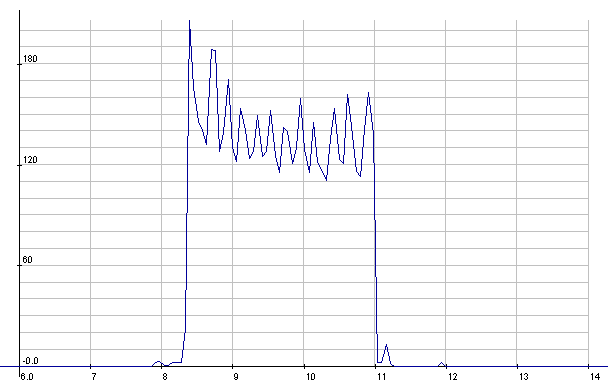
Lead-Acid: Starter cranking current
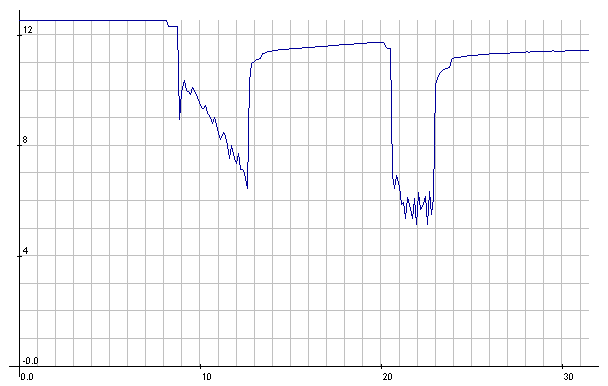
Lead-Acid: Starter cranking voltages. Decaying voltage with a few
seconds of cranking
(after a few previous short crankings that seemed fine) betrayed
emerging battery problems. You could hear it slowing down. It would
appear the voltage
should have stayed around 10 volts while
cranking.
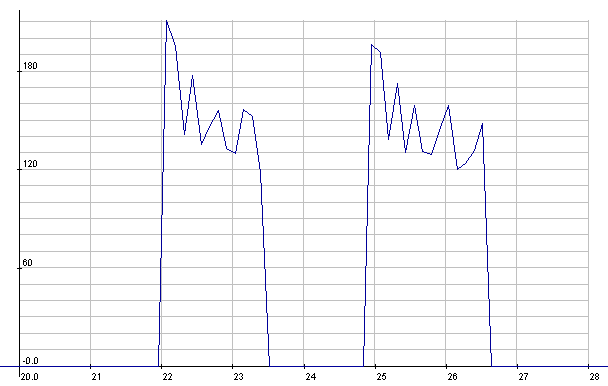
NiMH: Starter cranking currents
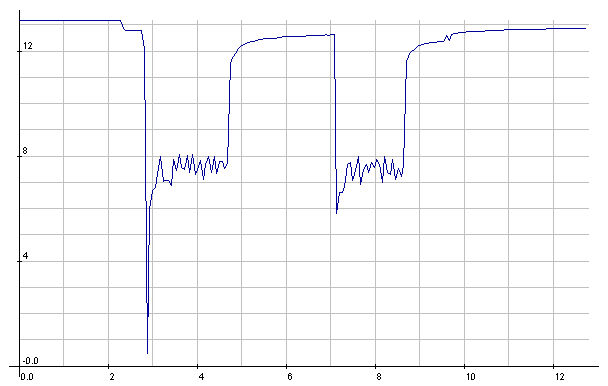
NiMH: Starter cranking voltages.
Seemed a little lower than with the
meter the previous day,
but it's probably typical.
(The 1/2 volt reading was probably a bad reading -
the setup was prone
to noise - or else a bad connection.)