Electric Hubcap Motor System
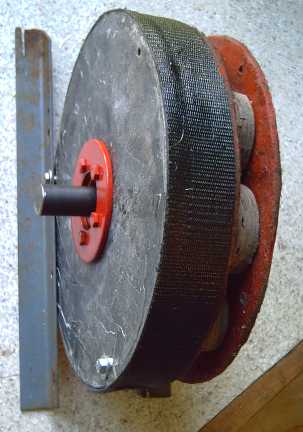
The motor profile with flat plate rotor.
Finally, 1/2 inch is to be trimmed from the diameter - less 'lip'
outside the coils and rotor.
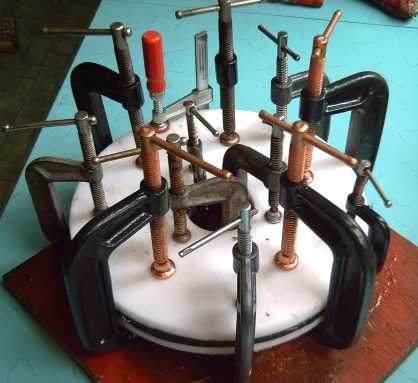
Pressing a drying PP-epoxy ring harder to try to squeeze out dry spots.
Afterwards I started backing the flexing PE plastic mold pieces with
plywood,
and then bought 1" thick to replace these 1/2" pieces.