A Similar Hybridizing Concept!
Someone pointed me to a very similar hybridizing
concept to the Electric Hubcap system. In fact, it's almost identical,
axial flux and all, to my concept without the magnetic torque converter:
http://www.poulsenhybrid.com/
It looks like they plan to keep the gas engine running and
use the electric motors to save gas, struggling with the same issues of
the motors not having quite enough torque to accelerate the car
practically by
themselves. The torque converter is the key to being able to run
without the gas engine turned on.
The most remarkable thing to me is that I hadn't run
across this design before!
Motor & Controller
The design for the Electric Hubcap motor and the
updated design for the Turquoise Motor Controller are on the
web.
Magnetic Torque Converter Project:
Torque Leverage Without Gears
July Details
A Little Test
I had hoped
to concentrate on this project in August, but somehow I found myself
drifting into battery and microcrystalline coil cores experiments.
I did, however, come up with a new design with an entirely
different
operating principle. It should be very efficient as well as effective,
so perhaps it's just as well I didn't get any farther.
Here's the basic idea I have worked out, as currently
envisioned:
Carmichael's Magnetic Torque Converter
* The motor is axial flux, so the supermagnets face the stator
crosswise, on one face of the rotor. (which is a car disk brake rotor.)
* Another set of supermagnets is glued to the opposite face of the
rotor for the torque converter. This provides a supermagnet strength
rotating magnetic field. The motor rotor does double duty, as it's also
the input rotor of the magnetic torque converter. (Of course, a
separate rotor would work too.)
* The aluminum output rotor is a "frying pan" or "bowl" shape. It's
bolted to the
car wheel (or drive shaft, or other load).
* Supermagnets are attached to the rim on hinges. They are free to
swivel from 45 degrees away (with one end touching the back of the
frying pan) to 0, flush with the back side magnets on the motor rotor,
with a small air gap. (I plan to put an aluminum plate ring around the
top of the frying pan for them to hit against, as the attraction
between supermagnets is very powerful.)
* When the magnets fold back to 45 degrees, they contact a small piece
of steel that latches them there magnetically. (Some on the bottom or
top may be retracted by gravity, and if the wheel is turning very fast,
they may also be held centrifugally - all depending on the pivot
balances in the exact layout used.)
* In operation, the motor turns. When a like polarity magnet face
reaches the pivoting magnet, it pushes it away, and it folds back and
latches against the steel piece. No significant turning force is
generated.
* When an opposite polarity magnet approaches the retracted pivoting
magnet, nothing happens until they are almost directly across from each
other. At that exact point the attraction between them overcomes the
attraction to the steel latch and the magnet jumps forward next to the
magnet going by, with a small gap.
* If the two magnets were simply fixed to the rotors, the output rotor
would have been pulled backwards as the attracting magnet approached
and then forward as it receded. The forces would have canceled and
there would have been no net torque.
* However, the output magnet is folded away as the motor magnet
approaches, so the output rotor isn't pulled backwards. But then it
jumps out, and as
the motor magnet recedes, it is very strongly pulled forward. Thus
there's a strong pulse of forward torque with no equal pulse of
backwards torque.
* At the crossing of the two magnets, the motor, while yanking the
wheel forward, is itself slowed. Between magnetic "hits", it has time
to recover its speed.
The best number and spacings of magnets on both rotors,
the strength and setup
of the magnetic latches (or retraction springs), and matters of
hingeing, angles and orientations, air gap and so on are matters of
trial and adjustment to create a good embodiment within the scope of
the invention.
With the 10 magnets on the motor rotor backside, it's 72
degrees between any two like magnet poles and 5 magnetic pulses per
revolution passing any given point.
I estimate that the main pulse of magnetic force is spread
over about 12 degrees. Thus, considering one output magnet and with the
output rotor stopped, the motor is slowed by providing a powerful
turning torque for 12/72 or 1/6 of the time, and it has 5/6 of the time
to recover its speed. Additional output rotor magnets will spread out
the pulses and smooth the operation. With 6 output magnets, there
would be 30 pulses per revolution.
The gap between rotors will have to be adjusted so that
the motor will reliably start if stopped at any one magnet, and any
additional gap necessary for smooth operation. This is the limitation
to the maximum coupling and force that can be applied for each output
magnet. To have more maximum force, more output magnets are required.
It seems to me that the stopped output rotor should have
almost 6 times the torque the input rotor - the motor - is capable of
delivering by itself. One Electric Hubcap motor will thus provide the
torque of six to get the car rolling. As the speed of the rotor
approaches the motor speed, the torque drops off until, if the torque
required is small enough, two magnets "lock" opposite to each other and
both rotors turn the same speed with one-to-one torque.
Right now
I'm working out pivoting mountings for the magnets and other hardware,
that I hope can take
the strong forces involved.
Microcrystalline Electromagnet Coil Cores
August Details
In Wikipedia I find the following definition:
"Superparamagnetism is a form of magnetism.
A superparamagnetic material is composed of small Ferromagnetic
clusters (e.g. Crystallites),
but where the clusters are so small that they can randomly flip
direction under thermal fluctuations.
As a result, the material as a whole is not magnetized except in an
externally applied magnetic field (in that respect, it is like
paramagnetism)."
Here is the essence: rather than either "normal" iron
crystals or paramagnetic elements, the main ingredient for a strong
flux carrier with virtually no magnetic hysteresis is microcrystalline
structured iron.
I tried 3 more cores with Fe3O4, FeO
and slightly different compositions, and baked them to the lowest
temperature yet, with a charcoal briquette in the kiln to create a
reducing atmosphere. Then I quenched 2 of them in hot water and let the
other one cool slowly.
The charcoal briquette, glowing but still solid, went in
the woodstove. The idea of using charcoal to create a reducing
atmosphere puzzled me until I actually tried it myself: wouldn't it
just burn up in no time and then be useless? But of course!: it's used
up all the oxygen - that's the whole idea - so tho it glows red hot
(along with everything else in the kiln), it only burns up as fast as
more oxygen enters the kiln!
None of the cores worked at all. With no results, I decided to put the
project on hold, as it isn't one of the key objectives anyway.
Then I joined an inductor making discussion list, where I was advised
to read about magnetically "hard" and "soft" ferrites. Sometime in the
reading, I finally realized iron was iron: not ferrous oxide,
magnetite, ferrite or ferric oxide, just iron powder. The usual main
ingredient of motor coil cores I hadn't tried adding at all!
I decided
to try steel grindings. I collected a whole salmon tin of grindings
with a
magnet from around my bench grinder, which it seems I fortuitously
hadn't cleaned around in ages. However, this core appears to be no more
successful than the others.
Now I find that in addition to "ferromagnetic" there's
"ferroelectric" materials - related but not necessarily including iron
in the mix at all, for instance barium titanate. Barium titanate can be
produced by mixing barium carbonate with titanium dioxide wet in
correct proportion, drying, and then heating to 900 - 1200 degrees C.
The barium carbonate melts (actually, it probably calcines) at 811 C.
I definitely need to read further.
Turquoise Battery Project
August Details
A Battery Reference Book!
Wow, I found a technical book on batteries! I was looking over an
obscure
patent and it quoted the book as a source. I went to the library and
got it on an inter-library loan (all the way from Queen's Dupuis Hall
Library).
The book, Alkaline Storage Batteries by Falk and
Salkind (1969), was a gold mine of information. However few copies may
exist, it's widely quoted in later patents and appears as far as I can
tell to be the
only
definitive reference work on the subject (aside from a 1920 write-up of
nickel-iron batteries by one of Edison's engineers). A bit dated but a
must read
for anyone making batteries! Aside from a few upgrades like spot
welding
and plastics, it was surprising how little "pocket
batteries" had changed by 1969 from Edison's 1908 designs.
No wonder I can't seem to get a consistent story on
electrode reactions off the internet: it seems they actually aren't (as
of 1969) too well understood, and the book gives conjectures for some
common reactions as to just what is really going on, saying Mr. X says
"this", but Mr. Y thinks it's really "that", with "the other thing" as
an intermediate product.
I also note there's "formation cycles" when a big "pocket
electrodes"
battery is first made. Electrodes are placed in baths of electrolyte
before installing in batteries. One interesting result is that
impurities in the electrode material dissolve out in these initial
charges. These are discarded with the used electrolyte. I'm not sure
just how this could be accomplished in a sealed battery. (I've put in a
1/4" bottom spacer so that anything that wants to precipitate out has
somewhere to go.)
August Battery
Experiments
Well, much the best electrode so far has been a perforated
tube that I rammed nickel hydroxide and fine monel powder into. With
about 50% monel by weight - but presumably under 25% by volume - it had
a very low dry
resistance, just tens of ohms as measured on an ohm meter from
"anywhere inside" to the collector plate. The potential was there for
extremely high currents.
However, the electrode swelled, pushing stuff out the
holes, and the conductance went way down. Still "okay", but now not
"amazing"! I surmise the NiOOH is even bulkier than the Ni(OH)2 so it
needs more room as the battery charges, so it pushed the grains of
monel apart and they lost contact with each other. (The book mentions
that Ni(OH)2 pocket electrodes swell. Also alpha NiOOH is even less
dense than beta if you manage to get extra valence change - swelling
from that could be theoretically up to 44%, by which point I suppose
you'd have NiOO. No one has got the valence above 3.8.)
This is of course a problem with the nickel hydroxide
reactions, not the electrode design, suggesting it would be nice to
find some other positive electrode chemical for physical as well as
chemical considerations.
At first I decided to capitalize on the tube idea. The
first tube
only had
dozens of holes, labouriously punched and drilled with a tiny drill bit
that, predictably, finally broke. This time I bought a perforated brass
sheet at the hobby shop with about 7 x 8 = 56 tiny holes per sq.cm, and
cut a 3" x 3" piece. This I nickel plated (ug!), then bent a hook onto
opposite edges, and bent it around into a cylinder with a locking seam.
I finished by soldering a 3" nickel-brass #8 leed wire on with silver
solder, and I went over the solder and the edge bends again with the
nickel plating brush. I cut a tapered plastic bottom plug. (top plug,?
later!)
Into that perforated cylinder I planned to cram some
previously
made lanthanum hydroxide mixed with monel and fired in thiamin
mononitrate (tinned bean sauce) for a positive electrode.
Instead of a matching negative electrode in another
perforated tube, this battery was to have two concentric electrodes.
The outer perforated surface would be the inner surface of the outer
electrode (with a separator of course), creating a good interface.
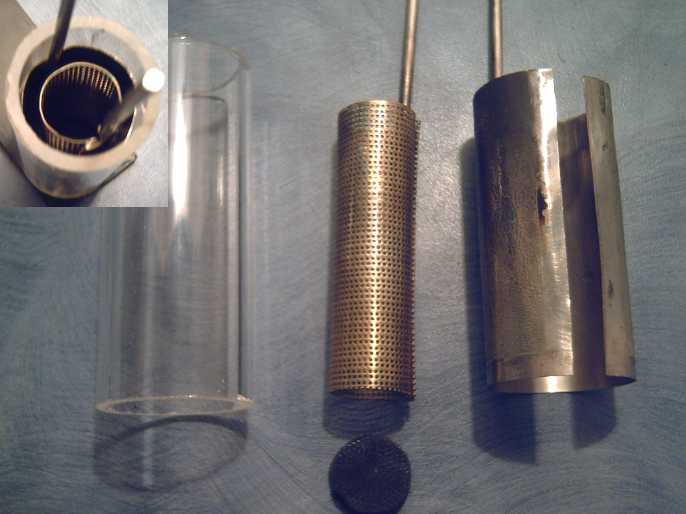
Cylinder battery pieces
If this could supply a good figure like 100 or 250
mA/sq.cm of interface area continuous, that would be about 5 or 12 amps
from a battery of simple construction not much bigger than a "D" cell.
Make it 30 cm tall instead of 7 and that would become 20 or 50 amps.
Then three wide for 150 amps times maybe 20 batteries for 36 volts
would be 60 tubes powering an electric car. 15" x 10" x 13" tall.
Without going into detail, maybe 3-4 KWH, 20-30 Km range. There's a
potential.
I cut a 3" x 4" piece of nickel-brass as an outside
"can" cylinder surrounding the perforated one. I soldered on a similar
leed wire and nickel plated the solder. (Normally these things are done
with spot welds, since you don't want a join that will corrode off or
leach contaminants into the battery. I don't have the equipment.) After
putting in a separator sheet painted with zirconium silicate powder for
an ion shield, I planned to cram manganese hydroxide powder (and monel
if the
conductivity isn't high) into the space between the inner electrode and
the outer "can".
The separator sheet must take the pressure and abuse
without letting the two
electrodes connect. The outer "can" wasn't to be soldered at the seam
and
would have no bottom, so the battery will be in a transparent
plexiglass
tube. (As I think about this, the transparent tube wouldn't
reveal very much with a piece of sheet metal covering most of it.)
That was the plan for the finished battery. However, I
planned
to try out a couple of perforated tube negative electrodes, and the
nickel and the lanthanum positives, with electrode tube pairs immersed
in a bigger tank of electrolyte for test batteries. I may still do
this. These won't have
the current capacity of the concentric electrodes, but they should be
good to test electrochemistries and measure battery voltages.
But I
couldn't help but think a square shape would be better than
cylinders...
but how to compact the electrodes... and keep them that way?
The answer to "keeping"
may lie in really tough separator sheets where the electrode can be
somewhat compressed against the sheet in use and all the electrodes
sandwiched into a rectangular box.
But what about powerful high pressure presses
for compacting them in the first place?
Flat Plate Electrodes
Following up on the thoughts above about square batteries,
over my holiday I
decided to abandon the cylinder without even trying it, at least for
now, and to try making a system for doing flat plates. For one thing,
in spite
of electroplating, the perforated brass
sheet still looks yellowish. I have little doubt it will quickly
corrode like the first one did.
I realized flat electrodes could be compacted about the
same way as the perforated tubes if they were placed in a steel box
with an END open instead of a FACE:
from one end with a plunger rod and a hammer. (I may or may not have
written of this idea before.) The trick is not to damage the the
stainless steel mesh on the collector plate in the process.
I decided to use the previously shown rectangular case
(right, below), but
after seeing the book, I would put it on end, with a small gap
- 1/4" or 1/2" - at the top, and another small gap at the bottom to
hold any sediments that precipitate out. The electrode terminals would
stick out
the top at the sides, with a pressure relief
valve/filler cap in the middle.
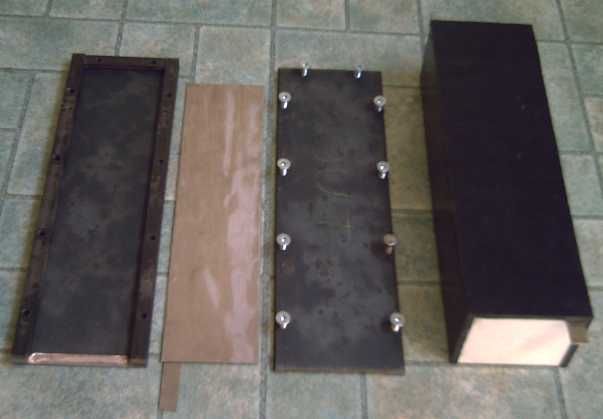
L to R:
Steel box bottom & sides (note beveled top end)
a 3" x 12" electrode collector plate, wrapped with stainless steel
mesh
box top (bolts through sides to bottom)
"ideal" final battery case (will stand upright)
I took two
flat plates of steel (1/4" thick) and three
pieces of steel bar, 1/4" x 1/2", and made a very strong, stiff box
that bolts together.
Inner dimensions are 3" x 12.5" x 7mm. The flat plate electrodes with
stainless steel mesh (left of center)
as previously planned are to be 3" x 12".
The
1/4" thick bar gives about ~7mm thick electrodes. Another
set of bars 3/16" x 1/2" gives thinner
electrodes (~5mm). Only one end of the box is open, a 1/4" x 3"
opening. I ground off the edges at this end at an angle to form a bit
of a funnel to pour electrode powders into the box.
The electrode compacting ("loading", "briquetteing")
procedure
is:
1. Cut a sheet of plastic (eg mylar, acetate...) to the outer size of
the box.
2. Bolt the box together with the plastic covering one inside face.
3. Slip in the electrode plate opposite the plastic, stainless mesh
facing in, leed sticking out the open top.
4. Put in a couple of temporary plastic wedge spacers to hold the
electrode plate
against the side.
5. Pour in some electrode mixture.
6. Tamp it down
using a steel bar that's thinner than the space and beveled at the end
so it won't easily rip the plastic or mesh. Pound it with a hammer.
(If the mixture is too wet, it may ooze around the sides instead of
compacting. Get it drier and try again.)
7. Repeat 5 & 6 until full,
removing the spacers whenever convenient.
8. Unscrew the box bolts, take the top off and peel off the
plastic.
9. Twist the sides and bottom end piece loose (if they stick to the
electrode) and remove them. (I should probably polish the side pieces.)
You should now have a solid - tho easily crumbled - electrode
sitting on a
piece of steel. The texture and stiffness will depend on the
formulation (that's another subject) as well as on how hard you
hammered down each layer. I note that the battery book calls bars
of compacted active material "briquettes".
11. Wrap it in an envelope of separator paper/material.
To try out electrode formulations, I made
electrodes just 3" x 1.5" instead of 3" x 12". I filled 10.5" of the
box with a wooden filler piece and worked
up by the open end.
The negative electrode was a mixture of manganese
hydroxide [Mn(OH)2, 23.4g] and potassium permanganate [KMnO4,
10.0g]. To this was added a bit of Sunlight dishsoap and a little
acetal ester as gel. On the second try it made an electrode about 77 x
35 x 5mm, giving 27 sq.cm interface area and 13.5 cc volume.
For the positive, I used 25g of the previously burned
monel powder/La(OH)3/bean sauce/Sunlight mix plus 12.5g of
straight La(OH)3, again adding a little acetal ester for
"polyester" gel. This electrode had the same dimensions but was about
7mm thick.
I confess I haven't worked out the amp-hours for these
mixtures (it should be a few AH), and the voltages are unknown except
that manganese hydroxide to manganese is -1.56 volts in alkali
solution, which I used. The battery could be as much as three volts,
which means I should have used the "voltage ramp" stuff. 27 sc of
interface surface is only 3/5 of the surface area of the rolled up
Ni-MH "AA" cell I cut open, so the max amps won't be too high.
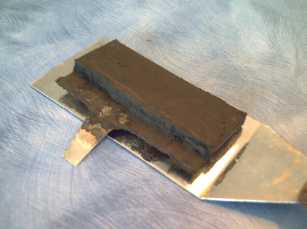
Mn Electrode as first made.
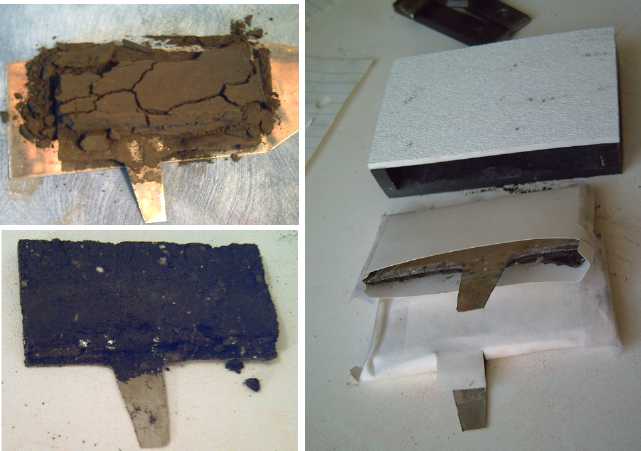
Crumbled Mn electrode after drying. This was redone later, with the
electrode mix dryer and harder hammering. That seemed to hold together.
Below, La electrode "briquette". Stuffing electrodes wrapped in
"Arches" watercolor
paper into the case. The inside of the Mn electrode envelope is painted
with zircon. The leeds are part of the electrode plates, so there's no
solder, welds or bolts. But I found sealing the case with such leeds
coming through virtually impossible except by clamping them with
C-clamps.
After charging the battery a few days with the top not
sealed, I took it apart. I inspected the Mn electrode: it had a hard,
lighter coloured crust on the face where it was against the other and
in contact with the ZrO2:SiO2 (AKA zircon,
zirconium silicate or pottery trade name Ultrox).
So, what's still missing for good working batteries?
* Leeds need to be welded or bolted to the collector plates. (These
batteries are "lead free" but have "leeds"!) Soldering, even silver
soldering, probably
won't last because the metals used for the solder will corrode away in
the salt and-or with the battery charging/discharging reactions.
Welding is
doubtless the best, but I don't know how to do that sort of miniature
spot
welding. Small, very short, stainless steel bolts, however, will be of
service at least
for prototyping.
* Then, it'll need the pressure relief valve/fill cap. I found a
screw-in adjustable pressure relief valve at Coast Industrial Parts.
(On order.)
The "cap" will have to be unscrewing the whole valve. I also got a
pressure reading dial to get an idea how much pressure builds up.
* The separator sheets have yet to be formulated. I'm asking a lot from
these - ion shielding, voltage ramping, very good wet strength, and
longevity.
* Actual working electrode formulations with high conductance that will
work and continue to work in a salt electrolyte that may be mildly
acidic, neutral or mildly basic. (Pick one!) The pH aspect
of the electrolyte in turn depends on what works well with the chosen
electrode chemicals.
I'm not content with a nickel hydroxide positive unless it
gives a volt instead of 1/2 a volt -- which it may do in a neutral to
acidic electrolyte instead of alkali -- and better amp-hours than the
typical less
than a single change of valence state. (which it has been enticed to do
by some lately, obtaining valence 2.2 discharged to 3.8 charged: a
change of 1.6.) There is probably some cheaper and maybe better
alternative - nickel has been going up and up in price.
Zinc oxide or hydroxide has been used to better effect
recently for negatives, the branching dendrite problem being reduced or
eliminated, but I'm trying manganese [eg Mn(OH)2
+ 2e- <==> Mn + 2OH-], an
enticing looking reaction probably about -1 volts in a more neutral pH
battery.
Cases Rerereconsidered
Round pipe is a poor
shape for flat electrodes, but the seams along the whole length at each
corner on the rectangular case continued to disturb me. I've finally
learned that to get a good seam, it should be C-clamped along its
entire length while the solvent/glue dries. But surely even so,
wouldn't such
long seams still be a source of trouble?
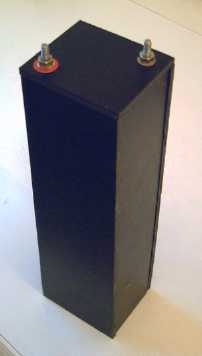
The 3" x 12" x whatever thickness, concept battery case. (A new
feature is
stainless steel bolts for terminals. The smooth heads are tightened
against the smooth plastic inside of the case, with a leed or the
actual edge of the collector plate welded to them. I think these won't
leak.)
I looked on the internet for seamless rectangular tube,
but
searching for merchandise has been made enormously difficult by dozens
of "linking" sites all claiming they have what you want - whatever it
is - but they only point to a zillion real businesses that are mostly
irrelevant to what you searched for, while the handful of real makers
of what
you want, that should have turned up near the top of your original
search
results, are hopelessly lost amidst hundreds of these bogus "hits" -
links to
links to links to irrelevance and a waste of time.
In one experiment quite a while back, I heated some ABS
plastic and
found it could be bent and would retain the shape when it cooled. It
seemed hopeless to try to bend a big piece with the heat gun, but a
new plan dawned on me: I could heat foot long battery lengths of 3" ABS
plumbing pipe in the oven, and jigs and formers would make it roughly
rectangular with rounded corners, or at least oval. Not perfect, but it
would be
just about the right size to make into batteries with four electrode
pairs. No seams!
Then all it would need is the ends sanded perfectly flat,
and the
flat top (with the fittings and electrodes) and a flat bottom glued on.
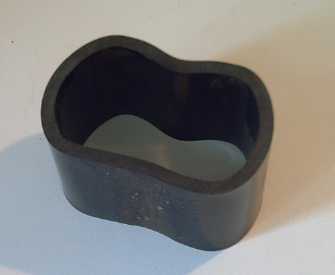
First try at making a 3" round ABS plumbing pipe rectangular in the
oven.
(It was just a rough test jig!)
Voltages Rereconsidered
When I started out and
found the reaction voltage of lanthanum to lanthanum hydroxide was -2.9
volts, I thought "Wow, what a great voltage, why hasn't anyone done
this? Why are they all using iron, cadmium or metal hydrides that are
under one volt?" Then I found out that water starts to electrolyze at
about 1.23 volts, so everyone was looking for lower voltages. However,
it was said to electrolyze quite slowly up to about 2.0 volts, so we
have, for example, one of the reactions of lead-acid being 1.7 volts
with a total of 2.1 volts. If the charging voltage goes up to about
2.36 volts (iirc) per cell, the water starts bubbling vigorously, and
the gasses
are vented to the air. (The 1.7 volt side probably hits the 2.0 volt
limit.)
But: These cells are vented, essentially unsealed. So are
all the other big batteries. What happens if a higher voltage cell is
sealed? Nothing is said about the idea in the battery book. One patent
mentions the challenge of high pressures involved with Ni-Zn "AA"
batteries because of their higher charging voltages, although they are
under 2 volts.
At first of course, the gasses start to be given off. That
raises the pressure.
Thermally, we know that the boiling point rises with air pressure, so
what about electrically? Will the gasses continue to bubble off at the same rate ad
infinitum until the cell, however strongly built, leaks or bursts, or
will high pressure raise the voltage the water bubbles at until at some
finite pressure it stops gassing at the given voltage? Alternatively, might the high
pressure gasses, H2 and O2, start to recombine
into water as fast as they're being generated?
I didn't find satisfactory or definitive answers to these
questions on the web. I also didn't know what pressure range to expect.
(15 PSI? 30? 60? 120?) Perhaps the only way to be sure is to create a
battery that doesn't leak under pressure and see what happens. I
strongly suspect that a pressurized battery is the key to permitting
these higher voltage reactions and hence attaining higher energy
density in an aqueous battery. (and goodbye to pricey lithiums!)
To test the theory, I simply reversed the charge on my
present La-Mn cell, making it Mn(+)-La(-), and if it doesn't leak and
the -2.9 volts reaction
works, it should charge up (with the manganese oxidation reaction at a
whopping
+0.15 v) to 3.05 volts! Thus the emphasis on sealed cells: this can't
work if they're not sealed, but it might if they are.
However, the attempts to create one so far have been
pretty unsuccessful. This cell keeps springing leaks, and it now has 3
C-clamps helping to hold it together.
The theory appears to have merit. The cell was up to 1.77
volts at one point (26th. and it should charge very gradually the first
time -- it's the "formation" charge), and every time it leaked, it lost
a little voltage, even with
the charge still on. I presume the pressure is gradually increasing
with the voltage, otherwise why would it keep springing more leaks once
it's sealed (again)? I've purchased a dial pressure gauge, and
belatedly (28th) put it onto this battery. (And its fitting is brass,
which
will corrode... and leak!)
On the 29th, after yet more leak repairs on the 28th,
teflon tape on the meter base threads, and four C-clamps holding it
together, the cell finally held pressure, and hit 1.9 volts and 8 PSI.
It'll be a few more days before it finishes "forming" and charges up
the lanthanum and manganese.
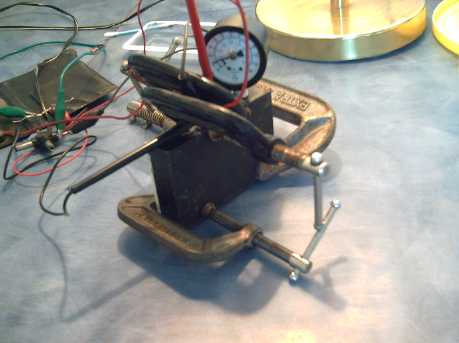
Several repairs and 4 C-clamps later (then 5):
No leaks, holds pressure!
Having such a high energy potential (-2.9v), lanthanum
metal
does spontaneously turn into lanthanum hydroxide in water (outgassing hydrogen). That would
gradually self-discharge the battery, but the process is very slow in
cold water: at least days, more probably weeks, maybe months. (It would
have taken years to convert my lanthanum ingots into the hydroxide
whole and in cold water instead of sliced up and in a hot pressure
cooker - it still took weeks.) If it works, we'd have a very high
energy density battery for daily driving, but not one to run a clock or
smoke detector, or to turn on a flashlight when there's a power failure
6 months after it was last charged. Making the battery a "dry cell"
might also reduce the self discharge.
Rereconsidering Cellophane
Several times I have tried to use cellophane, which is
said to be a very good electrode separator membrane, but it didn't
seem to work at all. In the battery book, I noted the term "silver
treated
cellophane", and I looked it up on the web. In so doing, I ran across
this revealing paragraph from someone making what sounded like
"microfiche" film from cellophane:
"3. Preparation of the Cellophane: Commercial
cellophane, such
as is
used for wrapping packages, is coated with a plastic resin to make it
non-porous.
Uncoated cellophane is available from chemical supply houses, which
sell
it as dialysis tubing or dialysis membrane. In all that follows we will
assume that you have only coated cellophane available. The coating must
be removed from one surface of the cellophane. Using a wad of cotton
moistened
with lighter fluid, rub the surface of the cellophane briskly. Turn the
cotton over, remoisten and repeat. Hold the cellophane up to the light.
The area you have rubbed should appear duller than the rest. Repeat the
process using a fresh piece of cotton to make sure. From now on, handle
the cellophane with tweezers or wear lint-free lab gloves."
I bought my cellophane at a crafts shop. It was called
"Clearphane" and there was no composition info on the package. But I'd
lay good odds it's actually plastic coated -- small wonder it doesn't
work! I've been concerned about the possibility all along, but now I
know something I can do about it -- assuming lighter fluid is still
available these days.
The problem with making a salt electrolyte battery is that
some of the reaction products are usually soluble in water, eg zinc
chloride with a zinc electrode. Treated cellophane is evidently a key
to making such batteries owing to its salt rejection, keeping the zinc
ions of their own side of the separator sheet.
The salt rejection properties of cellophanes are
substantially
increased, and permeation rates decreased, by pretreatment with certain
metal ions or presence of these ions at low concentration in feed
solutions. In a typical case, a cellophane which initially rejected
about 20% of salt from a 0.05M NaCl solution rejected over 70% in
Presence of 10
-3M ThCl
4. Permeation rates were
decreased, usually by a factor of 2 or 3. Additives found to have a
marked effect were Fe(III), Th(IV), U(VI), Cu(II), and hydrolyzed
Pb(II). Mg(II), Ba(II), La(III), and unhydrolyzed Pb(II) had little
effect. The mechanism by which the additives affect the cellophane is
not clear.
"
Fe(III) is of course the key ingredient of the red rust
I've
been smearing on. I suspect Os(VIII) is probably better than any of the
above.
Of course, neither the cellophane nor any of these
enhancements had any chance to work when the cellophane has been
deliberately contaminated with plastic, with no mention of that fact on
the package!
Lead-Sulfate Salt Battery
In an internet discussion list on August 31st, someone
reported emptying the sulfuric acid from "spent" lead-acid batteries
and
refilling them instead with alum solution. (10 oz weight of alum per 40
fluid oz distilled water)
He claimed that after a few charges the capacity comes
back, and
that they seem to be good for even more current than originally! He
said he hasn't bought a new battery in 20 years!
It sounded incredible, but chemically seemed plausible. I
thought I'd verify it by trying it myself, but then I
searched and immediately found a blog with many entries discussing it. It appears it's true, and
that many people have done it, also with epsom salt, and also even with
brand new batteries:
http://blog.hasslberger.com/2007/01/how_to_convert_a_lead_acid_bat.html
As far as I can tell the idea was thought up by a Chinese
person (a Chinese looking name on one web site), who patented it. It
would seem the patent must have expired, perhaps long since, from the
writer's "20 years" statement. It seems almost incredible that this
hasn't become common knowledge. The many, many little-known valuable
things like this, often of a medical treatment nature, disclose a great
communication weakness within our society: we are virtually unable to disseminate
valuable information to the public unless someone stands to make money
from it.
In fact, it seems that at least two sulfate salts - alum
and epsom salt - work better than sulfuric acid.
Compare:
H2SO4 (sulfuric acid: hydrogen-sulfate, ?)
NaAl(SO4)2 (alum: sodium-aluminum-sulfate, 35?)
KAl(SO4)2 (potassium alum:
potassium-aluminum-sulfate, pH "mildly acidic", 9.5)
MgSO4 (epsom salt:
magnesium-sulfate, pH 5.5-6.5, 33.7)
...All acidic sulfates, so like chemistries. Except one is horribly
acidic and the others only mildly acidic. Of course, the renewed
battery becomes much safer - a spill won't blind you or eat your skin
and flesh.
The numbers at
the end are the solubility in grams per liter of water.
I intend to try sodium sulfate. The molecular weight is a
bit higher than magnesium, but the solubility is good and the sodium
ions probably won't be as strongly bound to the sulfate as magnesium or
aluminum, giving higher current capacity. Higher current capacity in
turn means not only more engine starting capacity from a smaller
battery but substantially better amp-hour performance at the moderately
high current draw rates required for electric driving. Furthermore,
it's highly unlikely the idea has ever been patented.
Then, since using a salt reputedly "restores" old
batteries, it seems likely that the recommended maximum depth of
discharge can be increased from 50-60% to 70 or 80%.
Overall it seems likely we'll see the useful driving range
available to cars using common "lead-acid" (more accurately
Pb-PbO/sulfate) based batteries extended over 50%, and the life span of
the batteries tripled or quadrupled. Suddenly electric driving with
common lead batteries looks far more economical!
Na2SO4 (glaubers salt: sodium-sulfate, pH 7, 19.5)
NaHSO4 (sodium bisulfate, pH 1.4, ~~70)
With a pH of 7 (neutral), Glaubers salt by itself may possibly not
work. The bisulfate, which is the most soluble of any of these
substances and more than acidic enough, can be made by mixing the salt
with sulfuric acid (or NaOH + H2SO4), and although the pH of a one
mole/liter solution is 1.4, Wikipedia says it's used in foods. Or
perhaps just a little acid added to the mix would activate it. I've
ordered the salt and I hope to receive it and try it out this month
(September).
Although lead-acid batteries have lousy energy
density and
aren't the aim of my work, doubling (or better) their life span and
improving their effective range would
be very immediately valuable to electric transportation.
Evidently there's been no effective experimentation with the
electrolyte since Gaston
Plante invented lead-acid batteries in 1859 until rather recently, and
this great info isn't spreading well! (Our society seems to have no
means of spreading valuable general info unless somebody can make money
off it.)
I've decided to
try it out for myself. On September 1st I went in search of alum but
found only epsom salts - 2Kg for $3.77 at
Walmart. That's the cheapest battery chemical I've ever bought! (This
was before I found the blog -- I was just guessing that epsom salts
should work if alum did.)
http://www.turquoiseenergy.com
Victoria BC