Turquoise Energy News
#5
Craig Carmichael July 5th
2008
I spent most of June working on the Electric
Hubcaptm car motor and controller.
Notwithstanding that, I seem to have managed to produce a couple of
rather longwinded essays on other subjects. Whether or not it's wise
to include them, I wrote them so here they are.
Here's a little movie of the first successful wheel
turning test, June 10th:
http://www.saers.com/~craig/ElHubcapTest3.AVI
[25MB]. After that came more testing, frying a couple of underrated
MOSFETs and controller repairs, various mounting bracket improvements,
and more or less properly installing everything besides the batteries.
There seem to be a few things yet to be worked out... then
batteries.
I've had little time for the new Ni-La (3.25v
cells) Turquoise batteriestm, but I hope
get back to them this month, nor for the wave power.
Here's a link to a Danish made wave power unit with
a float layout like mine, though arrived at through a seemingly quite
different thought process and implemented somewhat differently:
http://www.dexawave.com/index.php?page=16 . It illustrates that
what appears to be a good solution to a problem can be derived in
different ways and may appear independently in various similar
forms.
I've left the movie clip from my May 20th wave power
unit test posted for now:
http://www.saers.com/~craig/CLIP0011-WPTest5Clip.AVI [26MB].
I took the projects to the electric
transportation show at Westbay Marina on Saturday June 28th, in
with all the electric bicycles and boats, hydrogen fuel cell and
hybrid car displays, and I was busy all day. There was quite a lot of
interest in the Hubcap motor. I think if it had been for sale now, at
least couple of people would have signed up on the spot. Luckily, I'd
just written up a couple of small posters and a handout about the
Hubcap hybrid add-on system. I gave out the 30 copies I printed and
could have used a few more. The batteries and the wave power unit
attracted considerable attention as well.
Coming up, I have a table reserved at the Green
Drinks "Building on Legacy" show on Tuesday (July 8th), 6-8
PM at Royal Roads University.
Topics Below:
Electric HubcapTM Drive Motor -
successful spin & car move tests
Turquoise Motor Controller - successful motor driving
tests
Turquoise BatteryTM
Car Conversion Economics
How is that Possible?
The Electric
HubcapTM Drive Motor
I'm glad to have conceived this motor. The more I
work with it and consider it, the more I realize it's the future. It's
the ultimate way to propel a car, and sooner or later, whether I make
a successful enterprise of it or not, all cars are destined to run
this way. First, permanent magnet synchronous motors are the most
efficient type of electic motor. Then, a direct magnetic link to the
wheel has no friction and low RPM for low inherent spinning energy. It
wastes no power in gears and transmission. All the losses it doesn't
have add up: Think of maybe 50% less power and overall energy needed
to run a car! If it takes 10 horsepower from a standard (or automatic)
transmission drive arrangement to keep a car moving along at 80 Km/Hr,
it'll be closer to 5-6 horsepower with the "Hubcap". And
there are no gears to shift.
Even with gasoline for power, having an electric
generator on the engine and direct wheel drive motors should be more
efficient, lighter, cheaper and easier to make than the usual
transmission, drive shafts, and CV joints and differentials that
connect the engine mechanically to the wheels.
Electrically powered, wheel motors will make much
better use of battery power - and behind that of the electrical grid -
than indirectly connected propulsion of any kind.
On top of these benefits, the motors and controllers
can be smaller and more economical because there are two (or even four
for all-wheel drive), while providing an extra margin of safety on the
road in the event of a motor failure.
The motor stator before pouring in the
polyester resin. (April 5th) Features: melamine skin, nail strips, 9
copper coils & wiring. Grey cables connect temperature sensors,
small RPM/tach coil.
In standard motor making, the coils must be
wound on a former, then fed strand by strand through the narrow stator
slots, into which folded papers (or mylar plastic) have been inserted
to insulate the wires from the iron laminates. After inserting more
"slot wedge" papers to hold the wires in, the motor is
dipped in varnish and baked in an oven to fuse everything.
In this motor, the coils are simply wound
(potentially by machine) and set in place, then casting resin is
poured in - it's much easier to make.
The hubcap motor is up and running, the jacked up
wheel first spinning on Tuesday, June 10th, powered with a 12 volt
battery.
To get the motor to turn, I had to make a new six
poles magnet rotor. It turned out that with 12 N-S-N-S- magnet poles
on the rotor and 9 coils - an ideal generator configuration -
as a motor all the magnetisms cancel out and there's no net
rotary thrust! It took me many days of puzzling to figure this out,
after first checking the motor and the controller a few times for
wiring mistakes.
Assembling the first magnet rotor. (Epoxy
glue.) The powerful magnets interact fiercely and precautions are
required.
The new magnet rotor. This time, I used a disk
ready made for a car wheel: a brake disk. The center had to be ground
out larger, which was easier than I expected. Then it was a perfect
fit. First I tried it with 6 magnets. When the wheel turned, I doubled
them up: NN-SS-NN-SS-NN-SS-. I may fill the gaps and try
NNNSSSNNNSSSNNNSSS.
Twelve volts naturally provided just a small
percentage of the expected full power. Then I tried 24 volts with the
wheel on the ground, and the motor moved the car, downslope but also
turning the stopped engine in second gear.
A lot of vibration showed the stator mounting
bracket needed substantial strengthening. I tightened a couple of
loose bolts and reworked it somewhat... and made it worse! I began to
see where it needed extra support, and also how it might be put in. I
added struts, a couple of pipes diagonally from the outsides of the
bracket to the axle, to stiffen the arms of the bracket. That still
didn't solve the whole problem, but finally simple steel straps aross
the top and bottom of the motor to each side, to keep the arms from
spreading a bit, made a big difference. Such metal fabrications, with
the layout of each piece, and every bend, hole and bolt individually
worked out, shaped and tried on repeatedly for size, take a lot of
time, and strengthening the bracket consumed a couple of weeks. I find
such time consuming "trivial" items frustrating to work on,
feeling I could surely be making better use of my talents. On the
other hand... it won't work right if they're not done!
Of course, for the second one I now know the
requirements better and have better designs in my head in advance.
Experience! The second time is always easier.
Installing the first bracket of the stator
mounting, ages ago (April 2nd).
If I was a car manufacturer the motors would
naturally go in behind the wheels, but the space in most cars as made
is very limited and I came up with the idea of having the
"Electric Hubcap" on the outside of the wheel instead.
Looking at the car again I see possibly workable
ideas for fitting a motor inside, but there are still objections:
tight spaces and close, awkward fits, needing scary supermagnet rotor
handling by the installer, and the need for motor designs customized
by car make and model - undesirable manufacturing complications.
In addition to the mechanical objections, the
Electric Hubcaptm fairing is visible on the
outside of the car. IMHO, it even looks COOL! (Molded fibreglass or
something would be even cooler!) Everyone can see that the car is
electric, which usually isn't obvious, and how a pair of small motors
are driving a car. And, when they've seen one, or a few, or a bunch,
they'll investigate. (Especially if gas prices continue to rise.) Thus
it will advertise itself out on the streets, with the potential for
spreading the word like wildfire if the production and delivery
capacity is in place. With an invisible motor behind a wheel, this
whole free, automatic and self-perpetuating potential ad campaign that
I've stumbled onto vanishes, and must be replaced by more
sophisticated and costly publicity.
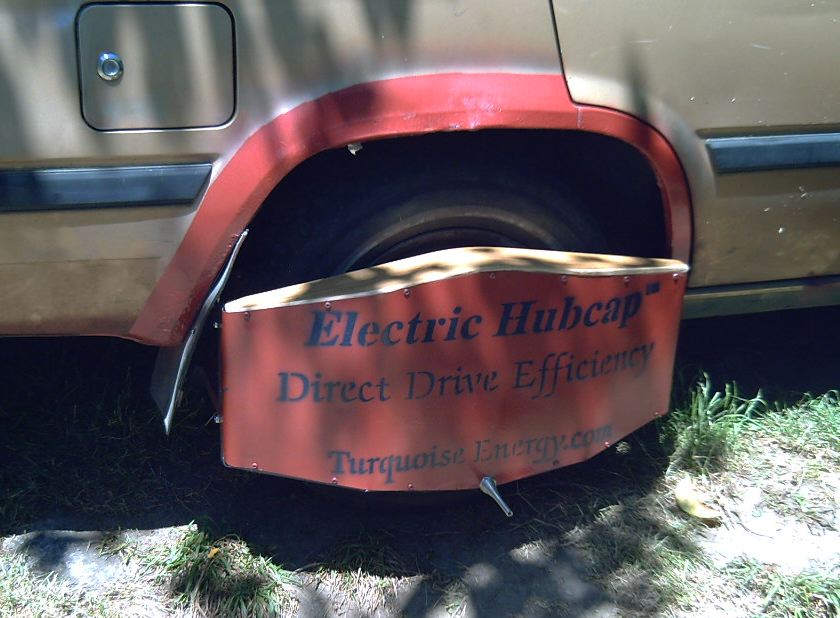
Direct electric drive will make those heavy,
inefficient mechanical drive trains obsolete: no more transmissions
manual and automatic, drive shafts, differentials, CV and Universal
joints. No more gear shifting or clutches.
The latest tests (July 2nd) were with 36 volts. It seemed the car
almost wanted to start moving on level pavement... but not quite. On a
very slight downslope it started going and seemed to accelerate more
than the slope accounted for.
Now, when they might make the evidently small
difference between "no go" and "go", might be a
good time to test a few configuration options.
I have three variants of the rotor configuration to
try out. (It's unfortunate for testing that I don't have any screw-on
magnets available and have to epoxy glue these ones into place. It
makes what should be simple layout trial comparisons
cumbersome.)
I'll also look for more ways to stiffen the mounting
bracket - it's much better, but there's still some vibration.
Three twelve volt batteries is all I have, so that's
precluded higher voltage tests so far.
Electric Hubcap Motor Factoids:
* The motor per se has no moving parts: only the car's wheel
turns.
* The frictionless magnetic link to the wheel magnifies useful
power by transmitting it all directly to the wheel. There's no losses
from a transmission or gears, it requires no gear shifting or other
attention by the driver, and it's virtually silent.
* Permanent magnet synchronous motors also have the highest
intrinsic efficiency of all electric motor families, further
leveraging the efficient power transfer. As a guess, one might perhaps
expect up to 50% greater range than other electric motor systems from
the same energy, and correspondingly better performance for the same
kilowatts of electricity used by the motor.
* Installation requires no connections with or changes to the
car's existing mechanical components and systems.
* When not in use, the motor has no more effect on the car than
any other 40 pounds of luggage. Built in by car makers, they would add
even less weight.
* The motor sticks out just 4" from the wheel or a couple of
inches past the fender, less protrusion than the outside rear view
mirror.
* The RPM with 13 inch wheels is about 10 per one kilometer per
hour of speed, that is, 450 RPM at 45 Km/Hour. Most electric motors
prefer much higher speeds, but the "Hubcap" has good low RPM
torque and power. 120 Km/hour is just 1200 RPM, a stately pace for
most electric motors but a good high end range for the
"Hubcap".
* A tachometer coil and an IC temperature sensor (AD590) are
built in to ascertain actual speed and to warn of any
overheating.
* It's air cooled. (I have a vague idea it will get pretty hot
driving a car up a mountain. I have an idea for "porous"
polyester casting to improve the stator's internal cooling, that I
hope to try out on the second motor.)
* The rotor is a 10 inch steel disk brake disk, 6 poles using 12
or 18 .5" x 1" x 2" NIB supermagnets. The stator, cast
in polyester, has 9 coils, each 60 turns of #14 wire, in 3 phase
"Y" configuration. Magnetic flux is axial.
* A unique design breakthrough is that the stator iron is strips
of regular nail gun finishing nails in the coil cores instead of
custom die cut iron laminate sheets. With no axle or other moving
parts, this motor is simple enough to make at home, or the coils could
be wound by machine, set in place, and cast, for super economical mass
production.
Turquoise Motor
Controller
I first decided to make my own AC motor controllers
owing to reputed very high prices for those suitable for electric
vehicles. I gathered that most people retrofitting cars with electric
drives at this time use less efficient DC motors and controls, and
that these motors don't do regenerative (AKA dynamic) braking.
Permanent magnet AC motors such as the Electric Hubcap motor generate
the most power from the least amount of electricity, and can recover
energy as the car slows or goes downhill.
But I hadn't done an exhaustive search. There do
seem to be some controller products I was unaware of.
My expectation of peak drive was along
the lines of 40-50 amps at 120 volts = 4800-6000 watts, perhaps six to
eight horsepower, and I made the controller accordingly. (If that
sounds "gutless", consider: electric motors accelerate
better than gas at low speeds, the car will take less horsepower with
the direct drive, and there'll be left and right side motors for
balance - and double the power.)
Motor speces, though, are hard to quantify except by
building and trying. As it turns out, the battery current at stopped
or low RPM is actually about equal to the voltage, ie, 12 amps at 12
volts and 24 amps at 24 volts. 120 V * 120 A = 14400 W or 19
horsepower. Since that's utterly unrealistic for this size motor, it
is evident that 120 volts is too much. For 6000 watts, the voltage and
current would both have to be about 77. So a good choice might turn
out to be 60 or 72 volts - with higher currents than I'd planned on,
but still in the tens rather than over 100 amps.
The power MOSFETs I used in the prototype Turquoise
Controller are rated for 200 volts at currents up to 65 amps, so this
is pushing their current limits. (In my first test at 36 volts, thus
~36 amps, two 30 amp MOSFETs I was using fried surprisingly fast. and
took out the controller chip with them.) Higher current capacity
MOSFETs with lower voltage ratings (eg 100V, 127A) are easily
available, so the trade-off actually doesn't mean much except for
heavier power wires - and voltages that are probably safer for humans
to work with anyway, especially in damp conditions. Nothing changes in
the motor or inside the controller except the 6 wired-in MOSFETs need
replacing. Now that the specs are clarified and the controller circuit
configuration is final, it would be nice to do a production version
instead of more hand wiring, but that's a design job I'd just as soon
hand off to someone with more recent PCB design experience than mine
as techniques have changed markedly since my last designs in the
1980's.
A few things got changed in testing. Driving with
three phase signals that are square waves instead of sine waves
doesn't work as well as desired with this motor. It seems a better
choice is to drive only two phases at a time in a six state sequence.
The change was simple to make on the PWB with a soldering iron.
Interestingly, the actual waveforms created do have, very
roughly, a sort of sine wave-ish energy pattern.
Finally, just when I thought everything was surely
right, I was puzzled by a strange higher frequency oscillation. I
finally found the culprit: the 12 volt battery I was testing with was
low after all the testing I'd done! The controller would drive the
coils, and those would draw heavy currents and reduce the battery
voltage to 9.6 volts, where the drive undervoltage protection would
shut them off. With the coil drives off, the voltage would come up
again, and the coil would turn back on and lower the voltage again, ad
infinitum. Thus it took an extra day to realize everything was in fact
working correctly. It was just the test battery that needed a
recharge!
The fact of this oscillation can be seen as an
advantage: starting to lose power and make noise gradually as the
batteries get low provides an automatic early warning that it's time
to switch to the gas engine.
I was going to put the controller in with the motor
where the air rushing by would help cool it and the wires to the motor
would be very short, but then I decided it would be better off inside
the car, out of rain, snow and mud. I bolted it near the fender and
the wires out to the motor are just about a meter long. The longer the
cable, the more the losses and the worse the stray inductance.
The other change on testing was to add small (~7uF)
"run" motor capacitors across the three drive lines to the
motor, to damp the motor's inductive switching spike voltages that
burn out solid state drivers (not to mention regular mechanical on-off
switch and relay contacts).
The Turquoise Motor Controller is simple,
economical, and electrically quieter than most, and it should probably
run cooler. Electronically, it contains only three standard integrated
circuits, the IR2130 three phase MOS gate driver (MGD) chip, also
readily available, the six high power MOSFET transistors, and of
course various associated "lesser" components.
Although I haven't priced out motor controllers, I
expect that with a parts cost around perhaps $70-$100 in small
quantity and relatively simple assembly, the Turquoise
Controller will be the economical choice for supplying with the
Electric Hubcap system.
How It Works:
The controller converts the DC power from the battery to a
variable frequency approximation of three phase AC power, on three
power wires that go to the motor to create a variable speed rotating
magnetic field in the stator, the motionless part of the motor. That
field pulls the permanent magnet rotor on the wheel around with it and
hence rotates the wheel. The frequency is controlled by pressing on
(what else?) the "gas" pedal.
Increasing the frequency above the wheel's current speed
(pressing farther) causes acceleration and the motor uses energy from
the battery. Conversely, a lower frequency (letting the pedal up)
causes deceleration, dynamic braking. In decelerating, the motor
generates energy, which goes back into the batteries.
Frequency will go from about 10Hz (3 Km/hour) to 360 (120
Km/Hr).
Turquoise
BatteryTM
With the GM EV-1, people thought the NiMH batteries
"would outlast the car". This sounded very reassuring, but
the EV-1s weren't on the road long enough to test this idea. I hear
NiMH hybrid car batteries have to be replaced as often as every five
years. Of course, these are only six or seven amp-hour batteries, 120
cells with less energy per cell than a NiMH "D" cell (about
10 A-H), from which about 1000 recharges are expected.
I've been hoping for substantially longer life from
the Turquoise Batteries. I may be oversanguine, but I hope the
NiOOH/Ni(OH)2 ("+" side) will last much longer in the
neutral PH electrolyte than in the usual KOH (caustic lye), and I'm
also expecting very long life from the lanthanum (La/La(OH)3, "-"
side).
Today I found (in town no less) a chemical I've been looking for,
potassium dichromate, so I've also bought some chemistry equipment to
make acetaldehyde (AKA ethanal) from vodka (AKA ethanol), but it's my
first move on the batteries in some time. I don't know how pure the
KCr2O7 is, but the alberta vodka claims it's "triple distilled
for the ultimate purity". (though it's actually 60% water - and
by now only 3/4 full.)
As I thus have little of substance to report, here's a general
essay. To the usual question, "If that was possible, why hasn't
it been done already?", in the case of the batteries I might
suggest the following factors:
1. Water dissociates above about 2 volts. People
thinking "inside the box" simply look for electrochemical
reactions below that voltage to make batteries from. Thus we have
lead-acid at 2.1 volts as the highest voltage water electrolyte based
cells. I'm more stubborn: "Lanthanum to lanthanum hydroxide, -2.9
volts, both sides of the reaction are solids, and it complements the
usual nickel [oxy]hydroxide '+' electrode reaction! What a great
reaction for energy storage! ...Now... what do I do to coerce it into
working?"
Somebody else with similar
"outside the box" thinking came up with the non water based
lithium batteries (3+ volts). However, these other electrolytes are
~~100 times slower at diffusing ions, and cars need fast batteries.
Lithium types haven't proven very workable for car batteries so far.
Most real electric cars are still using lead-acid.
2. Again, people look for dead simple. They pick
sulfuric acid (acidic) or potassium hydroxide (alkaline) as
electrolyte because of the ease of getting ions -- and understanding
the straightforward "textbook" reactions. And... it's what
the last guy used! But there are some fairly neutral salts that make
good electrolytes (even table salt), that allow other metals like
copper into the cell without corrosion, and the potential for
additives to accomplish specific tasks, like to catalyze the
lanthanum/lanthanum hydroxide redox reaction or prevent the
dissociation of water for example, is vast. I picked potassium
chloride (edible non-sodium salt from the drug store), a faster
neutral PH ion diffuser than sodium chloride. And I am or may be
testing the efficacy of several enabling "reagent"
additives: MEK, ethanal, DMSO...
3. Not many people who study chemistry study battery
chemistry specifically. It is a branch unto itself.
4. Few chemistry books and web sources mention the
electrochemical reduction-oxidation ("redox") reactions. As,
probably, no one is specifically looking for a lanthanum reaction, it
seems possible few battery researchers have happened across it, and
those who did noted the voltage was "too high". However,
somebody thought it worth mentioning in a chemistry handbook amongst
many other redox reactions, somebody put those on the web, and I got
lucky and saw it there.
5. Mostly, companies who gear up to make and sell
batteries aren't interested in anything new that might force them to
change. Who are these mythical companies who "must be" doing
research into improved batteries? Duracell? Energizer? Hah! If they're
making rechargables at all, it's only owing to slumping sales of
non-rechargables. Some recent lithium battery advances have come from
China. As so often happens with the real advances, the guy that
formulated the metal hydride used in the GM EV-1 batteries did it in
his garage on his own time and resources. Whether he made money off
it, I don't know. (I've heard recently that only about 1% of inventors
do well off their fine inventions, and that certainly fits my personal
experiences.)
There seems to be a lot of "pie in the sky"
talk of battery breakthroughs, but nothing seems to make it onto the
market. I read a glowing article about silicon nanowire batteries just
about when I was deciding to make batteries myself, what a great thing
they would be and how they fit in with familiar technology we already
know how to make. I emailed the experimenter full of enthusiasm for
his developments and mentioned the car motor I was working on. Here,
surely, was a match! Weeks later I got a brief answer simply saying
his batteries "need more development", which seemed to be a
marked contrast to "fit in" with "already known"
technology and manufacturing. I could well be mistaken and his
batteries may appear any day, but I confess I got the impression his
article was more about creating a good impression, even a sensation,
to leverage further research money - perhaps more for nanowires than
for batteries - than to announce an actual, workable technical
breakthrough that was intended to result in a real product.
Of course, the Turquoise Battery is also "pie
in the sky" until I've got them going. The work on the motor has
taken longer than expected, and the time I'll be able to concentrate
again on the batteries keeps getting pushed back. "By July"
is becoming "sometime in July".
Car Conversion
Economics
I try to create new things that seem to me to be
sensible and economical to replace things that seem needlessly
cumbersome, awkward and inefficient. I see over and over that most
people just try to improve what already exists by adding complexity or
refinements to it rather than taking a fresh approach.
Cars seem an excellent illustration of how once a
thing is once being done one way - engine, clutch (fluid or manual),
transmission, drive shafts and differential gears - it is amazingly
difficult for us humans to see fundamentally better ways, and even
once seen, to actually adopt them. Even most electric motors operate
through this lossy drive train. The Electric Hubcap can let us adopt
the best features of the better "direct drive" way now, en
masse in existing cars, without even waiting for the automakers to
catch up!
Without any intention of committing in any way to
specific prices or even price ranges, here is my train of thought on
the economics.
The motor controller (including the driver's
controls), might be retailed in limited quantities for perhaps $500,
or "mass produced" for as little as $200 (still less in
real quantity).
The electric hubcap motors with mounting brackets et
al might be $2200 in small quantities or as little as $550 in factory
production.
The batteries, from costs I vaguely worked out a
while back, might be $2000 in early small quantities down to $800 in
fair quantity production, for 6 or 7 KWH to drive 50+ Km on a charge
(before turning on the car's gas engine to continue on a longer
trip).
It will also take someone a few hours to install the
units. Most people won't want to do the work themselves and will take
it to a garage or Canadian Tire. Call it maybe 6 hours labour at 80
$/Hr, $480. Before mechanics are familiar with the procedures, maybe
count on 12 hours, $960.
(The figures below are for adding one motor
to the vehicle, though left and right side motors would seem more
desirable for balance. It's also possible for two motors that they may
be made somewhat smaller and lighter than the one, so the price for
two may not be double that of one, and the batteries don't
double.)
So the potential bottom line for early limited
production is $500 + $2200 + $2000 + $960 = $5660. That's worth doing
on an otherwise nice car.
Once they're being factory produced, the cost would
drop significantly: $200 + $550 + $800 + $480 = $2230. For someone
driving 10 Mm a year (~~25 Km/day) and getting 10 Km/L of gas, at 1.50
$/L, the fuel savings alone would pay off the investment within two
years. Drive 25 Km each way to work and plug in at work to recharge,
and it would be under one year.
Also that's not so much more than the cost of any
major work on a vehicle, and will eliminate much of the need for such
work. Installing a new clutch, front CV drive shafts and a few seals
and miscellaneous cost me $1200 a couple of years ago and I've spent
more than that on gasoline since then. If instead I could have had
this electric conversion in good time before the clutch wore out, I'd
hardly have used the engine, transmission and clutch since then except
for a very few highway trips, and so defrayed those expenses for years
(indefinitely), and the energy cost for electricity would have been
95% less than for gasoline. Even in my old car and with the little
driving I do, I'd have been well ahead to have converted, and could
still be now.
And there's an even better reason for the consumer
to go this route: The Electric Hubcaps are substantially more
efficient than what automakers are currently supplying, and the
batteries, if successful, will be smaller, lighter and a definite
advance in the state of the art. Cheap as electricity is compared to
gasoline, it will take significantly less of it to run the Electric
Hubcap equipped car than plug-in hybrids now in the pipelines from
automakers. They'll catch on eventually, but in the meantime, millions
of Electric Hubcaps could be sold to all for existing cars,
drastically cutting our fossil fuel usage, starting right here in
BC!
How is that
Possible?
This little tome took me a lot more words than I
expected to say and has little to do with the subject at hand. I
consider it a very interesting story, but if your reading time is
limited... well, you've just passed the real end of the
newsletter!
Whenever I'm making something new, whether it's the
improved violin bridge or the promising new battery chemistry, people
ask me questions like, "If that was possible, don't you think
someone would have already done it by now?" or "Don't you
think you're reinventing the wheel?" Such questions implicitly
challenge my motivation and impugn my credibility and judgement for
attempting the project. Is the overall state of affairs and the
feasibility and value of the project approximately as I see it, or
have I overlooked something, or even multiple things?
As I'm not omniscient - geez, I hardly even follow
the news headlines - it's not easy to give a satisfactory or firm
answer. Sometimes I'm not right. Perhaps it's been done and I haven't
heard of it. Perhaps there is some unbreachable stumbling block that
ruins the whole idea, that will stop me in the middle. Perhaps someone
else is about to release approximately the same product I'm working on
before I do, or a better one, or something new that makes my whole
project worthless. But no one who worries too much about such things -
without convincing evidence - is likely to go to the trouble of
bothering to try making something new that they've thought of... in
case they don't succeed, or somebody else beats them to it. Better to
do Sudokus or play cards on the computer or watch TV. Perhaps that's
why I invent things and others don't... notwithstanding the number of
Sudokus I've done lately.
Here's one story of a most valuable thing that was and is very
possible, and yet it has still never come to pass... so far...
In 1872 Christopher Shoals invented an innovative new typewriter
with a keyboard having both capitals and lower case letters on the
same keys. It was the first really successful typewriter. But the keys
were subject to mechanically jamming up together, and worse, the
printed side faced away from the typist, so she couldn't see it until
she'd finished the page. Unnoticed jammed keys made for a big waste of
time. So Shoals rearranged his A-B-C key layout to a pattern that he
thought would cause the most distant keys from left and right to be
used alternately as much as possible. This reduced the jamming, partly
by slowing the typist down quite a bit. This deliberately frustrating,
slow typing key layout was called "QWERTY".
Touch typing techniques were invented, typewriters improved and
the print faced the typist, and the reason for the awkward layout
passed into history. In the 1930's August Dvorak designed a new
"user friendly" key layout to speed up typing instead of
slowing it down. The most commonly used keys were in the home
positions, with the vowels in the home row on the left hand and the
consonants mostly on the right. Unfortunately at that time a
typewriter was a major equipment expense for a company, not something
purchased by ordinary people, and businesses didn't want to put out
big money for something the typing schools weren't teaching.
(Notwithstanding that, most of the world's record fastest typists have
been those few who've used Dvorak.) In world war two the US army badly
needed typists in a hurry, and so a Dvorak training program was run.
However, when the typewriters were ordered for distribution, a
bureauocrat in the supply department vetoed the order saying the
Dvorak keyboards "weren't standard". The momentum for
progress was smothered, and a myth grew that it was impossible to
change the keyboard.
Then computers came along. Instead of the keys attaching by
levers to the top of the keyboard, they were soldered to a printed
circuit board, and could be layed out as pleased! We associate
computer pioneers with innovation, and it was one of the greatest
disappointments of my life to see the first Apple computers. Not only
were the keys still in that abhorrent "QWERTY" arrangement,
but they hadn't even straightened out the now ridiculous staggered key
columns! IBM and other manufacturers also followed suit and bowed down
in ritual conformity to a design that had already outlived its
usefulness by a century, and the QWERTY juggernaut had taken the new
technology.
In fall 1984 I myself developed a new key layout based loosely on
Dvorak's that not only was a big improvement on his (after making some
computer studies of letter and other key usages he couldn't do back
then), but was optimized for computer word processing. It had, for
example, cursor arrows and backspace in convenient touch-typing
positions instead of off to the side, and several other advanced
features, some that couldn't have been done on a mechanical typewriter
and some that could have been.
There were later feeble attempts to provide "software"
Dvorak keyboard layouts, and some still exist, but they are just red
herrings that confuse the issue: virtually no one uses them. No one
can learn to type a key layout where the keys aren't what they say
they are, and nothing but confusion results from pressing
"Command-Option-R" when half the time the QWERTY "R"
(Dvorak "Y") or other bizarre mismatch results, and some
things don't work at all no matter how they're typed.
Another better key layout called "Maltron" was
developed in the UK. It had honed down many aspects of simply typing
words to a fine point, but it was harder to learn than Dvorak, didn't
improve some of the things that my "CSK" layout did, and
worse, it was offered as a "high-end" keyboard at around
$800. That's no way to change the world!
I also later learned in a phone call to Keytronics that they had
had a Dvorak keyboard, but that "it didn't sell" and was
discontinued. This was quite a surprise to learn, but no surprise to
hear it didn't sell when it was such a well kept secret. I had been
looking at Keytronics' glossy back cover color magazine ads now and
then in computer magazines for years hoping to see one, but there was
never a hint! (Don't forget there was no internet then to simply go to
a web site to view the catalog.)
In the pressures of life I didn't try to develop my keyboard
commercially until about 1997. The need was the same, the same
opportunity still existed, and keyboard usage was ever growing. I
further improved the layout to reflect more "modern"
keyboard standards and tried to get a very modest sum of NRC/IRAP
funding to make a prototype that would work with modern PC's and Macs.
(This was still pre-USB days.)
An ABS plastic mock-up of the "CSK",
Carmichael Simplified Keyboard, ~1997.
Home keys are OAEI and TNRS. Angles were in
vogue at the time - I'd probably drop them or reduce them
now.
There was skepticism that such a product could be marketed. I
said it was easy: keyboards weren't major cost items used only by
businesses any more; there was a much greater element of personal
choice possible today and those who wanted to type faster could safely
do so knowing that once a new product is on the market and in demand,
more companies will start making them. Give some away to elementary
schools where the kids were learning to type - they could judge
without adult prejudice what was better, and soon the parents would be
asking for them in Office Depot and Future Shop. Although most older
people wouldn't want to switch, basically in five years QWERTY
keyboard sales would be nothing compared to the new layout, and the
next generation's productivity would be way farther ahead.
This was deemed unworthy of the meager IRAP support I applied
for. My old RS-232 keyboard from 1984 couldn't adapt itself to USB,
etc, and a thing that upped my personal productivity for many years is
gone. Here I sit at my computer with Shoals' never updated "slow
down!" 1872 key layout on my "there was a crooked house"
carpal tunnel syndrome keyboard, like everybody else, unwillingly but
with no other practical option.
Since the computer became common, there have never been any
technical problems to making - or to selling - an improved keyboard.
What is lacking is the will to do so. Sadly I moved on.
Often the human race has to be dragged kicking and
screaming to adopt improvements that we love and "can't live
without" once adopted. If no one drags us (I don't exclude myself
- often I resist change stubbornly too), we stay where we are forever,
generation after generation, however foolishly, however needlessly,
doing things the hard way, while making the obvious change may get
harder and harder with passing time. (If a circle was 400 degrees
instead of 360, a right angle would be 100 degrees and a 1:1 slope
would be 50 degrees. Wouldn't that be easier? Wouldn't counting time
would be much simpler if a day was 10 hours with 100 minutes per hour
and 100 seconds per minute? That would make minutes a bit longer and
seconds a bit shorter than now. These and many other probably valuable
changes would have been easy in past centuries - and especially at
their beginnings - but who could try to change them today? Thank
goodness somehow the Arabs, taking a fresh approach, got us off Roman
numerals a while back. I can just see us still using them today on
computer spreadsheets!)
Back to the subject at hand: Since January I've for
some reason taken on, and I'm somehow - amazingly to me - overcoming
one by one, all of the technical obstacles that have held us back from
our best electric automotive ideals for decades, all by myself with
whatever resources I can scrounge up. I've invented what looks to me
like the world's best conceived electric car motor. I seem to be onto
a notably better battery chemistry. More, these things can be
retrofitted to existing vehicles without waiting for everyone to
eventually buy new cars.
Of course there's no guarantee that somebody else
won't unexpectedly announce some even better battery chemistry or the
very one I'm working on, now for sale at Radio Shack, or another great
direct drive electric car motor won't suddenly appear in the Canadian
Tire catalog. So should I just sit and wait for others to make such
things happen? Why haven't they been done already? There seem
to be fair reasons no one has previously come up with this battery
chemistry, and why no one else has invented this sort of electric
motor design. I'm doing it because I suspect there's every chance I'm
very much at the "bleading edge" of progress, where I have
so often found myself over the years (...and with so little to show
for it!), and that I'll never see anything as good as what I'm doing
or trying to do now on store shelves in my lifetime unless I make them
happen.
And with these particular projects, I am optimistic
that high fossil fuel costs and vague concerns for the future about
what might happen once lots of cars are powered by the grid, will drag
us kicking and screaming into a new, safer, quieter, cleaner, more
efficient and better transportation age - if the components are in
place to enable it.
http://www.turquoiseenergy.com
Victoria BC