As in the later half of December and in January, there
were a lot of things requiring my attention in February and diverting
it from the torque converter project, so I didn't get very far.
That's
not to say nowhere, but it was frustrating that mainly this one vital
laggard item seemed to be preventing driving the car down the street
electrically.
One thing diverting my attention required some weekend
trips to
Comox, and I stopped in on my way up one day at Canadian Electric
Vehicles in Errington. I got a great tour of
their
shops and drove a fabulous car converted to electricity. Quiet. Simple:
Fwd-N-Rev. The gas pedal started the car braking somewhat when you let
it up, just the way I'd envisioned as ideal (regenerative braking).
I noticed on the little analog(!) meter that 300 amps
would be used while accelerating, while only 50 or
even 20 or 10 amps would be returned when braking. To a considerable
extent, this disparity would be due to losses in the transmission (the
car was permanently set in second gear), which is of course a major
reason the Electric
Hubcap drive system deals with the car wheel(s) directly. A direct
drive system should reduce that 300 amps to 200, with all the savings
in motor size and battery requirements that that would imply.
Not
only did this side trip give me some small but real experience with the
way electrifying cars is done now instead of just theoretical
knowledge, I also found they had some 36 volt electric heater cores
that looked
just about ideal for my pivoting dashboard heater plan. Perhaps just
as well I hadn't got around to doing up that car heater yet - this
looked pretty simple to put together, with the same fan and switches.
And in fact I did get it assembled (plans are below), using my next
big score: a sheet metal break for $39.99.
On the next Comox weekend, on the 28th I stopped on my way
back at
Transfer Beach Park in Ladysmith, a lovely civic park on the ocean.
After walking a beach trail, I
stopped on my way out to examine a huge old "museum" steam engine to
see if
anything on it might give me any ideas for the torque converter. It
did! I now have a design with two main components that looks so
promising I hope to make and try part of it in March, including
actually driving the car down the street. This design is so simple, so
obviously efficient... and it would seem to be essentially the same as
part of Constantinesco's successful design, the recreation of a piece
in the photo I hadn't realized the workings of. My design could be
closer to Constantinesco's than I expected.
Adopting it would mean radically changing the entire
layout philosphy of the drive system. The Electric Hubcap motor
probably wouldn't even be mounted on the wheel - a change with serious
consequences to its very name. But if one wants to invent "world's
best" successfully, one must be willing to step back, recognize a
superior idea as better and valuable even though it conflicts with
cherished designs which have been established with much effort and
which have become part of the basic "assumptions" of what the project
is all about, scrap the work and redo it the better way.
Also near the end of the month, I finally decided that if
I wasn't
having much luck with my perchlorate battery chemistry, I should at
least now have sufficient processes and techniques worked out to make
very good alkaline batteries, and a nickel-manganese one should at
least hold about 65-75% more energy than Ni-MH, a good step up. Other
than the nickel, it should be cheap.
Only nickel metal
(or 100% nickel plated metal) works in the positive electrode - every
other metal soon corrodes away in the alkaline 'positrode' when
charging the
battery. But on trying to source even a few bits of pure nickel
(nickels are not pure nickel), it appears
I may pay more per kilogram for nickel than I did for lanthanum a
couple of years ago, and that I may well have to buy "production"
quantities to get any at all. It seems making one alkaline battery is
likely
to become a costly endeavor.
The Electric HubcapTM Vehicle Drive System
February Details
Revising the re-revised heater plan
I found a small (~5 x 5 x 1 inches), rectangular, 36-72V
electric heater core consisting of four finned
resistors, at Canadian Electric Vehicles in area 51 (take exit 51 near
Parksville).
They're also available for higher voltages. Prices (IIRC) were from 80
to 125 $. I think this one, the lowest voltage unit, was really made
for 1500 watts at 48 volts. At 36 volts it's 800 watts - four 200 watt
elements. They're wired in series but with access to the midpoints,
hence five connection terminals (seen on left side in picture). They're
made by DBK and bear the numbers
DBK HRKK01-16/14 36-72V L49V. I think they're 'special order' as the
voltages on the DBK web site are all 110/240. It seemed pretty much
ideal for the car heater I wanted to make, so, having not yet made the
heater, I bought it. It was much pricier than the $7.99 'off the shelf'
heater from XS Cargo and less than its 1200 watts, but still half the
cost of the finished 430 watt golf cart
heaters and with substantially more heating power. I suspect if one
ordered a bunch,
they'd make them however one desired, eg, 1500W at 36 volts.
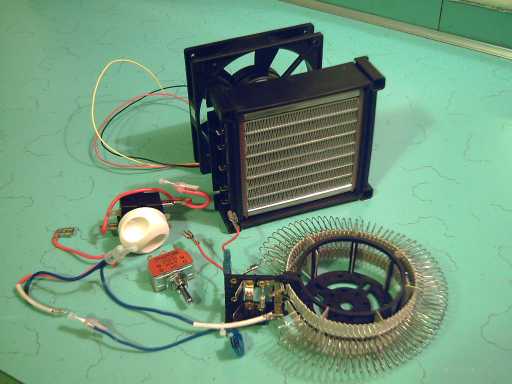
The components for the heater, with the old 120 volt coils at the
front.
All I'll take from that now is the heat safety switch and the
rotary switch (left) for Off-Low-Med-Hi: 0 200, 400, 800 watts. 100 and
600 watts would be possible but would need complex switching.
The Cheap Sheet Metal Break
Having all the parts, it needed a chassis. Aluminum
chassies may seem a little passé these days, but they won't
catch fire if there's a problem with the heater. And - not a trivial
detail for one-offs - you don't need an injection mold. I now knew just
what I
wanted to make, and I had the aluminum.
I had been casting about for an
economical sheet metal "break" (bender/folder) for years but had seen
nothing
under $200, and nothing recently under about $250. Those were just 12"
wide
units, but I figured that was wide enough for small chassies. Until
now, the
chief intent was for making motor controller chassies. I managed to put
together the last one without one, but it would certainly have
simplified things. Now this second and immediate usage spurred my
thoughts about them again.
I kept thinking it should be possible to make a cheap
break simply by welding some end plates onto lengths of angle iron and
putting pins in for a hinge. Then you could just clamp a loose flat
piece of metal on top to hold the piece being bent.
But starting yet another project wasn't exactly an
appealing idea! I thought I'd give buying one one more try. Was there
anywhere else but KMS Tools? Midland Tools in Nanaimo was in the
Victoria phone book, so I called. Wow!, they said they had 30 inch
breaks, for $90. "Very basic. Not a chassis or box bender." Okay, I'd
check them out on Friday. In the meantime, let's look one more time at
KMS and see if there's anything new. I drove out there and quickly
spotted an "18 inch benchtop sheet
metal break"... for $39.99! Wow! I bought it of course.
On closer examination, this break was made by welding some
end plates onto lengths of angle iron and putting pins in for a hinge.
There was a loose flat piece - you just clamp it on top to hold the
piece
being bent, with C-clamps. In short, it was exactly what I'd thought of
myself!, with a better mounting and very nicely made. I
suspect the 30", $90 one at Midland Tools is probably a bigger version
of the
same thing.
Heater Chassis Making - With Plans
I measured all the parts and put the chassis dimensions on
paper. I cut the aluminum sheets with a crosscut blade on the
radial arm saw (safety goggles, earmuffs), and trimmed the bits with
tinsnips. (Then I marked the dimensions on the actual pieces and
foto'ed them - too simple!) I decided to make the top and two sides
from one piece, and the
the
length turned out to be 17-1/2". How thoughtful of KMS to bring in
exactly the right size break!
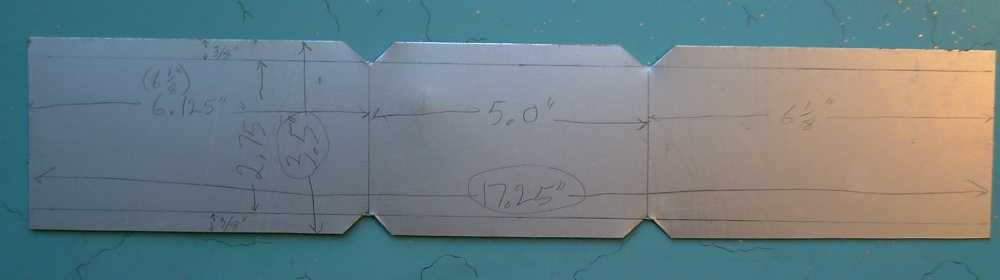
Heater chassis top (and sides) piece, #18 gauge aluminum, showing
dimensions and cutouts.

Heater chassis bottom piece, #12 gauge, showing dimensions and
cut-outs. I should have made it about 3/16" narrower so it would fit
inside the top piece, so change the main face from 2.75" wide to about
2.5625" (2-9/16") and the cut width from 5.25" to 5.0625" (5-1/16").
So! The
$250 12 inch break wouldn't have been able to do it. (This one was just
strong enough - pulling both handles, it was flexing a bit in the
middle on the 17" bends,
but it did the job. Well, it did say in the instructions something like
"Hey, this is a cheap little break made from angle iron, please don't
come crying to us when you wreck it on some heavy slab of steel it's
way too light for." I'm not sure those were the exact words...)
I sanded the cut edges on the stationary belt sander
(otherwise use a file), straightened them up a bit with pliers, and in
a fit of decorativeness, polished the top on the polishing wheel. (But
I suppose I should paint it all black now so it doesn't make glare at
the dashboard reflecting sunlight - and all those awful glaring
headlights that seem to have unfortunately become ubiquitous.)
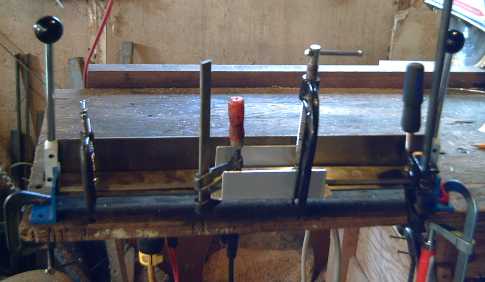
Bending the bottom.
The top piece of metal C-clamped down tended to
slide out with the pressure. The answer: more C-clamps, tighter!
I also used my space saving technique of C-clamping the entire tool to
the workbench when I need it rather than bolting it down.
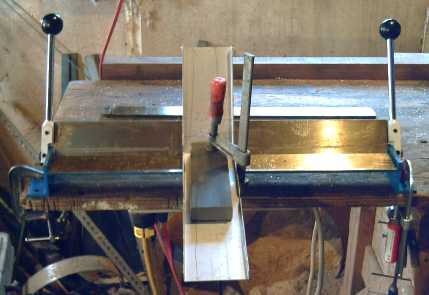
The bender proved much more flexible for doing boxes than expected.
Where 'regular' benders have movable teeth that are a pain to set up to
allow compound folds, with this one you can just use any old short top
clamp piece instead of the full length one. Cool!
Do the long folds first, and the short ones after, as per these
pictures.
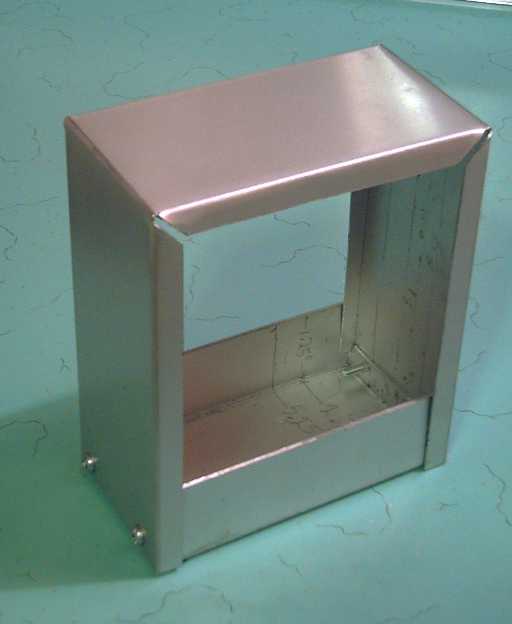
The chassis. The bottom could be made a little narrower so it would
fit
inside the top piece edges on both sides. might look better. As
it was, I had to do a small bit of hacking and have one side inside and
one outside.
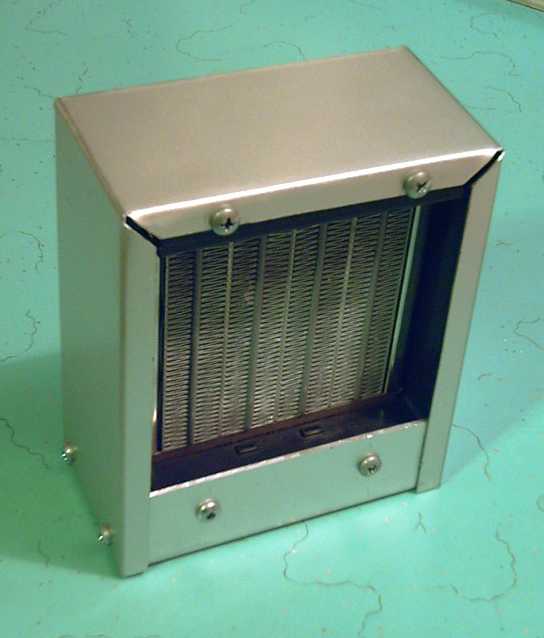
The heater from the heater element side.
The mounting lips had slots for bolts, but that would have meant trying
to do them up from the inside.
I drilled smaller holes in the lips to thread sheet metal screws into.
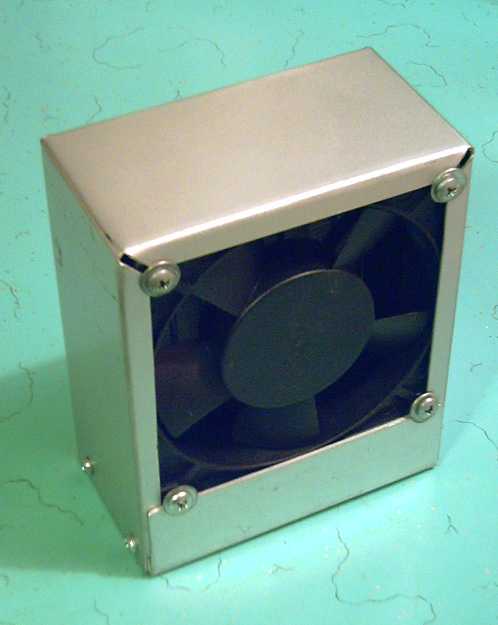
The heater from the fan side. Now it just needs grills.
Oh yes... and
wiring, switches and safetys, resistors and zenor diode for the 12 volt
fan, and the pivoting mounting. The 'extra' space below the fan and
heater element provides room for these items.
I threaded sheet metal screws into the holes in the corners, but they
proved to be inside the edge folds of the chassis. Washers made the
connection. When the grill is on, it'll be fine.
I spent the whole of the 22nd on this while putting off
many things that needed (and need) doing, from getting the break in the
morning to finally attaching the fan and heater in the evening. Then of
course considerably more time on the 23rd writing this up. Then on
March 1st I found some nice grill for it. So here it is, finished --
except for wiring it so it actually works, the telescoping conduit
pivoting mounting to aim it any direction, and painting the beautiful
polished aluminum some dreary dark color so it won't glint sunlight in
my eyes or reflect in the windshield at night.
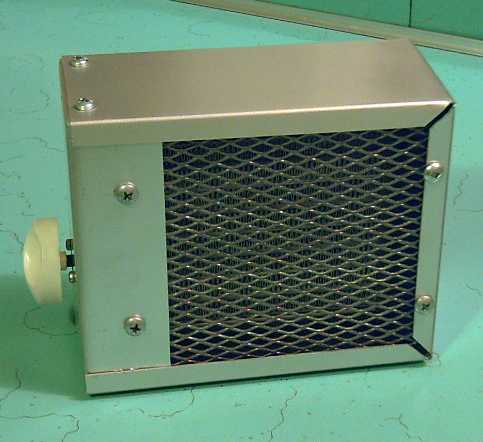
The assembled heater. The switch side (left) is the bottom.
A Broadening Marketplace
A new web search reveals several more 36 volt heater
choices on the web than last year when I only found one, and the prices
have come down somewhat. In essence, they seem much like this one.
Well,
I've bought the parts and I'm 2/3 done! Perhaps it will prove to have
some advantages. (If I'd used
the circular heat element from the $7.99 heater instead of splurging
on the nice rectangular one, I could at least say it was cheap!)
The only thing I can say is it'll have 'low-med-high'
(200-400-800 watts) with that four position rotary switch, where the
commercial models
I saw all just have 'low-high'. So nyah, nyah, nyah!
But looking in the parts box, I seem to have practically
enough left over to make another complete heater for no additional
money! Maybe if 800 watts
doesn't seem like enough I'll do the 1200.
I'm not going to try doing a car electric air conditioner.
If I was in Texas I might, but in Victoria there's just a few days a
year it might be 'kind of nice' instead of just 'in the way'.
Mechanical Torque
Converter Project:
Torque Leverage Without Gears
February Details
Regrettably (or perhaps not), I didn't find a lot of time
to work on this
in February. That's not to say none at all...
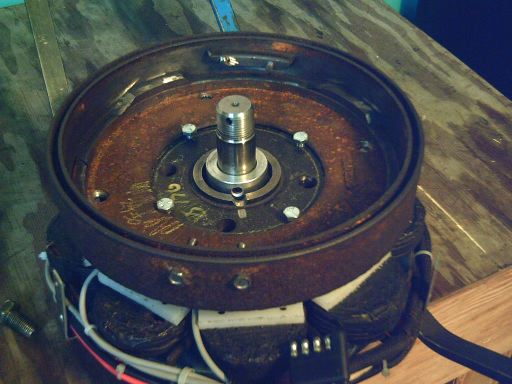
I thought, gee, if I just tie the rotor to the hub strategically with
some bolts, I could use the original drum despite the center and
mounting holes being cut out.
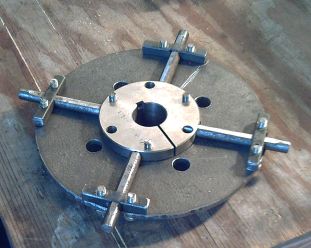
The "SDS" compression fitting I ordered in January arrived and
(uncompressed) it's a great fit - slides freely on the axle but has
very little
play. I drilled holes and put the inner ends of the pins right into it.
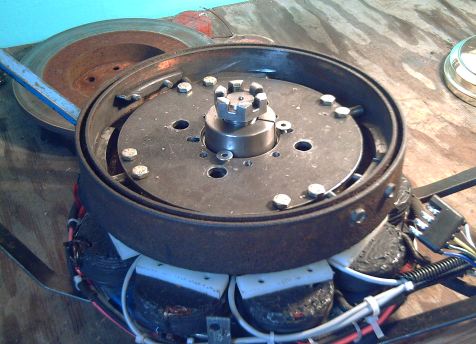
Assembled. The bottom of the rotor needs magnets glued on, but I can't
seem to get to that little job (and won't in the next few days,
either). The nut is about where it has to sit. I'll have to put it on
upside down to get the cotter pin through. (I suppose I could
grind the top of the SDS fitting down - ugh.)
A New Magnetic Torque Converter Idea
Did I have it *almost* right on the very first try last
spring?
A new idea has come to me for making a magnetic torque
converter. The very first attempt I made was something like an axial
flux induction motor, except that the rotating magnetic field was
generated by actual rotating supermagnets instead of by electricity
with electromagnets.
The rotor being turned was a flat aluminum plate with slots.
This arrangement had the advantage that the magnets were
going by aluminum rather than steel or other magnets. Since aluminum
isn't attracted to magnets, the output rotor wouldn't "cog"
magnetically and hinder the motor from starting to turn, but owing to
the induced field, it does try to follow along with the magnets.
I thought that in that system was a rotor with enough
field strength to turn the car wheel. But I didn't realize that the
output torque is never greater than the input torque, and that the slip
is only loss and heat rather than a torque increase varying with the
difference in speeds.
That meant that the better the coupling was, the more the
wheel would slow the motor down, but the car wouldn't move any better
than by directly connecting the motor to the wheel. It was a "torque
resistor" rather than a "torque transformer".
But, if there were, eg, four turning magnets, and the
aluminum was only present at four spots on the output rotor, all the
torque would be generated in four pulses per rotation as the magnets
lined up with the aluminum. The rest of the time, the motor would be
free spinning.
The motor would recover its speed between pulses, and the
higher speed would create more torque at the pulse points than a
continual drag on the motor, which would keep it from going very fast.
A major consideration for this design is whether it's
practical to get enough coupling from such an arrangement without
covering too much of the circumference with too many pulse points. You
could put in interleaved layers of magnets and aluminum. With enough of
them it would
be bound to work... but how many would it take? One would be nice...
six probably makes it "not a home project".
But, as long as the wheel is turning much slower than the
motor, this design would doubtless have some losses. I'm still sure
there must be some great way to do a magnetic torque converter with
virtually 100% efficiency, no friction and no heat, but this wouldn't
really be it. Enter the next
idea...
A New Mechanical Drive/Torque Converter Idea
On the last day of the month, looking at an old steam
engine, the pin driven by the steam piston made me think of having such
an off-center pin on the motor. That could make an arm go back and
forth, and some sort of ratchet mechanism on the car wheel could make
that back into rotary motion at a different speed than the motor speed.
With this conception, I understood a strange looking piece of
Constantinesco's converter, which design I confess I hadn't paid much
attention to (arrogantly thinking mine must be better).
Why, when one is starting with rotary motion, would one
want to convert that to linear back and forth "piston" motion and then
back to rotary motion with ratchets? Why not use a pair of gears? It
seems totally unintuitive.
Answer: the linear motion derived from a given RPM can be converted to
a lower RPM output - a wide and potentially variable range of "gear"
ratios can be derived,
without gears and very efficiently.
With no facility to make more complex special machine
parts, there was one potentially big hitch -- what sort of a
ratchet mechanism could I use? Surely a bicycle rear wheel piece was
too light for a car. In Lordco the next day I found a possible answer:
a heavy duty ratcheting box wrench for one inch nuts, $40. It's just a
prototype, but it could work.
I'd have been happier
with, eg, a two inch central diameter - or 3 or 6 - but this was the
largest size ratchet wrench in the store. I know
those things are pretty darn tough so they won't slip or bust when
you're
reefing on a nut - but it remains to be seen whether it's
tough enough to move a car along the roads, and how long it will last
in such an application. (I wonder what the maximum
RPM rating of the ratchet is?)
This ratchet has 72 'click' points, so the maximum speed
reduction possible is 72:1, ie, 72 turns of the motor
will turn the wheel around once - less rocking motion from the motor
wouldn't click the ratchet to its next position. Thus it would be
"neutral". But at 72:1 reduction the car should climb a
really
steep hill! Later I sketched out a
design using it - or better two of them. One will
suffice for an initial test - the car should move. Two will even out
the torque better. I think that's what Constantinesco's odd
looking piece essentially was: two ratchet arms on a hub.
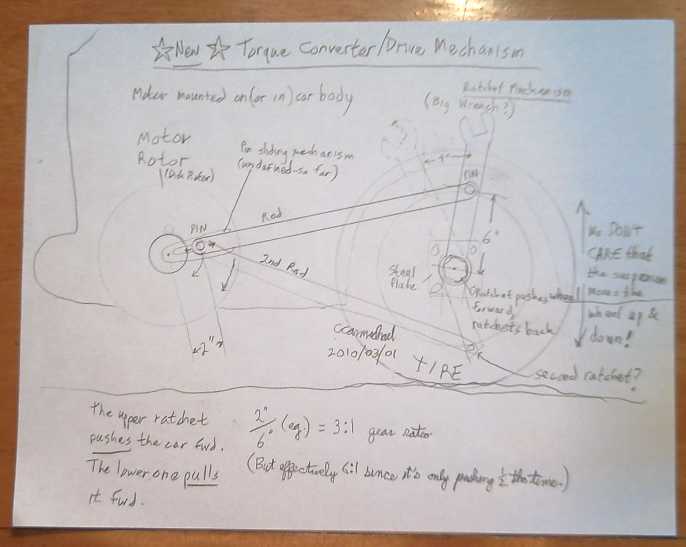
The basic plan.
At first, I
didn't like the idea of long horizontal 'reef bars'/rods,
which would mean the motor rotor would naturally be offset from the
output
rotor - the wheel. It seemed an unwarranted departure from everything
the motor was about. Perhaps there was some practical way to fold the
bars back on themselves? But then I started to think of some major
advantages of this
"radically" different setup:
1. The connection between the motor and the wheel
would be amazingly flexible. There's just the two rods to the two
ratchet devices, which could have a ball and socket joint at the wheel
end. The wheel could move up and down freely
with the suspension, while the motor remained stationary. The rod(s)
and
the ratchet(s) would move, twist and adjust.
2. The motor could and would be
mounted on the body of the car instead of on the wheel: unsprung weight
would be limited to the ratchets and mounting plate. Suddenly a few
pounds more or less for the motor is no big deal. And the electrical
cables wouldn't get flexed with the up-down motion of the wheel over
bumps, eliminating any chance they could wear out prematurely.
3. There would be no brackets to
mount onto the brake drum housing behind the wheel. This could
considerably reduce the installation time and cost, while at the
same time, the fewer parts mounted around the car wheel and axle
would make the system inherently safer if something came loose, and the
tire would be easier to change.
4. Perhaps the motor could be mounted high enough up to be above curbs,
eliminating most of the potential for sustaining damage when parking at
one. The geometry would vary car to car, partly with wheel diameter.
5. Needing only one spinning rotor and no protruding shaft, the EH
motor design becomes more flexible - it could again be made from any
old rotors and independent car wheel axles that can be fitted together
properly, with no machine lathe turnings.
6. Potentially, any sort of available motor might be mounted inside the
car behind the wheel, with the shaft sticking out through the body and
the drive mechanism attached outside. The
practicality of this idea would depend on individual motor and car
geometry and spaces.
A potential disadvantage is that the car body may be too
light to mount the motor on without reinforcement. Another is having
moving parts out in the open, though that can readily be fixed with a
guard over them.
This ratchet mechanism is the output end of things. In
that, we have a
drive
that's better than a gear in that the offset pin on the motor rotor -
and-or the ones on the wheel ratchets - can be adjusted, moved in and
out to
obtain whatever 'gear' ratio seems best. At the input end, the distance
of the pin off center determines the turns ratio of motor to wheel,
from no motion if it's dead center to a low ratio if it's out by the
rim. I can mount a pin at some fixed point and have the motor move the
car
with good power for a low speed test - that will be, at least,
gratifying. The part I haven't figured out yet (in all of two busy
days), shown as "undefined" in
the drawing, is how to get the spin
of the motor to determine the right distance out and hold it there.
Some centrifugal device will have to be worked out for that, that
moves it outwards as the motor speeds up.
...or it could be done Constantinesco's way, with a
pendulum.
A small detail: I don't see any quick way to do reverse
gear with stock ratchet wrench(es), because running the motor in
reverse will still drive the ratchets forward. I think I just won't
have reverse on the first prototype. There's always giant, reversible
socket wrenches...
I think this design is going to prove to be a winner!
Ocean Wave Power Project Revival?
The ratchet wrenches found for the torque converter are
also a better mechanism than the bicycle wheel ratchet
gears to link linear cyclic "piston" motion derived from the waves to
the generator shaft for the ocean wave
power. They'd be linked up with a couple of simple rods instead of
the clumsy 'bicycle chains on a stick' piece that I used.
With those, and a lawnmower motor for a great generator
with no magnetic cogging, I could
do a mechanically superior 'proof of concept' wave power unit. One that
would
probably even work! Perhaps I'll look for a used electric
lawnmower to get the motor from, and revise the wave power unit this
summer if I can find the time (and haven't lost too many of the pieces
- at least I still have the floats assembly).
Microcrystalline Ceramic Motor
Coil Cores Project
February Details
February Thoughts and work
I had occasion to do a bit of study on this subject, and
this time I varied my search terms more and came up with a key point in
the procedure that I'd missed previously. I now have about three
different things I'd like to try with these cores. I also found that
saturation flux of .9 to 1.3 Teslas is said to be attainable with
microcrystalline
cores. I don't have a figure for regular laminates (yet), but I think
that's at least comparable.
The first thing to try is the key step I'd missed in
making the
microcrystalline coil cores. I can try this with cores I've already
made. Once the cores have been fired in the kiln and then quenched in
water a la rakku pottery, they need to be heated up again to a lower
temperature, eg 420-510 ºC, and allowed to cool slowly. In this
second, 'annealing', heating, the micro crystals form as it cools,
embedded in the overall amorphous glassy structure.
Second, it seems most people are making them in thin,
flexible laminate strips. This seems superfluous, assuming the cores
are electrical insulators anyway - who then needs them to be laminated?
However, it seems they can't be made very thick. When I smashed one of
my cores, I noticed that the structure at the surface changed with
depth. This is logical as the clay doesn't transmit heat very well, so
the deeper volumes cool slowly in spite of the quenching, unlike when
quenching a metal.
Instead of making strips, 'solid' cores with lots of
little holes for water to pass through during quenching might work
okay. Otherwise, I suppose laminated pieces could work fine too. I can
address this point later - even if my solid cores just work near the
edges, I should be able to measure some effect and know if a
formulation is working.
The third item is test measurements. If I had a core
that worked a little bit, I may not have noticed it. A slight success
can be built on more readily than just continuing to try random things.
I needed a better way of testing wherein I could take a simple reading
and compare it.
To solve the third problem, I figured out a way to
use the first test jig I'd made, in a modified way. With the coil
sitting on top of a thin piece (of wood) and the scale placed
underneath with a piece of steel on it, the distance between the coil
and the steel would be constant, regardless of the exact size of the
core, the shrinking of which during drying and firing varies with
firing temperature, ingredients mix, and moisture content.
Energizing the coil with a 12 volt battery, using a .5 ohm
resistor in series with the coil (max 24 amps), the lift on the piece
of steel on the scale is indeed measurable as a decrease in scale
weight. Air core reads
about 10 grams decrease. The steel laminate core gives 30.
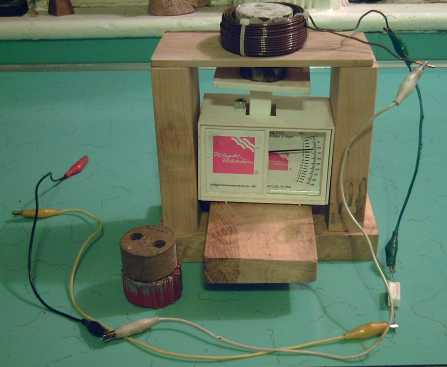
Coil test jig setup
To anneal the cores, I simply have to heat them in the
kiln and let
them
cool with the door closed, since the duration of the heating evidently
has little effect. The problem then is to know how long to turn the
kiln on for. The temperature is too low to use a pottery cone, but too
high for a kitchen oven. I need a 1000ºf
thermometer.
On March first, when I went shopping/hunting for grilles
for the electric heater, nickel metal for alkaline batteries, a ratchet
device for the torque converter and, by the end of the trip, a new
muffler for the car, I also managed to get some "type K" (higher
temperature) thermocouple wire. I'm hoping I can find somewhere on the
web with a table of voltage versus temperature for this common type of
thermocouple wire. Otherwise I need to spend $150 on the real
'pyrometer' and test probe (...made of type K thermocouple), instead of
$3 for
just a yard of wire.
As a final thought, having now, at one point, located a company on the
web that makes
microcrystalline core strips, I could try to simply order some.
Assuming I can find the company again on the web. I'm not sure
that will be any more successful than trying to make them has been,
because
usually such manufacturing companies don't want to talk to someone who
only wants enough material to try out a new design, notwithstanding
that success with a new design may bring in big orders later.
Turquoise Battery Project
February Details
February Experiments
In the last week of January I had put together a "ClO4-Mn"
battery and started charging it at low current as the first stage of
the "burn-in". Following this, like most of my batteries, it didn't
seem to hold a charge. It seemed to me I'd put in the right sorts of
chemicals, in reasonable proportions. The lead acid batteries had all
the right chemicals, but they needed deep cycling to "renew" them. And
there are proceedures for "burning in" or "forming" some types of
batteries. Perhaps
there was similar 'trickery' needed for my own batteries to get them to
work?
First I upped the current to around 30mA. Soon the cell
had over 5 volts across it. Seemed ridiculous. Then I shorted the cell
for a while. It delivered about 5mA. Then I charged again and it didn't
seem to do much differently. Then I reversed the polarity. I expected
the voltage to start at some value and work its way up. Instead it
quickly reached (-) 3-1/2 volts and worked its way down, at first
quickly and then gradually (seconds, minutes) to 1.9 volts. That's
about the voltage it should have risen to and stopped at when connected
the other way around! However, it doesn't stay near that voltage a
moment when the charge is removed.
None of this seemed to provide a solution.
Ni-Mn Alkaline Cell: to make
or not to make?
Sigh! To break the impasse of a great chemistry that I
can't get to work properly, I'm considering making at least a demo
Ni-Mn
alkaline cell. At least for alkaline I think I now have the essentials
worked out to make good working cells. The last missing piece was the
gums to hold
the
briquettes together. Ni-Mn alkaline should hopefully at least be
better than Ni-MH, by
about 66-75%, owing to it being around 1.8 volts/cell and perhaps 3/4
WH/g, instead of 1.2 volts and 1/2 WH/g.
Gas pressure may be an issue. In fact, I think I'd better
vent it - caustic lye spraying one in the face if there's a leak would
mean blindness! The higher the voltage, the more oxygen and hydrogen
are
made from the water. That's why lead-acid batteries (2.0V cells) are
usually vented. (I also expected lower pressures from the perchlorate
chemistry in spite of the voltage owing to higher current capacity,
resulting in
reduced charging voltage, eg, 2.1V to charge 2.0V cells rather than,
eg, 2.3 to 2.4V with lead-acid.)
For the positrodes I'll have to switch to pure nickel
sheet
metal instead of
nickel-brass, nickel powder instead of monel powder, nickel mesh
instead of stainless steel, and nickel bolts, if they exist,
instead of stainless for the terminal posts. The negatrodes can be the
more ordinary materials - it's the anodic oxidation during charging
plus the strongly alkaline environment that seems to corrode everything
except nickel.
Whether I try making it or not may depend on whether I can
get
some pure nickel products without mortgaging my house. With
nickel rod, I can grind it to
make enough powder for a cell or two, and I can pound and thread the
rod to form the positive terminal bolt. With a good mesh to conduct
across the electrode, it doesn't really need a nickel plate backing -
paper or plastic should work. That just leaves mesh... Hmm,
it seems a nickel mesh is 'available' for screen printing, but nobody
actually carries it. A supplier in Vancouver thought he might be able
to get some
in, but he didn't call back.
Likewise, nickel welding rods are 'available', but are a special order
of about $400.
Someone told me that electroplaters use nickel 'shot', but
a trip to Victoria Plating disclosed that it's purchased in bulk and
the entire load is dumped straight into the plating vats. They gave me
one little piece that had somehow escaped. Well, I can grind that into
a little powder!
Otherwise, most of these nickel products are probably
special
order from separate USA companies
(even Inco's nickel powder has to be ordered from the US,
notwithstanding Inco being in Sudbury, Ontario), and most companies will ship only by
couriers with their border piracy. ...This could be a pricey thing to
gear
up for!
Construction Technique: Internal Connections
I had considered that there appeared to be just two ways
to connect the electodes to the terminals, in particular the positive
side, given that solder
would
corrode away: Bolts made of something that wouldn't corrode (hopefully
stainless steel with salt electrolyte - nickel for alkaline cells), or
welding. Bolts are tedious and can come loose; spot welding is not
amenable to small scale, minimal investment manufacture.
As an example of the power of the corrosive power of the
'positrode', I used a #4 plain coated nut and bolt in the present
battery. I
took it apart weeks later and found half the nut, corroded away and
fallen down, and none of the bolt at all. (though perhaps some
remainder fell to the bottom once the nut was gone - I didn't check
there.)
But now I've thought of another connection technique:
riveting. Stainless steel rivets should work as well as stainless steel
nuts and bolts. Perhaps I'll try this next time. Nickel rivets if I
have to make alkaline cells... and if there is such a thing.
Lead-Acid/Sodium Sulfate Battery
Renewal Project
February Details