I started March having just conceived of what at
first glance looked like a great new way of
doing a torque converter, but after a couple of weeks working on part
of it, I started realizing it would have worse vibration problems than
my previous design unless it was made with some pretty complex parts.
And the way I was doing it before, though using some obscure mechanical
clock principles,
was theoretically better as far as I could tell. So I switched back and
finished it. Some
long overdue home maintenance then used up most of the last week of
March and I didn't get past a bench test.
But the part I had made for the discarded new idea could
instead be the main push-bar, arm and
ratchet assembly for an improved version of the ocean wave power
machine, tying the wave power capture floats to the primary rotating
shaft. I also got a lawnmower motor to use as a generator for that,
so the work and parts won't go to waste - assuming I find time to put
together and test the upgraded wave power unit.
I also plugged away at finding out more about nanocrystalline
magnetic
cores. The crystals are smaller than "micro", and using
"nano-" as the search term turned up far more info! (...not a real
"recipe book", though.)
And I plugged away too at finding nickel mesh and other
nickel materials to try making alkaline batteries. It seems astounding
that such a common metal should be so amazingly hard or costly to
actually
buy. Finally I came up with a plan to use the working electrodes from
old dead
(shorted) Ni-Cd/alkaline batteries to test one new component or idea at
a time. The perchlorate battery might all be working except one or two
details, but I can't isolate the problem(s) as to which electrode or
process.
Looking back after 27 months on the Electric Hubcap
project, it has
taken far longer to get this far than I ever expected. An impartial
observer might suggest that the project is anywhere from 6 to 15 months
behind where it "ought" to be -- depending on what I could be supposed
to have known or had figured out before I started.
But inventing is about doing things no one has done before
- uncharted things, and in spite of being a one starving inventor
operation, look what has been accomplished!
* The only effective 5-1/2 HP permanent magnet 'pancake' motor that
anyone
can make at home.
* A matching 3-phase solid state motor controller that's an easy
electronics project.
* Comprehensive plans for making both of these are on the web for
anyone, anywhere to use.
* A mechanical torque converter ("MTC") is in the works, to replace
entire automotive transmissions with a light, efficient "CVT" type of
unit.
* When the MTC is completed, these will bring a practical means to
turn any car economically into a plug-in hybrid -
an electrically ultra-efficient one needing less horsepower and energy.
* Plans for an electric fan-heater on the web for home construction
(okay... not much of an 'invention'!)
* Some valuable car installation techniques have been worked out for
the add-on drive system.
* Designs for electrodes, jigs and cases that will make it practical to
make batteries at home.
* The only current portable battery new chemistry & fabrication
research besides pricey
lithiums. (AFAIK)
* Two possible high-energy battery chemistries have been uncovered: One
uses techniques of ion chelation never before tried in batteries. The
other promises higher voltage, higher energy alkaline batteries.
* I've disclosed that lead-acid batteries can be treated
to last far longer or can be rejuvenated with sodium sulfate salt. (A
fact the
battery industry has kept hidden from the public for at least 70 years.
I also have some sodium
sulfate
for sale since I found it hard to get and had to order a 30
Kg bag of it!)
I've just learned a new term, Scope Creep. It's
the tendency of a project to keep growing in scope from the original
intent.
An inventive project is especially susceptible to this,
partly of necessity, and the Electric Hubcap project has certainly
acquired a lot of it!
The original seemingly simple plan was to use a version of
the pancake shaped generator of the wave power machine as a pancake
motor to attach to a car wheel. But that, in addition to becoming an
almost complete redesign in itself, necessitated creating an unknown
(to me) type of solid state motor controller - easily doubling the
project's scope, even for an experienced electronic circuit design guy
like me. The motor and controller are finished, first
working in 2008. (improved components and techniques keep popping up
now and then, though - necessitating frequent revisions to the
manuals!) But hybridized cars aren't rolling down the street on
electric power.
The components naturally needed proper installing on the
wheel and in the car, with connections to the gas pedal and a switch
for Off-Reverse-Forward up at the front of the car. And re-plugging the
fuses so the signal lights work with the key on "ACC". (Even now
activating the
system isn't tied into turning the car key, though the provisions are
in place... except for my car key's "ACC" contact not working. That's
right, the car radio doesn't work either!)
The October 2008 car move test - though the car did move -
showed that hooking the motor straight to the wheel wasn't really
practical. The RPM of a car wheel at low speed is just too low, even
for a lower RPM
motor. (...now if a car's tires were 10 inches in diameter...) I could
perhaps have used planetary gears to make a compact transmission, but
the better solution seemed to be some sort of highly efficient torque
converter or CVT. Some new design of magnetic or mechanical torque
converter seemed to offer the best prospect - but it was (is) another
big piece
of scope creep.
Then there was the realization that running the car with
the gas engine off would require an electric fan-heater (at least to
defog the windshield!) and an electric vacuum assist pump because car
brakes are made to need vacuum assist. I tried to buy a heater but they
never shipped it, so I made a better one. I have yet to install it or a
pump - more scope creep!
Early on, looking for batteries for the motor disclosed
that since
the successful electric cars made in the late 1990's, Chevron had put
Ni-MH batteries under lock and key and isn't about to let anybody make
any more big enough for electric cars, ever; that lead-acid batteries
were heavy and didn't (seem to) last very long; and that lithiums were
uneconomically expensive. So I decided to try making batteries,
hopefully better ones - Major Scope Creep!
Looking for an easier way to manufacture the motor coils,
I ran
across "microcrystalline ceramic" cores that were supposed to be very
good and would make the motors still more efficient. So without
knowing much about them but having enough ceramics skills to be
dangerous and my own mini-kiln, I decided to try making those... more
scope
creep!
And finally I discovered that certain sulfate salts could
greatly extend the life of lead-acid batteries, so, having so far made
no practical working batteries myself, I started looking into that. I
uncovered that they're used in long-life golf cart batteries, and that
prototype Interstate Optima batteries with sodium sulfate
lasted 5 years of daily EV use instead of "the usual" 1 to 1-1/2 years.
But though it has its practical advantages, perhaps even for Electric
Hubcap drive systems... here it's more Scope Creep!
The Electric HubcapTM Vehicle Drive System
March Details
A New Drive Configuration and Back
As hinted at last month, March opened with a plan for a
"radically different" drive
motor configuration. On the first, a critical part was found: a
ratcheting lever that would turn the car wheel in one direction when
pushed, but simply click back when pulled. This would permit an
off-center
pin on the motor rotor to drive the wheel via a rod and the lever. A
centrifugal device setting that pin's distance from the center based on
the motor RPM would then constitute it a variable ratio torque
converter.
By the fourth, an attachment plate for the car wheel
had been made and the mechanism was tested by standing on the lever and
moving the car. Nothing busted. It seemed good enough at least for a
prototype.
But with
long linkage rods required, the motor would have to be mounted next to
the car wheel, preferably above it, instead of on the wheel as per all
previous plans. But that should actually have some advantages!
By the middle of the month, work was progressing well, but
a sudden realization came that there were serious problems with the
design. It was abandoned and I went back to working on the previous,
"rotary" design.
The main work that hadn't been done was to mount magnets
on the drum rotor. To do that needed a new jig for 12 equally spaced
magnets at 300mm diameter, to replace the previous 18 magnet jig. I
modified the jig:

Top: old jig piece for 18 equally spaced magnets.
Bottom: revised jig for 12.
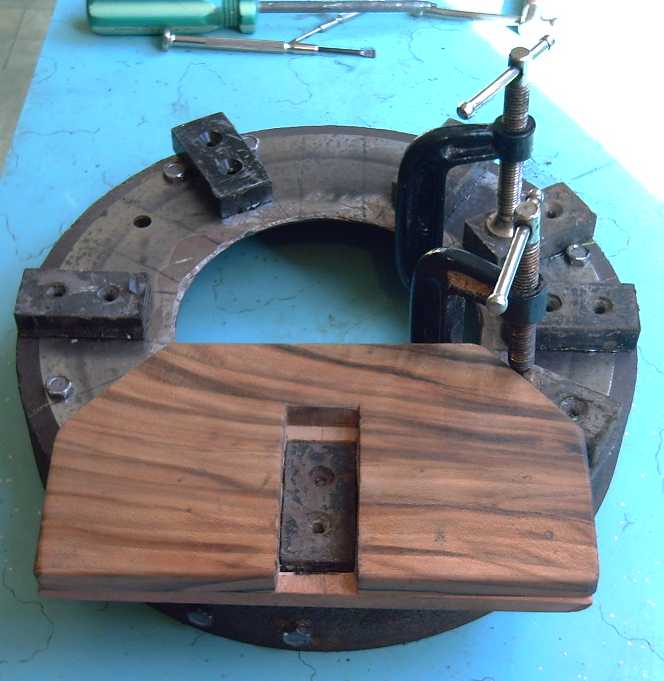
Gluing the magnets onto the drum rotor.
The second six kept trying to flip over as I tried to get them into the
hole.
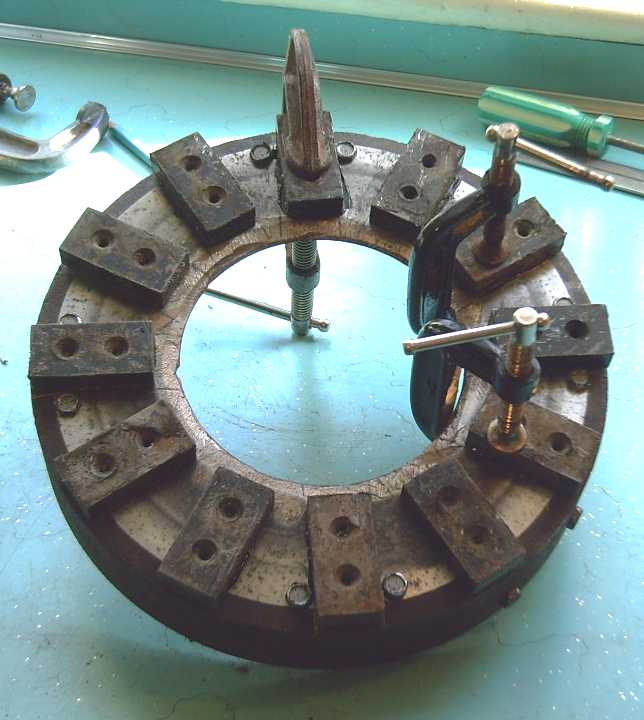
Got them all. (no fingers lost!)
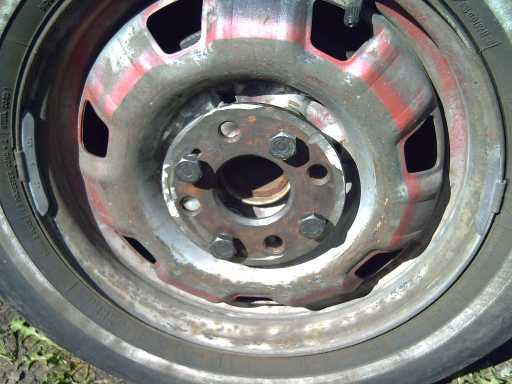
The plate bolted to the car wheel.
The pins from the torque converter inertia plate fit into the four
empty holes for a flexible coupling to the wheel.
Motor Controller Improvements
I decided to make another motor controller. I have no
particular need for a second controller, but I wanted to
improve the layout, and the instructions in the manual, and also see if
I could clean
up the heatsink area somewhat. I may make it 24 volts instead of 36 -
which just means a few power components with different specs.
Previously the wiring and components on the heatsinks looked a bit like
this:
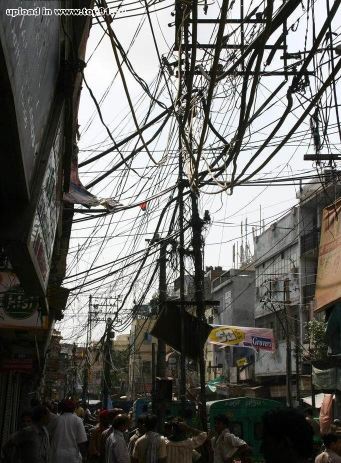
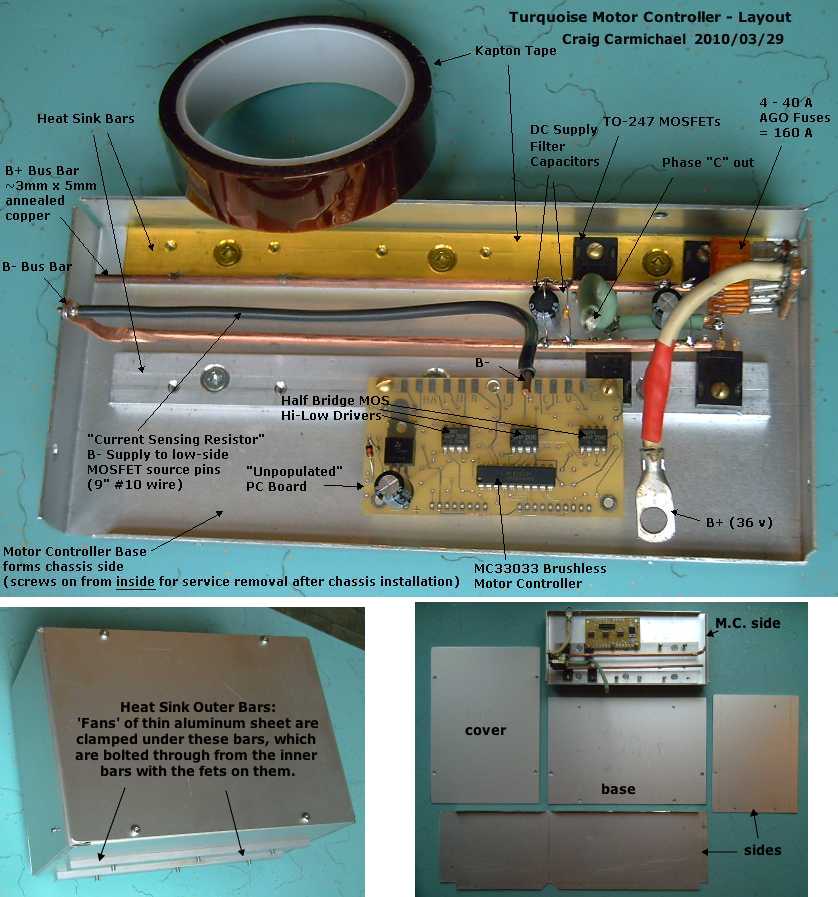
Tho it's unfinished, the likelihood of achieving a much neater job
seems evident
An interesting thought came to light: I had been puzzled
that the leeds on my filter capacitors had been "burned off", while the
capacitors themselves looked intact. Usually the capacitors pop aprt if
there's a problem and the leeds are fine.
In fact, I had been using some
lead-free solder that I later found was causing serious corrosion
problems. (Rather, its flux was.) It's likely that I used that solder -
the breaks happened at or near the solder joints - and so the problem
wasn't electrical at all. That means I probably don't need these
oversize 200 volt capacitors in this 36 volt circuit. I've gone back to
much smaller smaller 100 volt components. That also will help make it
tidier.
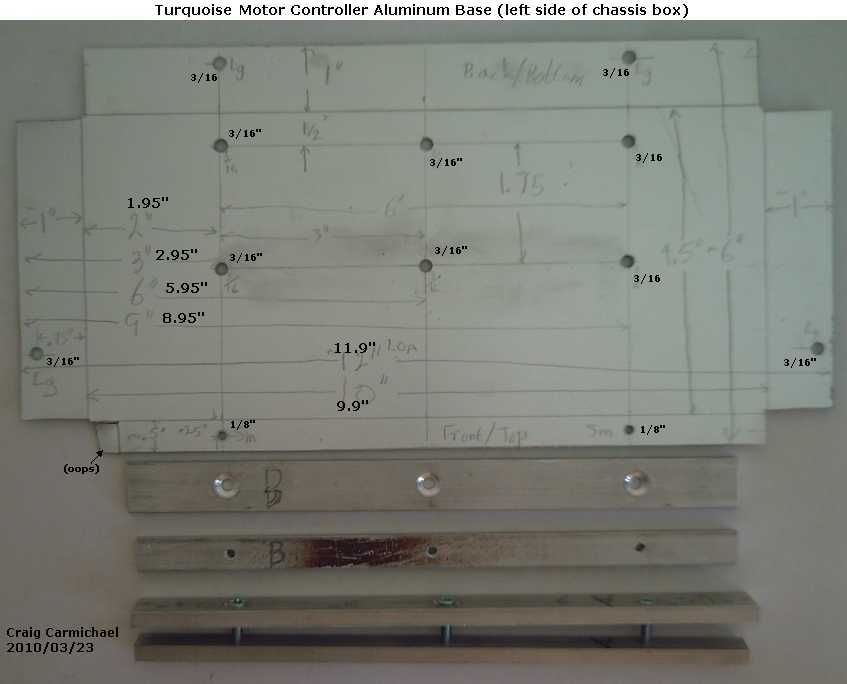
This is part of my idea of improved documentation for the manual -
the actual aluminum motor controller base pieces, cut and drilled, with
dimensions, as seen finished in the previous image. Of course, I
neglected to account for the thickness of the other metal pieces in the
written dimensions (and the actual piece), so I typed revised
dimensions into the image. Maybe next time I'll just go for typed,
which can be changed without a trace just by starting again with the
raw image.
36 V Supply and Dangerous Voltages
On testing the electric car heater and working with the
wiring inside
it, clipping on test leads and measuring voltages and currents, at
times I was nonchalantly touching
the supply voltage, and I thought, yes, it is a
really good idea for the main supply to be only 36 volts when DIYers
will be doing these sorts of things! Even 48 would
be getting up there, and 30 or 24 volts would be even better. 144 or
300 volts DC for electric car systems is madness - and worse in a "DIY"
system!
It took me some time to get out the trap of thinking that
because the car companies were using high voltages, that must be the
way
to go. The car companies probably started it in ignorance themselves,
the systems being initially designed by electricians familiar with line
voltage motors in buildings, running on the power grid. Those are
generally in dry, heated locations, and the connections to the power
are very long. The wiring would be very costly if thick wires for high
amperages
were needed. The fat wires needed in cars only run a few feet. (and fat
car battery cables can be had "used" at an auto wreckers, too.)
Electrically savvy types on the
DIY_EV_Cars@yahoogroups.com list keep haranguing me when I warn some
newcomer about the dangers of higher voltages, and reiterate that
motors of any
size can be made for any voltage and will perform exactly the same.
They seem not to realize that not everyone has the same experience they
have working with dangerous voltages, and that an amateur DIYer who
isn't an electrician designing his own electric car system, is in much
more danger than a cautious professional who knows all the angles and
safety precautions in
advance. (...who is nonetheless making a dangerous and needless hazard
for himself just to save a few dollars of copper.)
The only reasons for using higher voltages are: (1) if the
required kilwatts would result in absurdly fat cables that are hard to
work with. (2) if a surplus motor is available that is already made for
a higher voltage. The Electric Hubcap system partly addresses both
these issues, first by being a 5+ HP, 36 V motor than can be easily and
cheaply made at home, and second by needing less power to move a
vehicle. (I keep thinking I should make a 24 V EH motor just to show it
will work the same as the 36 V one.)
36 V Car Heater Project Continued: Schematic
and Wiring
The electric heater works nicely. I've posted the plans
for making it on the Turquoise Energy website at: http://www.TurquoiseEnergy.com/hybridize/heater/DC-Elec-Heater-Plans.html
so
I won't go into construction details in this newsletter.
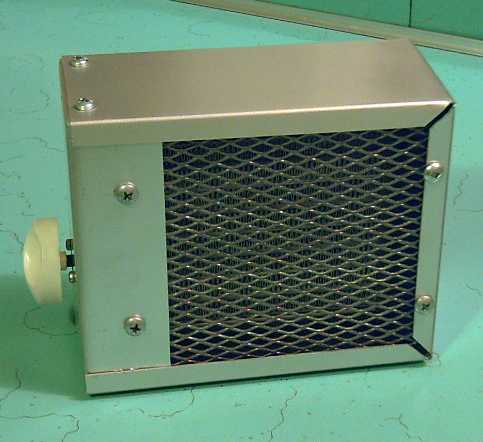
The assembled heater, minus its mounting. The switch side (left) is
the bottom.
Mechanical Torque
Converter Project:
Torque Leverage Without Gears
March Details
After figuring out what seemed like a much more
certain-to-work design for a mechanical torque converter that would
have much less noise and vibration, I abandoned
the half-made one and drew up a list of items that would have to be
completed.
1. Make a plate for the car wheel with the hex nut or bolt head at the
center.
2. Make a mounting for the motor and mount it on the side of the car
near the wheel.
3. Make a bar and both end fittings to connect the ratchet (wheel) to
the offset pin (motor).
4. Make a centrifugal device to adjust the offset of the pin from the
center of the motor,
based on the RPM of the motor.
5. Toss the wrench(es) and get something that could provide a reverse
gear.
6. Make and install covers for the moving parts and the motor.
7. Tidy up, get rid of old fittings, re-route motor cables, etc.
Once items one to three were complete, the car could be
tested in a big parking lot or on a quiet street. The speed reduction
ratio would have to be set to give it
sufficient starting torque to get up speed in reasonable time, yet not
overrev the motor at too low a speed. (Of course, there's no "too low"
a
speed in a first proof test!)
A four to one ratio would probably allow the car to get
moving on level pavement, and in theory get up to 50 Km/Hr. Ten to one
would let
it start up a good hill, but the car would only reach 20 Km/Hr. The
minimum ratio, two to one, would allow 100 Km/Hr... if the car would
start moving, by no means a sure thing.
One
The first item was done by March 4th, and it was also
tested that day: I attached the plate to the wheel, and moved the car
by standing on the end of the ratchet wrench. When the end of the
wrench sank down as
the car moved, I lifted it, ratcheting it back to horizontal, and
gradually moved the car over several feet of eneven gravel, including
uphill. This test
proved that the plate and nut, and the wrench, were all at least
nominally strong enough to not bust right away with the torque needed
to move the car.
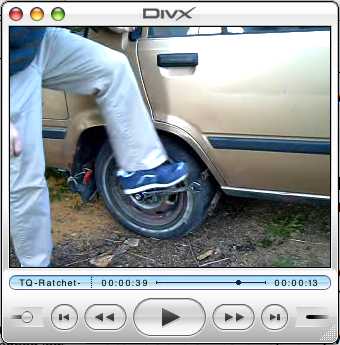
Moving the car by stepping on the ratchet wrench
(I didn't post the movie since this technique won't be employed
- if anybody wants it, please ask. 3.6
MB)
Total addition to unsprung weight will be around 1.5 Kg:
the plate with bolts and nuts, and the inner ends of two ratchet
wrenches.
This is a marvel -- mounting the motor off the wheel
solves all the problems of adding
unsprung weight to the wheel. You probably add as much when you go from
old worn tires to new ones with good tread!
Interestingly, the Constantinesco torque converter speaks
of "mechanical valves", which term I don't understand the meaning of
and was unable to find a fitting definition or explanation for.
"Valves" is the British word for vacuum tubes. In context,
that probably would imply vacuum tube diodes. But the text
mentions ratchets as an alternative - used in the "Meccano set" model
version, the effect appears to be the same:
"This example follows the same arrangement as in
fig.
18, but
ratchets
had to be used as it was not possible to construct mechanical valves
with
Meccano parts."
However, in the search I located a catalog:
"Morse/Browning Clutches and Torque Overload Devices". I suspect the
problem is mainly one of nomenclature - what do you call such
things? "Rotary diodes?" Some of them do have one way stopping, the
other way slipping, as desired. I suspect some of the mechanisms are
much superior to a simple ratchet. (The catalog has a lot of confusing
choices... perhaps I should make the one with the wrench, run the car,
then show them the movie and see which model they recommend!)
One choice I didn't see (at a glance) are any that can be
put into reverse.
Two
I decided to mount the motor above the wheel
instead of behind it. There didn't seem to be much room back there, and
above there was an adequate area... and it was certain never to hit
any
curbs while I was parking. (Another advantage of mounting the motor off
the wheel.) Here, however, it would stick out farther,
and the
bars to the wheel would have to have bends in them below the car fender
to line up right and still push, in by the wheel. The ratchet wrenches
would also move around a lot more with bumps as the wheel moved up and
down.
So what? In fact, the weight of the bars and ratchets will be held more
by the car than by the wheel, minimizing the effective "unsprung"
weight.
Looking at a few cars in a parking lot, it appears none
have much room near the wheel and each one will need mounting in its
own best place. But now considering unsprung weight, straight above
should actually be the ideal place.
The motor mounting brackets were made by the 10th. I
figured out a couple of good new techniques for bending steel bars in
the process. Also I got the inside trim removed from the car to access
the inside of the body metal and see where best to drill mounting
holes, and I pulled out the cables to the wheel and the motor
controller to reposition everything. Although this is the rear 'roll
bar' area, there's nothing but sheet metal to attach the motor to. Oh
well... brackets and big washers!
Then on the 12th, I decided to turn the motor around and
have the rotor face out instead of in. It would be a great advantage to
have access to the rotor without dismounting the motor for prototyping
the motor end of the torque converter. So much for the new mounting
brackets!
The 11th started with rain, and I started giving
consideration to how the link rod would attach at each end. I found a
ball bearing race left over from the wave power machine that was a
little bigger than the 1" wrench open end, with a 1/2" interior... for
a 1/2" bolt. If I ground out the open end end of the wrench right, it
could be gripped in there and could only come out the sides. With the
bolt inserted through a forked end on
the bar, it would all be held together. Presto! There's one end with
ball bearings. I ground out the wrench and cut the fork pieces on the
12th, but I didn't get them welded. (I also ran two tests on a
lead-acid battery, added sodium sulfate to it, re-fired my core pieces
in the kiln, improved the cores test jig, and wrote again to try to
order
nickel mesh for alkaline batteries.)
Whether it's a big enough bearing race to last reliably
for extended travel, I'm not going to try to answer. Some of the parts
could last anywhere from 50 meters to 50 megameters. I'll hope for
closer to the latter figure in all cases. Any that prove closer to the
former will have to be up-sized.
Three... strikes and you're out!
I felt it was inevitable that the offset drive pin on the
motor would have to have ball bearing connections to the drive bars to
the wheel. Failing bushings with oil being pumped through, nothing else
would take the strain of moving a car for too
long.
On the 15th, I welded together the rod end pieces and made
the
ball bearing
joint of the ratchet arm with the rod from the motor. Everything seemed
to be proceeding smoothly.
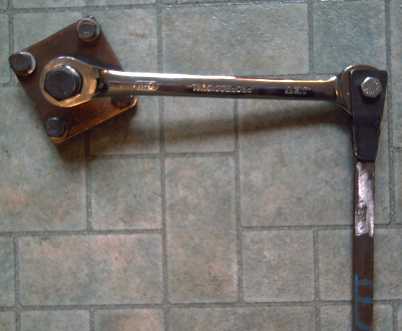
Wheel plate, ratchet device with arm (AKA wrench), having a ball
bearing race
securely gripped, and link bar to motor.
I noted that the weight of the completed assembly was
significant. Suddenly I realized the whole mechanism wasn't
going to
work! If everything was mounted on a solid frame, it
would work. But the car wheel is on springs. With the motor
mounted on the car body and links to the wheel, any non-symmetrical
forces such as would be created would act to make the suspension jump
around instead of turning the wheel, simply shaking the whole car!
Oops! One
could push the wheel horizontally from front or rear and the degree of
the problem would be greatly lessened, but it would still exist. It
seemed the only way to apply non-symmetrical force from the car to turn
the wheel
would be through something like a drive shaft. That would mean gears
and losses.
In the next few days I thought of a couple of other
features
of the design that would cause problems. First, the off-center pin
would create imbalance and unbalanced forces in the motor. That itself
would
cause a lot of
vibration. It might well be worse than my rotary design.
There are ways to make all the forces symmetrical and to
keep the motor balanced, but the whole thing starts to get complicated
with specially cast parts and double pins, rods and levers going
opposite ways. Constantinesco's last, most complex looking design
appears to have these sorts of balancing features. These then become
even more complex to make centrifugal as I'd envisioned. One of the
goals of this project is components that can be made at home or in
small shops rather
than in a foundry, or special factory.
Another consideration is that the push rod plus arm to the
ratchet assembly
weighed quite a bit, and they were to be pushed back and forth. That
would be fine at low speeds, but like a clock mechanism, wouldn't it
take a lot of energy to move the mechanism at
higher speeds - motor and car speeds? Especially if they were all
doubled up for balance? If they were a lot lighter, they might bend.
The losses could be much worse
than the minor frictional losses that might be expected in the rotary
prototype. The only part being shifted in the rotary design is the
inertia
plate, which is the active motion that governs the amount of thrust
transfered to the wheel at
any
given speed.
My lack of interest in the finer points of mechanical
engineering shows in not thinking of these details sooner. I guess I'd
rather be designing circuits or writing
software. So after two weeks, I decided I'd best go back to my rotary
design. (Too bad I ripped out
the motor controller and
the wires to the motor because I had intended to move the motor to
a new position! I also ripped off some plastic interior from the side
wall of the car. Sigh! At least I didn't get around to removing the
main motor mounting brackets on the wheel, and I bought a new piece
rather than cannibalize the
original motor
straps to make the new ones, saying "I'll keep these just in case...".
And I didn't quite get to drilling the holes
through the side of the car!)
But much of the effort was not wasted. The
rod, arm and ratchet piece is a perfect fit for an improved
proof-of-concept
ocean wave power unit.
Also, the idea of balancing the forces could be applied to
the rotary design. One could conceivably have two rotating inertia
plates instead of one, with opposite slots in the rim of the drum
rotor. As they would move oppositely, their movements tending to cause
vibration would cancel,
viz:
________ ________
____/
\________/ \____
____
________
____
\________/ \________/
Other parameters that may well want adjustments are the
slope and the shape of the slot ramps, and the actual weight of the
inertia
rotor plate(s). These will affect how hard the motor is worked to
produce a given impulse to the car wheel and how much noise it will
make. A curving ramp layout might make almost no noise, viz:
(
)
(
)
(
)
(
)
whereas the flat 45 degree slopes were very noisy and loaded the motor
heavily. I cut that slope in half for clockwise (forward drive), which
remains to be tested. I think the main problem with the curving ramp
layout is that it's harder to fabricate. Not impossible, though! I
suspect the first one will be so noisy that I'll have every incentive
to do a curved slot.
On
the 17th I trimmed a few things up and made ready to put the magnets on
the drum rotor. Since the rotor ramps were removed, I ground the entry
to the counterclockwise (backing up) ramps into a shallow curve.
I'll be able to compare forward to reverse - especially if the car
actually moves. But once moving sideways, the plate will still hit the
end stops full tilt.
On the 18th I drilled holes in a plate to mount on and turn the
wheel. This plate needed two sets of four holes, one set to bolt to the
car wheel nuts and the other for the link pins on the inertia plate
that drives the wheel. (One set was already drilled because this plate
was the center piece cut out of the brake drum.)
As previously mentioned, the connection of the link pins
to the plate forms a flexible coupling that greatly reduces the effect
of the weight of the motor assembly on the wheel as the car hits bumps
in the road.
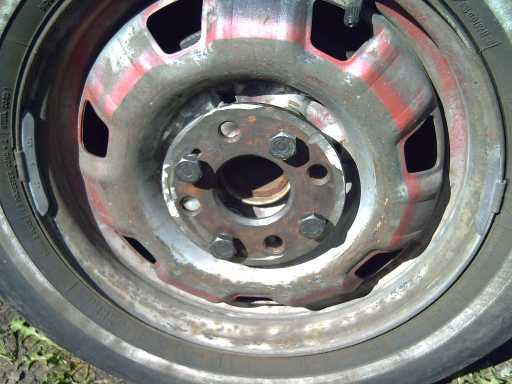
The 19th saw the magnet installing jig finally changed to
what
I've
wanted for a year: 12 evenly spaced magnets. I might like to experiment
with other magnet spacings and/or other sizes of magnets that might
tweak maximum performance or low speed torque a bit, but quite aside
from magnetic considerations, the 12 of the 1 x 2 x .5 inch size
magnets with even spacings makes a pretty good coil cooling fan. (At
the moment, not much air is blowing out, though -- in the present setup
there are no holes for
the air to enter at the center.)
Next the 12 magnets were glued onto the torque converter's
drum rotor. (See EH - Vehicle Drive System for photos.) With house
maintenance intervening for a week, the motor was finally tested with
the magnetized drum rotor on the 28th. It ran great. (Why wouldn't it?)
On the 31st, I clamped it down properly to the bench and made a lever
arm to hold the torque converter back with. Certainly there is force
there. The question is, is it enough force to move a car? Since the
force is in little pulses, each of which *should* be strong enough, the
question should boil down to whether the car will start to move in
small increments, or simply go back to where it was after each pulse -
sit there and vibrate. I can hold the lever from turning because my arm
moves a bit during the pulse, then pushes it back between pulses that
little bit - thus my vibrating arm holds back the *average* torque
rather than the max.
Here is a movie of the bench testing (click image, 5.7 MB AVI):
If it still doesn't work, there is one easy thing to try:
remove two of the four 'strike' pins from the inertia plate and half
the ramps
from the drum. Then there will be just four torque pulses per
revolution instead of eight (two pulses up, two down), and they can be
made twice as strong, eg, just because the motor would run faster, or
else by steepening the ramps.
A final thought for the month: People have asked me if the
converter will lock to 1:1 with the wheel when cruising. I've said
that if the converter is as efficient as it should be, it doesn't
matter a lot whether it locks or not.
However, I've thought of a way. Put in a spring that
pushes the inertia plate to one side, to the "bottom". Not so hard a
spring that it can prevent the motor from starting to turn if it's
stopped at the ramps, but anything short of that.
Then if the torque
isn't high enough, the pins will hit the ramps and not go up them --
1:1
direct drive. (No noise, no vibration except when starting from a stop
or accelerating!)
A spring would also eliminate the need for
having upper ramps at all. (It has to be strong enough to pull the
inertia plate back to base before the next ramp at
maximum RPM. I don't
think this is exclusive to not preventing
the motor from starting.) In fact, having spring return
and no upper
ramps would cut the number of torque hits in half even retaining the
four lower ramps, again allowing stronger hits. Say! It would also
simplify construction of curved ramps - there'd be no upper side to the
"slot"! This seems like a very promising line of development.
Micro Nanocrystalline
Ceramic Motor Coil Cores Project
This month I learned that the size of the crystals at
issue is "nano" - or tens of nanos - rather than "micro" - which would
be 100 times longer and a million times larger by volume. Searches on
"nanocrystalline" thus yielded far better info than previous searches
on "microcrystalline".
What's the big
deal?
A good question is, what advantages do
nanocrystalline ceramic cores have over the iron alloy motor core
laminates
everybody's been
using for over a century? A second question arises from the answers
to the
first: if they're better, why aren't the major motor
companies switching?
At first, I was mainly attracted to the idea they might
make the motor coils really simple to make. It looks like the
fabrication
will be more complex than expected (still quite doable), but other
excellent reasons have
come to light.
The first question has three main answers:
1. Increased
Motor
Efficiency.
Three main things keep efficiencies low enough that motor
cooling is very important:
* electrical wire resistance losses ("copper losses").
The core
material
has no effect on this.
* magnetic core material hysteresis losses. The
magnetism in
the electromagnet coils reverses as the motor
turns. This means repeatedly discharging the residual other-direction
magnetism that's
left over. Alloys are chosen so they
won't hold a magnetic charge (opposite to permanent magnet materials),
but with regular metallic alloys containing magnetic materials, the
magnetic charge holding is always greater than zero, and some
of the electricity going into the motor is used up reversing it.
Because the crystals in the nanocrystalline
ceramics/composites are so small and are not physically touching
each other, they won't hold a magnetic orientation: they demagnetize
spontaneously. Therefore the magnetic hysteresis losses are very
small.
* eddy current losses. The magnetism going by from the
rotor magnetism induces electrical currents into the core material -
generating
power into a short circuit. Regular laminates are used to "dam the
river" with
one little dam after another to prevent the electrons from flowing
freely.
When the cores are electrically conducting alloys, this technique is
not
100% successful.
Nanocomposite materials are insulators - virtually no
eddy
currents can flow.
("Slip loss" of induction motors doesn't apply in a permanent
magnet
motor such as the Electric Hubcap.)
Thus, the main motor losses except copper losses are
reduced to
near insignificance and higher efficiencies can be obtained. A 92%
efficient motor is only a little stronger than an 84% for "x" watts
input, but it generates only half as much internal heat that has to be
dissipated. (This is especially significant if it allows turning
"liquid cooled" into simple "fan cooled".)
2. The
Magnetic Permeability is Higher
Surprising as it seems, and quite unlike ferrites, the
maximum
magnetic field before saturation is higher for the nanocomposites than
for solid metal - .9 to 1.2 Teslas. (Sorry, I have no figures for the
metal, but it's said to be lower.) It might be possible for motor coils
to
develop "supermagnet strength" magnetic fields similar to the
supermagnets they are driving.
That means the motor can develop a higher torque. It's
still doubtful whether a motor of the EH size range could develop
enough torque directly
connected to the wheel to start a car moving uphill. And even more
unlikely it would do so without also developing "burning out" levels of
heat in adverse driving conditions. Higher torque would however mean
that the mechanical torque converter could "latch up" for 1:1 drive at
higher torque levels.
3. The
Material is Lighter
The weight of the nine coil cores is reduced from around 2520 grams
with
steel to around
900 - that's a 3-1/2 pound reduction in total motor/torque
converter weight, 7% off of 50 pounds.
4. Are
they Less Attracted to Magnets?
It seems to me that some
ferrite inductor cores aren't attracted to magnets at all. When I noted
this, it struck me as surprising, since their whole purpose is to carry
a magnetic field. I could be entirely wrong about this observation of
years ago. The one and only piece of ferrite I have now is slightly
attracted to magnets. Of course, possibly it could also be only a
marginally effective core material. But if it is true that a material
that isn't attracted to magnets can conduct a magnetic field, it
could also be
the case for nanocrystalline ceramics. Certainly my failed cores mostly
are unattracted... of course, they're also failures. But If it's
possible to have such a thing (a big IF), this would give rise to two
major
advantages:
* The components would be easier and safer to handle.
Anyone
who has tried to put a permanent magnet motor together or take one
apart knows how hard it is to pull the rotor out and how it pulls
itself back in. The difficulty - and danger - increases once
supermagnets
are brought into the picture. For the Electric Hubcap, the stator and
rotor have to be brought together and forced apart by an inch or more
with
bolts. Failure to do it properly could result in very serious finger
and hand injuries. (At least it can be done without special equipment -
I don't see how it could be on radial flux supermagnet motors!) An inch
of non-attracting coil materials, or weakly attracting materials,
between the stator
backing steel and the rotor magnets would be a great improvement.
* There would be no cogging. "Cogging" is the magnetic
grip
holding onto the rotor as the rotor magnets line up with the core iron
in the stator coils. It causes the rotor to align to certain positions
when it stops, and there's a breakaway force needed to overcome the
cogging before the motor will start to turn. It also causes some
vibration, and the pull between the rotor and stator causes extra load
on the ball bearings between rotor and stator.
In a motor, the cogging can pretty much be ignored.
(Greased bearings last for ages anyway, and there are other things
causing more vibration.)
But in a unit used as a generator, it causes a minimum
threshold of wind speed, wave height or whatever before the unit will
overcome the cogging and start to turn. This leads to non-cogging air
core generator designs that use more materials, poorly utilized, to
achieve the desired power, raising the price for alternative energy.
Non-attracting, non-cogging nanocrystalline cores - IF they are
possible - would greatly improve the situation.
The second question was: Why aren't main-line motor
manufacturers using it?
The way motors are usually made, the alloy laminates are a
major structural component of the motor. Look at a car alternator: The
laminates make up the body and give it its form. They hold the end
bells apart. Where an
outer
shell is used, they must be securely attached to it, and that would be
hard with ceramics, especially as the coefficient of expansion would
probably be different from
the shell. To use a material that might be subject to breakage would be
a nuisance and probably a safety hazard.
Additionally, the finished dimensions of ceramics are hard
to control
to the degree of accuracy required. The clay shrinks as it dries, and
it shrinks more when it's fired. The usual gaps between stator and
rotor are measured in 100ths of an inch, and the ceramic dimensions are
likely to vary by considerably more than the gap.
To put it more simply, with typical motor construction,
using nanocomposite ceramics would be a great headache.
This is a big advantage of the Electric Hubcap motor
design. The
coils are made separately and simply bolted to the stator backing
plate. Whatever works best is only relevant to the individual coil
design, not to the motor design as a whole. The EH's huge 3/8" air gap
between the coils and the supermagnets
makes minor dimensional variance unimportant.
Another answer to the question might be that it's all too
new and there are too many different directions, materials and
formulations being followed. The options are still confusing.
Still,
if one finds a practical way to produce the nanocrystalline structure,
it would appear it's easily adopted on the axial flux machine but
difficult to
employ on traditional radial flux, hence motor makers might have to do
a lot of rethinking about what goes into making a motor - the sort of
rethinking
that's gone into the Electric Hubcap.
March
Experiments
In February and early March I did a little reading on this
subject. I finally realized there were two quite different categories
of microcrystalline or nanocrystalline materials: the ceramics with
metallic glasses, "metglass", and also alloys. The alloys would of
course be electrically conductive and would need to be formed into
insulated laminate strips like other metal cores. The ceramics, also
called "microcomposities", are
insulators, and it seems to me they should, all else being equal,
perform better simply by having virtually zero losses from electron
flows.
But the gains may be greater than just zero eddy currents.
One web site about "nanocomposites", says: "A
completely new phenomenon has been observed when reducing the particle
size and the separation between neighboring particles into a nanometer
scale in composite matters. For example, it has been found that a
Co-
or Fe-based nanocomposite can possess a permeability much higher than
that obtainable from the bulk Co or Fe metal. This large
enhancement in
permeability is due to the exchange coupling effect. The exchange
interaction which leads to magnetic ordering within a grain also
extends out to neighboring environments within a characteristic
distance, the so-called exchange length Lex. Thus,
neighboring grains
separated by distances shorter than Lex can be magnetically
coupled by
exchange interaction. For a traditional powder material of large
particle sizes, exchange coupling effect is negligibly small in
determining magnetic properties. However, when the particle size plus
the separation between particles is reduced to approximately Lex,
intergrain
exchange coupling plays a dominant role and the material
will possess a variety of properties different from the bulk size
material. One important effect is the cancellation of the magnetic
anisotropy of individual nanoparticles: when the particle-particle
separation is significantly less than Lex, the intergrain
exchange
interaction makes all the neighboring particles coupled. This coupling
averages out the magnetic anisotropy of individual nanoparticles. As a
consequence, the permeability of an exchange-coupled nanocomposite can
be even much higher than the permeability of its bulk counterpart."
I also saw sites listing actual strengths of .9 to 1.2
Teslas for some of these materials. Perhaps we may after all be able to
obtain electromagnetic fields in a motor stator on the same order of
strength as the supermagnets on the rotor?
Notwithstanding the ever increasing difficulty of finding
anything uncommon on the web, I located and e-mailed a couple of places
making strips of the alloys in order to get some - one in USA (didn't
return my e-mail) and one in China - but no luck. They probably can't
be bothered if it doesn't look like you'll imminently order an
industrial quantity. Too bad for me perhaps, but too bad for them,
since being listed as the supply source for a superior material in the
Electric Hubcap motor plans would be very good free advertising and, if
the price were economical, would probably bring multiple big orders
later as the motors gain popularity. I won't dwell long on suppliers of
unobtainable
materials.
So much for trying to offload even this one project, and
back to trying to make the microcrystalline ceramics! I realized the
problem is (presumably) more in my methods than in my materials. If I
can get them to work, cheap clay cores might allow me to thumb my nose
at the alloy suppliers.
First, the ceramic has to be fired and then quenched
(dumped into water) to cool it quickly. This creates an amorphous,
glassy structure because crystals don't have time to grow as it cools.
This I was doing except for my first few attempts, but I was making
whole solid cores. Ceramic conducts heat poorly, unlike metal, so
only near the surface would they cool quickly. It would seem they need
to be made as thin laminates. However, being electrical insulators, the
laminations are only needed for the quenching - perhaps they can run
any direction regardless of the direction of magnetic field motion.
That would mean they could each be a complete thin cross section of the
core, built up to whatever height is desired, in this case one inch.
unless each minute gap interferes with the magnetic circuit, in which
case they would better be vertically oriented.
I tried to slice one of my current cores, #14, into thin
strips with a zip disk on the angle grinder, but I got a mess of broken
pieces. Bowing to the inevitable, I broke #21 apart with a hammer. I
re-fired and re-quenched the pieces to re-test the same cores after
proper processing. Then to anneal them, I reheated them to 430c and
allowed them to cool slowly.
Next was a magnetic strength test using the test setup
mentioned last month that lifts a steel piece on a scale. First was a
calibration with air (-4 grams) and then with the steel core (-17).
Next I dumped all the pieces of #14 into the coil and tried again (-6).
#21 also gave -6 grams. However, these figures are very approximate on
a spring scale with 10 grams per division, and I wasn't sure they
weren't just minor discrepancies. (I spent $45 on a 100th of a gram
electronic scale but it turned out to be a lemon. Not only does it need
to be banged and cajoled into turning on, it then keeps shutting itself
off, at least once per minute, right while you're trying to use it.
Ugh! Its name, "snake eyes scale", should have warned me it was a
losing dice roll. I have to go out again and try to find one that
actually works.)
I re-heated the two sets of pieces to 490c to see if a
higher annealing temperature would make any improvement. This was
hotter than I'd planned and near the upper limit - I hadn't stuck the
thermocouple wire in far enough. I was puzzled by the slow heating.
Finally I pushed it in a little farther, and the readings rapidly rose
and showed that the kiln was already above my target of 465c. The next
test seemed to definitely show they were no better than air. Were they
before, or was the difference merely within the limits of reading error?
Turns out it was the battery. The coil draws a lot of
current, and the battery changes its state of charge a bit with each
test. It starts high, gets a touch lower after several tests close
together, then recovers a somewhat in a while.
Now I have read an e-mail sent to a list months ago that I
missed reading (along with several others that day), suggesting that an
analog/linear Hall effect sensor be used to measure magnetic fields.
Duh! Why didn't I think of that? I'll get a couple next time I'm
ordering electronics parts at Digi-key.
I also looked at some pieces with a 10x magnifying glass
and I got the vague impression they were more glassy right at the
surface than in the interior (exposed by further breaking the pieces).
This wasn't very certain and trying a 40x didn't help. If the
impression was correct, one might only want the pieces to be 1/16"
thick or even less.
The next step may be to roll the clay mixture out with a
rolling pin to about 1/16", and make a cookie cutter to cut them out as
2" circles (complete with the mounting bolt holes)... or else as 1"
strips. Making them as
laminates as thin circles might actually be easier than pressing them
into a
mold to make solid cores. Then the finished ceramic pieces would have
to be stacked up to 1" thick... or the strips cut to length... and
(presumably) glued together. Gluing
*might* be done with certain ceramic materials (eg, rutile in sodium
silicate?) as part of the annealing step. Or else, a dip in motor
varnish along with varnishing the coils would likely work fine.
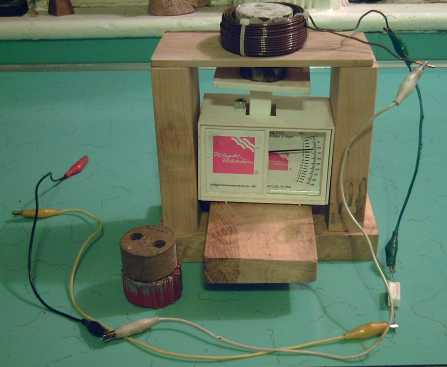
Coil test jig setup
(I finally bought another more precise digital scale towards the end of
the month - the new one actually seems to work.)
Looking at the chemistry of Laguna Borate, I see it's choc
full of good glass forming things already mixed for the amorphous
glassy substrate. Including of course the boron. Frit, essentially
finely ground glass, will help out.
The other component is the substances for the
nanocrystals. Iron would be traditional, and-or nickel and cobalt, for
ferromagnetism. Unlike nickel metal itself for alkaline battery
materials, nickel oxide, carbonate and sulfate are readily available at
local pottery supplies.
As I thought about it, an "amorphous glassy structure" sounded much
more like a
pottery glaze than a clay body. Perhaps then the
structure
should be:
* thin strips of ceramic or porcelain - simply something to apply a
glaze onto.
* a glaze in sodium sulfate ("water glass") with minerals containing
magnetic elements
which are likely to segregate into metal and oxide elements (per web
info) - perhaps
mainly ilmenite, rutile or an iron oxide, and borate, perhaps with
barium carbonate. Copper was also mentioned as selectively forming the
metal, giving its oxygen to, um... some other metallic element.
* Perhaps even two (or more) glazes in layers, applying the highest
temperature one first, then the lower temperature one, firing which
wouldn't get up to the temperature that would de-crystallize the first
one.
The glaze(s), rather than the clay, would then be quenched
when glowing hot, raku
style, in accordance with the techniques and jigs already worked out
above.
Barium titanate (BaTiO3 = barium carbonate + rutile - CO2
?) is one of the materials mentioned in the connection of nanomaterial
and strong magnetism, and boron is always in there somewhere, (eg, in
NdFeB supermagnets) and is also a "glass forming element". Ilmenite is
FeTiO3, the titanium plus iron. Part of the trick is evidently to pick
things that will segregate, one ending up as its oxide and the other as
the metal with its magnetic properties.
...Okay, the first try didn't work. (Na2SiO3, ilmenite, laguna borate,
BaCO3, custer feldspar - cone 6 (1000c) March 29th.) A good question is
whether a reducing atmosphere in the kiln might help - after all, we
want some metal(s) nanocrystals, not all oxides. (The one time I tried
this, I was amazed that a charcoal briquette could sit in the kiln and
glow white hot like everything else yet not burn up. Of course, it was
selectively using up all the oxygen in the kiln - its very purpose -
and
when that was gone, it couldn't burn.)
Ocean Wave Power Project
March Details
In trying to design a different torque converter - more
like
Constantinesco's - I made a ratchet with lever arm and push rod, which
I also suggested seemed like a good fit for an improved
proof of concept ocean wave powered generator unit. After I made it I
realized that that torque converter design was unsuitable for the car
drive.
So the assembly is now available to be used as a main
linkage
component for the wave power design. It would be better to have two of
them, but perhaps one would get things moving, and anyway I now have or
can easily obtain everything needed to do the second one except one
bearing race. (I might just find bearings at a motor repair shop? Aha!
"dealextreme.com" has bearings!)
This mechanism would eliminate a good deal of the "slop",
the free
play in the mechanism that contributed to poor working.
The other contributor to the problems was the cogging of
the generator, which was fierce. I had expected the force of the
waves to overcome any and all cogging with ease and didn't worry about
it in my generator design. It didn't - at least
not in the waves available at the boat launches I went to on windy days
-
and so the
other thing is to ditch my generator (still makes a great car motor!)
and get one with little or no cogging.
And I knew of one that's readily available... one of those
direct drive electric lawn mower motors. Then I just need to
re-configure a new version of the power transmission assembly from the
floats assembly so the waves can drive it.
I wasn't about to leap right in and start with so much
else on my plate, but I thought I'd keep my eyes peeled for the ever
scarcer $50 used lawnmower. UsedVictoria.com was bleak - there were
more people looking for them than selling them. I remembered the
mower A & C Equipment had offered me one a few months ago for $75.
Chances seemed slim it might still be there, but I ran down there and
asked. Nope. I asked what a new motor would cost, and in the end the
guy went into
the back and came out with two motors, a 12 and a 9 amp. "Don't know
what condition they're in. They're yours." he said and handed them to
me! I thanked him and said he'd helped ocean wave power.
To make a long story short, the big one had some burned
out coils, but with some fixing and fitting
of a new brush the small one ran fine at 12 volts (3.1 amps) or 24
volts (3.7 amps), and
generated a few volts when turned. It works! The RPM to get 12 volts is
going to be rather high, though. It will be ironic if I have to rewind
a 120 volt motor to get more voltage to make 12 volts.
Anyway, I now have all the main components for an improved
proof-of-concept wave power machine!
Turquoise Battery Project
March Details
Ni-Mn Alkaline Cell: to make
or not to make?
In searching for sources of nickel, I ran across and read
a little treatise by DREO/CSA about making the very successful
nickel-cadmium batteries for the Alouettes and a couple of other
Canadian satellites, and it seemed they made the electrodes very
similarly to my own plan for the alkaline electrodes. They started with
a nickel mesh, and they sintered carbonyl nickel powder onto it to make
a conductive porous sheet. Then they vacuum impregnated the sheets with
nickel nitrate or cadmium nitrate powder. Finally they passed current
through the sheets, submerged in potassium hydroxide solution, which
converted the nitrate to hydroxide. They also 'coined' the sheets,
compacting around the edges and a couple of other places to eliminate
any protruding mesh wires (after having trouble with shorts).
My plan is to start with nickel mesh, mix nickel powder or
flake and maybe a little cobalt oxide (for conductivity) with nickel
hydroxide (which I already have, so forget having to make it from
nitrate), plus veegum and CMC gum to hold it all together, and compact
these (wetted) powders into a thin electrode "briquette". Similar for
the manganese 'negatrode' except I can use stainless steel mesh, a mix
of manganese and manganese dioxide powders, and perhaps a different
conductive metal powder -- if it's even needed.
One 'refinement', if such it is, is I plan to fold over
one long edge of the mesh and embed a ~#15 leed wire in the mesh across
the entire edge of the electrode, to connect to the terminal post. (I
may flatten the contact portion that wire in the rolling mill first if
it seems too thick.)
Since nickel electrodes swell in use, I'm going to back
the electrode with the Arches 90 pound watercolor paper, which can
compact
a bit as the electrode swells. I won't use sheet nickel backing - with
the conductive nickel mesh to carry current to the wire and the wire to
carry it along, it seems superfluous. Paperback batteries!
Well, I decided to try to order nickel material to make
alkaline batteries, or more specifically, to make the 'positrode' for
them. I called one place and they seemed to have everything, which
I thought would be very convenient. They e-mailed me a quote that took
my breath away! For my few little pieces, perhaps 3 pounds, including
the tiniest mesh screens that weren't even big enough for one
electrode, they wanted 782.54 $US! With shipping and taxes, that would
be over $1000 for a few scraps that wouldn't go very far even for
experimenting. At another site it seemed nickel was 2.50 $/pound from
the mines.
Then I asked a place in Ontario, a wholesaler that
imported nickel screen from China, if they had any dealers. I included
the absurd quote for $205.50 for a teeny little piece from the American
company, and they offered to give me "a much better quote than that!"
for my needs, a few square feet. I asked "How about you just send me
all you care to send for $75?... and by the way do you know offhand
where I might get nickel wire, rod, and powder?" Then I didn't hear
from them again in spite of two more e-mails, until I phoned on the
30th. Then, the quoted prices of $40-$50 per square foot took me
aback.
Perhaps I'll have to
nickel plate other metals - even just for experimental quantities. My
nickel brush plating solution doesn't seem to work any more, but a new
bottle
for $50 is starting to sound very attractive.
Great Idea for April
About the end of March I suddenly realized that I had a
possible solution to part of the battery making and testing problem at
hand. I had a dead Ni-Cd battery pack from an old cordless drill
someone gave me - 8 cells with only one that charges. It seems that
Ni-Cds usually die by shorting through the separator sheet, therefore,
the
electrodes should still be good if separated.
For the first time in my battery experiments - and for
alkaline batteries only - here's a possible way to test each individual
component, one at a time.
First, disassemble the battery and unroll the electrodes.
Hopefully they will retain their integrity. (This drill is so old
they're probably 'solid' sintered electrodes rather than compressed
powder types. That will help.)
Separate them. Re-compact them (flatten) if it seems
necessary. Remove the separator sheet and put in a new one. Put it in
some sort of case, with the electrodes flat. (Ensure minimal exposure
to air - CO2 in the air turns the KOH electrolyte into K2CO3 + H2O.)
Top up the KOH for the extra moisture the new sheet will absorb, and a
bit of water for what's evaporated, and close the case. (Vented case.)
Now the battery should charge and discharge pretty much as it did when
it was new. If it doesn't, it's the separator sheet or something basic
in the setup is wrong, because the electrodes used to work. This can
also be used to test the effectiveness of various separator sheets and
compare the rate of current flow they provide.
Second, make a manganese electrode and put it in in place
of the cadmium one. If that works, great, we're off to the races!
(should have our ~2.04 volts open circuit.)
If not, make a zinc electrode and try that. (~1.75 volts
O/C) Since nickel-zinc is known to work, if this doesn't work,
something is wrong with the way I'm making the electrodes. On the other
hand if the zinc works, the electrode construction must be okay. It's
possible then that the manganese chemistry doesn't work as expected.
Once (and if) I get that working, I can try making and
testing new nickel electrodes. Then I'll have replaced, one piece at a
time, the old Ni-Cd cell parts with the new types.
I think I'll still need that new bottle of nickel
electroplating solution, if only for making connecting wires that won't
dissolve!
What's the energy potential by comparison? Manganese is
1/2 the atomic weight of cadmium, so double the amp-hours per kilogram
(this isn't strictly accurate once the OH-'s are factored in, but we'll
use it for the equation) and a voltage of 1.56 volts instead of .82. 2
* 1.56 / .82 = 3.80 times the energy density of cadmium. (We don't
actually know if the Mn will become MnO or the heavier "hydrated" form,
Mn(OH)2
when discharged. Cd -> Cd(OH)2, the heavier form.) Call the energy
density at least triple, anyway. Over double that of a good metal
hydride. The nickel side won't be much different from other nickel
electrodes. Any I make will be a good modern powder type.
Construction Techniques:
Internal Connections, Battery Cases
I had considered that there appeared to be just two ways
to connect the electrodes to the terminals, in particular the positive
side, given that solder would
corrode away: Bolts made of something that wouldn't corrode (hopefully
stainless steel with salt electrolyte - only pure nickel works for
alkaline cells), or
spot welding. Bolts are tedious and can come loose; spot welding is not
amenable to small scale, minimal investment manufacture. (Hah! - even
DREO had to go to NASA for help getting the welding right!)
As an example of the power of the corrosive power of the
'positrode', I used a #4 plain coated nut and bolt in the present
perchlorate
battery. I
took it apart weeks later and found half the nut, corroded away and
fallen down, and none of the bolt at all. (though perhaps some
remainder fell to the bottom once the nut was gone - I didn't check
down there.)
But now I've thought of another connection technique:
riveting. Stainless steel rivets should work as well as stainless steel
nuts and bolts. Perhaps I'll try this next time. Nickel rivets for
alkaline cells... if there is such a thing. Or nickel plated.
The battery case plan has been in place for a while, but
hadn't actually been made in its planned final form. While shopping on
the 30th,
I bought some #10 - 24 threaded rod to
use for 7-3/4" 'bolts', having earlier formed a rectangular ABS case
body from 3" circular plumbing pipe, and having already bought 3/8"
thick acrylic
plastic for the top and bottom covers.
I cut a couple of covers and drilled the holes, threading
the bottom ones so nothing would stick out the bottoms.
If the acrylic seals well against the softer ABS when the
nuts are tightened, it'll be good as is. If not, a rubber gasket (eg
from an inner tube), cut to fit, seems to work well. The bottom could
be gasketed or glued. The cells inside had better be good - so far it's
600 grams and provides zero watt-hours!
If this case seems a bit cluttered, heavy and labour
intensive, it also has its advantages:
First, it's the only form of sealed case I've made so far
that's held under pressure, which sealed cells do build up when
charging.
Second, if a cell shorts out, it can be opened, the
offending
electrodes pried apart, and new electrode separator sheets put in. That
could extend the lifespan to decades.
I've been reluctant to do alkaline cells, as the
perchlorate
chemistry promises to be better all round: I expect lower pressure,
much higher current density, and higher energy density. But if I can't
get that going for now, at least Ni-Mn should be almost a double step
up over, eg, Ni-MH, and potentially far more economical than lithium.
There are of course things that could go wrong with this
seemingly predictable chemistry, too. I haven't tried it yet. Nickel
hydroxide positives are well known, but the manganese 'negatrodes' are
an
unknown. AFAICT no one ever seems to have tried them,
and it might not work out like the properties of manganese I'm aware of
seem to indicate. Or, my techniques or my chemicals (not all are of
known quality/purity) might conspire to produce unknown problems I
personally can't figure out with my limited chemical knowledge and
primitive test setups. (...as seems to be happening with the
perchlorate.)
Still, they seem quite a good bet, and the idea of using
the "known-to-work" dead Ni-Cd cell electrodes for testing will make it
much more evident where any troubles originate, an advantage I don't
have testing a completely new chemistry type.
Lead-Acid/Sodium
Sulfate Battery
Renewal Project
March Details