allowing finer voltage reading steps.
I also discovered by trying to charge the car from the
solar collectors on the house that it would be desirable to be able to
charge the car even more slowly for the situation of limited power.
Either special chargers could output reduced amps, or banks of chargers
could be turned off and on individually via solid state relays -
perhaps by the battery monitoring system. In this
way, even a single solar panel on the roof of a station wagon could
gradually charge the car via the regular charging system. But simply
monitoring the batteries for the driver and warning him of trouble is
the
main thing, and I should stick to that for a first
point.
As part of the exploration for the idea, I ordered a
Cycle Analyst performance monitor [made in Vancouver by
ebikes.ca] from
TerrAqueous (AKA Cam Rawlinson - starter of VEVA[.ca] Islands). It came
and
was installed on the evening of the 17th. In fact, we worked until 1 AM
under LED lighting, and got it in except for the Hall sensor
tachometer, for which a magnet had to be fastened to the drive shaft.
Then we took a short drive and he showed me how to set it up and use it.
It has a number of useful features:
* voltage
* current
* kilowatts
* lowest voltage of the trip
* highest current of the trip
* number of amp-hours consumed
* % charge remaining, evidently based at least partly on battery
voltage, expressed as a partly filled battery picture (rises while the
car sits after driving, which is only partly indicative).
Once the hall sensor and the magnet on the drive shaft are
fitted, it will also show:
* distance travelled
* speed
* amp-hours per distance
All these things would be simple enough to do with my
planned battery monitor, but they all take programming time. And the
Cycle Analyst has still other features such as a connection for reading
torque, which I don't plan to use at present, but which might be handy
for the ultra-efficent transmission tests.
Electric Equipment Projects
Solar PV Car
Charger
I've considered that it would be great
to charge cars with a solar PV panel on their roof. The station wagons
could easily be outfitted with roof racks holding a collector. For 36
volt systems, I was thinking of three smaller collectors each directly
charging one 12V bank through a simple 14.0 volt regulator. The Mazda
on the other hand has a tiny roof area with a sun roof window in the
middle, and uses more power than my ultra-efficient drive ideas. It's a
poor candidate.
But the solar
panels I installed on the house last July have been rather
underutilized so far - at least in summer sun. Now the sun is coming
out
at times again, and I have an
electric car to keep charged up. Sounds like there must be a match
there
somewhere! With the batteries in the car all floating at different DC
potentials, a direct DC to DC wire-up from the house is problematic.
The obvious solution was to put the DC solar power through an inverter
and charge the car with 120 VAC through its usual charging system.
If ten chargers in the car were charging ten batteries at
5 amps each, that would be 10*5A*14.0V=700 watts. The DC to AC
converter plus the AC to floating 14.0 or 13.8-13.9V DC power adapter
chargers in
the car might be each about 80-90% efficient, or together say 75-80%
efficient. 700/.75=933 watts. That's just over what all four collectors
should theoretically put out in full sun (892). The equipment should be
sized for the max
to prevent it from shutting down on overload, or burning out, when most
needed. Skipping my
light duty plastic 750 watt inverter, I employed the big, "industrially
noisy" 3000 watt one for a few days. On the 13th, I bought a 1500 watt
inverter "on sale" at Canadian Tire for 120$ whose (quieter) fan only
came on if it was needed. In fact, the unit gets pretty hot and the
fans stay off.
It's certainly not going to
charge all those car batteries at night off the few batteries in my
solar PV system, so it should run only during the day in the sun. First
I
hooked it direct to the DC to DC converter ahead of the diode isolation
for the batteries. It couldn't drain
the batteries and quickly kill the 12v power to the house (mainly, to
the fridge at present), but it
could cause overloads and problems in evening, early morning, and
clouds.
Next, the plug-in. For a lighter load I'd use a CAT plug
and socket, but this is serious current: 933W/14V=67 amps. It's hard to
even find a circuit breaker that large. I used short #10 wires, with a
75 amp APP connector to unplug the "plus" wire - highly desirable since
the inverters have no hard "OFF" switch in case anything goes wrong, or
for low power situations. The
inverted 120 VAC ran through a 100' extension cord to the car.
More ideally would be a flexible input inverter that would
take about 24 to 34 volts input -- and shut itself off for a few
minutes if the voltage dropped too low under load. This could be wired
right to the collectors without going through the DC to DC converter
with its 13.9 volt output, avoiding stressing the converter and also
its inevitable percentage power losses. I didn't find one, much less at
an affordable price. I also thought about using a grid tie inverter and
having the collectors supply the mains to reduce the power bill, but
one for 1000 watts would have been over 1000$.
Sure enough, when I came back from another 2.2 mile test
drive with very low batteries and plugged the car into the solar system
in full sun, the 13.8 volts started out at 11.5, the amps read over 90
and the watts said over 700. This dropped somewhat in a few minutes,
but the 14.2 volts stayed down at 13.2 and soon the Zahn DC to DC
converter got hot, and the #10 wires from it to the inverter got hot.
Barely able to supply the total load, the collectors were down at 19
volts, way below their maximum power point around 27-29 volts. The 13.8
volts to the house was running off the batteries and started dropping,
in full sun. The car was eating everything.
After perhaps 1/2 an hour the DC to DC converter was up to
14.1 volts, the house voltage stopped dropping, and the voltage from
the collectors went above 25. But the DC to DC converter was hot, and
the wires to the inverter were still warm. With a DC amp probe, I found
the current was still almost 40 amps - over 500 watts from the DC to
DC. No wonder everything was struggling! However, it was all holding.
The solar panels were for the first time being utilized to capacity.
In the next couple of days I found that it only worked in
absolutely full sun near the middle of the day. Any hint of clouds and
the panel voltages dropped
off, the DC to DC converter wouldn't put out, and the 3000 watt
inverter made squealing or buzzing noises, even if it was turned off.
It had to be disconnected to stop it. Later on after the charging
currents had dropped down, the system worked, drawing around 25 amps
from the 14.2 volt DC to DC converter. Then the clouds got a little
thicker and it quit again. I could probably charge half the batteries
at once, but that was (a) a hassle (swapping around plugs in the car)
and (b) it would be twice as long before I could use the car again.
Easier to plug into the power grid except on very sunny days. But those
do often come in the PNW summer - typically June, July, early August,
and September.
One day it seemed to work well if I waited until the car
was more or less charged to plug into the solar - then the whole thing
drew much less current. But that's not saving a lot of electricity. And
the next day, with just 90 watts load, it started squealing when some
heavier clouds covered the sun. Obviously inverters
connected direct to solar power shouldn't be left unattended at any
time.
On the 19th after a 3.2 mile drive, the new inverter
started out saying about 440 watts, which soon dropped under 400. After
40 minutes it was under 300, or 30 watts and 2 - 2.5 amps for each of
the 10 batteries - on average. Then some light clouds dimmed the sun
and it started squealing. I remedied this on the 31st per the article
below.
With the self contained solar system, I should at least be
able to drive almost for free during sunny summer weather... all except
those nasty 56 $/month car insurance premiums - over 100 $/month for
two cars for one driver who doesn't even drive either one every day -
and never both at once. That probably means I'm paying 30 or 40 cents
per kilometer for fairly minimal insurance. I definitely feel
overcharged on that, and no amount of efficiency or electrical power
generating equipment can fix it.
I usually have quite a lot of food in my freezer. (I used
up my last Y2K blackberries just last year and am up to 2006 berries.
It's amazing how long frozen berries last. The relative food nutrition
index is worth remembering: fresh is best - then frozen - then canned -
then dried.) A side benefit to the electric car is that all those
batteries, plus the 3000 watt inverter, plus the solar PV system in the
summer, give me some insurance that I can keep the freezer frozen in
even quite a lengthy power failure. (The freezer itself has worked
reliably for well over 30 years so far.)
Solar PV System
Main Panel Improvements
Solar PV Breaker Panel with all breakers at front and
high current schottky diodes with a finned heatsink.
In the solar
PV system, I've had a schottky
isolation diode floating in the air between the DC to DC converter and
the breaker panel ever since the installation last summer. This diode
would have fried with heavy current. But with the 1500 watt
inverter connected directly to the DC to DC
converter, they both tended to do wild things when high power was
required to charge the electric Mazda RX7.
So now it became important that the isolation diode have proper high
current capacity, in order to connect the high-powered inverter on the
battery side of the isolation diode(s), where I hoped the diode and the
batteries would filter out the deleterious interactions.
On the 31st I finally put
together a diode-heatsink assembly for the DC to DC converter. I
waited until after dark to install it in the breaker panel - easier
when the solar panels
wouldn't be live. (Another late night!) I used 3 dual 20 amp schottky
diodes for a total of 120 amps capacity. Since the DC to DC converter
puts out up
to 80 amps, this should be more than necessary.
At the same time, I had originally mounted the 30A solar
PV panel
circuit breaker on the side of the panel. (30A*30V=900W) Then I made
the front plate
with holes for 10 Blue Sea Systems (or OEM replacement) breakers (holes
nice and even, drilled on the CNC crill-router) to put the branch
circuits on. But now having one breaker on the side of the panel seemed
odd. I could see someone trying to find that breaker to shut it off and
not seeing it. The branch breakers were all attached to the same bus
bar, so I unscrewed them all at once and moved the whole thing over
three places to make room for electricity source breakers on the left:
one for the solar panels, one for a thermal (eg, woodstove) electricity
generator, and one for a grid power supply, a Darrieus or
éolienne windplant, a magnet machine... or something. maybe for
solar panels oriented west of east for evening or morning. I moved
the solar breaker from the left wall to the leftmost place on the
front.
After I had driven over 4 miles on
June first, it delivered 400 watts of 120VAC to the car in light
overcast near
noon, working smoothly - success! This soon dropped to 350 watts. The
diodes' heatsink fins in the breaker panel were quite warm but not too
hot to hold on to. Soon, when the clouds got thicker, the DC to DC
converter started buzzing (rapidly going on and off), and the solar
system batteries went down to 12.5 volts, but when they thinned,
everything perked back up again with the panels at about 28 volts,
roughly their maximum power point. It was windy with fluffy clouds, and
the buzzing went on and off and up and down in pitch. The Zahn DC to DC
converter seems able to handle this - kudos to the design! An hour
later charging was down to 300 watts and clouds weren't affecting it.
Charging the car with my slow float charging system seems like a good
use of the solar electricity. It could still be tied into a water
heater to good effect, to use up any and all excess power the
collectors make.
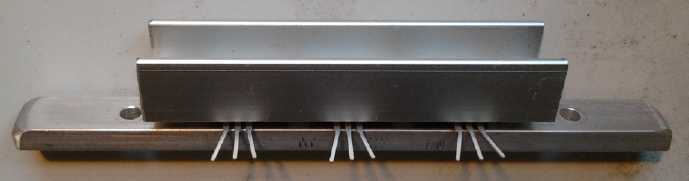
The three dual 20 amp schottky diodes clamped into the assembly.
The fins (seen in the image above this one), made for water pipes,
simply clip into the top square piece.
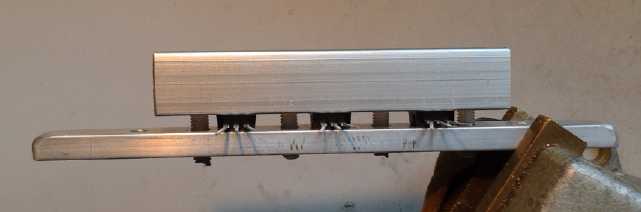
Side view.
At first I was going to have the fins 'live' inside the panel, so here
the metal side of the diodes faces up,
and the machine screws are nylon.
Then I decided that was asking for trouble and put some kapton tape on
the metal
faces of the diodes, to allow heat through but prevent electrical
connection.
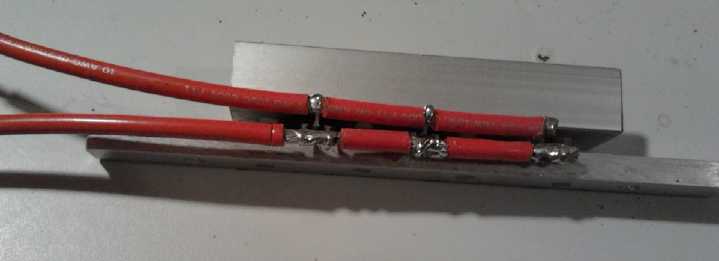
The heavy (AWG #10) wires soldered to the leeds almost touch the bottom
bar, each other, and the top bar.
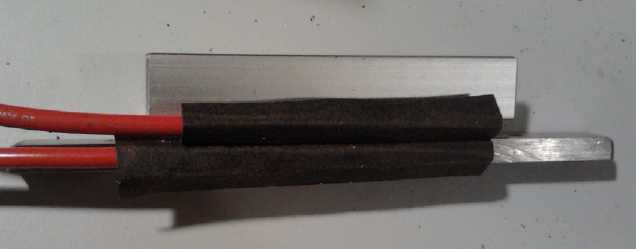
The close gaps made me nervous, but taping and heatshrink wouldn't fit.
So I stuffed in some folded strips of tarpaper.
(My confidence in these is little higher!)
I bought a
new Blue Sea Systems 50 amp circuit breaker to put the inverter on its
own circuit the next night. I trust that's big enough
since 60 amp and larger breakers are not
only triple the price but larger, so they won't fit in my breaker plate
holes. (It should be big enough: 50A*14V=700W, and the car's
charging system as-is doesn't use much above 500W. The four solar
panels are rated for 892 watts in full sun.)
On June 2nd, charging the car at over 300 watts in the
later afternoon, there were 24 amps coming from the collectors via the
buzzing DC to DC converter, and a further 11 amps coming from the
little 32 AH of NiMH's in the solar PV system - 1/20th of the capacity
of the car. Naturally, the battery voltage was dropping as the car
voltage slowly went up. After an hour of that I plugged the car into
grid power so the PV batteries could recover before night. If seems if
I really want to save car charging electricity, I should drive in the
morning, leave it uncharged overnight, or get enough batteries in the
solar PV system to save up electricity for the car charging. That would
be a
lot of batteries. But perhaps it's a good use for the weaker renewed
batteries, and being used might gradually bring them up to fuller
capacity.
(Where are those cheap MnMn batteries?... oh, right, I
haven't had a chance to work on them for two months, and minimal time
for 2 or 3 months before that.)
The problems suggest yet another new product - or a
modification of the "dump load" control - to make solar power more
practical: a solar powered equipment output monitor and control. When
the available electricity is insufficient to get the desired results
and causes excessive input voltage drop, resulting in battery insead of
solar PV power usage, this could take various
actions. For most situations, it could cut the input power to the unit,
making decisions like "It's not working - shut it off and try again in
5 minutes... or maybe in 1 minute if the voltage reaches a higher point
than
before", rather than letting units cut in and out and in
and out or squeal when they aren't actually able to operate with the
amount of power available. A
programmable unit would be ideal since everybody would
would have different equipment and would be doing different things with
it. For the case of an inverter, before shutting power off, it might
try shutting off one or two of two or three receptacles to run some of
the equipment at a time. It might be desired to grant priority of power
by rotating times, eg, as with charging two banks of the car batteries,
or, eg, 'the freezer' might always have highest priority. All such
things might be run similarly to the already conceived "dump load"
feature, and ideally would keep the collector voltage near its maximum
power point. Alarms might be set to alert someone that, eg, "Car isn't
charging" (or "freezer is off"), so they can decide whether to plug it
into the regular power grid instead.
And I still think a flexible input voltage inverter
to run directly off the solar panels would be a good idea - the DC to
DC converter, the isolation diodes, and the inverter are all quite
warm, suggesting there's 100-150 watts being wasted as heat by all the
components to get 300 watts to the car. (where more is wasted by the
power adapter-chargers.) That's a lot of inefficiency overall. If we
assumed every piece was 85% efficient and the diodes 95%: .85 (DC to
DC) * .95 (diodes) * .85 (inverter) * .85 (each charger) = just 58% of
the solar panel electricity getting to the batteries. A "no
inverter" alternative of generating floating DC charge voltages
directly from a DC source would need a lot of extra wiring -
essentially an entire new charging system - and would a high current DC
source be available anywhere but at home?
MSP430
Microcontroller
Software Development
One upshot of my telephone consultation about the Mazda
batteries was that
I really needed that individual battery monitoring system so that I
could tell what was going on while I drove. (Measuring each battery
with a voltmeter after driving soon started seeming pretty tedious.)
That, along with the several other needs I have for microcontrollers,
meant getting a
microcontroller software development system working has become a
priority.
I picked the MSP430 for several reasons. In particular, at a
glance the instructions and registers of the MSP430 series seemed to
be on a par with Motorola's MC6809, which was a definite
improvement over trends to crappy 8/16 bit CPU architectures after the
1970's until just a few years ago. But I found one gaping omission as
soon as I started assembly language programming on it: there's no "load
effective address" (lea) instructions, nor program counter relative
branching and subroutine calls, so it's impossible to write position
independent code. That is, a program will always contain different
numbers if it's assembled at F000 than at F800, and either will bomb if
loaded at the other address. Okay it's a limited purpose
microcontroller that's intended to run a fixed program, not an open
desktop OS... but it didn't really need to have major limitations built
in.
For all the built-in features, hardware things are also
much more limited. Where the 40-pin 1970's chips could address whatever
external memory was attached, the 16- or 20-pin microcontrollers have
whatever memory is supplied internally and no pins to connect any
more. Where I had 8KB of battery backed up SRAM storage for
user-written "control basic" programs and a further 48K of banked DRAM
in my 1986-1988 Micro Energy Manager ("MEM") for extended data
logging, the MSP430g2553 has just 512 bytes. It has 16KB of flash
memory where (IIRC) my unit had 32KB of EPROM. Connecting flash storage
as serial SPI like SD cards etc. at pretty high speeds is some
compensation.
Luckily the things I want to do now are quite limited compared to the
all-purpose, fully user programmable MEM.
Other poorly done things came to light as I
worked. Instead of integer 'multiply' and 'divide' instructions, there
was a hardware multiplier implemented as a peripheral device. That
would have been reasonable - except there's still no divide, and worse,
they didn't put it into some of the chips including the MSP430g2553,
presently the most common version and the one that I'm using. Why not?
It takes no extra pins! I think the last time I had to write "shift
& add" and "shift & subtract" software functions to perform
'multiply' and 'divide' was about 1981 - 3 decades ago. I found no
ready-made code to copy and paste, so I had to look it up on the web
and figure it out again instead of getting on with what I wanted to do.
I wrote the multiply on the afternoon of the 26th. I had the process
clearly in my mind when I wrote it, and it worked flawlessly the first
time. For divide my mind was muddy and I went back to the web. This
time I found both a divide and a multiply, so I just copied and pasted
the divide. The multiply was pretty similar to what I wrote, but used
an extra register.
This "maybe" hardware multiply feature hearkens back to
Motorola always changing and chopping their 6805 microcontroller family
instructions and registers with each new chip, so that if you changed
chips to get some new or expanded hardware feature, you had to rewrite
all your software. They had virtually ideal CPU sets in the 6809 and
68000 and if they'd stuck with them and maintained compatibility with
them as they expanded their microcontroller product line instead of
chopping and twisting, they'd probably still be in business. I suspect
they had one really brilliant guy there in the late 1970's that
designed the architectures of the 6809 and 68000. They probably didn't
appreciate what they had once they had it, and so would have turned up
their noses at any advice he may have tried to offer. Given the
several [so needless!] instruction set limitations of the mostly quite
attractive MSP430's, it still can't be considered as any sort of
ideal of a 8/16 bit rocessor, and I might still take a 6809 based
system if
it was available in a modern microcontroller form.
First thing to get was the microcontroller communicating
to a simple display so one could see what was happening. On the evening
of the 8th I connected one of my old four digit 7-segment LED
"display-controllers" that I made in the 1980's for the Victoria School
District/MEM, to a TI 'Launchpad' MSP430 development board. (It also
has 6 buttons for user input) The next morning I wrote a quick
"bit-banging" program in 'C' to send alternate 1's and 0's to the
display
segments. It worked as expected. This checked out the connections.
At first I thought I'd look up specs and examples of
driving the
MSP430g2553's built-in serial peripheral interface to use it as
designed in the
chip. Then I wondered whether that actually had any real advantages
when the SPI data clock could run as fast as you could send the bits,
and I decided 'bit-banging' would be good enough for the battery
monitor anyway. It's more flexible and for me it had a zero learning
curve. Updating a largely static display 10 times a second probably has
no practical advantage over updating it 7 times a second (or whatever)
anyway.
On the 14th I looked up some of the features of the
MSP430g2553 in more detail. On the 15th I struggled for 2 or 3 more
hours with the frustration of trying to get the C compiler with its
punctuation heavy and inconsistent syntax conventions to do anything
sensible
with anything I wrote myself instead of just a given simple sample
program. The job I'd been struggling with for over a week - sending
ASCII data to a 7-segment display as a beginning exercise and as a
potential debugging tool - was pretty trivial to do in a couple of
hours in assembly language, or in BASIC, in 1983. And, while I've been
told by enthusiasts that C compilers are getting better and better,
"almost as good as
assembly language", I'm afraid I'd have to give the cludjy C compiled
code I saw in the disassembler a failing grade, vis:
clr R15 ; loses the data from R15. Why? just to get a zero.
You could just go setz (set zero flag) and
keep R15.
tst R15 ; Sets the zero flag
based on the zero in R15.
jz somewhere ; jump if zero flag is set (which you've gone to needless
trouble to ensure).
But the whole sequence, repeated over and over, is
redundant: The
MSP430 series has an unconditional "jump" instruction. All that is
needed is the single instruction: jmp somewhere. The compiler appears
to have been written for some 1970's 8 bit CPU with no unconditional
jump instruction (like the 6502), and then it became "set in stone",
piling garbage on garbage instead of cleaning it up. In C it's too much
trouble to clean it up - better to generate obsolete code.
And too often I see subroutines called, with all their
inherent overhead plus
their obsolete "C" 'put everything on the stack' calling convention
overhead (designed for old 1960's -70's processors without enough
registers to pass parameters), which
in effect execute just one or two machine instructions that could
simply have been put in-line. Then there's "include" packages where
only one or two - or even none - of many included functions are
actually used in the program, because in C it's too hard to sort
through them all. All this sort of
stuff helps make "C" programs much larger and slower running than
assembly language.
When I tried to put in some inline assembler in a "C"
program, it needed quotes around each instruction and semicolons
everywhere -- and then the final program compiled with the assembly
instructions omitted anyway.
The whole
computing industry is built around these sorts of obtuse things,
cludjed around until they work.
Finally I got totally frustrated by quirky "C" language
syntax and
usage. It took hours to create a simple array of bytes to convert ASCII
characters to 7 segment diplay bits. First I was using "byte", which I
finally remembered 'C' doesn't understand. It uses the word "char" for
"byte". Then it inconsistently used "char {" or "char ("... depending
on how the following data bytes were described, and I was
following the wrong example! The error messages from the compiler were
so
bizarre as to be pretty much useless. Then when the array was finally
right, I
couldn't get a pointer to
index into that array depending on the ASCII character. Obviously
there's some way to do it but after enough unsuccessful searching, I
gave up on "C". Time to go back to "A" which has always served me well.
I started to think it might actually be easier to write my
own MSP430 structured assembly language software development system, as
I had done 3 times from about 1982 to about 1990 for 6809, 6502, and
68000 CPUs. This seemed to be getting in awfully deep for the limited
purposes for which I now wish to write software.
Finally I decided to first see if I could write an
assembly language only program with whatever given assembler I could
dig up for Ubuntu and avoid C entirely. Some searching on my own
netbook uncovered one that had come with the C compiler: msp430-as.
That
left figuring out how to use it, for which I hunted up some rare
example programs on the web... done with other assemblers that did
things a little differently. The fixes were easier than with "C"
because msp430-as turned out to use mostly the most "normal" expected
syntax, and the error messages made sense. Labels (ubiquitous with an
unstructured assembler) end with a
colon and rigid tab/space delineation of "label: opcode operand ;
comment" isn't enforced, which are my own preferences and make things
less annoyingly nit-picky.
But on the 16th I tried for several hours to assemble a runnable
program. The RESET vector has to be set to direct program control to
your program before anything
else will work, and if it can be done at all, the syntax is somehow
different from other assemblers and nowhere explained. No documentation
nor any examples were to be found. I couldn't get
it to successfully create a workable program no matter how I cludjed
it,
or linked it with the "C" compiler to have "C" set the vector to
something sensible. I could write a program, but I couldn't do anything
to start execution of that program.
A search disclosed another MSP430 assembler, Naken Asm.
The
instructions
said
there
was a Windows version and a Mac version...
but only for a Mac newer than mine. No mention of Linux. Oh well! I
finally downloaded the Windows version to a memory stick and took it to
the clunky PC that isn't web connected, that runs the CNC drill router.
When I read the "readme" file, it said "How to install in Ubuntu".
What?!? I took the memory stick to the Ubuntu netbook. I couldn't get
it to install and spent some more frustrating time trying things and
searching the web for answers. Finally I downloaded it again on the
netbook itself from the .tar file on the web... and then everything
worked
per the instructions.
I assembled and ran the sample program, then before
midnight on the 22nd, over 3 weeks after initially getting the netbook
to send data to the MSP430 board, I had the 7-segment display program
working. Writing the program itself was a 4 or 5 hour programming job.
The last hurdle that ate a
couple of those 4 or 5 hours was that in calling a subroutine, with
the MSP chips having no LEA instructions or mode, the unspecified
addressing mode
for a subroutine call ("call sendSPI") defaults to a weird one that
crashes the program, unless a sign is inserted to specify the mode that
works: "call
#sendSPI". Much of the rest of the time was spent deciding which LED
segments to light for some of the letters and numbers. Coding the
program instructions other than "call" took perhaps the least portion
of the time.
The "call" glitch being the same in all assemblers, by the
time I was done, I was
sure I had picked the best one. On the 23rd I improved "sendSPI"
and made it a callable '.include "7seg.asm"' file for other programs to
use. (I still need to write a callable "readSPI" to read the buttons on
the controller.)
At some point, the four digit, six button
'display-controller' will
be replaced by the final 128x128 pixel color display with the colored
bar graphs and whatever displays, and touch sensitive "capacitance"
buttons, but
this is good for testing and for test versions of, eg, the fridge
control.
Next, reading analog levels was accomplished a couple of
days later. At this
point I decided to tackle the fridge control first, which reads the
fridge temperature and the fridge's own 12 volt solar/battery supply
voltage. Gosh - I'd be able to stop having to manually turn the fridge
on and off morning and evening!
On the car battery monitor, analog levels means battery
voltages. The first
problem was the high DC voltages, up to maybe 160 volts. If the 10 bit
ADC was to measure 0 to 2.5 volts, 160V/64=2.5V. Then what would the
resolution be? 160/1024=.15625 volts per step. That seems a little
coarse,
but lead-acids drop a whole volt or two when high currents are demanded
- and more as their charge drops - so it's probably adequate for
lead-acids. Batteries lower on the chain could perhaps be reduced less.
For
example, the midpoint of 80 volts could be divided by 32 giving .078125
volts per step. But then if the wrong battery is connected to the wrong
input, the unit might be damaged by overvoltage. Dividing them all by
64 has the merits of simplicity and safety. Also , the µC itself
could
easily figure out which battery is which regardless of which one went
to which input, simplifying installation.
Unfortunately the MSP430g2553 chip has only eight analog
ADC converter inputs to monitor typically ten to twelve batteries, or
more for lower voltage batteries, eg, a typical 24 six volt golf cart
batteries... or even more individual 3.2 volt lithiums. Since I'm only
using 9 or 10 ...now 11... batteries, I decided initially to simply
have 8 inputs
with a couple of 24 volt double sections. I'd allow that to be
configurable - 6, 12 or 24 volt sections - at worst problems can be
narrowed down to one of two batteries.
The second problem was that the high voltage drive is
floating. I decided the simple solution would be to have the entire
monitor unit float with it, have a plastic case with no connected metal
on the outside, and power it off the lowest 12 volt battery. (That one
will have to be in the right order in the sequence... or sparks will
fly!)
Electricity Storage - Turquoise Battery Project (etc.)
Prussian blue, ferric additive, barium chloride & barium
manganate
Someone pointed me to some interesting battery research
where the potassium ion from the electrolyte takes part in the 'posode'
reaction. One of the
types used "prussian blue", a rather complex iron-organic molecule
which is usually used as a pigment, but is supposed to have indefinite
cycle life, good voltage, and good utilization if used as a battery
active 'posode' material.
I said I didn't understand the chemistry or
know how to make prussian blue, so next he sent me detailed
explanations. It
looked sort of like English. He may well be onto something good, but
the chemistry and crystallography are over my head. Perhaps I
could run it by my biochemist brother and attain some glimmer of
understanding. Article: http://en.wikipedia.org/wiki/Potassium-ion_battery
The makings of
the other
type were along more familiar lines. It was an iron-zinc dry cell,
using higher oxides of iron: Fe2O3 (ferric
oxide) charged to K2FeO4 (potassium ferrate). This surprised me since
I thought ferric oxide was an insulator and couldn't be used in a
battery. But they note "...the high impedance of the discharge
products..."
so it sounds like K2FeO4 must be more conductive, and perhaps they were
intending non-rechargeable cells.
On the other hand, it's quite similar in form to my use of
MnO2 (manganese dioxide) charging to KMnO4 (potassium permanganate).
While K2FeO4 is apparently stable, K2MnO4 (potassium manganate) is
unstable - it forms stable permanganate instead - which also moves a
third electron, upping the amp-hours per weight.
According to their graphs, they also tried using barium
instead of potassium, and it actually gave somewhat
better results - higher voltages,
higher energy density and better active material utilization,
approaching 50%. This seemed exciting. For my cells, that would imply
using barium chloride
[BaCl2] for electrolyte instead of potassium chloride [KCl], with the
MnO2
charging to BaMnO4 (barium manganate). BaCl is about as soluble as KCl,
and the charge
product BaMnO4 has the advantage of being insoluble as well as stable,
where KMnO4 is slightly soluble. BaCl can be made
from BaCO3 [pottery supply] and HCl acid [hardware store].
The researchers found the voltage of the K2FeO4 makes an
alkaline iron-zinc cell of about 1.5 volts.
Although not the real idea of the article, I can easily
try adding some ferric oxide powder, or perhaps some ferric chloride,
to one of my positives and see if it has any notable effect.
abstract: http://www.electrochem.org/dl/ma/206/pdfs/0477.PDF
A feature of all
these types including mine is the charging and discharging of the
potassium ion (...or barium ion) from the electrolyte. This may
happen in nickel-whatever battery types too: Ni(OH)2 -> NiOOH ->
K(NiO2)3. The various aspects of these researches could bear some
scrutiny. I think I'll try the barium chloride (hmm... what about
strontium chloride or calcium chloride?) and ferric whatever as an
additive. The troubles are (a)
finding time to do these things and, perenially, (b) having no
consistent, working control standard against
which to measure the results.
NiMH Batteries
NiMH Float Charging Voltages Revised
When I put the first
60AH NiMH battery in the electric Mazda RX7 I didn't get as much out of
it as I expected. I used a 'regular' charger on it to see if
it would hold more charge after being charged to 14.2 volts and then
the charge stopped, instead of with a steady 13.9 volts, the float
charge. Its voltage/charge did indeed stay much higher over
more extended driving.
This seems puzzling to me since they soon drop below
13.8 volts no matter how they're charged, but it's hard to argue with
the results. This seemed to smear my whole float charging philosophy!
So I
soon tried charging some to 14.00 volts on the lab power supply, and
found the current dropped to well under "c/50", or 200mA for 10AH D
cells, once they were pretty well charged. c/50 is the accepted "okay
to leave
on charge forever" level for NiCd & NiMH dry cells. Apparently I
relied too much on my initial
rather quickly done test conclusions from about 2-1/2 years ago,
without ever rerunning them to verify the results.
13.8 or 13.9 is okay
for a gas car starter
battery, because it never gets drained down too far anyway, but if you
want to obtain a fairly maximum charge, it's a bit low and it only
charges up to 1/2 or
2/3 the rated amp-hours. Using approximately the same test procedure as
in 2011, I obtained the following apparently 'steady state' currents
with different voltages on a D cell
battery (the current readings are very rough, but indicative):
14.00 - < 30mA
14.05 - 60mA
14.10 - 150mA
14.15 - 200mA (c/50 - the max)
14.20 - 300mA (too high for float charge)
The current at each voltage was
somewhat lower than I expected recalling my first tests a couple of
years ago. Evidently my whole scale needed to be
raised about .2 or .25 volts (.02 to .025 volts per cell), to an
optimum of 14.00 to 14.05 volts. Those would leave a small margin for
error in case of voltage drift, current change with temperature, and
tolerances of the voltage setting components.
This also explains why the solar PV system battery storage
wasn't lasting as long as it should have been. I raised the DC to DC
converter voltage to 14.4 volts, to give the batteries (through a
Schottky diode) about 14.0.
The higher voltage in turn will mean higher currents to
the fridge, which may mean two 15v peltiers in series will make enough
ice to run
the fridge at a lower power, at maximum efficiently.
More 12V NiMH Battery Sticks
Unfortunately the 4.5 hour prints
of the square battery cases are to some extent matched by considerable
labor to put together a large cubical battery in this format. If I took
most of my D cell batteries, I could make three more 60 amp-hour
batteries for the Mazda.
And I also still had enough PVC pipe to make them all as 12 volt
battery sticks. If I made a big ventilated wooden box sized to fit
across the front of the car, I could put the tubes in it and eliminate
three
lead-acid batteries and half of their weight, which was pressing the
front springs down to the max, especially the left one. (I think
the left front spring was weakened in the accident the car had before I
had it.) It might save around 70 pounds. Then,
two of the lead-acids to be removed worked better than two in the rear
which could then be replaced, and the whole pack - 4 NiMH of 60AH and 5
(or more) PbPb of around 90AH (that actually work well) should give
substantially more range.
Making two would have been simpler since I was scrounging
up my last D cells for a third (240 cells overall for all four), but
the advantages
of making a (75 pound) box of three rather
than two were that the "-" would be at one end and the "+" at the
other,
rather than both at the same end, and it wouldn't reduce the front end
batteries from 5 to 4 -- the
box takes up almost the length of 3
PbPb's regardless of how many tubes it contains. Even well packed into
a box, the battery
pipes take up more room than the stacked cases. With all stacked
cases, I could have upped the batteries under the hood from 5 to 6.
I cut the plastic pipe and end caps on the 11th for almost
enough tubes, then outfitted 7 of them. I had forgotten just how fast
and easy it is to make them up. That used up all my free D cells - and
a
6v unscrewable pipe with 5 more.
The next day I unsoldered the remaining 30AH
soldered-together vehicle battery. It had two broken solder connections
- reason #1 for why that's a poor way to make a battery. (#2 is in the
article below.) So no wonder it
barely started the truck! I put those cells into three tubes, and took
the two 12v tubes from the solar system, giving 12. I tested
them all, and found the soldered ones I'd just done had poor
connections. I broke open one end of each, scratched and rubbed the
soldering flux off both ends of each and every cell, and reassembled
them, with better results. But on a couple if not all three it seemed
the ends hadn't been properly pressed together (since they were just a
little shorter when assembled the second time), which probably explains
the problems better than some flux. Or maybe the flux itself made them
longer by enough to notice.
Then I made a new box of figured lombardy poplar and
plywood, sized to hold the 18 tubes and to fit under the RX7 hood as
required. It was barely tall enough to hold all the battery pipes and
it barely fit under the hood at the front.
For the last 6 tubes, rather than disassemble almost every
other battery I had or remove the one just installed to get 60 more D
cells, I decided to use the battery made from
twelve 6v tubes (last used in the boat for the Electric Caik Outboard)
for the time being until I had money for another order of batteries. I
removed it from its box, and on the 13th assembled everything. I had
made the new box a little longer in order to accommodate them.
Another Soldered NiMH Battery Pack Disaster
The 1500 watt inverter and the DC to DC converter in the
solar PV system were interacting strangely, and one day, I heard a bang!
from upstairs. The DC to DC converter had gone into its wild mode,
putting out as high a voltage as it could instead of 14.35 volts. This
puts far too much current into the batteries and has caused trouble in
the past. As with the soldered-together 60 - "4/3 A" cell pack, the 120
- AA cells got so hot their plastic cover sleeves melted, and the metal
cans started short circuiting together. As soon as that happens, they really
start making heat, which melts more and more sleeves, and they started
exploding. I flipped the solar panels breaker off for whatever help
that might be, grabbed a bucket and filled it with some water, grabbed
a full face shield, and ran back into the room, where these
firecrackers were now going off every few seconds. I ripped off the
alligator clip cords that I've been using to connect whatever batteries
happen to be connected to the PV system, picked up the melted case, put
it in the water, and took it outside. The cells from the D cell battery
sitting on top of this one (which had no lid) were scattered around,
and I even
found one empty AA outer shell in the paper tray in my printer on the
other side of the room.
This should be my last lesson on not making batteries with
the cell cases touching each other, because it was my last
soldered-together battery. (Well, except a couple of small ones in
electric drills.)
I've already taken all the soldered-together D cell batteries apart and
used the cells in safer arrangement batteries.
The other lessons that I have yet to act on are to enclose
the batteries in a box... and to put in a mains backup power supply
that can't raise the battery voltage up to or above what the Zahn puts
out - that's what sets it off. Or the new inverter. I try to watch the
Zahn converter, which
usually works great, and to not have the unregulated mains backup power
supply or the inverter plugged in
when nothing is running (ie, when the fridge is off), but you can't be
everywhere and remember everything all the time. Moving the inverter to
the battery side of the diode appears to have stopped most of
the wild
interactions.
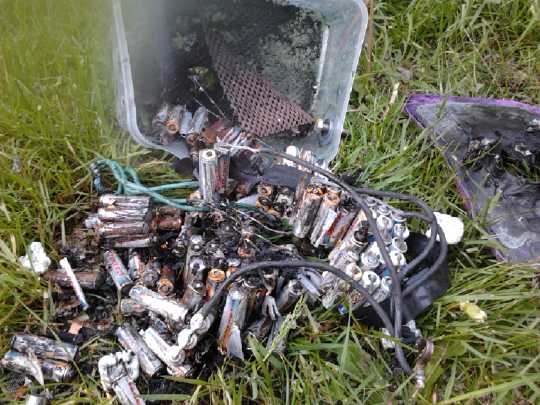
12V, 30AH, 120 NiMH AA cell battery afterwards on the lawn.
Even then, when I moved them around, some touched each other and
started hissing.
So I cut all the interconnection wires before bagging them and throwing
them in the garbage.
(NiMH's are environmentally benign for disposal, "green".)
I wore safety goggles and washed caustic potassium hydroxide off my
hands a few times while handling them.
http://www.TurquoiseEnergy.com
Victoria BC