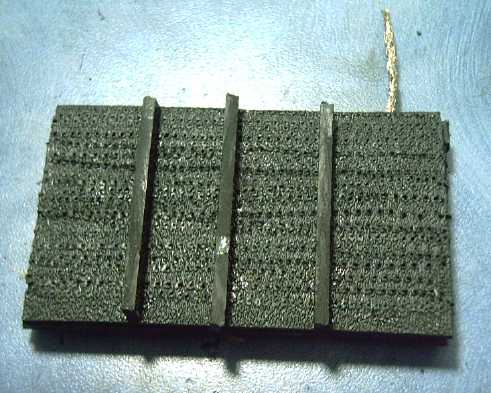
First flat plate perforated plastic pocket electrode.
I glued ribs outside on both faces, fearing the center would bulge out
too much.
For flooded cells gas needs a gap to bubble up
though anyway.
This nickel plated current collector grill and leed was the last one
before I found out they had to be zinc coated.
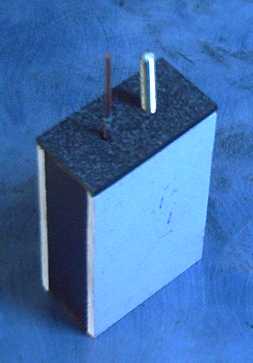
First pocket electrode battery with 1/2" square cylinder electrodes.
Case is sheet ABS fised with methylene chloride.
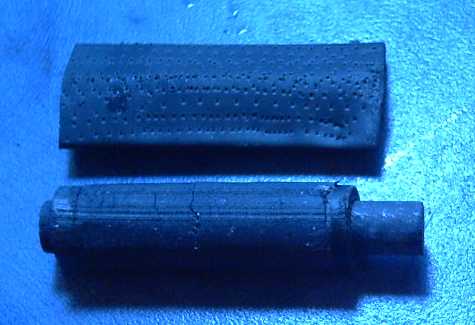
Compacted zinc electrode on carbon rod, and perforated heatshrink.
Note ABS plastic "washers" at each end.
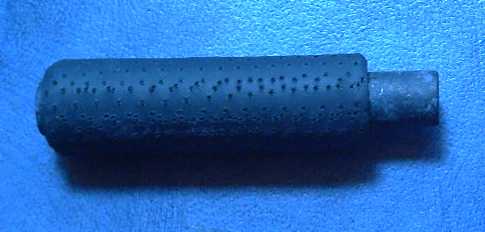
Heatshrink on and shrunk