Detailed
newsletter articles are posted on the Turquoise Energy
Ltd. website. Only these highlight/contents blips are included in the
email. Complete newsletter:
http://www.TurquoiseEnergy.com/news/TENews21.html
Department of Inventive Progress: The government's missing organ
Directions for Softening Epoxy Glue (eg, to Remove Magnets from Rotors)
Electric Hubcaptm Car Drive
Motor and Controller Project Detailed Report
* a mistaken
diagnosis - Hall effect sensors - New MC chip (sigh!)
Magnetic
Mechanical Torque Converter Project
Report
* Conceptual
Adaptation and Design Growth
* A test indicates it'll work better without magnets, so it becomes
purely "mechanical"!
* Works by inertias and masses - reminiscent of mechanical clock
escapements.
* First Mechanical Torque Converter proves itself vastly superior to
geared transmissions in every respect, doubles gas mileage. Adoption is
sabotaged by GM duplicity, and it's rejected by the automakers -- IN
1923!
Microcrystalline
Ceramic Motor Coil Cores Project Detailed Report
* No Activity - no
report
Turquoise Battery Project Detailed Report
* Design
Considerations: Dimensions
* ABS battery case forming tool #3.
* At Last: The awesomely powerful flat-plate electrode compactor
mega-press!
* Squashed stainless steel mesh to replace "perforated nickel sheet"
for pocket electrodes?
* Veegum, CMC gum, xanthan gum for electrode briquettes
* Semipermeable Membranes
* More on Manganese; Certain Rare Earths
The Lead-Acid Battery
Project Progress Report
* Overview
* The plate cleaning reactions figured out...(?)
* October Quantifying Experiments
* Instructions for Renewing a
lead-acid battery with sodium sulfate salt.
* More & long term testing is needed to get hard figures
& statistics.
Newsletters
Index/Highlights: http://www.TurquoiseEnergy.com/TENewslettersIndex.html
Construction Manuals for making your own:
* Electric Hubcap Motor
* Turquoise Motor Controller
http://www.TurquoiseEnergy.com/
While nothing more is actually finished and ready to use,
this newsletter is simply packed with strong progress in several areas
and also holds what I believe to be a fantastic idea for a new
government organ, the "Department of Inventive Progress".
Early in the month I made excellent progress with design
and tools for home
or small scale fabrication and formation of alkaline or salt
batteries,
whatever chemistry is chosen for the electrodes. Not only was the case
former improved and an acceptable large "seamless body" case produced,
but a
solution to another intractable problem, compacting electrode materials
into briquettes, was found and the press made. As so often happens,
complex and expensive solutions were being visualized (hydraulic press
equipment) while a practical, simple solution (torque down some bolts)
was just a concept away. I suddenly visualized that solution in the
first days of
October.
The lead-acid battery renewal project proceeded apace, a
couple of dozen battery cycling tests being run.
Yes, it would seem lead-acid batteries now can be de-sulfated -
renewed - fixed - and made long lasting - simply by adding an
electrolyte additive: sodium sulfate salt. There is good promise that
they will
potentially last 3 to 5 times as long as previously, ten or twenty
years
instead of three or five. This suddenly makes them a much more
practical choice for off-grid energy storage and electric cars. The
prognosis is so far based on other peoples' good results with alum plus
seeing that sodium sulfate is chemically the better salt. So simple it
seems just
too good to be true, but there it is!
I've been publicizing it on some
battery related chat lists to spread the good news, gratis, hopefully
far and
wide. There is skepticism. Experiments continue to determine best
quantities to add and to put actual performance figures to the
"anecdotal evidence", but firm figures to convince the skeptics,
especially for increased life span, will take time and effort, and it's
not my prime focus. The project could really use a full-time
researcher... perhaps a university grad student.
It dawned on me that the government is missing an organ, a
"Department of Inventive Progress" overseen by a government
minister, and that that lack is a major
stumbling block in advancing civilization, from doing things from
adopting concepts for improved and updated methods of government when
good ideas appear, to paying inventors so original inventions happen,
and
then
liaisoning with industry for commercial adoption to ensure that they
aren't cast aside and wasted once invented. (Another great example of
an invention cast aside with no one looking out for the public interest
also came to light this month: George Constantinesco's 1923 Mechanical
Torque Converter, which I write more on in this newsletter.)
I spent a couple of weeks
on the project of writing and explaining the idea in some detail to
Canada's Minister of Finance with whom I had had previous
correspondence on the subject of funding for inventors. I CC'ed to my
M.P. Dr. Keith Martin, who had put me in touch with the minister, and
to the Premier of BC, to whom I had also complained earlier about the
complete lack of funding. Whether this effort will bear fruit I don't
know, but I've now done what I could.
I also offered to speak on the
subject, "Hidden Barriers to Inventive Progress and the
Government's Missing Arm" at Island Tech '09 on
November 13th following their request for speakers, but was turned down.
As I was spending my time writing, I was also considering
how best to make the magnetic torque converter work. The
project
details evolved considerably in my head up to the last week of October
without building anything more physically, and I felt I now had a
more or less final design for a prototpye that would actually drive a
car. I started making it on October 25th and got the basic assembly
made that day. Construction goes faster when you know what you're
building.
Then on testing simply by turning the rotors by hand, new
design ideas arose one after another, and the "moving target" plan
shifted yet again. Now the torque converter will use masses and
inertias and no magnets, and so will be mechanical rather than
magnetic. Looking up that idea revealed that mine won't be the first
mechanical torque converter, and that their performance is simply
amazing. Using one will surely allow a 5 HP electric motor to run a
car. Mine will be the simplest one to make and easiest to understand,
with the fewest moving parts - one. That's not counting the input rotor
(which is the motor) and the output rotor (which is the car wheel).
November holds considerable promise for definite results!
Department of Inventive Progress:
the government's missing organ
Canada's Minister of Finance, the honourable James M.
Flaherty, had replied during the summer to a letter I wrote in the
spring about the possibility of getting funds to be made available to
inventors via an inventors professional association that I had proposed
and tried to organize.
My letter followed, first, my e-mail to my M.P.,
Dr. Keith Martin, which was simply a "FYI" about trying to make an
association, and then, a letter that Dr. Martin wrote to the minister
on
the subject. (Dr. Martin had tried unsuccessfully to find me funding
for
the wave power project a couple of years previously.) I saw that his
letter didn't explain things in sufficient detail to be likely to cause
the minister to act, so I followed with my own.
The reply showed the minister, like most everyone, had no
idea what the problem was or that there was a problem. I spoke of
support for "inventors" and "inventing", but his reply spoke of
Canada's support for "businesses" and "business innovation", as if they
were the same things. Meanwhile I had found there weren't enough
inventors around with the interest and the time to try forming an
association and had given up the idea.
I just thought, "Well, that figures - no point pursuing
that!" For quite a while I let the matter drop. This month I was using
the back of the minister's reply letter as scrap paper to write some
battery test results on. Seeing the letter again I thought, well,
nothing ventured, nothing gained - why not write again and try to
explain better?
I would describe how inspired individuals invent
new solutions, not companies (and still less "consortiums of
companies" per SDTC), and how impossible it was for inventors to
actually access funds that were supposedly made for doing "innovative"
things, forcing them instead to find other work that would allow them
to live and eat.
And for an excellent example of how government was unable
to recognize solutions and act to bring about the very progress it was
trying to achieve, I had no farther to look than
my own recent experience. How absurd was it that
$10,000 couldn't be
had by - surely - one of Canada's most experienced and accomplished
inventors, to
prove that a practical design of floating ocean wave power
units would work. If it did, it could well save three billion dollars
and a major tract of Peace River valley land? I had taken the case to
my MP and the BC Premier's office - the highest levels of government
short of the prime minister - and no one could suggest a source of
funding that proved accessible when investigated.
Early in the writing, inventive inspiration struck. I
suddenly realized the problem is that the government is missing an arm!
Both
the education department that funds university research and the
department of industry that funds corporate developments feel, probably
rightly, that inventors, inventing, inventions and the progress of
society and civilization are outside of their mandates - hence the
non-support for inventors. There's no Department of Inventive
Progress headed by a government minister to
enable and foster the advancements the government and people want
to happen.
No one notices it's missing - the store shelves don't
empty, there's no disorder on the streets. But the effects of its
absence have gradually shaped our world.
For example, we've all wanted electric cars for decades.
Inventions
help, but there's never been a technical barrier - there were electric
cars before gasoline cars - what has been the
hold up? The Department of Inventive Progress would not only fund
promising inventions, but make sure that once invented and proven they
don't go to waste, get spirited away by "dog in the manger" vested
interests or tied up in government red tape. It would identify and work
to overcome barriers to
adoption of
desirable technologies and ideas, to enable, foster and ensure motion
towards progressive goals.
My letter proceeded along those lines. I spent a couple of
weeks on it, with supporting documents. I sent "CC"s to Dr. Martin (one
of parliament's top speakers and legislators) and to the honourable
Gordon Campbell, Premier of BC. Whether it will bear any fruit, I can't
say. But I think it's the right idea, and I'm glad to have taken the
time
to figure it out and to say it.
How to Remove Epoxy Glue to
Disassemble Glued Parts
This has general applicability as well as specific. I'm
writing it up because I've read it's "not really possible" to
disassemble epoxy glued parts once the epoxy has set, and there are in
fact ways to do so if it's important enough. My brother Stuart, a
biochemist, suggested trying vinegar or amonia. I won't do "1, 2, 3"
instructions as situations will
vary.
The first couple of times I had to remove supermagnets glued to
a steel rotor, I put the rotor in a bath of vinegar for a week or more
until the magnets were loose. But the magnets were quite corroded by
the acid by that time.
Then I tried sodium hydroxide, again for a week or more.
The steel metal and the supermagnets didn't corrode in that, but it
didn't seem to work as well. Here I
first put a 14" crescent wrench across the magnet and tried to twist it.
Then I hit on "Draino". It has sodium hydroxide plus some
other chemicals. That seemed to work as well as the vinegar or better
without
corroding the metals. I think I dumped in about 1/3 of the can into 3
or 4 liters (quarts) of water.
These chemicals don't dissolve the epoxy, at least not on
the time scales I used, but they soften it enough to make it possible
to break the parts free.
The next time, I didn't want to wait a week if I could
possibly help it. So instead of a plastic bucket, I put the rotor and
Draino solution into a big canning pot and simmered it on the stove for
a few hours. (I put in an aluminum chunk to keep the rotor magnets from
clamping onto the bottom of the pan too hard. The aluminum corroded
quite badly. (oh ya... aluminum in sodium hydroxide is a no no -
perhaps the vinegar is a better bet for aluminum parts. I haven't tried
it.))
I took it outside, pulled out the rotor and hosed off the
chemicals, then I put the big crescent wrench on a magnet and hit the
handle with a hammer. Most of them came loose with the jolt, but a
couple of magnets shattered. To get the very last one of these off - I
should say its remnants - I put it back and simmered it a while longer
and then soaked it overnight in the Draino solution. Then it/they came
off.
Sodium Hydroxide and Draino are
dangerous chemicals. They can burn your skin and blind you. ("Blindness
is forever" - chem prof.) Wear face/eye protection and rubber gloves.
I had an accident regardless of precautions when I picked
up the pot: the magnets yanked out the stove burner, ring and drip pan,
and then dumped the burner face down on my kitchen floor. It had been
on low, but it was enough to burn a black spiral into the beautiful lino. There's a warning if you
use this technique to unglue a magnet rotor!
The Electric HubcapTM Vehicle Drive Motor
October In Detail
Motor & Controller
The design for the Electric Hubcap motor and the
(updated) design for the Turquoise Motor Controller are on the
web. They are "finished" as far as the original intent to make a motor
and controller that work for the drive system. I updated the motor
controller manual again this month with a clearer schematic of the
power MOSFET transistors and supporting components of the heatsink area.
A system to propel a car now only needs a working Carmichael
Magnetic Torque Converter, the subject of the next section. The
motor and torque converter unit now weighs about 56 pounds.
Magnets and Wires
I was finding that the motor didn't want to start going
very well on the bench, and I mistakenly attributed this to my "skip
tooth" magnet configuration. In fact, the problem persisted when I'd
changed to just six whopper 2" x 2" magnets. It was actaully swapped
phase power wires to the motor, ie: BCA instead of ABC, when I wired up
the new APP connectors.
Come to think of it, it was working just fine with the
"skip tooth" magnet arrangement on the car previously.
It's too bad I didn't recognize the problem before I
changed the magnets: the "skip tooth" configuration didn't get a fair
trial to see if it might in fact be superior, similar, or not as good.
However, having come up with a way to soften the epoxy glue and get the
magnets off a rotor in a day opens possibilities for trying things like
that out more easily.
Magnet spacing options worth comparing:
* The six double size magnets
* Six pairs of regular (2" x 1") magnets, all twelve evenly spaced
around the rotor.
* The "skip tooth" arrangement with 18 positions, 12 occupied: NxNSxSNxNSxSNxNSxS.
* Close regular magnets in 18 positions (6 gaps): NNxSSxNNxSSxNNxSSx.
(Not so different from the six big magnets.)
One of these might have highest starting torque, another might have
more even torque, etc.
Other Motor & Controller Developments
I've decided to order some hall effect sensors to try out,
as they appear simpler to install and use than the optical position
feedback system.
It seems the MC33033 brushless motor controller chip is to
be
discontinued, but it also seems I've missed seeing some more recent
chips that may be better.
I looked one up that appeared it could be
quite good and would be a single chip solution, as it has the high-low
mosfet drivers built in. (Only good for 50 volts instead of 200 or
600... but this is a 36 volt motor, so hopefully it should just make
it.) Maybe I can find one with regenerative braking built in!
I'm not looking forward to designing a third circuit
board, however.
A Few Thoughts on Magnet Safety
It occurs to me that with a measured 25 pounds of force
required to pull a small steel cylinder away from a supermagnet, when
only a line of metal is in contact, the force needed to pull two
clamped together supermagnets straight apart must be at least hundreds
if not 1000 or 2000
pounds. This potential crushing force is why it's a serious hazard to
get a finger between two of them.
Here's a little anecdote to show how innocently magnet
accidents can happen.
In the rotor work for the magnetic torque converter, I was
working in the kitchen because
there are simply too many metal things around in the shop. I was
sanding
the (previously used) magnets clean and setting them 16 inches apart
on the kitchen floor preparatory to epoxying them on. I decided a
couple of them were too much in a traffic area and should be moved
elsewhere lest I kick one.
I went to pick them both up to move them... both at once
in the same hand. Oops! Of course, this did the very thing I most
wanted to avoid: brought two magnets together, with my fingers there.
Luckily I wasn't gripping the first magnet in my hand very strongly,
and it jumped out of my hand as the two clapped together.
Neither one shattered, and I used the jig (see torque converter
project, below) to get them apart.
I wonder if it might be good safety policy to get some
tongs (eg stainless steel or plastic) and always hold the magnets with
the tongs, never touching them by hand at all. I can also see this
would make it awkward to get them off the strip, apply the epoxy glue,
and get them onto
the rotor. I mostly handled the big 2" x 2" x 1/2" magnets with pliers,
except when I was applying the glue. Stainless steel or other
non-magnetic pliers would have been much better if there was such a
thing.
Then when you're done, there's the dangerous rotor with a
bunch of magnets all on one or both faces, capable of clamping onto a
piece of metal with several tons of force!
Magnetic
Mechanical Torque
Converter Project:
Torque Leverage Without Gears
September Details
This writeup became something of a diary, with ideas
coming fast and furious throughout the letter part of the month. I
cleaned it up a couple
of times to reflect the latest thoughts... and then more ideas came,
making what I'd just written a day or two before obsolete.
The Magnetic Hammer
While writing the letter about the "Department of
Inventive Progress", I kept thinking at odd times about how the
magnetic torque converter might work.
I had had the inspiration that magnetic pulses should
provide
short moments of high torque, while for the remainder of the motor's
rotation, it would have no load and thus would be able to resume its
speed in order to impart the next torque pulse.
Then for some reason, I intended to put six pivoting
magnets on the output (wheel) rotor. Since there were ten magnets on
the
input (motor) rotor, five of each polarity alternately, each magnet
would produce its torque pulse at a different time, many times (30, I
expect) per motor rotation. That would be smooth, but it would just
average out to more pulses of a fairly low torque instead of producing
the highest possible peak
torque and then motor speed recovery time.
What's needed is the torque pulse of, eg, five magnet
attractions at once, to get the car to start to move. So now
I've put five magnets on the output rotor instead of six,
and five
attracting magnets on the input rotor. These will all meet at the same
time, five times per
revolution of the motor. Five magnets at once will naturally give five
times
the torque
of a one magnet pulse, one fifth as often. It will then be five times
as hard to hold back the car wheel and prevent it from starting to
turn. (It is unnecessary to twist the magnets per last month's idea;
they are left
"on the flat", which will work equally forward or reverse.
Since all the magnets were now to act together, they
wouldn't
need to be on separate pivots: the entire plate of magnets on the
output rotor can move at once, and has become the "slip plate".
This is the first arrangement I've hit on that would
surely have enough torque to start moving cars up hills and
accelerate them well, rather than just gradually get them moving
on level ground.
The next idea was that instead of moving the output rotor
magnets up and down, the plate holding them should be free to turn a
couple of inches, to twist back and forth relative to the car wheel.
Here's the sequence of operation, and for simplicity we'll say the
output rotor doesn't
turn:
1. The input and output magnets aren't in close contact. The
motor, spinning freely, picks up speed.
2. The magnets of the input rotor start to overtake
the output rotor magnets. As they attract, the output rotor magnets are
pulled backwards. The magnet plate twists freely until they line up
with each other. No
backwards force acts on the output rotor and car wheel.
3. As the input magnets continue to turn, the plate starts twisting
back again, with the output magnets freely following the input
magnets.
4. Then the plate hits its end stop. The output magnets try to continue
to follow
the input magnets. They can't unless the wheel turns, but the
attraction is very strong, and a whopping torque pulse is produced. The
motor loses speed at this moment. Some of its momentum energy is
transferred
to the output rotor, the car wheel, which tries hard to turn. (If the
wheel is turning and not too much torque is required, motor and wheel
lock together magnetically here, providing a lossless direct coupling.)
5. The input/motor magnets pull away from the output
magnets, then the motor starts to pick up its lost speed.
6. By the time the input magnets start to overtake the next set of
output magnets the motor has regained its speed and all repeats, every
72 degrees of rotation.
This works equally rotating either direction. The
magnetic pulses all pull in the direction the motor is turning. The
spots where "equal and
opposite" force should be pulling backwards are nullified by the free
twisting of the magnet plate, like a bicyclist pedaling backwards.
The faster the motor is turning, the less time there will
be between pulses for the car to try to roll back to where it was. But
even at just 300 RPM, there are 25 torque pulses per second.
Towards the end of the month I considered the mechanical
details for an actual prototype output rotor implementation. There seem
to be at
least two considerably different main arrangements to achieve the above
effect: to have the magnet plate slip back and forth within the frying
pan, or to have the plate affixed and make some bearing & stops
arrangement at the center shaft to allow the entire assembly to shift
back and forth.
I selected the former as being the easier to make, and
also the slip pins (or
whatever), which will suddenly hit their end stops as the motor turns,
will have much less torque pressure behind them at the rim than near
the center, reducing wear and tear.
Nevertheless, I'll probably have to beef up the aluminum
slot ends with some strong spring steel end-stop springs or something.
But before I get too fancy I'll try it out as is to see how it works.
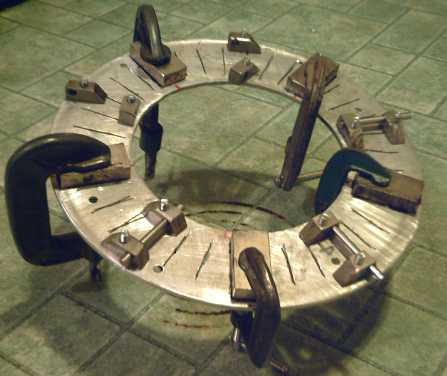
The magnets clamp themselves magnetically to steel.
Aluminum is a different case!
Later it was found that the epoxy didn't really adhere to the aluminum
regardless - magnets simply fell off under stress.
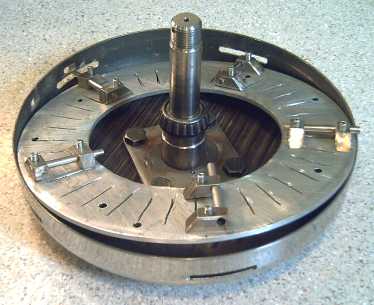
The magnet slip plate assembly.
(Before mounting the magnets.)
On the 25th I made the pins and their mounts, and cut the
slots in the frying pan rim. That's the main assembly. Then it occurred
to me that to compensate for having the extra magnets stuck on the
input rotor, I could widen the slots and allow the slip plate to rise
up
and somewhat away from the repelling magnets "giving them a miss" and
only use the attracting magnets.
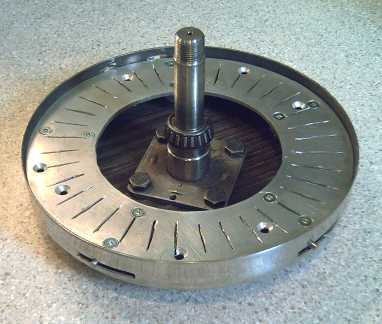
The complete output rotor.
The four black bolts hold this rotor and the axle, and hence the entire
system, to the car wheel.
I had made the input rotor earlier with 10 magnets, 5 of
each polarity
alternating. But the more I thought about it, the more I liked the idea
of just having the same few magnets, all the same polarities, on both
rotors. That way, the motor has the most time to speed up between "all
alike" torque pulses, which can be set to be as strong as desired with
the
magnet sizes and gap. On the 26th I finally decided to bite the bullet,
get the magnets off the rotor, and start again.
I put the rotor in a solution of Draino
and water. From previous experience I expected I'd have to wait a week
or so for the "epoxy steel" glue to loosen, delaying the final assembly
until November. Then I thought, hey,
why not heat the water - simmer it? That'll speed up the reaction, and
the motions
of the water will get the stuff in under the magnets better.
A "magnet accident" occurred in this. First, to put
it on the stove, I had
to put the rotor in a big steel canning pot rather than a plastic pail.
I
put a chunk of aluminum on the bottom so the rotor wouldn't clamp down
flat magnetically in the pot. Then I put it on the stove, and it
glommed down on the metal stove and
became hard to move. After a few hours, I went to take it outside to
see if the magnets would come off.
When I pulled hard enough (on a pot with
caustic soda and a supermagnet rotor - yikes!), it came off -- complete
with
the burner ring, the drip catch piece and the burner element, which
then fell on the floor, face down. It had been on "low" and the water
wasn't boiling, but by the time I'd set the pot of hazardous chemicals
and magnets down safely, the burner had melted a nasty black spiral in
my beautiful near-new kitchen floor, one of only two really nice
looking floors in the whole house! Visual appeal isn't my strong point,
but this made me feel rather sick.
The magnets mostly came off, but I broke the second one.
My technique is to get the magnet in the jaws of a 14" crescent wrench,
then hit the handle of the wrench with a hammer to twist the magnet and
break it loose. I hadn't quite closed the jaws and so the pressure was
on one corner and the middle of the other edge instead of spread out. I
got it off and was more careful after that, but one of the last ones
simply wouldn't budge. It crumbled into pieces. All ready to go in just
one day, except for this one chunk of rubble still glued solidly to the
rotor! (Anybody want some strong, jagged fridge magnets?) I put the
stove burner back together, put the rotor back in,
boiled it a while, and then left it to sit overnight. It came off the
next morning.
Reassembling the Magnet Rotor
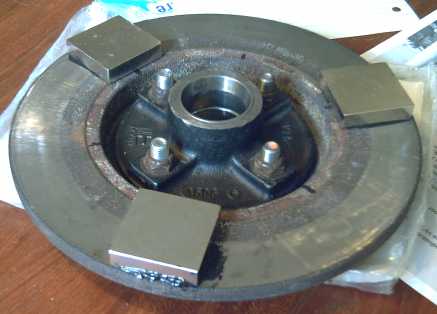
Magnet rotor with the first three 'whopper' 2" x 2" x 1/2" magnets
installed.
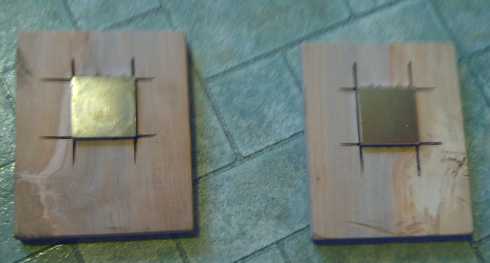
I used pliers pulling these magnets off the strip, and it wasn't easy.
I got two pairs clamped together and had to make this wooden jig
(arbutus, no finish) to separate them by sliding them apart. I used the
radial arm saw to
make the grooves and then chiseled out the squares. (Note the distance
between the pieces & magnets - they're only this close together for
the photo!)
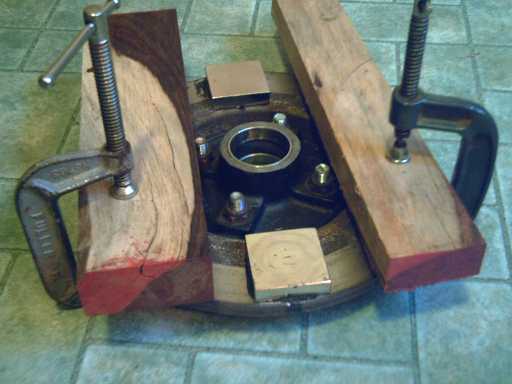
When installing the second three of these extremely powerful
magnets, prudence required making sure they couldn't glom onto the
nearby ones by fully covering them. (Rosewood sapwood with painted
ends.)
Always bring the magnet straight in to its position, not near the rotor
on the approach.
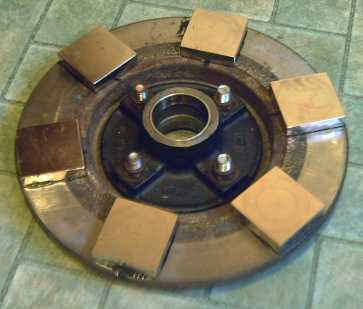
Finished motor side of the magnet rotor.
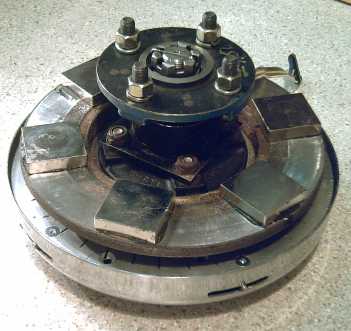
Assembled for a motor test run before installing torque converter
magnets.
(shown without motor stator)

Re-magneting the torque converter side. The spacers were required as
the magnets all
tried to slide up against the center hub until the epoxy set.
(Here I
didn't cover adjacent magnets as they are well separated. Note the foam
safety cover, held in place magnetically with sheet
steel, over the magnets on the other side.)
When I put the two rotors together on the shaft, I found
it
impossible to turn them relative to each other by hand. It seemed like
plenty of magnetic coupling to turn a car wheel. They went together
violently, and I had to use wooden wedges and spacer pieces to separate
them enough to pull them apart.
On the evening of the 29th I made a spacer to slip onto
the axle before the bearing, to keep the rotors farther apart. With a
gap over 3/4", I was able to turn the two pieces against each other by
hand. As long as there was slot travel, the plate would follow the
motor rotor rather easily, but on reaching the end of the travel, there
was about a 1.5" range where I could barely pry them into going further
- the torque pulse area. So that's around 7.5" out of about 37.6": 20%
of
the total range where the motor supplies torque, and 80% where it gets
to pick up lost speed. The maximum torque boost thus works out to
perhaps 5 to 1. With direct drive to the wheels, even Electric Hubcap
motors on all four wheels would have less punch for starting the car
moving than just one with the torque converter.
Well, that was the result at first. Then things got
strange: the forces dropped way down and there was the sound of things
sliding around when the rotors were twisted. Sure enough, three of the
five output rotor magnets had come loose! The other two I tapped off
easily with a hammer. I guess "epoxy steel" doesn't stick to aluminum.
My main concern is that it may be hard (read "not
possible") to start
the motor turning against the powerful force in the torque pulse area.
And the motor is bound to come to a stop in that very position almost
every time.
But the test, turning the rotors by hand, led to more
observations and ideas...
I note that there's a bit of lifting (ie, repelling)
force when a magnet is held between two of the output magnets rather
than over one. Perhaps it will be beneficial to arch the slots so the
slip plate can "rise" away from the input rotor during its turning.
A separate thought is to force the slip plate up
with an arch just before it hits the end stops. That way, the stops
would be gradual, gentle, instead of simply a sudden hit at the end,
and perhaps that's a key to having the motor able to start turning,
without losing the essential wheel turning torque.
Then on the 30th I had a substantially new idea, and the
more I thought about it, the more new ideas started flowing in all day.
I've been
keeping the twist plate light. What if, instead, it was made rather
massive, so when the pins hit the five end stops, much of the torque is
developed from the impact of the mass of the plate, rather than
directly from the magnetic fields. That way, the field only has to be
strong enough for the motor to carry the heavy plate back and forth,
not to develop the actual wheel-driving torque. Any torque ratio might
be achieved, and the magnetic fields could be kept light enough not to
hold the motor stalled regardless of stopped magnet positions.
It's conceivable with this design that one could possibly
use the motor rotor itself as the slip plate, driven back and forth in
a complex sequence with a computer program, and "hitting" the wheel at
only one or two points of revolution so it could get some speed up
before the hit. Yikes! On the other hand, the motor needs to spin to
really get up speed and develop power.
So I thought I'd stick with the present three piece
design, but add mass to the slip plate.
Another thought was: if all the magnetic fields are
attracting fields, and if
they are too strong anyway, why have supermagnets on both rotors? Why
not just have steel
blocks in their place on the output rotor? Heavy ones to give the
desired mass?
Then the next idea came in. If, instead of end stops, the slip
plate pins hit 45 degree slopes, there'd be flat "high" areas and flat
"low" areas, with 45 degree slope points in between. The plate would be
free to turn with the motor rotor. Each time the pins hit a slope (all
five at once), the plate would shift "up" or "down", and in the
transition, some of
its rotary energy would be transferred to the output rotor, especially
if the plate was massive. If the magnets were strongly attracting,
most of the force would be developed on the "up" slopes while the
"down" slopes would be a free ride. Once again, it provides short spots
of torque with long
areas where the motor has no load. It's a variant of the "clock
escapement" mechanism mentioned last month.
These ideas led to the next thought: If the plate simply
rotates with the motor rotor, why have a separate plate at all? Why not
just mount the pins on the motor rotor? Or, mount the plate on the
motor rotor, rotating with it but free to move in and out?
And then, what are the magnets for at all? why not just
use springs? or even, why not just make the pin mountings or plate
massive enough to impart their kinetic energy at the 45 degree slope
points without any particular springs or magnets forcing them one way
or another? The stopped motor would be free of any notable starting
load
no matter what the relationships between the stopped rotors. Since E =
1/2 M * V2, the torque developed would be a function of the
motor speed squared, as it ought to be.
With several attractive designs suggesting themselves at
almost the
end of the month, it was obvious there would be no electric car test
drive
in October, the anniversary of the motor first moving the car across
level pavement. I feel like I've just gone through several generations
of torque converter designs, any of which might be made to work, more
in my head than actually built.
Then there was the thought that if no magnets were needed,
it went from being a magnetic torque converter to a mechanical
torque converter. I started thinking, "wow, if it's just
mechanical, if it doesn't need supermagnets, it could have been
invented long, long ago, but it wasn't!"
Or was it? A web search on "torque converter" had turned
up
only hydraulic ones (as far as the eye could see). Then I had looked up
"magnetic
torque
converter", and though I found a couple of patents by that
name, I didn't find anything that actually was a torque converter as
such - they were just magnetic-tooth "gears".
Not so searching for "mechanical
torque converter"! It seems the first design - nothing like
my latest concept but achieving the same effect by similar means -
masses and inertias - was created about 1923 and an efficient automatic
transmission car (no gears!)
was made, and later, locomotives and other applications! So, it
actually was
invented rather
long ago! And there are some more recent patents. (What's the betting
they've all been acquired by oil companies and stuffed in closets?)
So possibly I may be re-inventing the wheel, but looking
over a few of the designs, at least I hope to make a much simpler, easy
to
make and to understand wheel, and my work will be unpatented "open
technology" available now, not in 2028 or so.
And, lets not forget the people trying to create
"continuously variable transmissions" with belts and pulleys since the
1970s. Laudable, and progressive compared to what's actually in use,
but this far superior solution had already been around for the taking
for
50 years - now it's headed for 100!
By the morning of the 31st, I'd decided on a specific
design (unless another new idea hits before it's made!):
The torque converter will be mechanical, not
magnetic. The plate - now an "inertia plate" - will rotate with the
motor rotor, mounted on six posts (smooth bolt bodies, between the six
magnets on the motor side of the rotor) that will allow it
to shift up and down as it turns. There'll be a steel slot just
inside the rim of the pan that the ends of the pins will ride in,
which will have a 45 degree bend, every 36 degrees around the rim (10
bends), alternately "up" and
"down". The pulse of torque each "hit" on a 45 degrees bend will
produce
would depend on the motor speed (squared), and will be adjustable
by changing the mass of the plate, adding or removing metal from steel
blocks. There'll be no resistance beyond slight friction to
starting the motor to turn. Thus it will never be stalled. The load on
the motor will increase exponentially with motor speed. (More
precisely, with the difference in speed between the motor and the car
wheel.)
45 degrees is the angle the watch makers say imparts the most energy
with the least amount of friction. It may be desirable to use ball
bearings on the pins to further reduce friction. Here's the path of the
slot around the rim of the pan, causing torque by repeatedly
forcing the inertia plate to suddenly shift sideways:
_____
_____
_____
_____ _____
>__/ \_____/
\_____/ \_____/
\_____/ \___<
Now to get those magnets off the rotor... again! ugh! (or
should I just keep them there, just in case they'll turn out to have
some use next week?)
George Constanesco's (1923?) Mechanical Torque Converter
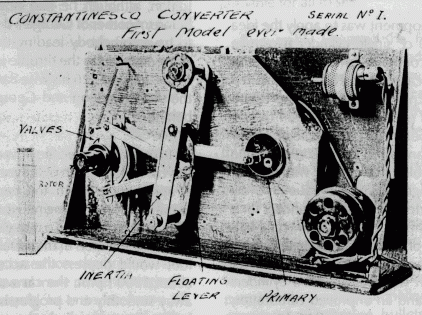
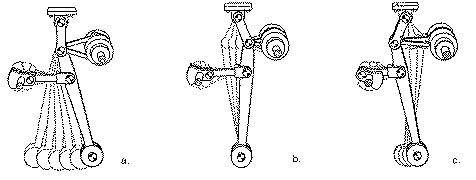
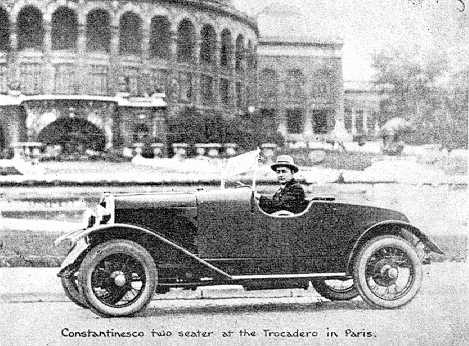
George Constantinesco's Mechanical Torque Converter: First
Prototype,
drawings, 1926 automatic car (with improved version of converter).
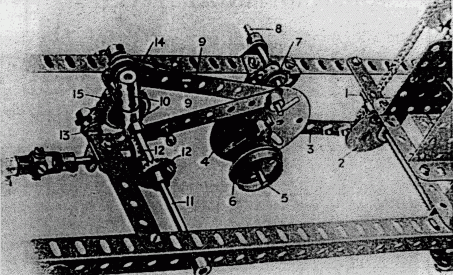
There's even a Meccano Set version for kids,
...but not one in your car!
Here's some text describing the impressive capabilities of
the mechanical torque converter:
(from http://fluid.power.net/fpn/const/const005.html
)
"George first successfully tested a Torque
Converter in a car in May
l 923, using an experimental model that had been built only for bench
tests.
He obtained an old Sheffield Simplex chassis and replaced the big 45 hp
engine with a 10 hp "light car'' Singer engine, and built a platform
on the chassis. This car was driven around the outskirts of London
loaded
with 10 people, including the inventor at the wheel, fig.
21, and later towed a lorry [truck] up a steep hill. As a further
demonstration
of the capabilities of the car, six inch wooden blocks were placed in
front
of the wheels. When the accelerator was depressed the car climbed over
the blocks smoothly and without hesitation, to the astonishment of the
bystanders. This test was merely to demonstrate the possibilities of
the
Torque Converter, because even a 10 hp engine was much larger than
necessary
for the production car envisaged.
"
That I'd never heard of a "mechanical torque converter"
before conceiving one myself is a good demonstration of how information
on the web is easy to
locate... IF you happen to know exactly what you're looking for
and
exactly what search terms to use.
It's also a good demonstration of how good inventions get
sidelined and collect dust on the backs of shelves. The mechanical
converters have
high efficiencies, and they can be made with wide conversion ratios
that completely eliminate
the
need for transmission gears. ("Forward" and "reverse" gears for
gasoline
engines were done at
the rear axle where there are other gears anyway, thus with
no extra transmission gearbox and its added weight and inefficiencies.
Electric motors on wheels will run either
direction and independently, eliminating all need for gears.)
It's apparently superior in
all respects, yet the
automotive industry rejected it. In fact, General Motors made a
lucrative sounding agreement with Constantinesco that prevented him for
some time from going to other car companies with the product, but
"then" chose not to make them - no doubt their plan all along - and the
lack of the agreed and expected royalties left him in financial
trouble. It probably wasn't the first, and certainly wasn't the last,
time the big automakers have acted in bad faith and contrary to the
public interest.
The industry chose instead, and continue to choose, much
larger engines than otherwise necessary, driving wasteful
fluid converters coupled to wasteful gear systems that need gear
shifting: giant, heavy dinosaurs requiring operator attention and with
an overall 30-40% loss of power (per Wikipedia etc.) in the drive
train.
Unbelievable! Why are we bailing out these corrupt,
moribund
automakers when their ships are full of gaping holes and they don't
lift a finger to repair them until water is pouring into the bridge?
Instead, why not fund creative
people having ideas and ideals, people like Constantinesco perhaps, to
become innovative auto makers and
bring progress and new industry? The 80 million dollars just in
bonuses that the 50 "top" stuffed shirts at Chrysler awarded
themselves last
year alone while their company was going down the tubes could have
given
someone who actually cares a very good start!
Here we can guess that a government "Department of
Inventive
Progress" would have been known and understood as the proper place for
Constaninesco to submit the prospective design, hopefully it would have
recognized the amazing potential, fostered development into a practical
product (ie, contracted him to make it and paid him the trifling sums
needed to enable him to create, prove and improve his design and live a
normal life), and then finally ensured the torque converter
would find its way into vehicle use to supplant the dinosaurs, whether
by means of
existing companies if they co-operated willingly, or by fostering new,
more
progressive companies to take over.
Turquoise Battery Project
October Details
Design Decisions: sizes
After finding that the 1/4" thick ABS plastic cases
needed to withstand considerable pressure to have a sealed battery, I
previously settled on 3" wide electrodes as
being (a) an even divisor of the 6" x 12" purchase size for
nickel-silver or nickel sheet metal and (b) the widest size likely to
handle the pressure well.
Then I thought I might as well simply split the sheets in
half and have 3" by 12" electrodes. But now I think that's just too
much to deal with at a time for home manufacture, and I'm shrinking it
(at least for starting out) to a more managable 3" by 6". I have made
an electrode compacting jig for that size, the latest and most
fantastic
tool for home battery making (below).
The newly made battery case forming jig (below) will
handle 13" cases, but I'm sure 7" long cases will be easier and luckily
no modifications are required.
With the 3" ABS pipe, it seems to work out that forming it
to 3-1/4" wide about a 2" width is obtainable, for eight 6mm thick
electrodes:
four bipolar cells or quadruple prismatic plate sets.
Voltage of course depends on the chemistry chosen, but
bipolar cells would make a battery with four times the voltage, eg, 2
volt cells would make an 8 volt battery, while prismatic construction
would make a single cell with four times the current capacity of a
single pair of plates.
For a "dry cell" with limited (non-flooded) electrolyte,
the bipolar "battery pile" construction is preferable because there are
no internal welded connections to potentially fail except one to each
terminal post.
In looking at the Alkaline Storage Batteries book
by Falk and Salkind detailing the state of the art in 1969, 3" x 6"
electrodes seems more than ambitious. Pocket electrode briquettes were
usually made 9 or 14mm wide and about 4" long (Edison's & Jungner's
original size, I think), and this size of small pockets were combined
into flat electrode plates maybe 3" by 4" or so.
I can go back to 3" by 12" (or other chosen size) later if
desired by making a new electrode compacting jig for that size.
Case Making
I improved the
torture rack for stretching three inch I.D. round pipe into 2+" x 3+"
rectangular. This forms it, stretching the 9.43" inside radius to about
10.75" to get the desired size rectangle. Hmm - that adds 1.3", no
wonder the
screws are hard to tighten sufficiently!
It seems to take 3 or 4 times, tightening the screws a bit
each time, heating for an hour in the oven total. Perhaps I'll try
getting it hotter next time, say 350ºF, and see if it's easier to
work with. I've gradually gone up with each case, from 285º to 300
to 325. Of course, I'd rather it didn't melt down -- and I really don't
want it to catch fire! At 325º leather gloves are just adequate
for turning the thumbscrews, but they might take less turning pressure
at 350 if the plastic is softer.
Another idea to try is to set the nuts so that when the
right size is reached, they're all the way in, touching the metal
tubes. That way you'll know when you're done without taking several
measurements, and the size will be more consistent. (The hex nut and
the wing nut are strongly tightened against each other to make a solid
"bolt head", and they can be set anywhere on the threaded rod.)
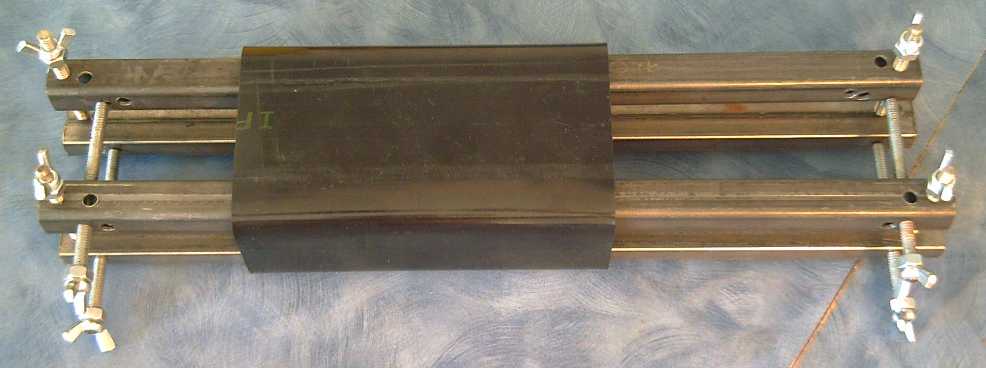
"Case Former - Mark 2" to make round 3" ABS pipe rectangular.
The plastic is heated in a kitchen oven to soften it (~325ºF),
then the screws are turned in until the pipe is square and the desired
size. Weights with aluminum top and underneath plates make the long
sides flat. Two new pieces (not shown) are to be inserted in future to
prevent the ends of the long sides from bending inwards in the middle.
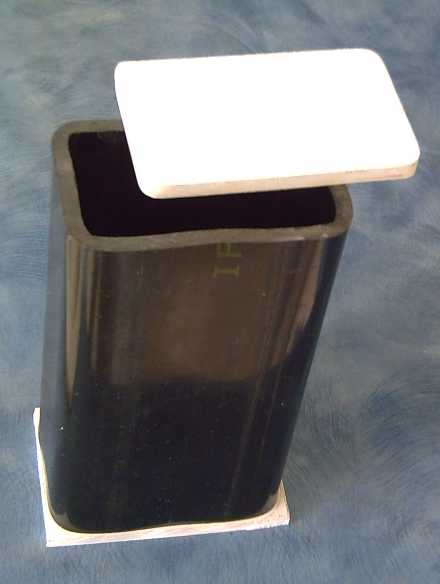
The case, ready for bottom cover glueing.
I'd rather put in a gasket and screw on the top cover. That would make
the batteries potentially repairable.
Interior size is 2" x 3-1/4" x 6-3/4" for four bipolar (or prismatic)
cells with 3" x 6" electrodes plus electrode side, top and bottom
clearances.
This version has the wing nuts all on the outsides where
they are easily accessible. Only two long bolts have to be unscrewed to
insert the rack through the 3" tube before forming.
The Awesomely Powerful Electrode Compactor Press!
A great answer hit me as I was considering possible pocket
electrodes (below):
How to compact the electrodes? Screw it! Sandwich the electrode between
two pieces of steel with many bolts all around the edges. Oil the bolts
and screw them up a bit at a time until they just won't go any farther.
If there's enough bolts for the plate size it should end up as a well
compacted electrode briquette!
Wow! So there's the multi-tons strength
press I've been wanting all these many months! Another of the several
intractable battery making problems is solved, suddenly and simply!
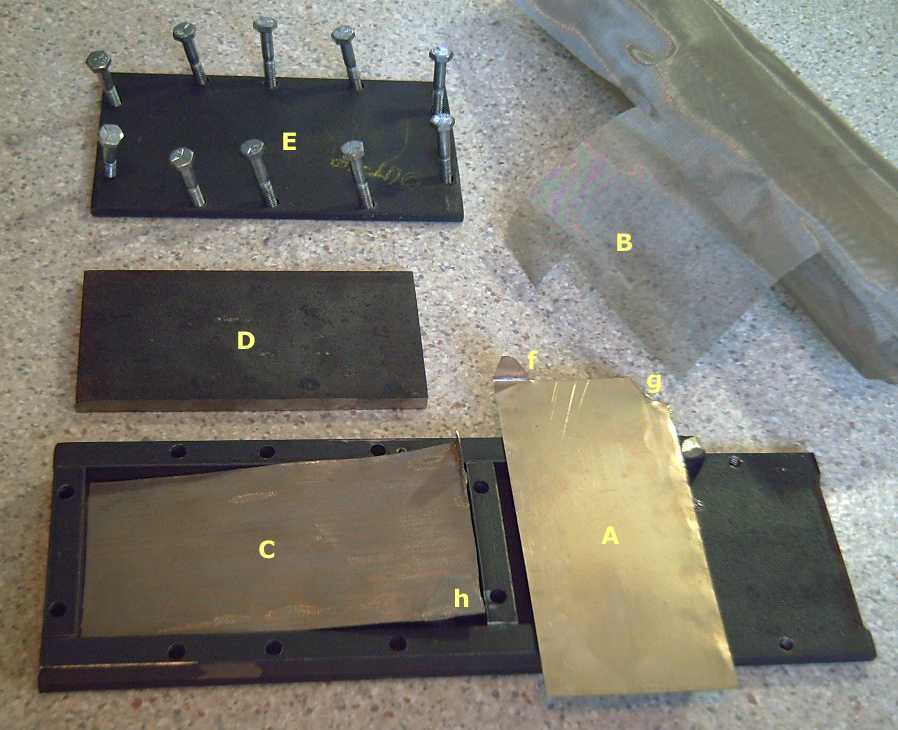
Electrode Compactor
To make an electrode, a nickel-silver or nickel electrode
collector plate (A) is covered by fine stainless steel mesh (B). The
12" plates to be connected to the terminal posts are cut especially in
half by hand "jogged" to make a tab (f) to weld to the post. The
missing bit on each side taken for the other tab (g) is filled in with
a small scrap of the same sheet metal under the mesh (h). The mesh is
cut a little bigger than the plate and is wrapped tightly around all
four edges for good connection between the active electrode material
pressed into it and the collector plate. For a two-sided electrode, the
mesh is wrapped all the way around. (This leads to the thought that the
metal sheet is perhaps not even needed for interior electrodes - it
could be a mesh-wrapped plastic sheet. Cheaper!)
The ready electrode plate (C) is placed in the bottom of
the compactor and the active material paste (of whatever formulation)
is scooped in and spread evenly. Depending on results, the edges may if
required be
lined with plastic to keep the material from sticking to the sides.
A plastic liner and then the punch plate (D) is placed
on top of the electrode "stuff" and the lid (E) on top of that. The
screws are inserted and gradually torqued tighter and tighter to
compact the electrode material into a solid briquette that is embedded
firmly into the conductive mesh.
Then the screws are removed and it's just a question of
getting it out in one piece. If I make one end wall removable, a
spatula
or whatever can be inserted under the electrode to pry it up.
The electrode thickness depends on the amount of paste and
how much it compacts. The sides of the press are 1/2" tall, and
the press plate is 3/8" thick. If the finished electrode is less
than 1/8" the press plate will need a spacer. If it all gets too thick
- more than 1/2" of uncompacted material is required or if it's the
second side of a thick two-sided electrode - I may need to replace the
sides with taller ones, or put extender sides above these. (Hmm, I do
have 1/4" and 3/16" side pieces for extenders - left over from the
previous design. Problem solved!)
Pocket Battery Pockets
Wanting something simple that actually works just to
say it does, I keep thinking
of the old "pocket electrodes" used since Edison's time in alkaline
batteries.
The stopper is not having perforated nickel sheet or tube.
(I e-mailed a company that says they make them in August, but they
didn't reply.) I have the
nickel silver sheets, but drilling hundreds of holes in a sheet would
likely just
waste all the fine drill bits the hobby shop has. I found perforated
brass sheet at the hobby shop, but that
would corrode quickly and attempts to nickel plate it have been
unsatisfactory - then when I cut it the new edges would need replating.
I thought a couple of times of the #60 stainless steel
mesh as a "perforated sheet", but it's about 80% open space and I know
the electrode material would simply make its way through.
But I started thinking "if only they made it with flat
pieces of stainless instead of round, it would be like a flat wicker
basket and mostly closed space." Then I thought, "Hey! Why don't I take
a piece and flatten it in the rolling mill?" (Hmm... stainless steel...
well, the rollers have hardened steel faces, which *should* be harder
than stainless and they *shouldn't* dent... theoretically!)
After several runs through the mill with two (very rapid)
annealings with the propane torch, the mesh wires were flattened to the
point where they occupied about 1/3 of the total space, length and
width, and so the holes were down to around 50% of the area. Hmm...
just *might* hold the stuff in! And the cross junctions were pretty
well mashed together for good electrical connections. (Better still, I
didn't feel any dents in the rolling mill rollers!)
And what's left of the thickness for strength? Hah! It's
now like a satin fabric. It's just 0.0025" thick - about like grocery
bag plastic! It's floppy in one direction, though the width still has
some
stiffness.
I may try it, but it's not going to work except at a very
small - experimental - size.
Gum for making Spongy, Cohesive Electrode Briquettes?
I asked about CMC (carboxy methyl cellulose) at Victoria Clay Arts as I
wasn't satisfied with my
electrode results, had seen "CMCs" mentioned as binders for alkaline
battery
electrodes, and had noticed "CMC" in the Seattle Pottery Supply
catalog. Evidently it's sold for pottery as a gum, "CMC Gum". I was
told
there's "Veegum"
as well. On looking it up on the web, it sounded like
Veegum is really more promising. However, near the bottom of the
excerpts copied from the Veegum info itself, it suggests combining both
Veegum and CMC gum for maximum effect:
VEEGUM and VAN GEL Clays (R.T. Vanderbilt
Company)
(Long excerpts...)
VEEGUM Magnesium Aluminum Silicate and
VAN GEL Magnesium Aluminum Silicate
are natural smectite clays that have been water-washed to optimize
purity and performance. Smectite clay (also known as bentonite) is
valued for its ability to swell in water and to impart
useful rheological properties to aqueous compositions. VEEGUM and VAN
GEL clays have consistently been the formulator's choice to stabilize
suspensions, perfect emulsions and optimize flow properties
HOW THEY WORK
The value of VEEGUM and VAN GEL clays as stabilizing and rheological
agents is due to their colloidal structure in water. Each smectite
particle is composed of thousands of submicroscopic platelets stacked
in sandwich fashion with a layer of water between each. A single
platelet is one nanometer thick and up to several hundred nanometers
across. The faces of these platelets carry a negative charge, while
edges have a slightly positive charge. The net negative charge of the
platelet is mostly balanced by sodium ions. These charge-balancing ions
are associated with platelet faces and are termed "exchangeable" since
they are readily substituted by other cations.
Hydration - When clay and water are mixed, water penetrates between the
platelets, forcing them further apart. The cations begin to diffuse
away from platelet faces. Diffusion, the movement of cations from
between platelets out into the water, and osmosis, the movement of
water into the space between platelets , then promote delamination of
the platelets until they are completely separated.
RHEOLOGICAL PROPERTIES
Once the clay is hydrated (i.e., the platelets are separated) the
weakly positive platelet edges are attracted to the negatively charged
platelet faces. A three dimensional colloidal structure forms, commonly
called
the "house of cards". The formation of this colloidal structure
accounts for the characteristic rheology imparted by these clays.
Dispersions of VEEGUM and VAN GEL clays are thixotropic and
pseudoplastic, in addition
to contributing useful yield value.
This colloidal structure is particularly valued for its ability to trap
and segregate solids in suspensions, oils in emulsions, and gases in
foams or
mousses.
Yield Value
-
The colloidal structure also provides the smectite's most useful
property - yield value. This is a measure of the resistance of the
structure to breakdown. A certain minimum force, the yield value,
must be applied to start disrupting the structure. Solids, oils and
gases are trapped and segregated by the structure. They must exert a
force greater than the yield value to be able to move through the
liquid. This means that the greater the yield value, the more stable
the suspension, emulsion or foam. A unique and valuable feature of
VEEGUM and VAN GEL clays is their ability to impart yield value at low
viscosity. Stabilization of the
dispersed phase is possible even in thin, fluid systems where
flowability is
important. Most common organic thickeners [CMC Gum?] possess little or
no yield value and can stabilize suspensions, emulsions or foams only
at high viscosity.
The properties of individual smectite clays - e.g., viscosity,
hydration rate, electrolyte tolerance - vary according to their
particular structure, exchange cations and exchange capacity. Each of
these properties can be manipulated by the choice of smectite clay,
based on location and type, and by blending smectites from different
locations so as to obtain the desired balance of properties. For
example, VEEGUM K clay provides greater electrolyte tolerance while
VEEGUM clay provides greater viscosity and yield value. In addition, certain gums, such as xanthan gum and
CMC, act as synergists and protective colloids when used
together with VEEGUM and VAN GEL products. They can significantly
improve the compatibility of the clay with relatively high levels of
water solubles.
I suppose any old bentonite/smectite clay would have the
right sort of
properties, but the Vanderbilt Veegums are specially formulated, eg,
Veegum K "provides greater electrolyte tolerance" - presumably
especially good in a battery. But I don't have that, so it'll be the
basic stuff.
On the 12th I made an electrode using the
gums and the press. I wanted a 1/4 size test electrode to fit my
testing case, so I walled in a 1.5" x 3" space and made a press plate
that size.
Here is the latest and strangest technique for making an
electrode:
Ingredients: Ni(OH)2 6g, Monel 6g, Co2O3 0.3g, veegum 1g, CMC gum 1g,
agar 1g, LiCO3 0.22g, KClCrO3 0.6g, Sunlight dishsoap 1g, water 6g.
This made quite a dry mix, but as it's compacted it gets moister - a
wet mix before compaction would be oozing water everywhere during it.
I brushed enough Ca(OH)2 onto the electrode plate to loosely fill up to
the screen. (The voltage of the calcium oxidation is 1.5v, about right
to prevent oxygen gas generation if the battery/nickel is overcharged.)
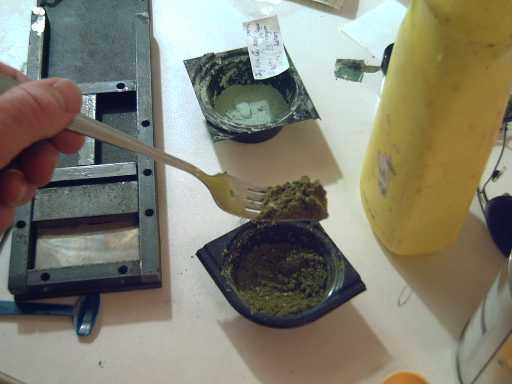
Nickel hydroxide electrode mix for Ni-Mn: surely a "green" battery
formula
I only put about 2/3 of the mix onto the plate in the press.
I did up
the bolts as tightly as possible, just the six near that end of the
press. The electrode compacted from 8 or 10 mm to a 3 mm thick
briquette. The things weren't very well mixed for all my efforts -
splotches of potassium chlorochromate were apparent here and there.
Evidently I need a "kneading machine" (being unwilling to stick my
hands in there, especially with the potassium chlorochromate). The
electrode was still fairly dry, except around the edges, where it
appeared saturated, and there
were actual drops of yellowish liquid under the plate.
Next I dripped ethanol (AKA Alberta "triple distilled"
vodka) onto it
and wetted the whole surface. Then I steamed it for a couple of minutes
in a pot on the stove. The wet heat activates the agar, and creates
acetaldehyde between the chlorochromate and the ethanol. The electrode
rose a bit, somewhat like a sponge. That's probably okay - the battery
book says positive nickel electrodes swell.
Then I dripped on HCl and wetted the whole surface with that. The acid
changes the acetaldehyde into an acetal ester monomer, which then
polymerizes (using dishsoap ingredients) to make a plasticy filling to
help glue the electrode together. ...Or so goes my rather tenuous
theory.
The electrode changed color back to turquoise. Under a 10x magnifying
glass it appeared to be well gelled. The impression is of a dense
sponge, which consistency is to be expected with the gums. One corner
curled up a bit and lifted away from the mesh, but most of it was
embedded.
The best proportions - or even good proportions - of
ingredients have yet to be worked out. A considerably less spongy
electrode (less gums, maybe less agar) would
probably conduct better, or else it needs more
monel.
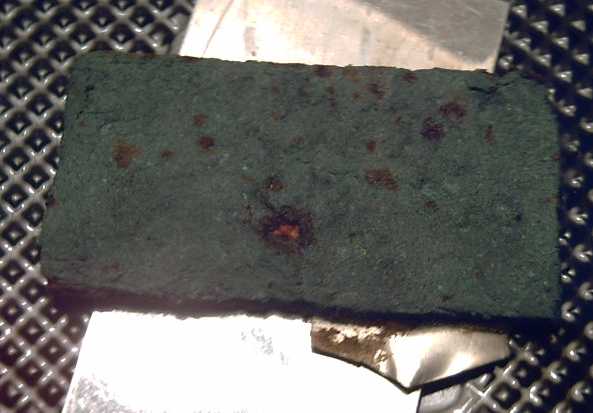
Steamed/gelled nickel electrode
Finally, I put the electrode in a tray with
some 3% NaClO
(bleach) to oxidize it to NiOOH, in hopes of starting with the battery
at least partly charged, which may help establish the chemistry.
Questions are whether it'll be beta or gamma, and whether it will work
at all without adding also NaOH. However, unlike with previous
electrodes, it looks like I'll be able to rinse the bleach out of this
one without washing away material.
(Well, the rinsing did wash away some material, though not
very much.) The color changed from turquoise to blackish (hmm, no
picture). That probably indicates success - and that evidently
NiO(OH) isn't the turquoise color of Ni(OH)2.
In the last electrode set I made, I noticed
that part of
the stainless steel mesh had corroded away. I thought steels were
impervious to alkali, but evidently the anodic action in KOH is too
corrosive even for stainless. It would seem I should buy nickel mesh
for (at least) the positive electrodes, which is unfortunately pricey
and much more so as it's not available in Victoria and will probably
have to be imported. Unless of course I can make the salt-based battery
as I hope to do, in which case the stainless mesh, and also the
nickel-silver, *might* not corrode.
Then I made the manganese electrode.
I used: 6g Mn powder, 3g MnO2, 0.1g Sb4O6, 0.9g KClCrO3, 1g veegum, 1g
CMC gum, (0.5g agar), 1.2g Sunlight, and 3g water. The 3g of water was
too much: the mix seemed only damp, but on compaction, yellow liquid
was oozing out and puddling on the table. I'll try half that next time.
After compacting the electrode, to about 2mm thickness, I realized I'd
forgotten the agar. Scraping the mix off the electrode screen
wasn't easy - it was well stuck down and came up in slices with a
knife. It also filled the mixing dish much lower than before.
I used 2/3 manganese metal powder and 1/3 MnO2, so in theory
it would
start out 2/3 charged up. This idea was dashed when I added the HCl:
not only would it turn the acetaldehyde into an acetal ester... of
course it would
turn the Mn powder into MnCl, releasing H2 gas! That is in fact the
exact procedure normally used to make MnCl. A white foam came out
of the electrode, that wasn't there on the positive one. Something will
have to be done differently next time!
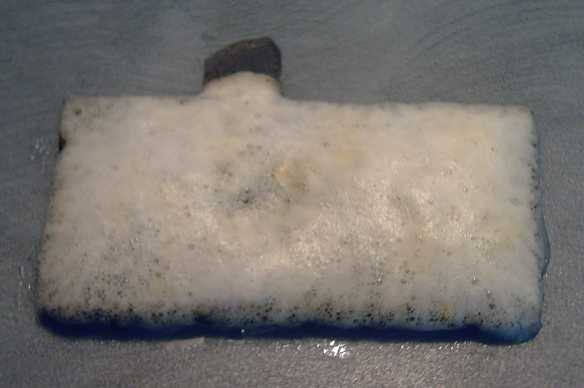
Accidental reaction!
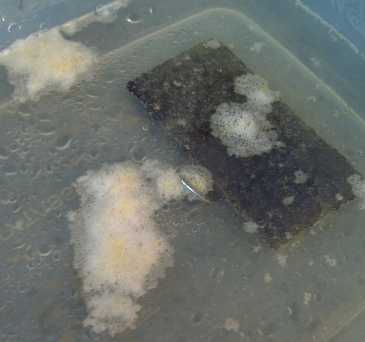
Rinsing it off - wonder what's floating away?
Now if I've charged the
positive electrode, as intended and as it
appears, and accidentally discharged the negative, the whole thing, in
theory, shouldn't work! If it doesn't, I'll use H2O2 to discharge the
positive and try again, having no way to recharge the negative.
I put both electrodes in water, which I repeatedly changed until the
yellow color from dissolving chlorochromate was much reduced.
The texture of the negative electrode is reminiscent of a piece of
rough sponge rubber,
although bits break off rather easily. The positive is more brittle and
it lost quite a few bits before
it made it into the battery. Charging the battery should solidify them
- I
think.
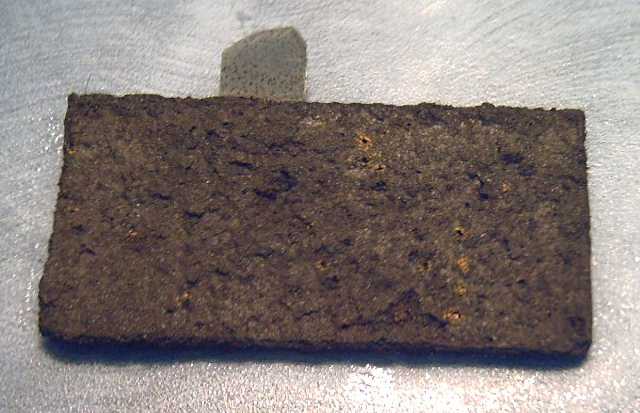
Mn electrode
The separator sheet was:
- a layer of Arches heavy watercolor paper nest to the manganese
electrode. The side facing the electrode was painted with zirconium
silicate (ion shield for the manganese), and the other side with ferric
oxide.
- The negative electrode with said paper was wrapped with two layers of
cellophane.
- The nickel electrode was faced with a piece of watercolor paper and
then another piece of cellophane.
Rather than immersion, it was put together as a dry cell.
It doesn't seem to want to charge, like all my other
batteries except the one Ni-Fe
one I made as an alkaline wet cell 'pocket battery'. I REALLY have to
figure out why this is happening, or in spite of all else, I'm not
making batteries!
Next I'll try some other ingredients in the electrolyte.
Copper chloride will be first.
Another thing to try is to make a gelled separator with
agar (& the gums?) to create a "salt bridge". Something I read
recently about agar says it's used for this purpose, and a salt bridge
is something I've wanted to try all along without knowing how to do
one. This leads us straight into the next section on membranes, written
earlier...
Creating Semipermeable Membranes
Now that I finally have working cellophane, I probably have a decent
microporous electrode separator sheet, in conjunction with the
watercolor paper, for alkaline batteries. But it will last longer if
the side next to the positive electrode is protected against oxidation.
Separator failure is the main cause of failure of small alkaline
batteries. (Hence the longevity and popularity of pocket electrode
batteries without separator sheets.)
Plus of course, I would really prefer to make batteries
with safer salt electrolyte rather than strongly acidic or alkaline
chemistry.
It's quite possible that since the discharge reaction
product of salt batteries at the negative electrode is a chloride, and
since most chlorides are soluble in water, to have a rechargeable salt
battery requires the separator sheet to be a semipermeable membrane
that won't allow the dissolved metal ions to pass across to the other
electrode. That, of course, would be on top of the zirconium ion shield
and gelling the electrode.
More on Manganese; Certain Rare Earths
The manganese metal powder (and more monel) arrived on the
9th. I'm getting quite excited about
using manganese - electrochemically it looks just about perfect for a
negative alkaline
electrode, and it's quite conductive. Barring some unexpected problem
(the dendrite
growths that have plagued zinc electrodes come to mind), it is surely
the best element
for the purpose on the whole periodic table! It's almost as good in
salt solution - the
reaction voltage is lower but still higher than most.
I sort of wonder how I missed it earlier. And why did no
one else spot it in the past? Well, the many reactions and valences of
manganese are sort of overwhelming. I've looked at it before and missed
seeing that the best one on the far right wouldn't do anything weird,
at least if the battery is positive limited - the usual case - and not
driven into reverse charge. (Even then, it's probably reversible.)
Mn(OH)2 + 2e- <==> Mn + 2OH- [-1.56 volts in
alkaline solution,
probably about -1.2 in salt] And, manganese oxides seem to be very
conductive as oxides go.
MnO2 (Mn valence IV) is the standard grocery store dry
cell and alkaline dry cell positive electrode material (discharging to
MnO(OH) - III), and a lower oxide (Mn(OH)2 - II) should be
substantially more conductive. Unless there is a hidden problem, it
should make for excellent cells with inherently high current capacity,
about 2 volts for Ni-Mn in either alkali or salt.
Tabulating the 'rare earth' elements discloses that praseodymium and
terbium could make good alkaline battery positive electrode chemicals.
In alkali, XxO2 dioxide (or XxO(OH)2, oxyhydroxide)
<==> Xx(OH)3, valence IV
to III:
La +? - No valence IV energy listed, but "lanthanum
oxyhydroxide" exists.
Ce -0.7 volts
Pr +0.8
Ne +2.5
Pm, Sm, Eu, Gd - no valence IV listed.
Tb +0.9
Dy +3.5
Ho, Er, Th, Yb, Lu - no valence IV listed.
Pr(OH)3 + OH- <==> PrO2 + 2H2O +
e- [+0.8V]
Tb(OH)3 + OH- <==> TbO2 + 2H2O +
e- [+0.9V]
Those are better voltage than NiO(OH)<==>Ni(OH)2
[+0.5 volts] and might be fairly good alternatives to it. On the other
hand, these are likely to be moderately pricey elements, the molecular
weights are higher, and the electrical conductivity remains to be
determined. If the conductivity is higher, that would be a good point
in their favor. I still haven't determined for sure that lanthanum
oxy-hydroxide (which has been mentioned on the web but isn't in the
regular tables) has a workable voltage as I suspect. Lanthanum is
considerably more common than praseodymium or terbium.
La(OH)3 + OH- <==> LaO2 + 2H2O +
e- [around +1.0V or a bit more in alkali and +1.5V in neutral
salt solution is my guess - and hope. That would make La-Mn cells
around 2.45 volts nominal. Pr-Mn: 2.25V, Tb-Mn: 2.35V.]
molecule weight
Ni(OH)2 (59+34) = 93; NiOOH = 92
La(OH)3 (139+51) = 190; LaO2 = 171
Pr(OH)3 (141+51) = 192; PrO2 = 173
Tb(OH)3 (159+ 51) = 210; TbO2 = 191
Owing to the molecules being about twice as heavy, hence
having half the amp-hours per kilogram, any of these will
have to have over twice the voltage of nickel to improve the energy
density. Or, they need to be denser by enough to shrink the size of the
electrode and hence the battery, which would reduce the weight of the
monel needed to get good conductivity and of the case and electrolyte.
Since Ni(OH)2 is very fluffy, it isn't impossible one or more of these
elements could be better overall. (Or, they need to charge to valence
five and move two electrons per molecule, eg, LaOO(OH), which idea I
have little confidence in as I've never seen it mentioned for any of
them.)
All October's new battery design work was in the early
part of
the month. Then the letter, lead-acid battery tests and the magnetic
torque converter took precedence.
Finally, here's what people who get funding get for
testing individual electrodes so they can see what's working out and
what
isn't:
The Lead-Acid Battery Renewal Project:
Progress Report
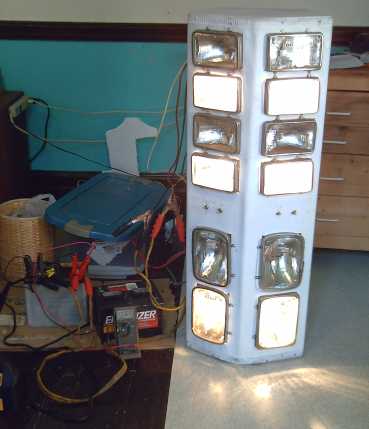
Project Overview
On August 31st I heard some people had been renewing
lead-acid batteries by replacing the electrolyte with alum (sodium
aluminum sulfate). A short web search revealed that it was also being
done by adding epsom salt (magnesium sulfate) to the existing
electrolyte. Since the batteries normally work with sulfuric acid
("hydrogen sulfate"), these related salts seemed to make some sort of
chemical sense and I decided to check it out.
First I should dispel a couple of fallacies: Some people
wrote that their scrapped battery seemed to perform "better than new"
after being restored. This appears unfounded - but "like new" is
probably attainable. It should also be noted that some were saying
that the
electrolyte was now "safe" because it was salt solution instead of
acid, but in fact whatever sulfate salt is put into the battery quickly
forms sulfuric acid and the pH drops to 1 (strong acid).
I determined that both alum and epsom salts would leave
solid precipitates - sludge - in the bottom of the battery, but that
Glauber's salt (sodium sulfate) wouldn't: it's the "correct" salt. I
also discovered that the pH of the electrolyte quickly goes to 1,
strong acid, regardless of what is used or added.
So after several weeks of playing around and
experimenting, I found the right salt, have the essence of the renewing
action figured out
(more
or less), have written practical instructions for treating or renewing
a battery,
and obtained some illustrative test results. These findings and renewal
instructions are below.
Sodium sulfate salt appears to solve the main problem of
lead-acid
batteries: gradual passivation of the electrode surfaces by
non-conductive lead sulfate build-up. It appears to dissolve this
corroded layer. Instead
of ever decreasing performance, lead-acid batteries should continue to
give "like new"
service for long periods.
Claims by enthusiasts of alum and epsom salt that restored
batteries seemed to perform "better than new" appear to be unfounded,
but I confidently expect that the life span of lead-acid
batteries will
be more than doubled with sodium sulfate salt - perhaps tripled or
quadrupled, allowing them to provide many years of "like new" service
in all
applications - and that they will suffer considerably less damage from
overdischarge, or from being left for a while in an uncharged
condition, than has been the case until now.
Now for me, the time has come to quit this detailed
experimenting
and
just use it. (I do have other things to do!) I'm putting some sodium
sulfate salt (as sodium hydroxide) in my car battery and in the three
big
"deep cycle" batteries I've been using to test the Electric Hubcap
motors, though they have been so far in good shape. (The car battery is
near new, the previous one having been recycled a few months ago.)
I've changed my car battery to the Panasonic in
"Experiment 1". The next test on it will be after I've used it there
for a couple of months, to see if there's been any "long term"
improvement with the salt in it in actual use. Then, similar "long
term" tests with the batteries for the electric motor once I have the
car running with it.
The battery cleaning/restoration reaction figured out(?)
The main killer of lead-acid batteries is buildup of
corrosion on the electrode plates.
It is commonly said that this is a build-up of lead
sulfate. I first conceived that it must build up to a thickness or
consistency where the
surface of the electrode is no longer in electronic contact with the
electrode's connections - the good layer is shielded from the
electrolyte by the bad. This "passivates" the "sulfated"
portion of the electrode. Passivated portions, can't
charge up to eliminate the corrosion and renew themselves any more, and
the useful portion of
the battery plates keeps shrinking.
But on considering the problem and the solution, it seems
likely to me that the main problem may be a build-up of lead oxides -
corrosion. The positive plate is supposed to have lead oxide, but the
negative plate is supposed to be metallic lead. When the corroded,
oxidized negative electrode is charged, it charges only from the oxide
to the sulfate ("sulfation") instead of from the sulfate to the metal,
while the positive plate has finished charging and the battery will
charge no further. The battery gradually becomes more and more out of
balance as the lead corrodes.
By solving this main problem, these batteries will last
far longer, and will perform well for most of their life
rather than continually deteriorating.
When the sodium hydroxide or sodium sulfate is put into
the cells, a couple
of visible things happen. First, they percolate - obviously the
immediate cleaning action - and
sometimes the gas (sulfur dioxide) may be seen coming out the hole.
Second, the electrolyte turns from clear liquid into dark brownish,
sludgy looking liquid. This color gradually clears, the lead sludge
probably
sinking to the bottom of the case. It appears to form clumps, so it
probably won't move once it's settled.
An invisible thing happens too: the specific gravity of
the electrolyte drops a little, eg from 1.250 to 1.225. Evidently the
battery is discharged some in the process. It seems to come back up
after recharging.
Here is my basic take on what's happening: The motive
cleaning factor is that the voltage of the PbO2 to PbSO4 reaction is
1.68 volts in acid, however, in neutral solution, it would be over the
2 volt limit
for aqueous solutions, and the lead dioxide will discharge
spontaneously to lead sulfate. Adding a salt puts neutral factors into
the solution and the oxide starts discharging. Even if oxide on the
positive plates is discharged, the overall effect of reduction of
oxides brings the battery back into balance so it can be fully charged
(and the pH lowers to 1).
But I don't have
it all figured out. The brownish color is probably
some form of lead oxide (there are several types) or lead sulfate, a
powder that has come off the plates, and the gas is part of the same
reaction. For example: PbSO4 (plate sulfation) ==> PbO2 (powder) +
SO2 (gas). I'm not
sure how the interactions would work to cause such a reaction. There
may well be lower oxides involved in oxidized plates: PbO, Pb2O3,
Pb11O15... or conceivably higher oxidized sulfations: PbOSO4, Pb(SO4)2
(which may or may not exist but if they do may well be insulators and
hence can't be electrically discharged). I'll leave it for some chemist
who may someday get paid to figure out exactly how and why it works.
The presence of the salt appears to have a lasting
residual beneficial cleaning action.
Further Experiments
In September I was under the illusion that the pH of the
electrolyte could possibly be raised, which might yield a higher
battery voltage. Owing to this, in most of the batteries I was putting
extra sodium in some cells trying to get the pH and voltage to rise.
This made for delay
and poor test conditions for simple battery renewal, and used up my
batteries, leaving them in unknown conditions for trying to record
improvements.
I wrote of one battery that at the end of the month was
taken from a non functional state with an internal bad connection
(presumably corroded) to a working condition. But it still had very
little energy available.
In October another experiment was performed on a newly
acquired battery with some performance figures noted, and I did
some practical renewal of batteries that were in actual use, some on
what would normally have been
their last legs. I had planned to do at least two well documented
battery renewal experiments, but the first one took up considerable
time and I didn't have the stomach for doing it again.
First experiment: A scrapped medium size (about 33
pounds wet)
"Panasonic" car starter battery was load tested, then treated, then
retested, then re-treated, then retested again over about 3 days.
Ongoing load tests continued for several more days to determine any
gradual
or residual changes. No performance specs
were printed on the battery. Discharge Rate in all
tests was very close to 10 amps (4 car headlights: Actual data: at
11.2V they drew 9.8A; 11.6V - 9.9A; 12.8V - 10.5A). Charging was
limited to 8 amps by a "smart charger" that reduced the current as the
battery came up and ended with a small continuing float charge. Load
tests were terminated when the voltage dropped to 11.00 volts. As the
voltage dropped it dropped progressively faster, and discharge to, eg,
10.5 volts would only have added another minute or two to the times -
even just seconds in the first two tests. I wrote down exact
time and voltage figures, but the main results are the interesting
thing.
Two discharges on the untreated battery gave the following
results:
Test 1: In 12 minutes and 30 seconds (12'30") the battery discharged to
11.00 volts
Test 2: It discharged in 12' 30" to 11.50 volts
For the greater part of both tests, the voltage stayed
near 12 volts,
then it started dropping rapidly. I accidentally stopped the 2nd test
1/2 volt higher than the others, but the voltage was dropping so fast
by
11.5 volts that it would been down to 11.0 in another minute or so.
These tests
indicate about 2 amp hours were available (above 11 volts) at this
discharge rate. The
battery recovered to over 12.5 volts both times, indicating it had only
used around half of its stored energy owing to poor operational
conductivity. (With a slower discharge rate, eg one headlight, it might
well
have given more amp hours overall.)
The treatment was 60 cc/cell of s.g. 1.30 sodium hydroxide
solution. This was squirted in the vent holes with a syringe, and mixed
by sucking and squirting the fluid with a hydrometer to circulate it.
Gas could be seen emitting for a short time, mostly
visible while the NaOH was being squirted in. The cells percolated
vigorously for a minute or two. The electrolyte turned a dark brown,
almost opaque. This gradually cleared up.
(I wore a face shield but only one rubber glove. I thought
I was keeping my other hand well away but later I noticed a finger was
sore and I found a small hole through my skin by a knuckle, doubtless
made by a small unnoticed stray drop of splattered acid or caustic
soda. Without the face shield it could have been my eye! A nice pair of
pants has three small holes in them from previous stray drops that I
didn't think could reach there. Here again, you're warned - these are
dangerous substances; don't take any foolish chances!)
Test 3: Discharged to 11.00 volts in 23 minutes.
Test 4: 11.00 volts in 24'40".
Battery sat overnight after charging; in AM (Oct 5th)
voltage was
12.69 --
Test 5: 11.00 volts in 23'23".
As before, the battery lingered around the 12 volt level
for some time, but when it started dropping, below about 11.75 volts,
it was more slowly than before so that the running time was about
doubled and figures of around 4 AH were attained instead of 2.
The recovery voltages after 5 - 15 minutes were lower
(around 12.2 - 12.3), indicating the battery was conducting better - it
had been better able to draw on its stored energy and had less
remaining.
There seemed to be no further increase in performance over
time or charge cycles.
After test 5 I added another 30 cc/cell of NaOH (Oct 6th)
to see
what effect that might have -- better or worse. There wasn't a lot of
bubbling, and there was much less brown in the electrolyte this time.
The first time it was almost opaque, this time just a somewhat
darkening color to the liquid.
This is no doubt partly because I only added 1/2 as much
NaOH, but the great amount of decrease suggests that there was much
less lead sulfate remaining on the plates to react with.
Test 6: Dropped to 11.00 Volts in 24'25".
Test 7: 25 minutes even to 11.00.
Test 8: 26'30" to 11.00v.
Test 9: 27'13".
- sat on float charge 36 hours -
Test 10: 29'05".
Evidently adding more salt had no immediate notable
effect. But the energy storage after treatment appears to be very
gradually increasing with time and-or cycling, a 26% increase by the
last test.
The voltage drop at one minute into the load tests
increased in
tests 3 to 10, the voltage being, eg, 12.03 volts in the first couple
of
tests to about 11.8 volts by the last ones. Recovery
voltage in 5 minutes after turning off the lights progressively
decreased from tests 3 to 9: 12.26, 12.22, 12.20, 12.17, 12.14,
12.14 and 12.10
volts. One might attribute these results to gradual deterioration, but
that is belied by the gradual increase in running time.
And this was a car starting battery, not a "deep cycle"
battery. This type is well known to hate being very much discharged and
cycled, an operation these tests repeated ten times.
3.8 AH (rising to 4.85 AH by test 10) doesn't seem like
much
energy. Of
course, when one takes batteries off a recycling pile at "Battery
Doctor", who themselves reconstitute whatever batteries aren't too far
gone for resale, one must expect very questionable batteries. (Two of
five I got had leaks!) Questions
for further study:
1. Was 60cc/cell already more sodium hydroxide than was needed for
restoring this battery?
2. Will the "excess" sodium sulfate remain in solution and cause the
battery to remain healthy for an extended period of time?
3. Is it useful to add salt to a new battery?
Perhaps questions 2 and 3 are already tentatively answered
by the gradual increase in performance after treatment. There must be
some optimum amount to add, though.
I added another 20cc/cell and did more cycle tests. It hit
the 1/2 hour mark. I put it in my car. In a month or two I'll bring it
back in and see what change there may be in its performance, better or
worse.
(I must note that in experiment 5 there was a
similar initial doubling of capacity in the third and fourth tests without
adding any salt.)
Second Experiment: The next battery that looked like a good test
candidate was a Megatron Deep Cycle battery about 7w x 10L x 8t nches,
45 pounds wet. (This was from a different store's scrap bin.)
To my surprise it was 12.6 volts before I even did
anything. After charging and then sitting all night, it was still 12.98
volts in the morning. Why then was it in the scrap bin? Answer: reduced
capacity.
Test 1 (Oct 10, untreated): Dropped to 11 volts in about 57 minutes.
(9.5 AH)
The exact time to 11.00 volts wasn't recorded: at 55' the
voltage was
11.46 and dropping increasingly quickly, but I answered the phone and
unexpectedly it was way
down to 8.5 volts when next read at 60'. Like the Experiment 1
untreated
battery it died rapidly once it went under around 11.5 volts.
The treatment was 25 grams of anhydrous sodium
sulfate powder poured into the hole of each cell. When I did this, to
my chagrin I discovered that the fluid level was way down in all cells
and it took over 2 liters of water (400cc/cell) to refill it. The level
was probably well below the tops of the plates (the plates can't be
seen in this battery.) Unfortunately, this makes the results of the
"before" test (test 1)
pretty much irrelevant, and the salt was now in the battery.
After the salt treatment and refilling, the S.G. was only
around 1.075 - very diluted. (Normal for a charged battery is 1.25.)
After charging it went up to 1.16 or so. The next morning it was 1.175
and I did a load test. It stayed near 1.175 even when the battery was
discharged.
Test 2: dropped to 11.00 volts in 83'45'. (14.0 AH)
Better, but not very good. I tried it a couple more times
with similar results, and then added another 10g salt.
Third Experiment: A friend brought a car battery that wasn't
starting his car (not until the very day it wouldn't start), another 33
pound Panasonic battery. I charged it a little while and did
a load test at 10 amps. The
battery ran above 12 volts for almost 5 minutes, then nose-dived to
11.00 volts, where I shut it off after exactly 5 minutes. It almost
immediately recovered to 12-1/2 volts. 15 grams per cell of anhydrous
sodium sulfate were added to the electrolyte, which only clouded a
bit and bubbled a bit.
I was expecting dark brown and considerable percolation.
Seems it's only when you add sodium hydroxide that that happens, and it
probably indicates that adding sodium hydroxide straight to the
battery is a bad idea.
I recharged the battery at 8 amps until it seemed pretty
much charged. This also gave the salt some time to act. Then I ran a
second load test. The battery dropped more slowly and didn't "plummet"
until below about 11.4 volts, and ran a total of about 17 minutes to 11
volts.
Probably it will continue to improve for a while with use.
I charged it again for 15 minutes at 15 amps until my
friend (who had phoned just as the second load test ended) came and
took it back to use on his car. I only had it a couple of hours. I
asked him for a report in a week, but he brought it back the next day
saying it was barely starting the car and he'd bought a new one. It
didn't get much chance. I wished I'd been able to charge it more and
cycle it a couple of times.
I didn't have time to look at it again for a while, but on
the 30th I charged it quite a long time and then did a load test. This
time it lasted over 24 minutes, again spending most of that time above
11.5 volts and only a couple of minutes once below 11.25, and it
recovered to 12.33 volts in 5 minutes. On the 31st I ran it again and
it went 29 minutes.
Fourth Experiment: Trojan T-105s. Somebody gave me two of these
huge 6 volt batteries and I hurt my weak back carrying them into the
house. The SG of the cells was very low - one or two seemed to be just
water. I charged them for a couple of days, and they were still drawing
several amps of current. The SG went up to 1.10 to 1.125.
As they were so large, I decided to run tests at 25 amps
load instead of 10. The voltage dropped below 11 volts in 45 seconds,
but as it dropped the rate of decrease slowed, so I ran them down to
10.5 volts. As the rate of decrease was still slowing, it was evident
that they still held considerable charge, but I ended the tests there.
In the "before" test, they ran 4'30".
Then I added just 15cc/cell of Na2SO4. That seems like not
much for such giant cells, but I think I may be adding too much, so
this is an attempt to see how little is effective. The electrolyte was
almost clear.
The second test, they lasted for 6'. Better but not much.
But if they continue to improve, perhaps it's enough that they will
gradually restore? More tests!
The third test they only went 5'.
I dropped the load to 10 amps and they behaved better, but
they seem to have lower voltages than most batteries. Running them down
to 10.00 volts gives them up to about 2 hours time, or 15 - 20
amp-hours. But they don't seem to be improving much over time, and they
glurp and spit out or drool acid that collects on top while they're
charging, even with a very low charge rate. I think I'll toss them. The
voltages test even between the two, so it's not just one bad cell in
one battery.
Fifth Experiment: this is a third Panasonic, which had been
sitting unused for some time. This time I did several "before" tests
and it showed considerable improvement just from being cycled.
Initially, it didn't stay up to expected voltage, dropping to 12.2V
overnight.
"Before" tests (time until voltage dropped to 11.00 volts, in whole
minutes): 18, 16, 28, 29, 35, 37, 33.
After these cycles, it held at 12.9 volts overnight.
Evidently, cycling of a battery that's been sitting does considerable
good even without the salt.
Then 50cc of sodium sulfate solution, SG 1.25, equivalent to about 12.5
grams of anhydrous salt, was added to each cell. Tests afterwards ran
26 and 29 minutes. Here time ran out - I'll try a few more runs in
November.
This experiment wasn't a very positive report for the salt for
immediate improvement, and it suggests that some other results may have
been positively affected by cycling as well as or instead of by the
salt. I still expect it should work well for long term maintenance of
condition, instead of the usual gradual deterioration. I'll be putting
it in my healthy batteries and monitoring them over the long term...
and I'm still using the previously discarded battery from experiment
one in my car - almost 3 weeks now.
Simplified
Lead-Acid Battery Cleaning/Renewing Instructions
Using the salt is safer than using sodium hydroxide. I said "15 grams"
below, but I'm still not sure what might be an optimum amount to put
in. I've tried 15 to 50 grams, and beyond, but somewhere beyond is
worse. If 15 grams doesn't seem sufficient, try 30.
1. Buy: face shield (at least eyewear), rubber gloves (grocery), a
funnel, and at least 100 grams of anhydrous sodium sulfate salt
(compounding pharmacy), preferably more, eg, 500. (You might also find
it at a pottery supply, but it may be impure and-or it may be hydrated,
in which case double the weight or four times the volume (2.27 (over
double the molecular weight) x 2.66/1.46 (density, g/cc) = ) is
required.)
2. Don the eyewear and gloves. This is important - the acid is very
corrosive, and you don't want holes in your pants, nasty little red
sores on your fingers, or much worse to be severely burned or blinded.
(I met a virtually blind chemistry professor recently. Familiarity may
breed contempt, but it doesn't lessen the danger.) Old clothes you
don't care about are an asset.
3. Remove the covers to open the 6 holes in the top of the battery. Set
them on the battery, on cardboard or in a plastic container. Be careful
not to splatter anything on yourself. The acid will make holes in your
pants and-or in your skin. I've taken to putting a piece of cardboard
(or a cardboard box) between me and the battery, so only my gloves, old
sweater and face shield are subject to little flying droplets. (I've
ruined two pairs of pants so far and have had three small painful sores
on fingers.)
4. Check the fluid levels in the battery. If any appear low (eg, tops
of plates exposed), add pure water (use the funnel?) to top them up.
(If you used the funnel, you then need to dry it.)
LEAVE THE COVERS OFF THE CELLS AFTER PUTTING THE SALT IN.
5. Using a measuring device (scale, measuring spoons), for a medium car
battery (25 - 35 pounds) measure out somewhere around 15 grams, 15 cc
or one tablespoon of sodium sulfate. (That's for the anhydrous salt.
Use 30 grams,
4 tablespoons for the decahydrate.) Using the funnel, pour it into the
first cell. Repeat 5 more times. Don't lose track of which cells you've
done. I feel the salt will all dissolve sooner or later so there's no
need to mix or stir it in, which has the additional risk of possibly
splashing acid.
6. The cells may "percolate", bubble, weakly or strongly for quite
some time, even hours. If the covers are replaced while there is too
much percolation, they might pop off, splurting acid all around. This
would be hazardous. Some types of covers are screw-on, which is safer,
but others simply pop on - and off.
7. Carefully rinse off the gloves, covers, and any equipment or surface
that may have got acid on it. When it seems the percolation has died
down, or if there isn't much or any, put
on the gloves and eyewear and replace the covers.
8. Use the battery.
Revised
Lead-Acid Battery Cleaning/Renewing Instructions
also see "simplified instructions" immediately above.
1. Get a battery hydrometer (auto supply, eg Canadian Tire), rubber
gloves
(Grocery) a face shield (Builders Supply) or at least eye
protection goggles, and some sodium hydroxide (NaOH, caustic soda
- Borden Mercantile gardening etc. supply (in Victoria) or a soap
making supply). (I
presume
you have a lead-acid
battery.)
2. There are two alternatives: use sodium sulfate salt directly (drug
store or compounding pharmacy) or make it using sodium hydroxide. I'll
describe using the hydroxide here for now because it's what I've mostly
been doing. The salt is safer to handle -- it's been used as a
laxative. But it will only go to around 1.125 density when dissolved
unless it's heated up to about 35ºC, at which temperature it's
much more soluble.
3. Put on the face shield (or at least eyewear) and
rubber gloves. Fill a jar with pure water, not to the brim, and put it
in a sink. With a small scoop, slowly add sodium hydroxide powder while
stirring. It takes minutes not seconds to dissolve,
and during that time it gives off heat. If you add too much too fast, a
plastic jar may melt or a glass one shatter, or perhaps the water may
boil. The powder and solution (it's also called "caustic soda") is corrosive
to skin and will BLIND eyes. When the water clarifies and isn't
too hot, you can
add more powder. Check with the hydrometer and stop when the specific
gravity is about 1.25 or so. I tend to add half, go have a coffee or
something, then come back and add the other half.
3. Put the lid tightly on the jar and rinse everything: sink, jar,
scoop, gloves, counter. Put away the caustic soda powder.
4. Now to the battery: In addition to face shield and gloves, shield
bare skin. Old
clothes or coveralls are an asset. Place the battery outdoors or in a
sink (bathtub?) where a spill won't do
much to anything. (Remember the acid will etch and eat stainless steel
if it doesn't get rinsed off.)
5. Siphon acid out of the battery down to the plates with the
hydrometer, into a jar. Put the lid on the jar. (What to do with the
acid??)
6. Add some sodium hydroxide, an equal amount to each cell. I'm
guessing 80cc per cell for a small car battery - maybe a couple of
hydrometer
fills worth. Keep the liquid level fairly low, not far above the tops
of
the plates. Leave the top covers off the cells!!! (Otherwise,
it might explode, spewing acid!) There will be a strong bubbling,
percolating action, bubbling off sulfur
dioxide gas. This seems to be the cleansing and renewal of the battery.
7. Charge the the battery, preferably still outdoors. It may bubble
furiously the first
2 or 3 charges and the covers may still 'explode' off if they're pushed
on -
that's dangerous.
8. Do some charges, and discharges down to about 11(?) volts to
recondition it. I use a halogen car headlight or two or four for a load
- they
draw about 3 amps each... and if placed strategically the light will
remind you not to accidentally leave the battery running until it's
dead again.
At some point the bubbling will be reduced to the point
where it is
safe to replace the battery covers. It seems no matter how much salt or
alkali is added, after the bubbling the battery pH is 1: strong acid.
Thus, there's probably a limit to how much sodium sulfate is useful or
desirable. Another question is: Does it just act once, or is there an
ongoing anti-corrosion or other beneficial (or otherwise) effect?
BTW: If you notice a white powder around the battery holes: if it's
long
thin "needle" crystals, it's sodium sulfate salt (Na2SO4) formed by the
acid (H2SO4) and the hydroxide (NaOH). (The other product of this
reaction is H2O) If it's simply
powdery it might be NaOH, nasty hydroxide, AKA "caustic soda". (If
there's liquid it might be anything.)
Whatever... put the covers on the holes after it stops bubbling and
hose down the battery.
http://www.turquoiseenergy.com
Victoria BC