Turquoise Energy Ltd.News #12
Victoria BC
Craig Carmichael - February
9th 2009
Contents:
January in Brief
(overview... summary... the short version!)
* or, this TOC is the Super Short
version...
Electric
Hubcap Car Drive Project, Longwinded Detailed Report
* Electric Hubcaptm
is (today) ready to test
Turquoise
Battery Project, Very Longwinded Detailed Report
* Interesting Chemistries Emerge
* University Battery Researcher to run
performance tests and evaluate my Electrodes
January in Brief
This month is the
anniversary of starting on the batteries. A year ago I was looking for
good batteries to use with the motor concept that became the Electric Hubcap.
The NiMH batteries of GM's EV-1 sounded great until I found that Chevron
et al had seemingly hijacked Cobasys, the new company that had started
making them, buying up the shares and then quietly making the batteries
unavailable.
That got me going and I spent January 7-10th (2008) on the web trying to
see if making Ni-MH batteries at home looked potentially doable. I thought
the potential was there, so I started ordering chemicals, then I got into
even more promising looking chemistries. But I had a lot to learn about
electrochemistry and batteries, and it's taken a year to more or less nail
down all the basics.
After a few months on batteries with nothing that worked acceptably, I
decided it was time to do the car motor, planned vaguely since about December
2007. That, at least, I thought I could have working soon enough. It turned
out I had a lot to learn about synchronous permanent magnet motors, too!
A few motor and motor controller designs and variations later I did get
a prototype to move the car, but not until October. Then, what with cold
weather, various things and perhaps some project "burnout", it seems to
have taken about an extra two months to get the "production prototype"
on the car to test, which I've just finally done today. Now I'm very nervous
to connect the batteries and see what happens!
Having already seriously trespassed on February -- thinking I'd have the
car running on electricity and to be able to say at least a few things
about it -- I'm sending this newsletter now, and God willing, for the next
newsletter (in under [3] weeks) I'll have some good details!
The Electric HubcapTM
Vehicle Drive Motor
January Gory Details
In marine thought,
gasoline and electric outboards are considered to be equivalent with a
ratio of horsepowers of 2.5 to 1. (Diesel is 4 to 1.) My car is "62 HP",
but it pings like crazy if I push the pedal more than half way, so perhaps
I really only use 30 HP. IF one can apply the 2.5 ratio to cars, then 30
HP over 2.5 means a 12 HP "typical" electric motor. If the Electric Hubcaptm
is a further 1.5 to 1 ratio, that's 8 HP. That would require two of them.
On the other hand, it's said that 10 HP is needed to move a car along a
level highway at highway speeds, that reduces to 4 HP for a typical electric
motor then to 2-2/3 HP for the EH.
Without being more sure until I've tried one out, I'm anticipating that
one EH will drive a car, though performance may not be spectacular. Two
should give it very good performance.
Although I feel I'm six weeks behind, January saw testing the new motor
stator and repaired controller on the bench, breadboarding and testing
then making the new control circuit with the low frequency pulsing to protect
the motor at stopped and very low speeds, Searching out a new rotor with
a better shape for the magnets, mounting magnets on it, rewiring the car
and a new aluminum wiring box for better heat dissipation.
The new control circuit uses just three standard chips to provide pulse
width modulation, the low speed protection, and forward-reverse: basic
motor operation. I thought that was a pretty lean design, however, when
I counted up all the discrete supporting components - resistor, capacitors,
diodes and a transistor - there are thirty of them! But it works, so the
microcontroller version, a project in itself with the required programming,
can wait a while.
The "new" rotor (from the garbage at some brake shop - I think it's
a Subaru rotor) is a much better fit. I also finally found the long lug
nuts I've been looking for - lying on the ground at an outo wrecker's.
I was having such trouble getting what was needed that I had got as far
as buying hex rod and a 12mm tap and making two myself - ugh!
Previously, the rotor went onto the wheel, then long lug nuts went on,
sticking out past the ends of the bolts to extend the lugs, and the rest
of the motor mounted outside of those nuts via short bolts fitting into
them. That meant to remove the magnet rotor required jacking up the car
and taking the lug nuts off. With the new rotor, everything mounts outside
except the wheel, so the tapered nuts go into the wheel properly and they
don't have to be removed to take the whole motor off. And it's about three
pounds lighter.
The car rewiring was overdue. I'd used #10 wire when I was going to use
120 volts DC, and it was too thin when I decided I'd be more likely to
live through the
project if I used 36 volts with triple the current. I
went up to #8, which should be adequate for the three foot run. #6 would
have been better, but it was just Soo heavy looking, and would need such
big holes and clamps, that I set it aside. Some of the connections from
the front of the car had to be changed for the new PWM control too. Now
there's nothing up front except the rheostat under the gas pedal and the
Forward-Off-Reverse switch beside the gear shift.
As long as I was rewiring so much anyway, I decided to change the wiring
box mounted in the car. The old, steel, one by now had a lot of holes from
various designs but none (and no room for one) in the bottom corner to
bring the motor wires in by the shortest route. And I wanted it to be aluminum
to help disperse heat from the power MOSFETs in the motor controller.
All in all, there was a lot more work to getting the new version motor
on the car than I'd anticipated.
As a final thought, I've noticed a minor disadvantage to the axial flux
motor design: owing to the tremendous attraction between the rotor supermagnets
and the stator iron, there'll be a lot of sideways pressure on the inner
bearing. The pressures can be balanced on a radial flux machine. For the
future, I may consider a tapered trailer axle with a larger bearing on
the inside, even though it's just holding a 30 pound motor stator and not
half a trailer plus whatever it's carrying.
Electric Hubcap Motor Factoids: (Deleting this: please see "About Electric hubcap" web page)
Turquoise Battery Project
December Gory Details
In the battery field,
this month sees a lot of ideas and some new chemicals. They make this write-up
quite long, but with trying to push the motor towards "finished" and "tested",
not much actual battery work has been done.
It also sees a university battery researcher volunteering to test a few
of my electrodes and seeing if they're as good as I think, decent, mediocre,
or if I should scrap the works and stick to electronics. He'll also be
able to test electrodes individually, which I can't, and so he may find
one is good but the other has problems.
I'll also send him some electrodes made with chemicals I write of below,
in particular the calcium and the titanium, which look very promising in
alkaline solution, which is what he works with. I may try antimony in neutral
solution myself.
Lead-Acid: Sum Current Thoughts
It appears that one
Electric Hubcap motor would require more lead-acid batteries than I'd hoped
in order to be really practical. Each battery, even if capable of supplying
hundreds of amps, only wants to put out a very limited amperage over any
extended period of time, thus needing two or more batteries in parallel
instead of one, to avoid being "empty" far sooner than it should and having
a much shortened cycle life. (Look up "Peukert's
Law" of lead-acid batteries if interested.)
I have three 50 pound, 100 AH, 12V, "deep cycle" batteries that will put
out "625 amps". In fact, the amp-hours rating is for gradual discharge
over 20 hours (ie, 5 amps), and discharge even at 25 amps reduces the available
amp-hours to around 70. At 75 amps, it's down to 50 AH, ie, 40 minutes
of (highway?) driving. (Furthermore, lead acid batteries lose cycle life
if they get anywhere close to fully discharged, so one should switch to
gas well before the indicated time. Thus, 30 usable amp-hours is a more
realistic rating with only one set of three.) I didn't take this halving
of capacity into account in my price comparisons a couple of months ago!
On the other hand, some of them are rated for up to 600 cycles if discharged
by 60% or less each time, whereas I based my previous economic expectations
versus gasoline on 200 cycles.
It all means that rather than simply having three batteries weighing 150
pounds to get 36 volts, to be practical it should have at least double,
300 pounds, or better 450 or even 600 pounds of lead-acid batteries, even
without needing the extra driving range all the "extras" would bring. (It
partly depends on what the "average" current draw of the motor in "typical"
driving conditions turns out to be, eg 45 or 70 amps.)
It would seem that lead-acid is quite a delicate battery chemistry that
needs to be carefully nursed along to get anything even approaching the
full specified value and life out of it!
Someone asked "What about using Ni-MH "AA" cells?". It's been done to run
a car, and so has 3000 "C" cells. But let's compare instead with solder
tab "D" cells: 10 AH, 1.2 volts, so 12 WH. (Those are the biggest "economically"
available Ni-MH's since Chevron and friends abducted Cobasys. "AA"s are
1/4 that size.) The "D" cell is likely to put out about 10 amps max, so
for 100 amps at 36 volts, 10 wide x 30 deep = 300 cells: $3000, for 3.6
KWH. This is minimal, like three lead-acid batteries. Again, they would
be happier putting out one, two or three amps over time than 4.5 or 7,
so 450, 600 or 900 cells would be more effective. According to web sites
selling them, they'll recharge "1000 times". No doubt they'd last considerably
longer than lead-acid, but like them, attaining the "1000 x" probably has
some conditions. Lithium cells appear to be even more expensive.
The lead-acid batteries might be $150 each, so nine is $1350, for (100
AH * 12 V = 1.2KWH, * 9 batts. =) 10.8 KWH. (10 KWH of large Ni-MH
batteries probably would be about $3000 (300 $/KWH) at fair market price.
I'm not sure what happened to Ni-Cd's: I think they're available somewhere.
If the recycling program is good, there should be little objection to the
cadmium.)
Better
still, I just bought one of the batteries new for $49.95 ("factory seconds"),
not $149.95, which triples the economy! (Hah! -- Try finding a bargain
on gasoline in Victoria!)
Herein, in the absence of big Ni-MH batteries, is why most people that
convert a car to electric are still using lead-acids! 1/2 the price * 3
x the energy / 1/3(?) the life = still 2 x more miles for the same cost.
(And withal, they still look cheaper than gasoline... even without bargain
prices.)
And of course, herein is also why I'm trying to make better big batteries,
lighter, more robust, and economical.
Car Battery Design Principles
The above discloses
that the main need is lighter batteries, yet capable of delivering sufficient
average continuous AMPS during driving, rather than AMP HOURS. Any batteries
able to deliver sufficient amps are likely to also have enough amp-hours
for a "typical" day's driving by the "average" driver, and beyond that
there's the car's original engine. If we can obtain 50, 75, 100, 150, 200
or 500 milliamps per square centimeter of electrode interface without stressing
the battery, increasingly lighter batteries can be used. Lead-acid and
Ni-MH prefer to run in the lower tens of mA/cm^2. Lithium is in the ones
range, so it is generally made as thin film electrodes folded or wrapped
up many times to increase contact area. The newest fuel cells and some
zinc-air batteries under development obtain up to 200 or 250 mA/cm^2, but
again would work best delivering much lighter loads.
The bulk of the batteries is of little import, only the weight. So, a fluffy
material that delivers 500 WH/Kg is in principle as good as a dense material
with that spec, except insofar as adding bulk will to some extent increase
the weight by increasing the case and constituent sizes.
Other well known principles are that the batteries should operate well
in any state of discharge and should be amenable to random bursts of power
and bursts of charging during braking. For these, lead-acid and lithium
cells are generally poor and Ni-MH are best.
If batteries can be recharged in ten or fifteen minutes, or if enough energy
can be stored for a full day's driving in a reasonable weight, new possibilities
are opened for driving on long trips without gasoline.
I have only recently fully appreciated that reaction speed is the most
important design factor, and I'm now on the quest for more AMPS from any
given electrode surface area. I'm by no means convinced 100+ milliamps/cm^2
of efficient, continuous output can't be done. An alternative is wrapped
up electrodes to gain interface area in a small space, but I wish to avoid
that alternative for batteries I hope can be made without setting up a
complex factory.
Voltage Limits
When I started, in
my ignorance I had hoped to use lanthanum as a -2.8 volts negative electrode.
Then in my ongoing studies, I found that water - H2O
or HOH - dissociates into H+ and OH- ions starting at 1.23 volts. But evidently
it's doesn't get very serious until 2 volts is reached. Any substance with
a reaction over 2 volts - and there are actually quite a lot of them, eg
aluminum at -2.3 volts - will soon discharge itself to its unenergized
form. Lanthanum ingots gradually turn to La(OH)3 in
hot water alone. Aluminum fizzes away in alkali solution and gets very
hot until it's all converted. The heat shows aluminum Has a lot of energy,
but it can't be used the way we want. A white powder (Al- or La-(OH)3)
is left on the bottom in both cases.
So I started looking for reversible reactions of around 1.5 volts, thinking
of a battery of around 3 volts. (In fact, some things I wrote below reflect
this.) However, I've belatedly read that when water hits about 2.4 volts
or so (depending on temperature), it starts electrolyzing (one might say
charging) into O2 and H2 gasses.
So the upper voltage limit for a water based cell overall is evidently
about 2 volts. Unless my "voltage ramp"/"ion exchange" idea doubles that
(I do have some hope of that) or somebody can suggest some novel solvent
(preferably non-flammable) with a higher breakdown voltage than water that
will still deliver a lot of ions quickly, perhaps I'll have to stick to
substances totalling below that voltage, perhaps two that are about +1
and -1 volts.
Notwithstanding the limitations imposed by even two volt voltage restrictions,
I keep finding lots more promising looking things to try that seem to have
never been tried. (I wish somebody would write a paper on "Battery Designs
that Didn't Work". It could perhaps save a lot of trouble if some of what
I want to try has already been tried somewhere! Maybe by the time I'm finished,
I'll want to write it myself!)
Electrode Separators
I knew Cellophane
was used as a semipermiable membrane and should be good, but I wasn't having
any luck with it myself. Soaking it in a solvent wasn't working. For one
thing, I had tried wetting it with solvent for a minute or two, but it
turns out it takes 15 to 45 minutes to absorb it. Apparently much slower
than a paper towel with water! For another, the last solvent I tried, that
(finally) worked to some extent, was a spray with lubricant in it.
I now suspect oil or grease smeared on it will act as an interface to let
things pass through, but haven't had time to try it out yet.
Having just sold a remaining Supercordertm,
a clarinet-like recorder (duct flute) instrument I designed and built a
few of from 2003-2006, I've bought the last (I hope) expensive chemical
I've wanted to try out in the batteries, osmium, to "dope" the cellophane
separator with. Of elements that are actually present on Earth, osmium
is the second rarest, beat only by its neighbor iridium, but it looks like
it should pass protons like nothing else.
I had also, ever since I started, been trying to think of a good non-woven
textile that might be available for a separator. Aside from uggy fibreglass
mat, there's polyamide, but I couldn't find it for quite a while. Even
phoning Dupont where it's made no one seemed to know anything about it.
Turns
out you don't ask for "polyamide" unless you just want blank stares
- you ask for "fusable web" cloth in any old fabric store. Then you look
at the label and it says "100% polyamide". What I found is pretty thin
- you'd need a half dozen or so layers to be safe, I'm sure.
But the cellophane has more promise to split the battery into two halves
that can each handle up towards 2 volts, for a cell of around 3 volts.
Zinc
There's theory, and
then there's what actually happens. Zinc is right above cadmium on the
periodic table. The electrochemical reactions look pretty similar as shown
in "standard electrode" potential tables:
Cd + 2OH-
<==> Cd(OH)2 + 2e- [-0.81v]
Zn + 2OH-
<==> Zn(OH)2 + 2e- [-1.24v]
But it turns out that's not what actually happens with zinc! Instead, unless
the electrolyte is exhausted, the zinc hydroxide continues to absorb hydroxyl
ions:
Zn + 4OH- <==> Zn(OH)4--
+ 2e- [-1.28v]
We've still
moved two electrons, but we now have dissolved zincate ion instead of solid
zinc hydroxide. This is where zinc gets its troublesome penchant for moving
around and (without design precautions) growing crystal "dendrites" and
shorting out the battery after say 10 to 50 recharges. But that's not the
end of the reaction. The zincate ion then spontaneously turns into zinc
oxide, again a solid, and gives up the two extra hydroxyls (again without
moving any more electrons):
Zn(OH)4--
<==> ZnO + H2O + 2OH-
So
the overall reaction, indirectly and not very intuitively, is:
Zn
+ 2OH- <==> ZnO + H2O + 2e- [-1.28 volts,
I presume]
An interesting point
about this for a Ni-Zn battery is that the nickel creates water from OH-
ions when charging while the zinc creates it while discharging, which should
keep the electrolyte level and concentration constant, as is also the case
with Ni-MH. With Cadmium, there'd be more water in the battery when it's
charged than when it's discharged. There can be too little liquid left
in a discharged Ni-Cd dry cell, which may contribute to or account for
its problems with shorting after sitting too long or otherwise being completely
discharged. (Add some more water and I suppose you can have it burst when
it's charging, instead!) It
also means calcined zinc oxide ("denzox") from a ceramics supply should
be good stuff as-is! The calcium should be a good additive.
It's good news for limited production as anything coming from a ceramics
supply store will probably be considerably less expensive than a similar
chemical from a chemistry supply and locally obtainable, although the purity
is usually less.
Magnesium
Looking for interesting
possibilities for electrode materials, again the theory and what actually
happens can be two different things. An interesting magnesium reaction
shown in a table for an acid electrolyte battery is:
MgO(s)
+ 2H+ + 2e- = Mg(s) + H2O [-1.722 v]
That's a great voltage, not too high for water electrolyte but has a lot
of energy.
Looking further, however, one discovers that MgO in aqueous liquid will
turn into Mg(OH)2 spontaneously, a reaction with a
voltage potential that is too high to use - it won't stay charged. That's
the opposite of zinc, where the hydroxide (ion) becomes oxide unasked.
Manganese
Manganese is used
for most simple one-time batteries. So-called carbon zinc is actually manganese-zinc
-- the manganese oxide, a poor conductor, is mixed into graphite (carbon)
to increase the conductivity. One-use alkaline batteries are also manganese-zinc.
Manganese has a really exciting looking bunch of reactions that seem to
hold a lot of promise, but as one delves deeper, one sees that to use any
desired one, it would actually be hard to prevent any unwanted ones from
happening both in charge and discharge.
Better to find elements with few, distinct reactions, where one of them
is a good one!
Zirconium
I've been sprinkling
zircon (zirconium silicate, ZrO2:SiO2),
on the surface of the zinc electrode before placing the separator in the
attempt to stop ion migration and hence zinc dendrite growth. Evidently
it's been done before, although with the oxide (which as usual - and unlike
the zinc - becomes hydroxide in an alkaline electrolyte), and in a different
(primary) battery. "...our
recently demonstrated zirconia hydroxide-shuttle overlayer, which stabilizes
alkaline cathodic charge transfer chemistry, 3 also is demonstrated to
prevent corrosion of the boride anode."
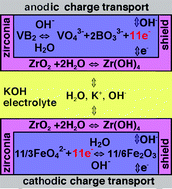
When I found
a patent for a cerium-zinc battery with an acid electrolyte, I thought
that perhaps the patenters could have used zirconium instead of zinc, since
zinc loses almost 40% of its voltage (and hence energy density) in acidic
electrolyte as opposed to alkaline.
On the other hand, zirconium's voltage in alkali is too high, and putting
it in acid reduces it just enough to make it work in a water based electrolyte
- in theory - with exceptional energy. In fact, there are several acidic
reduction reactions listed, all starting with zirconium metal and all about
-1.5 volts. It almost might not matter which one actually takes place,
except for any reaction making ZrO2 or other electrical
insulator that would hinder recharging, and migration of ions (with the
same challenges as zinc) or other untoward effects.
IF it works, then with a positive electrode of similar potential (eg the
+1.7v of the cerium in the Ce-Zn cells), cells around three volts would
be obtained - a voltage range currently "owned" solely by lithium battery
types.
Not knowing enough electrochemistry myself to be sure, I enter into a shady
realm of possibilities:
a) The patenters were fully occupied trying to make the cerium side work
and they didn't even think about trying anything besides zinc.
This is quite likely, especially as they speak of zinc as being the
commonly recognized highest energy electrode substance, without
discussing its lesser energy in acidic solution.
b) They dismissed it knowing it wouldn't work for some reason.
This is also quite possible.
Given a good chance it was (a), zirconium could, as far as I can tell from
the paucity of web search results:
c) not work anyway for some reason.
d) work fine but no one has explored it.
e) work fine but only in some more complex form, for example as a
chelated metal, which avenues no one has explored.
So my dillema now is: is it worth trying? One can of course run so many
experiments in trying to attain "the ultimate" in possibilities that one
simply burns out without ever achieving a marketable product. Better a
two volt battery than none!
Unless it simply works flawlessly or quickly looks like a total flop, the
logical result of the first inconclusive experiment is to try more experiments
to improve it, turning it from seemingly trying out one simple thing into
a whole new area of exploration in itself. And that can get complicated.
As with zinc's ion migration and resulting dendrite growth problem, zirconium
may have unique vexations that can only be tackled with more experimentation
that could potentially take years.
After all, I started out simply to make Ni-MH alkaline batteries before
I saw what looked like some very tantalizing possibilities. If I had just
stuck with Ni-MH, there's a fair chance I'd have had working batteries
by now. (This is a very good reason to just use zinc or other known electrode
material and not think about anything else while you get the cerium - or
in my case now, lanthanum or dysprosium - to work!)
In a best case scenario, the zircon I'm sprinkling on the zinc anyway will
work as a binary system with the zinc in the lanthanum/perchlorate battery
and the anode will charge up to the zirconium voltage. Then it'll be just
a matter of finding best proportions, perhaps mixing some zircon in with
the zinc. Otherwise,
I've found sone more things of good promise, below!
Antimony
In a web search, I
found that mineralogists had "discovered a rare inorganic cation", positively
charged antimony oxide hydroxide, in a clay.
This caught my attention. Could "Sb" oxyhydroxide replace "Ni" oxyhydroxide
in alkaline batteries? If so, would it have a higher voltage or other advantage
such as better conductivity (for more milliamps per square centimeter)?
Had anyone ever tried it?
I got some antimony oxide at Victoria Clay Arts, originally as a minor
zinc electrode additive, but I may try it out as a positive electrode of
its own some time. Antimony looks like it'll work better in a neutral solution
than in alkali.
Calcium
After finding the
antimony, I thought a good survey of the elements using "webelements" (.com)'s
redox diagrams might reveal more. I found barium had interesting possibilities:
specifically, barium hydroxide, charging to either barium dioxide or barium
oxyhydroxide. But a bit more searching showed barium hydroxide as being
rather soluble in water. However, it seemed that barium, strontium and
calcium had identical redox diagrams with almost identical voltages.
Could it be? Yes! Calcium hydroxide is little soluble. It would appear
the common lime atom may well make an excellent +1.5 volt potential electrode
in alkali or neutral solutions. (If I really must stay below two volts,
I'd have to find something crappy for the negative side!)
The trick with calcium hydroxide is to keep it away from air, as it will
spontaneously react with CO2 to become H2O
and CaCO3 - which is the form in which it must be
purchased. This is gradual as there's only a trace of CO2
in the air, but it means a sealed battery would be vital.
Changing CaCO3 into Ca(OH)2 is
a two step process: heat it to several hundred degrees, eg 1400 F. This
splits it into CaO and CO2, a process that emits a
bright light: limelight - you've heard of it! Then put it in water. As
mentioned with some other things, the voltage of the reaction causes it
to turn into Ca(OH)2 by itself. Put that in a sealed
jar until you're ready to make the electrode and put it into the sealed
battery!
Other
questions are how conductive and how dense the substances are, which reaction
will actually take place, and how much it might change size when charging
and discharging. If, for example, the hydroxide is 'fluffy' but the oxide
is 'dense', the electrode will do a lot of heaving around when in use,
which may greatly reduce cycle life and-or performance. Ideally they'll
both be the same size.
Titanium
Also in the elements
survey was titanium, just two elements beyond calcium (elements 20 &
22), as a possible negative electrode. Unlike most of the other candidates,
it's not shown as converting to a hydroxide, just to oxides. TiO2
is used in food colorings, cosmetics, paints and pottery glazes. The voltages
of these are rather surprising in alkali, and should result in an
electrode very forgiving of over and undercharging. The discharged state
would be TiO2 (Ti at valence IV), which will discharge
no further, and which would charge to Ti2O3
(III) with -1.38 volts potential. If this was seriously overcharged, it
would convert to TiO (II) at -1.95 volts, and even more voltage (-2.13)
could make it Ti metal (0). None of these states have dissolved ions to
allow the zinc problem of dendrite growths, and -1.38 volts is very close
to zinc's -1.28 volts.
Those two forms, especially the last, would quickly self-discharge in water
(to Ti2O3). But those reactions
should keep things below the 2.3 or 2.4 volts where water starts to make
a lot of gas (H2, O2) and builds
up strong pressure inside the battery. They should eliminate the need to
add other elements to the titanium oxide to perform that function.
A couple of other interesting things about these oxides are that the two
of interest are about the same size, meaning it won't shrink or expand
as the state of charge changes, and the the charged Ti2O3
is "violet-black", unlike the other - and many other - oxides, which are
whiteish. According to one battery researcher, "black powders are usually
good conductors". If that holds true, it should mean an excellent rate
of charge and discharge when the battery is in the upper area of its charge
state -- perhaps that continuous 100 mA/cm^2 is attainable with titanium
in alkali!
I should note, however, that the titanium reaction only moves one electron
where the zinc one moves two, so titanium's amp-hours per kilogram rating
is lower.
In web searches,
I find many of the above chemicals are mentioned as exciting materials
for lithium batteries, though not in other battery connections. I suppose
it could be it's all been tried before, but personally, I think major battery
research of such an experimental nature wasn't done earlier and now everyone's
excitedly experimenting inside the lithium box and they don't look beyond
that. It's probably a lot easier to get funding specifically for lithium
battery research at the moment - it seems to be the "in thing", hence,
that's where the research goes.
One must narrow one's focus, but not into something with obvious drawbacks
without first surveying the possibilities and seeing if simple things of
promise have been overlooked, as they so often are.
The Electric Hubcap is a good example of "missed simplicity": Automotive
mechanical transmissions and drivetrains have been the subject of much
design effort over the decades, and yet they are still complex, heavy,
inefficient mechanical monsters. A motor directly turning the wheel - what
could be simpler? - would render all automobile transmissions entirely
superfluous. The entire motor is lighter and simpler than the transmission
in the drivetrain. But the whole thing was missed until now owing to everyone's
narrow "in a box" focus on refining the complexities and nuances of automotive
drivetrains. The combination of a PMSM and axial flux to provide such strong
low RPM torque that it can directly turn a car wheel enables a fundamental
change. (Today's computers and software are chock full of fabulous examples
of missed simplicity from one end to the other, but I digress.)
Doubtless not everything I try will work, and all these chemicals can't
be used in the same battery even if they all do as I hope, but it seems
likely that experimentation will disclose 3 or 4 practical improved "green",
aqueous battery chemistries for electric cars!
http://www.turquoiseenergy.com
Victoria BC