Turquoise Energy Ltd. News #20
Victoria BC
Copyright 2009 Craig Carmichael - October 3rd 2009
http://www.TurquoiseEnergy.com
Highlights/Contents:
September in Brief
(summary, below)
Detailed
newsletter articles are posted on the Turquoise Energy
Ltd. website. Only these highlight/contents blips are included in the
email. Complete newsletter:
http://www.TurquoiseEnergy.com/news/TENews20.html
Electric Hubcaptm Car Drive
Project Detailed Report
* The motor and controller are both
finished and the designs are on the web.
* Motor Controller Making Manual updated - schematics.
* Regenerative braking ideas
Magnetic
Torque Converter Project Report
* Project Recap
* Painfully slow progress towards a prototype - changing design ideas.
* Preliminary test... It Runs!
Microcrystalline
Ceramic Motor Coil Cores Project Detailed Report
* Cores with "Barium Titanate" -
didn't
work
Turquoise Battery Project Detailed Report
* Good Cellophane - YAY!
* Ion passing electrode separator
sheet.
* Battery cases: Squaring round ABS tubes in the kitchen oven
* Battery making idea: start with charged electrode chemicals instead
of
discharged.
* Manganese negative electrode: Higher energy density and voltage than
MH, Zn, Cd, Fe...
* Making Lithium Hydroxide electrolyte additive.
Lead-Acid Battery Project Detailed Report
* Tried epsom salt - yuk!
* Tried sodium sulfate - Higher voltage: ? Test battery is crap - leaks!
* Made sodium sulfate by adding sodium hydroxide to the battery's own
sulfuric acid. (Cheaper!)
* pH Test Paper Famine!
* Tentative Instructions for "Renewing" a
lead-acid battery with sodium sulfate salt or sodium hydroxide.
Newsletters
Index/Highlights: http://www.TurquoiseEnergy.com/TENewslettersIndex.html
Construction Manuals for making your own:
* Electric Hubcap Motor
* Turquoise Motor Controller
http://www.TurquoiseEnergy.com/
September
in
Brief
I finally made a start of piecing out and putting
together the rest of the Carmichael Magnetic Torque Converter,
the final drive piece to enable hybridizing of regular cars with the Electric
Hubcap add-on motor. But at the same
time new design ideas keep cropping up, suggesting I shouldn't build
too
hastily. Of course, more practical ideas often emerge through
trying rather than through sitting and theorizing, and I have put
something together and run
a couple of illuminating tests. Although it's not all together or
adjusted yet, it
takes considerable force to stop the output rotor completely with the
motor running. This version, if it were finished, might put a car on
the street, at least for a demo. But it's doubtless not optimum. The
next variant visualized holds promise for really getting cars moving,
even up considerable hills from a stop.
And I thought of a
couple of possible reasons why my Turquoise Batteries haven't
been working and tried a couple of experiments,
and I finally (after all this time!) made a good sealed battery
case -- that can be
opened,
too! by forming 2" ABS plumbing pipe into a rectangular shape, so the
case has no seams except for the top and bottom covers. I also got
a pressure meter, so I know the case held at 34 PSI. (To get that, I
was charging too fast.) I made another jig
to square up 3" ABS pipes for multi-plate batteries. It essentially
worked, but I will be improving on it. I've ordered manganese powder
for making what should be very high energy negative electrodes - almost
double the energy of the best metal hydrides (Take that, costly
lithiums!) - and I'm trying CMC gum
and Vee gum to make electrode material "briquettes" more solid.
Having a vague idea, I tried out a couple more formulas
for
microcrystalline
ceramic motor coil cores, but they weren't successful. Perhaps I
should
be checking the crystal/grain structures I'm obtaining under a
microscope. I just need a microscope and to know what I should be
looking for!
And I revised my Turquoise Motor Controller manual
a bit
- an
improved power MOSFETs diagram for clarity, by e-mail request from
someone
whose English wasn't very good. (As I've said, if North Americans don't
have the imagination and drive to turn our vast fleet of gasoline cars
into plug-in hybrids, others will beat us to it.)
I also experimented with renewing lead-acid batteries
with
sulfate salts. The common lead-acid battery is notorious for
its
short cycle life and fragility, having exacting usage requirements to
give its rated life and performance. There have been
better economical electric car
batteries available in the past (Ni-Fe, Ni-Cd, Ni-MH) but lead-acid is
the only one on
the market today. It seems it can be rejuvenated and may last up to
five times longer by simply adding some sodium sulfate
salt or sodium hydroxide to the electrolyte.
These batteries are common, cheap, refillable and in current use,
so improving them is of immediate practical value to electric
transportation. Especially, increasing the cycle life dramatically cuts
the cost of electric driving.
While I'm not sure that I've achieved all that's
possible, it seems to work and instructions for renewing a battery are
in this newsletter.
The Electric
HubcapTM Vehicle
Drive Motor
September In
Detail
Motor & Controller
The design for the Electric Hubcap motor and the
(updated) design for the Turquoise Motor Controller are on the
web. They are "finished" as far as the original intent to make a motor
and controller that work for the drive system. I updated the motor
controller manual again this month with a clearer schematic of the
power MOSFET transistors and supporting components of the heatsink area.
A system to propel a car now only needs a working Carmichael
Magnetic Torque Converter, the subject of the next section. The
motor and torque converter unit now weighs 56 pounds.
I hope to improve the motor in the future with custom flat
rotors having built-in hubs, to replace the car disk brake rotors and
re-machined trailer axle hubs, and with microcrystalline coil cores.
The set-up for doing the rotors with abrasive waterjet
cutting will cost money, but it will allow for thinner profile motors
that
are easier to make and somewhat lighter and simpler.
Microcrystalline cores would make the motor coils
easier to
produce, improve efficiency, and make the motors a little
lighter. Of course, they depend on the success of the microcrystalline
cores project.
The motor controllers provide great basic operation, but
they can be improved by options for regenerative braking. This seemed
impossible
using the present MC33033 motor controller chip, so I wrote to ON
Semiconductor, who make the chip, to ask if there's any variant of the
chip made for electric cars that I'm unaware of, i.e. with
regenerative braking, and if not, to suggest detailed ideas for such a
new variant. There has been no reply.
But in the last days of the month, it dawned on me that
there
is probably a way to "trick" the motor controller into doing
regenerative braking, by reversing the drive outputs or inverting the
position sensor inputs, so the motor is being pushed backwards when the
controller thinks it's pushing forward. It's likely to take an
extra logic chip or two and some devious connections.
Of course, these improvements are minor details: these are
working
products and the instructions for making them are on the web.
Presently, I'm putting my time into the magnetic torque converter, and
(currently more so) into battery ideas and development.
Magnetic Torque
Converter Project:
Torque Leverage Without Gears
September Details
Project Recap
In October 2008 I got a prototype Electric Hubcap
motor to move my car across level pavement. It didn't seem like enough
torque, so I made another one with bigger coils, and made some motor
controller
improvements, by early summer (2009). I realized then that the Electric
Hubcap
motor system just wasn't going to propel cars on the streets by direct
motor connection to the wheel: there just isn't enough torque with this
size
motor even with the high torque design and supermagnets, to
accelerate quickly and to go up hills - perhaps not even with a motor
on
each
wheel. Now what?
Then I had the idea it should be possible to make a torque
converter using supermagnets. I made what turned out to be an
"electromagnetic coupler", but it couldn't have any more torque at the
output rotor than at the input rotor, a fine point which had at first
escaped me. In July I came up with one possible
design. (I'm suspicious the induction technique wouldn't have
worked
well.) Then in August I came up with a completely new design. It had
the advantage of needing the components I'd already made, with some
additions rather than changes. This one should give some
"magnetic punch", but again the details of actual operation are a bit
hazy. A
couple of fine adjustments would be critical. In
September, some feeble attempts were made to fabricate
it.
Near the end of September, I got another new design idea,
to
make a mechanism like a clock escapement. Again I haven't figured out
an exact layout yet.
In
essence, as a magnet goes by and pushes the pivoting magnet
("escapement cam") away, it pushes into a slot with 45 degree sides.
The farther from the motor rotor magnets it pivots, the less the
magnetic force. When the force is less than the torque needed, they
will slip apart.
However, such a mechanism again appears like it can be
arranged as an addition to the original and the August designs
rather than "instead of",
so I'm continuing that one, however gradually. If it works well, I'll
use it as is. If not, there's the alternative "escapement" idea.
A final late-breaking idea (Sept. 30th) is to angle the
magnets 45º. This would provide a short range, almost a point, of
powerful thrust when magnets meet, while also reducing the powerful
(and worthless) attraction between the input and output rotors.
But on October first, the original (August) idea was
together to a basically testable state and I ran it. It's promising,
though noisy. Even though only two pivoting magnets out of six are
installed, and even then are incompletely done and with a wide air gap
to the other magnets, it takes very considerable force to completely
stop the output rotor while the motor is turning.
Are there alternatives to the torque converter that could
put Electric Hubcap systems on the road? Of course! One is
planetary gears
so the motor can be geared down, eg 2 speeds 8:1 and 2:1. This gets
complicated and is doubtless inefficient, so two motors and two sets of
gears would probably be needed, adding expense and decreasing electric
driving range.
A second alternative is a continuously variable
transmission ("CVT"). Here is one someone pointed me to that uses balls
that roll at different angles
depending on the shifter position and an oil that solidifies
momentarily to provide traction when there is sufficient pressure on
it, when the rolling ball meets its contact point:
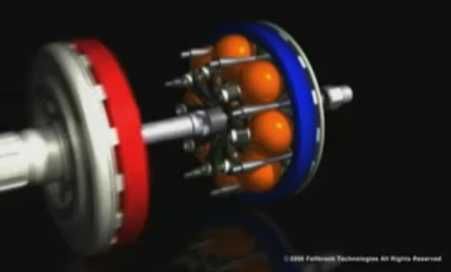
The NuVinci (made so far for bicycles), and other CVT
mechanisms and other alternatives,
make putting together a magnetic torque converter look so much simpler
than when considering the project by itself!
September Progress
For the construction, first I tried to find rectangular
stainless steel tube
1/2" x 1" (inside dimensions) to put the magnets in. No one seemed to
have any, but I had an inspiration and I bought a piece of 1-1/4" round
tube. Then I got a 1/2" x
1" steel rod to slip inside. I hammered the tube to the right shape on
my big garden rock "anvil", and it seems ideal.
I also picked up 1/4" stainless round rod for hinge pin
axles, 1/2" square stainless bar as hinge mounting pieces, and a piece
of sil-fos (silver-phosphorus) solder. I drilled the bar with 1/4"
holes
for the
axles and made threaded 1/4" holes for mounting bolts. Easier shown,
below, than described.
Everything seemed to be going smoothly... then I went to
solder the hinge pins on. I heated the stainless to bright red hot
(like the guy where I bought solder said to do) with
the 'swirljet' propane torch, but nothing would stick to it. Silver
solder, sil-fos and brazing rod all beaded up and fell off! No amount
of flux helped, and hotter MPS gas made no difference. I knew stainless
couldn't be soft soldered (low temperature tin-whatever solder), but I
hadn't realized that might also apply to silver solders and even brass
brazing!
Reluctantly, I concluded there was nothing for it but to
weld it. Not my favourite sport! I dug out the arc welder and all the
paraphernalia and protective gear - I don't think I'd used it in a year
or more. Then I proceeded to burn holes in and
warp my nicely made parts! The pieces were smaller and the metal
thinner
than anything I'd welded before. By the third one of the three I'd
made, I had the technique down: get the weld started and almost
immediately quit!
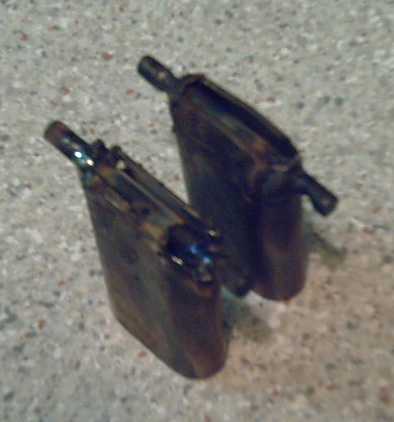
Stainless steel magnet pivot cases:
first overheated by torch, then mutilated by arc welder.
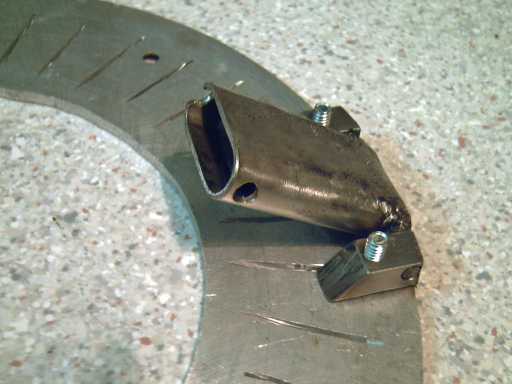
The best pivot magnet assembly (never torched) mounted on "the ring" of
the output
rotor. Nothing sticks out past the outer edge. (or I'll grind it off.)
Shown in "retracted" position. The
magnet is inside. I haven't decided whether to put a bolt across the
open end or just hammer it closed to retain the supermagnets.
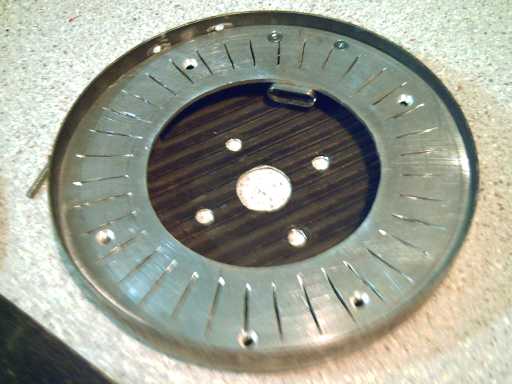
The ring with pivot magnet in the output rotor, which gets attached to
the car's wheel. The ring will be raised to about the top of the rim of
the pan to leave more depth for the magnets to retract into. The input
rotor magnets (rear face of the motor rotor) will spin by 'the ring'
with a
small air gap.
One detail that may become an issue is magnet gap: if it's too small,
the motor won't start spinning. If it's too large, the torque won't be
enough to move the car. Hopefully these ranges will not prove mutually
exclusive!
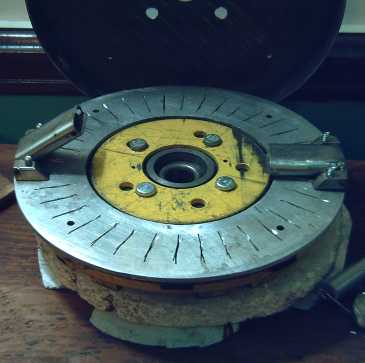
The ring, sitting on the motor rotor, with two magnet assemblies
mounted, Sept. 30th.
On the evening of Sept. 29th, someone pointed
out to me
that magnets slide past each other on the flat with relative ease
compared to trying to pull them apart. He had a good point.
Interactions between magnets are weird. If the coupling proves
insufficient, twisting the output magnets by some angle such as
45º would give the whole system more punch in the radial
direction, while also reducing the more powerful (and useless)
attraction between the rotors as magnets pass by each other. (In fact,
this is probably a good idea regardless - sigh, back to the drawing
board!)
On October first, I finally put everything together (as it
was by then already made). First I had no magnets in the holders, but
the bolts
were magnetic steel. I put it on the axle with the motor rotor and
turned the motor rotor by hand. Somewhat surprisingly, the output
rotor, though resting on its four bolts on the bench, bumped along,
turning a bit at a time as each magnet went by a bolt. A steady turning
pressure of the force applied would have been insufficient to move it,
but the same average force, split into the periodic strong magnetic
"bumps" with the longer times with no force in between, did it.
And there was certainly not enough time between bumps for a car to roll
back again if it had been moved. This seemed like a good sign!
In fact, it gives rise to the idea that simple pivoting
blocks of steel retracted by springs, instead of supermagnets, could be
used in the output rotor. Of course, supermagnet against steel would
have much less punch than supermagnet against supermagnet.
I put the magnets in and they clacked up and down as the
rotor turned by them. Then I put the motor together and ran it. With
the motor turning at a fair power, I put my hands (leather gloves) on
the output rotor and held it back. It was very noisy with the magnets
clacking up and down fast!
It had quite a bit of torque, but I could stop it by hand.
It probably wasn't enough to move a car (though I wouldn't
swear it wouldn't have on level pavement either), and I can't say for
sure that
it had more torque than the motor by itself. On the other hand, there
were only two magnets installed, the air gap was 3/4", and I hadn't
installed the magnetic catches. Six magnets with 1/4" gap and pivoting
at
the optimum times ought to be another story.
Running the motor at a lower power level, it would stall
when I stopped the output rotor. This is probably largely a result of
my skewed motor magnet arrangement. I'd redo that if epoxy glue wasn't
so hard to get off, or if I felt I could afford another batch of
magnets.
I want to devise a mounting system and try
pivoting the magnets the other direction, at a 45º angle, before
making more magnet holders of this type. Checking magnet interactions
by hand, I can tell there'd be much more "punch" at that angle instead
of flat, so it should work
better - and more quietly! It has yet to be proven, but I expect it
should shove a car even up a good hill.
Microcrystalline Electromagnet Coil Cores
September Details
I decided I shouldn't let a month slip by without at least
attempting one core -- lest I forget what mineral is what and what
they're for! And I had obtained one additional material I wanted to try
after a bit of reading: barium
carbonate. Barium titanate is a compound often mentioned as a ferrite
core, although more as a 'hard ferrite' that retains magnetism than as
a soft one for electromagnets.
There's titanium in the ilmenite, but no source of barium
in what
I'd been using thus far, so cores #20 and #21 had as "active
ingredients" laguna borate, magnetite, ilmenite and barium carbonate.
The carbonate "calcines", sheds its carbon to the air above - um - some
temperature:
BaCO3(s) => BaO(s) + CO2(g)
In with all in the clay, I expect some barium titanate will be formed
in the firing because, um... Ah, here it is:
"Solid-state reaction between BaCO3 and TiO2 in an
equimolar ratio at temperatures >1200°C has often been used to
prepare BaTiO3 powders."
Of course, ilmenite isn't TiO2, it's FeO:TiO2. Oops... on
writing the above, it seemed I'd already gotten too much out of touch
with the project: RUTILE is TiO2! Ilmenite
might work anyway as it contains titanium, but I went off and mixed
core #22, with rutile instead
of ilmenite!
Well, none of these cores worked. What am I missing? On
the other hand, I didn't heat it to 1200ºC, either. I didn't want
to heat the other ingredients so hot.
I suppose I could try mixing some BaCO3 and TiO2 powders
and heating them separately to over 1200 C. But would I know if I'd
succeeded, and would BaTiO3 make for a successful core when nothing
else has?
What am I looking at?...
TiO2: white powder
BaCO3: white powder
BaTiO3: "white crystals" (Wikipedia)
Here's something interesting about manganese and
magnetism, which
element I was looking up for battery info:
"With aluminum and antimony, and especially with small amounts of
copper,
it [manganese] forms highly ferromagnetic alloys. [And presumably could
make "superparamagnetism"? The authors speak of metallic alloys,
not oxides. I now have 5 pounds of manganese powder on order for
batteries.]
But perhaps I'll refrain from making any more cores
pending some additional understanding or an idea for a fresh approach
to try out.
(To the point for batteries, with respect to self discharge: "The
metal is reactive
chemically, and decomposes [in] cold water slowly." ...But does
"slowly"
mean hours, or years?)
Turquoise Battery Project
September Details
Good Cellophane!
Though having got no answers from the company about the product by
e-mail, I bought some "Pacon" brand "clear" cellophane from amongst
several "coloured" types at Island Blueprint, and to my surprise it
appears to be the real thing: uncoated microporous cellophane that
breathes. When I suck on it, cool air very gradually comes through it.
And
it makes an ionic connection instead of a very high resistance inside a
battery: it works!
Semipermeable
Electrode Separator Sheets
Having found microporous cellophane at last, I see it
probably
isn't the whole answer, because my batteries still won't retain a
charge.
Perhaps a potassium and chlorine
ion permeable membrane - a "salt bridge" - that won't let too much else
through may be key. That way,
dissolved metal ions will stay on their own side and can be used,
rather than all charge and discharge reaction products (other than the
electrolyte) having to be insoluble solids.
The battery book has a few notes on semipermeable
membranes.
They're okay starting points, but vague on exactly what and how in a
mostly quite explicit book. This probably represents the unsure,
groping exploration that had been ongoing and probably continued until
the lithium juggernaut evidently
pre-empted all other battery research.
September
Battery Experiments
I decided to try out my acetaldehyde and
acetal ester tricks for preparing the surface. I used an artist's brush
to brush acetaldehyde (fresh batch) onto a piece of cellophane. Then I
brushed in some ferric oxide, then I brushed in some 20% hydrochloric
acid to turn the acetaldehyde into an acetal ester. Notwithstanding
that
this cellophane is permeable, I turned it over, did the other side the
same, then sprayed some seal oil on that side.
It didn't seem to work any better than a regular untreated
sheet.
Case Making
In order to have cases with a minimum of seams and a
maximum of strength for battereis that will hold a certain amount of
pressure, I started making and trying out improved jigs for turning
round pipe into square in the oven. The maximum temperature to heat the
oven to is around 150 C / 300 F. That, of course, is according to my
oven's dial. Somewhere not much higher the ABS started sticking to
the base it's on, and probably soon to the other jig pieces as well.
Two inch I.D. ABS drain pipe can just be coaxed into
making a 3.2" x 15mm (5/8") rectangular case (inside dimensions) for a
single 3" wide cell, though considerable stretching of the plastic is
needed to accomplish this since the original circumference is 2 pi
(6.28) inches and the final lengths add up to 7.25".
I found a pressure meter and an adjustable pressure relief
valve at Coast Industrial Supplies. The meter is finally starting to
tell me just what pressures are in fact building up inside my batteries.
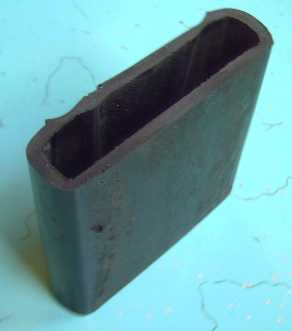
Two inch pipe made into a 3" wide battery case. The skew was an
unexpected feature of the stretching/squaring technique.
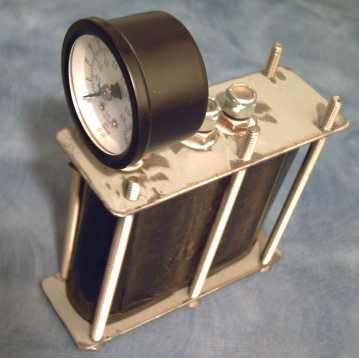
This finally made a well sealed battery, one that can be opened by
removing the clamping bolts. It held 34 PSI!, but
not without a rubber gasket and some wooden pieces under the metal lid
to spread the force of the bolts.
Two short 1/4" stainless steel bolts, their
heads screwed up tight against the lid on the inside, worked for
sealed terminals. I had to drill small holes into the heads and thread
them for #6 screws to allow a connection to be bolted to them on the
inside.
The most extreme internal pressure measured - after
charging at a high rate - was 34 PSI. At that pressure the sides of the
case were bulging and bending the side bolts out, but it held!
I must mount the pressure relief valve next time! I'll
probably set it at about 15 PSI.
I thought a three inch I.D. pipe should work out quite
well for three inch wide plates
batteries without such exertions to stretch the plastic as well as
square it. However, it seems a four cell enclosure would again require
some
stretching while the plastic is hot. Perhaps I should just settle for
three cells per battery. or thinner electrodes, which would also be
higher current capacity.
Here is an attempt to make a squaring jig for 3" tubing.
It needs 8 bolts:
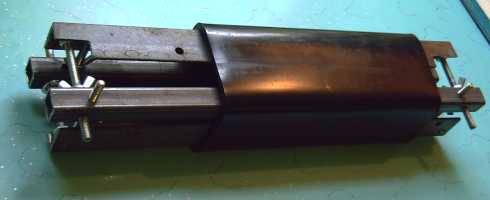
A jig to make round 3" ABS pipe rectangular. Using the two types of
former pieces, square bar and angle iron, resulted in a somewhat skewed
diamond shape, not quite a rectangle. It is also a bit under 3" across
the long side instead of a bit over. The next one will be wider but
thinner.
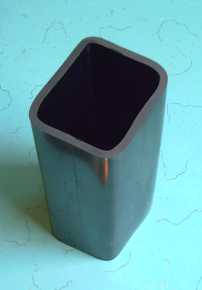
The tube, with rough ends and then with the ends sanded. Even with
slightly rounded corners and skew, this is a much better shape for flat
battery plates than a round pipe!
The next version will have four identical corner formers
and a better system of pushing them apart. Four of the eight wing nuts
can be on the outsides as long as they aren't over 3" long, but one end
has to fit through the 3" tube before forming. At least a couple will
have
to be removable so the jig can pass through the unformed pipe.
With the formed case sides rectangle, the only seams are
at the top and bottom joins, much improving the chances of getting a
sealed
battery.
After forming,
the cases are sawed flat top and bottom (if
necessary),
and then sanded very flat and smooth. Inspect for complete flatness
with no unsanded areas. Set the flat top or bottom piece onto the case.
Hold it up to the light, and if you can see any cracks of light between
the pieces, re-sand.
Once satisfied, dip a "q-tip" in the "aerogloss clear
gloss"
model airplane dope glue (or other ABS solvent glue) and carefully coat
the entire rim of the case
with no gaps. Put on the bottom cover piece. Carefully weigh the
assembly down or clamp it, to press the two pieces together firmly at
all points
until the cement sets.
Of course, if I could simply find injection molded cases -
or rectangular plastic pipes - of suitable material, size, shape and
wall thickness, it would make forming them in the oven superfluous. So
far, I've had no luck.
Another idea that occurs to me to try out in October, now
that I've thought of heating the plastic, is to make cases from flat
pieces and then heat them in the oven until soft, perhaps arranged with
weights pressing the seams together. A bit of "melting together" might
just impart the needed strength to the joins, including the top or
bottom cover. This might - possibly - be easier, and would provide
complete control over the dimensions. (On the other hand, I find making
every edge of every piece perfectly straight and smooth so the seams
are "seamless" isn't trivial even if they can then be made strong
enough. Somehow, Plexiclass does much better cuts than I do - it might
work out well if I have the pieces cut there.)
Electrochemical
Starting Conditions & Manganese
Until now I've been putting "uncharged" chemicals in my
batteries. In reading I've seen people putting chemicals in in
charged condition. Nickel hydroxide is bleached with 10% NaClO to
oxidize it to nickel
oxy-hydroxide, and metallic
zinc powder is used along with some zinc oxide. Since the battery is
supposed to be positive limited to prevent hydrogen gas production (ie,
the nickel's charge runs out before the zinc's does), it makes sense
that perhaps some of the negative electrode should be installed as the
metal,
the "charged" condition, even if the positive is uncharged.
Plus, the only battery I've made that's really worked so
far is the nickel-iron one, in which the iron electrode had some steel
(impure iron) filings in it as well as iron oxide. (And it turns out
Fe2O3 was the wrong oxide: purified Fe3O4 powder is the right one.)
Perhaps using some "charged" negative
material is a key to success?
I bought a chunk of zinc and sanded some zinc powder off
it, but I think manganese could make a better negative electrode and
couldn't find anywhere in town to get manganese powder (or metal), so
it's turned from a simple $30 sample purchase into a $350 US import,
counting getting some more monel powder as it's the same company
(micron metals) and I'm almost out anyway. Manganese dioxide is
available at pottery supplies and I have some, but this is an (overly)
UNcharged state for a negative electrode.
For a negative electrode, manganese seems to have great
potential energy in alkaline solution: about 1.5 KWH/Kg. That compares
favourably with
zinc at about 1.0, the best metal hydrides at about 0.8 or cadmium at
0.4.
That's without counting the OH's in the compounds and in
practice none of these theoretical figures will be achieved, but the
manganese looks like a very good bet! I think the reaction voltage of
-1.56 volts should be okay -- after all, the lead oxide <=> lead
sulfate reaction in lead acid batteries is +1.68 volts and that works.
But if it
proves a bit too high in alkaline solution, it could work in a salt
electrolyte (probably around -1.3v), still a higher voltage than zinc
(~ -1v).
139/58.7
Mn + 2OH- <==> Mn(OH)2 + 2e- [-1.56v]
The discharge reaction may carry on to Mn valence III in alkaline
solution:
Mn(OH)2 ==> Mn2O3 [-0.25v]
or just possibly:
Mn(OH)2
==> MnO2 [-0.05v]
It is also possible the reaction, in alkali electrolyte,
may proceed straight from Mn
to Mn2O3, and the voltage is likely to be lower
rather than the sum of the two valence changes, perhaps -1.4 volts
instead of -1.56. But then it should move 3 electrons per Mn atom
instead of 2, multiplying the amp-hours by 1.5 and reducing
self-discharge, so that could actually
be an advantage.
Manganese has a confusing array of reaction possibilities,
but the reaction products mentioned for a negative electrode
are all solid and likely to be trouble free. In salt solution, reaction
is likely to end at valence II as going to III will no doubt become a
positive
voltage
reaction instead of weakly negative.
Lithium Hydroxide
Edison used lithium hydroxide to improve the conductivity
of his nickel hydroxide positive electrodes. How it works evidently
isn't clear,
but it does. I've decided to try it in both nickel and lanthanum
electrodes, and also perhaps in the lead-acid batteries, where it might
help desulfate the lead oxide plate.
I couldn't find lithium locally except as carbonate. (One store can
sell this
over the counter, at another you need a "prescription" to buy it - such
is Canada's maze of arbitrary chemical restrictions.)
It turns out the hydroxide can be made from the carbonate by putting it
in solution with calcium hydroxide in a swapping reaction. I weighed
the ingredients carefully so as to have very little left-over unreacted
stuff:
Li2CO3(aq) + Ca(OH)2(aq)
==> LiOH(aq) + CaCO3(s).
The calcium carbonate precipitate is filtered out, leaving
the lithium hydroxide in solution in the water. I bought a coffee cone
filter at Cairo Coffee to filter it with. (The merchant made the
mistake of asking me how I planned to use the coffee filter - I doubt
the
answer was at all what he expected and he offered little advise!)
The only things that aren't clear are how much water to
use and how long the reaction takes... seconds? minutes? weeks? Too
much water and the LiOH will be dilute, too little and it will all be
somewhere within the sediment, or even some will come out of solution.
I also had to buy calcium as carbonate rather than as
hydroxide. The procedure for converting that is simply to put it in a
pottery kiln and "calcine" it:
CaCO3 + ~900 degrees C ==> CaO + CO2
100 grams of CaCO3 shrinks into about 56 grams
of CaO, giving off 44 grams of CO2 (that's ideally - I get
about 57-58 grams). This calcium oxide ("lime")
turns into hydroxide ("slaked lime") spontaneously in water. The
temperature at which lithium carbonate calcines is too high for this
direct method. (Calcium also has the interesting property of losing an
electron, and, juggling the empty spot back and forth, can ride light
beams and thus escape from the sun to wander through space.)
In theory, I can dry and re-convert the calcium carbonate
to hydroxide again after making the lithium hydroxide, ready for the
next batch.
New: The Lead Battery Project
September Details
Fanciful Ideas, More Modest But Effective Results
Inspired at the end of August by stories of people
reviving old lead-acid
batteries with alum and epsom salt, I decided to look into the idea
myself. The possibilities for improvement of the venerable lead battery
seemed exciting:
1. If they had a higher current capacity, as some were
saying they seemed to have, that would have some beneficial effects:
a. A smaller battery could start a car engine, potentially
slightly reducing
vehicle weight.
b. Fewer batteries in parallel would be needed to provide enough
steady-state current for electric driving. This could reduce the weight
of batteries needed simply to get the car to operate well.
c. At a given current, the amp-hours would be increased.
Lead-acid
battery capacity (amp-hours) is usually rated for gradual discharge
over 20
hours. Used up in one hour of electric driving, the
amp-hours actually available might be only perhaps 60% of the rating.
With
greater current capacity, the rate of discharge should be less limiting
- maybe 65% to 80% might be usable.
2. There seemed to be promise of increased voltage as well. 15 volts
instead of 12 would mean four batteries in series would replace 5 for
60 volts, for example, a 20% battery weight savings. Higher voltage
would be set by adjusting the pH of the electrolyte.
3. Much of the ongoing cost of electric driving is for replacing
batteries. Tripling the life span, as is
apparently the least expected, would dramatically cut that cost.
4. If lead-acid batteries are discharged too far, they are soon ruined.
It seemed likely that they could be made less "fragile", less prone to
serious
damage from overdischarge.
For a "best case" view, saving 20% of the battery weight
by higher voltage and 20% of the remainder by higher current yielding
higher amp hours is a total of 36% less weight or 36% fewer batteries,
eg, 1000 pounds becomes 640, or twenty 50 pound batteries becomes 13.
And a 400 pound vehicle weight reduction itself should save at least
another battery, so make it 12 batteries, 600 pounds.
And if the fewer batteries should last four times as long, long-term
battery replacement expenses would be just 15% of the previously
expected amount!
What experiments over the month showed was that adding
sodium sulfate (or sodium hydroxide) cleaned the battery, evidently
removing corrosion and sulfation, but that the pH always went back to
1, so there was no way
to up the voltage or to operate the
battery at a less hazardous level of acidity.
Those who aren't interested may wish to skip "The
Experiments" and go directly to the tentative directions for renewing
batteries.
The Experiments
Initial results weren't quite what I expected, but I
figured out much of what was happening, realized that most people
wouldn't, and realized that sodium sulfate would work better than alum
or epsom salt. Seems I've learned some chemistry from my other battery
work.
So I decided that it would be worth a diversion from other research to
make a small project out of it, the Lead
Battery project. I hope it'll be a short project.
Ah, here's the name... Feng Yuesheng would appear
to be the person who discovered that using alum instead of sulfuric
acid helps "restore" lead acid
batteries.
One thinks, "Wow, salt instead of acid! Way safer!"
However, this is evidently not the case. After filling a
battery with epsom salt (magnesium sulfate), which has
a pH of around 5.5-6.5, and charging for perhaps 1/2 hour, I checked
the pH
and found it was 1 - strong acid! The magnesium was probably on the
bottom as
insoluble magnesium hydroxide.
Apparently the charging-discharging reactions still make
sulfuric acid, using hydrogen from the water and sulfate from the salt.
That means the cation(s) of the salt are "left over" in the reaction,
and would make hydroxides. [Below, HOH = H2O. Water
breaks down into "H+" and "OH-" ions, so I like to think of it
conceptually as H-OH.]:
Alum: NaAl(SO4)2(aq) + 4HOH(l)
=> 2H2SO4(aq)
+ NaOH(aq) + Al(OH)3(s)
Epsom Salt: MgSO4(aq) + 2HOH(l) => H2SO4(aq)
+
MgOH2(s)
Aluminum and magnesium hydroxides are almost insoluble -
they'll settle out on the bottom. The one sodium hydroxide of alum will
remain in solution. It's alkaline and it's probably a reason for
improved performance, but it doesn't balance out the two
molecules of acid and the pH will remain near the bottom of the scale.
Somehow adding epsom salt to the acid evidently renews the
battery, but the
electrochemistry actually appears to be unchanged. Perhaps simply the
increase of acid is what was needed. Or, it may - possibly - be
that the magnesium hydroxide settles on the surface of the plates and
improves the
conductivity of lead sulfate so the battery gets "desulfated". This is
more doubtful.
The sodium sulfate is a different story because sodium
hydroxide is soluble:
Sodium Sulfate: Na2SO4(aq) + 2HOH(l)
=> H2SO4(aq)
+ 2NaOH(aq)
Theoretically, the acidity and
the alkalinity cancel each other, leaving pH = 7,
neutral.
In fact, the two products should recombine
spontaneously to make salt
solution and water again. Instead of replacing acid with sodium
sulfate,
which I'd ordered but it hadn't arrived yet, I tried adding
sodium hydroxide solution to a battery that already had acid in it to
derive the salt. ("Caustic soda" is dangerous - see instructions below)
I used the hydrometer
to siphon some acid (also dangerous) out of the battery, bringing
the level down to
the plates. Results, on a battery that wasn't
working well anyway and turned out to have a leak, were inconclusive.
Finally the pre-made sodium sulfate salt arrived. I added
it to warm water to s.g. 1.25. Not surprisingly, it took about 5
liters and over a Kg of the salt - about 30 $ worth - to fill one
battery. The NaOH is much cheaper. But it turns out simply adding some
to the battery rather than replacing the existing acid is best.
The solubility of sodium sulfate is of interest: according
to Wikipedia it rises tenfold between 0 and 33 degrees C from 50 to
almost 500 grams/liter, and then doesn't change much above that. The
battery may have poor low temperature performance, and may be more
subject to freezing in cold climes.
The "usual" lead-lead battery half reactions with
"hydrogen
sulfate" electrolyte are:
PbO2(s) + 4H+
+ SO42- + 2e- <-->
PbSO4(s)
+ 2H2O [+1.685 v]
PbSO4(s) + 2e- <--> Pb(s) + SO42-
[- 0.350 v] (1.685 - -.350 = 2.035 v)
The voltages obtained with lead reactions tend to rise
with pH, as seen on
this chart from webelements.com:
Since voltages above 2.0 can't be used in aqueous batteries, it seems
evident that the lead-lead battery can't be an alkaline battery.
However, I suspected that by raising the pH somewhat with some acid
and some sulfate salt, voltages above the pure acid ones could be
obtained. Perhaps at pH between 3 and 6 we might see the positive
voltage go up to, say, +1.8 from +1.65, and the negative from -.35 to
-.5, yielding 2.3 volts per cell or 13.8 volts. Unfortunately, it
probably isn't practical to go much higher with the positive electrode.
+1.9 volts might be just workable if the charge is slow so that 2.0
volts isn't reached. The cells might then be 2.4 or 2.5 volts - 14 to
15 volts per battery.
At neutral pH (7.0), the battery bubbled strongly as it
was being charged. Evidently, the voltage of the positive reaction is
too high at neutral pH and the water was making gas instead of the
positive electrode charging. This was not unexpected. [Later note:
Actually, they bubble like coffee percolating coffee as soon as the
NaOH or Na2SO4 is added even without charging,
for quite a while, giving off SO2 gas. This is probably the
desired cleaning action that renews the battery.]
I added a some concentrated sulfuric acid to each cell
("1/4 cup" according to the measure), but the battery still bubbled,
and the experiment was halted for want of pH test paper. I had tried to
buy some at "Science Works" a day or two previously, but they were out
and I didn't know of any other supplier in town. I hadn't counted on
that! I diced up my last two strips into "microchip" pieces, but they
didn't go very far. The next day I found Van Isle Water Supplies had pH
test paper (after being directed fruitlessly to garden stores, wine
making places and aquarium stores). They looked very nice, but it was
over $40 for a pack of 100 instead of $4! I decided I'd just have to
wait for Science Works. Anyway, it would seem better to have something
to discern between pH 0.0 to perhaps 5.5 in fine increments rather than
these broad range papers, where it reads "somewhere between 1 and 3".
When Science Works finally got some in a couple of weeks later, it was
only a few jars and they'd only sell me two for now because others were
also waiting for some. The pH test paper famine continues in Victoria,
now with rationing!
Then, still without being able to check pH, I tried
another "deep cycle" old "dead" battery, adding "some" sodium hydroxide
to the acid. After a
couple of charges and partial discharges, it seemed to be working quite
well. The voltage seemed no higher though.
I tried adding a little lithium hydroxide (made per
"Turquoise Battery Project" above) to this battery to to see if the
current capacity might be increased - it worked for Edison, though in a
very different
kind of battery. I'll determine the current capacity just by seeing
what the immediate voltage drop is when a heavy load (eg 25 amps) is
turned on. Surely the less the drop, the better the current capacity.
But I doubt it had much effect.
If the current capacity is increased, not only can a
smaller battery start a car engine, but the effective amp-hours &
watt-hours
available at the continual higher loads of electric driving will be
increased, giving greater driving range, or the same range with fewer
or smaller batteries. Almost the same comments could be made about
increased voltage.
The batteries I've tried so far have been "brought back
from the dead" by the conversion. That's less of a feat than Jesus'
raising of Lazarus of course, but still it's a surprise that it should
be so simple given that everybody "has known" for over 100 years that
they "can't" easily be restored. Knowledge is power!
A result
The last battery done, on October first, had a bad
internal connection. It sat at about 10.7 volts, and connected to four
headlights, it instantly dropped to about
5 volts and made arcing sounds. After treatment, it would stay at 12.7
volts and it lit several lights fine. Though it still didn't hold much
charge, the bit it had increased 60% between the first and fourth load
tests, with some hours of trickle charging in between each test.
Tentative Lead-Acid Battery Cleaning/Renewing Instructions
1. Get a battery hydrometer (auto supply, eg Canadian Tire), rubber
gloves
(Grocery) a face shield (Builders Supply) or at least eye
protection goggles, and some sodium hydroxide (NaOH, caustic soda
- Borden Mercantile gardening supply or a soap making supply). (I
presume
you have a lead-acid
battery.)
2. There are two alternatives: use sodium sulfate salt directly (drug
store or compounding pharmacy) or make it using sodium hydroxide. I'll
describe using the hydroxide here for now because it's what I've mostly
been doing. The salt is safer to handle -- it's been used as a
laxative. But it will only go to around 1.125 density when dissolved
unless it's heated up to about 35ºC, at which temperature it's
much more soluble.
3. Put on the face shield (or at least eyewear) and
rubber gloves. Fill a jar with pure water, not to the brim, and put it
in a sink. With a small scoop, slowly add sodium hydroxide powder while
stirring. It takes minutes not seconds to dissolve,
and during that time it gives off heat. If you add too much too fast, a
plastic jar may melt or a glass one shatter, or perhaps the water may
boil. The powder and solution (it's also called "caustic soda") is corrosive
to skin and will blind eyes. When the water clarifies and isn't
too hot, you can
add more powder. Check with the hydrometer and stop when the specific
gravity is about 1.25 or so. I tend to add half, go have a coffee or
something, then come back and add the other half.
3. Put the lid tightly on the jar and rinse everything: sink, jar,
scoop, gloves, counter. Put away the caustic soda powder.
4. Now to the battery: In addition to face shield and gloves, shield
bare skin. Old
clothes or coveralls are an asset. Place the battery outdoors or in a
sink (bathtub?) where a spill won't do
much to anything. (Remember the acid will etch and eat stainless steel
if it doesn't get rinsed off.)
5. Siphon acid out of the battery down to the plates with the
hydrometer, into a jar. Put the lid on the jar. (What to do with the
acid??)
6. Add some sodium hydroxide, an equal amount to each cell. I'm
guessing 80cc per cell for a small car battery - maybe a couple of
hydrometer
fills worth. Keep the liquid level fairly low, not far above the tops
of
the plates. Leave the top covers off the cells!!! (Otherwise,
it might explode, spewing acid!) There will be a strong bubbling,
percolating action, bubbling off sulfur
dioxide gas. This seems to be the cleansing and renewal of the battery.
7. Charge the the battery, preferably still outdoors. It may bubble
furiously the first
2 or 3 charges and the covers may still 'explode' off if they're pushed
on -
that's dangerous.
8. Do some charges, and discharges down to about 11(?) volts to
recondition it. I use a halogen car headlight or two or four for a load
- they
draw about 3 amps each... and if placed strategically the light will
remind you not to accidentally leave the battery running until it's
dead again.
At some point the bubbling will be reduced to the point
where it is
safe to replace the battery covers. It seems no matter how much salt or
alkali is added, after the bubbling the battery pH is 1: strong acid.
Thus, there's probably a limit to how much sodium sulfate is useful or
desirable. Another question is: Does it just act once, or is there an
ongoing anti-corrosion or other beneficial (or otherwise) effect?
BTW: If you notice a white powder around the battery holes: if it's
long
thin "needle" crystals, it's sodium sulfate salt (Na2SO4) formed by the
acid (H2SO4) and the hydroxide (NaOH). (The other product of this
reaction is H2O) If it's simply
powdery it might be NaOH, nasty hydroxide, AKA "caustic soda". (If
there's liquid it might be anything.)
Whatever... put the covers on the holes after it stops bubbling and
hose down the battery.
http://www.turquoiseenergy.com
Victoria BC